第121回~第130回
第121回~第130回第121回 「はやぶさプロジェクト」にわが国の誇る技術力を思う
第121回 「はやぶさプロジェクト」にわが国の誇る技術力を思う提供:JAXA 昨年末、内閣府において、約7年、60億kmの宇宙航行を経て、イトカワから約1,500個の微粒子を持ち帰った小惑星探査機「はやぶさ」プロジェクトに関わった宇宙航空研究開発機構(JAXA)のはやぶさプロジェクトチームと、それを支えた118の企業や大学などの功労者に対して、海江田万里・宇宙開発担当相と高木義明・文部科学相から感謝状が贈られた。
ヒンジ部にNTNの球面滑り軸受採用
プロジェクトチームには、探査ロボット「ミネルバ」と回収カプセルを開発したIHIエアロスペース、サンプル採取装置を開発した住友重機械工業、イオンエンジンを開発したNEC、化学推進スラスタ・イオンエンジン推進剤供給系を開発した三菱重工業などのほか、重要な機械要素である軸受のメーカーとしては、NTNが参画した。
「はやぶさ」外観(提供:JAXA)。3枚の太陽電池パネルを開くための関節部分(矢印の箇所、接合部位)にNTN製軸受が採用
「はやぶさ」に採用された球面滑り軸受(提供:NTN)衛星は打ち上げ後、その駆動源である電力を主として、宇宙空間で展開した太陽電池から得ている。太陽電池は一般に平板で効率よく発電するためには、太陽方向に対し直角に向いている必要がある。太陽電池パドル機構部(PDM)はこの動作を行う機構で、この展開駆動部となるヒンジ部(関節部位)に軸受が用いられている。「はやぶさ」では、宇宙空間で太陽電池パネルを開くためのこのヒンジ部にNTN製の球面滑り軸受が採用、宇宙空間という特殊な環境で作動し、太陽電池による電源供給を確実にする役割を果たした。
プロジェクトチームにはそのほか、固有技術を持つ多くの中小企業も参画、その中に海江田宇宙開発担当大臣が自ら視察を行った、固体潤滑被膜を手がける川邑研究所がある。
各種駆動箇所には川邑研の固体潤滑剤

(提供:住鉱潤滑剤) 宇宙空間では10-5Pa以下の真空、微小重力、原子状酸素などの環境にさらされる。この真空環境では、地上で使われているオイルやグリースなどの液体潤滑剤は蒸発による機能の大幅な低下が避けられず、真空中でも蒸発しない固体潤滑剤が用いられる。中でも層状固体潤滑剤であり、摩擦せん断時の劈開により潤滑なじみを実現する二硫化モリブデンの焼成膜などが国際宇宙ステーション(ISS)の日本実験棟「きぼう」などでも実績がある。
宇宙関係での二硫化モリブデンの適用に長年の実績を持つ川邑研究所では、「はやぶさ」でも二硫化モリブデン被膜を提供、打ち上げのロケットブースターの切り離し部や、太陽電池パドル駆動部、探査ロボットの脱着部など、各種の駆動箇所に多用されていると見られる。
「はやぶさ」を支えたこうした技術に触れた海江田宇宙開発担当大臣は、「宇宙開発は総合的な技術力が求められる裾野の広い分野で、多くの機関や企業の力を集めてはじめて成り立つもの。はやぶさの成功も、探査機の製造、打上げ、運用、回収、試料分析など様々な分野で、プロジェクトメンバー一人一人の力の結集があってこその快挙」と語っているとおり、中小企業に至るまでのわが国の世界に誇る技術力の結集によって、はやぶさは数々のトラブルに見舞われながらも奇跡の帰還を果たした。「プロジェクトメンバーの表彰は、はやぶさの成功に貢献した個々の高い技術力を顕彰する目的」(海江田氏のブログより)とのことらしいが、わが国の優れた技術力のアピールを国内にとどめていてはもったいない。はやぶさが世界的に注目される中、衛星ビジネスも少しずつではあるが立ち上がってきている。今年こそ、こうしたわが国のインフラ・システムの世界市場への輸出を本格化させられるよう、官民一体となった取組みに期待したい。
第122回 タブレット端末の操作をなめらかにするコーティング技術
第122回 タブレット端末の操作をなめらかにするコーティング技術提供:アップル ハードディスクドライブ(HDD)大手の日立グローバル ストレージテクノロジーズの堀家正充社長はある席で、「デジタルデータは年率55%で増え続けており、その中心を担うHDDはクラウド・ストレージの増大で今後も市場を拡大していくだろう。そしてそのクラウド・ストレージを押し上げるキードライバーの一つが、iPadなどのタブレット端末だ」と語った。
タブレット端末の操作をスムースに行うためのコーティング技術
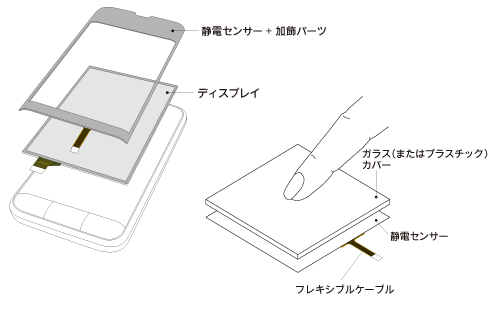
ピンチアウト(提供:アップル) iPadでは、画面上のアイコンなどを指先で軽くつつく「タップ」、画面に指をつけたまま、上下左右にずらす「ドラッグ」、指の腹で画面上をはじくような「フリック」、二本の指で画面を押さえ、その指の間隔を広げる「ピンチアウト」、二本の指で画面を押さえ、その指の間隔を狭めてものを挟むような「ピンチイン」といった動作があるが、これら動作をスムーズに行い、またガラス基材表面の耐久性を高める技術の一つが、コーティング技術である。
その代表的なコーティング技術は、基材にフッ素樹脂塗料などをディッピングまたは蒸着し、滑りの良さや指紋除去性を高めるもの。
たとえばダイキン工業が先ごろタブレット端末の市場拡大に対して増産を決めたフッ素樹脂コーティング剤「オプツールDSX」を見ると、その優れた撥水・撥油性により、タブレット機器のタッチ・スクリーンの基材であるガラスなどの表面にコーティング処理することで指紋汚れが付くのを防ぐ「防汚性」、タッチ操作をなめらかにする「表面滑り性」を付加できるほか、さらに10nm以下の極めて薄い皮膜で視認性や反射率などの光学特性にほとんど影響を与えないため、ディスプレイの見やすさを損なわないという。
OH基がガラス基材のSi基に吸着、効果を持続(提供:ダイキン工業) 同フッ素樹脂コーティング剤は、水酸基(OH基)を介した強固な化学結合によりガラス基材のSiに吸着、コーティング膜がはがれにくいことから、長期間それらの効果が持続する。
タブレット端末は、15年には10年の約10倍となる800万台の予測
こうした防汚性・潤滑性コーティング剤はダイキン工業のほかに、旭硝子や信越化学工業などが手がける。
調査会社のシード・プランニングでは、タブレット端末の2015年までの市場規模予測を実施、タブレット端末の日本市場は2台目のニーズをとらえていたネットブックと個人向けのノートパソコンの需要、業務用端末としての需要を取り込み、2015年には2010年の約10倍となる800万台の市場となると予測している。ここではタブレット端末の再表層の技術だけを取り上げたが、使われる部材は多く、iPadでもすでに、液晶ディスプレイや携帯電話高層波処理、フラッシュメモリー、水晶振動子などで日本メーカーが参入している。タブレット端末では、タッチパネルやバックライト、バッテリー、アルミフレームなどとその材料および加工技術など、わが国の強みである技術は多い。是非とも拡大基調にある市場に、その技術優位性をもってさらに食い込んでいってほしいものである。
第123回 モーターのトップランナー基準で、産業界のさらなる省エネ化の推進を!
第123回 モーターのトップランナー基準で、産業界のさらなる省エネ化の推進を!提供:日立産機システム 経済産業省は1月24日の総合資源エネルギー調査会第16回省エネルギー基準部会を開催、温室効果ガス削減に向け自動車や家電製品、OA機器などのエネルギー消費効率の改善をメーカーに求める「トップランナー基準」について、現行の対象機器は基準の見直しを進めるほか、新たに主要な産業用モーターである三相誘導モーターを対象機器に追加することを決めた。
「トップランナー基準」対象機器に三相誘導モーターを追加
トップランナー基準は1999年に導入された省エネ規制で、商品化された製品で最もエネルギー消費効率の高いもの(トップランナー)を基準として、機器メーカーにその効率を達成する省エネ型製品の製造を求めるもの。現在、自動車や家電製品、OA機器など23品目を対象に、品目ごとにエネルギー消費効率の目標基準値、製品区分、目標年度、基準値達成の判定方法などを規定。目標年度に基準値を達成できなかったメーカーに対しては、経済産業大臣による勧告や社名の公表、命令などの措置に加え、罰金が課せられる(省エネ法による)。トップランナー基準導入により、たとえばルームエアコンでは導入前に比べエネルギー消費効率を68%改善しているという。
三相誘導モーターはブラシや整流子がなく堅牢構造でメンテナンスフリーで使えること、周波数と電圧の制御(VVVFインバータ制御)が可能なことなどから、国内で年間1,000万台弱が出荷、1億台を超える機器が国内で普及しポンプ、圧縮機、送風機から、工作機械、新幹線に至るまで、各種産業用機械に幅広く採用されている。しかし、三相誘導モーターによる電力消費量は、わが国における産業用電力消費量(約4,900億kWh)の約75%と推計されるほか、電力消費量全体(約1兆kWh)の50%超を占める。
米国では1997年に施行されたエネルギー政策法(EPAct)に代わり、2010年12月19日にはエネルギー独立安全保障法(EISA)が施行され、その中で米国内で製造・輸入されるモーターの効率が規制、これまでEPAct(IE2レベル)効率が適用されていた機種にはPremium(IE3レベル)効率の使用を、規制対象外だった機種にはEPAct効率の使用を義務付けており、効率基準を満たさないモーターとモーターが組み込まれた製品が販売された場合にはペナルティーが課せられる。欧州でも同様の高効率化が進んでいるのに対し、わが国は、ロシアやインドとならんで効率規制が取られておらず、トップランナー基準によって三相誘導モーターの標準品から高効率品への移行を促すことで、産業分野での省エネ化の推進をねらうもの。
メカニカル・ロスを抑制し、さらなる省エネ化へ
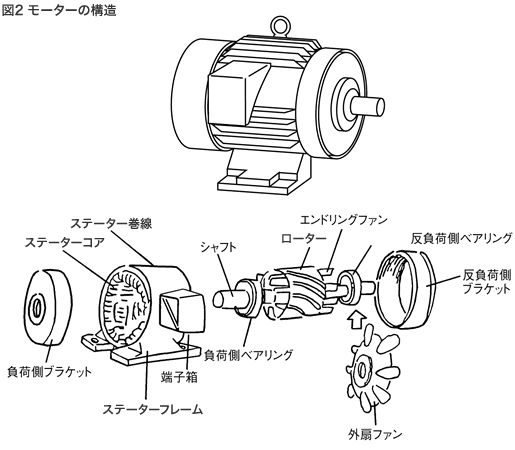
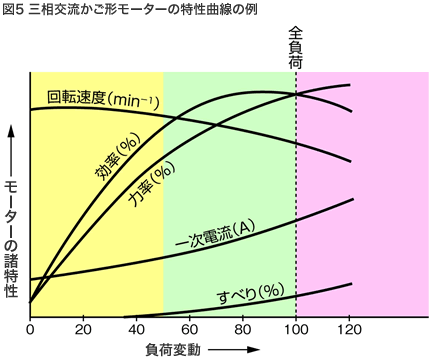
モーターの効率は一般的に次のように表される。
効率(%)=出力/入力×100=(入力―損失)/入力×100
つまり出力=(入力-損失)から、損失は(入力-出力)として定義される。損失は、モーター内で熱、振動、音などのエネルギーに変わってしまうもので、銅損、鉄損などの電気的な損失と、ベアリングの摩擦損失や冷却ファン損失による機械的な損失などからなる。
電気的な損失に対しては、高磁束密度鉄心の開発や電線充填量の高密度化などで高効率化が図られている。メカニカルな損失に対しては、軸受ハウジング部の冷却性能向上により軸受の発熱を抑えたり、軸受に封入するグリースの配合を変えるなどで低トルク化を図っている。
仮にすべてのモーターが高効率モーターに転換された場合、わが国電力消費量全体の約1.5%にあたる年間約155億kWh、温室効果ガス排出量(12億8,200万t)の約0.4%に相当する約500万t-CO2 が削減されるという。トップランナー基準対象機器への三相誘導モーターの追加により、ベアリング技術などメカニカル・ロスをなくす技術開発が促進され、産業界のさらなる省エネ化が図られるよう期待したい。
第124回 建設機械の省エネ化がグローバルで進展
第124回 建設機械の省エネ化がグローバルで進展ハイブリッド油圧ショベル(提供:コマツ) 日本建設機械工業会が先ごろ発表した2010年の建設機械出荷額は、前年比59%増の1兆8,489億円と、2年ぶりのプラスとなった。中国をはじめ新興国向けを中心に輸出が2倍近くに急増、特に油圧ショベルが前年の2.1倍に増え、出荷額を押し上げた。そうした中、新興国向けを含めたグローバルでの建機の省エネ化が進んでいる。
建設機械におけるシール、作動油の省エネ化
建設機械ではディーゼルエンジンを回して油圧ポンプを駆動し、油圧作動油をブームシリンダやアームシリンダ、バケットシリンダといったアクチュエータに送り、車体各部を作動させる。油圧作動油を用途別に見ると建機向けが5割強というから、油圧機器もまたその主要用途は建機と言えるだろう。油圧機器に使われるパッキンの某メーカーでは、業績がリーマンショック前の9割近くまで回復、生産をスリム化していたため受注の急増に対してうれしい悲鳴を上げているという。
油圧シリンダ(提供:KYB) さて、油圧機器の省エネ技術を見ると、350気圧といった高圧シリンダにおいて、油圧作動油の密封性を高めつつ作動時の摩擦を少なくするPTFE製のシールリングと合成ゴム製Oリングを組み合わせたロッドシールなどが用いられている。シールの摺動面にダイヤモンドライクカーボンコーティングを施して、さらに低摩擦化し省エネ化につなげようという取組みも進められている。
また、油圧作動油でも省エネ化が進められている。高粘度指数(高VI)基油と非金属系の添加剤を使うことなどで、低温における始動トルクが小さく動力損失を軽減できるほか、高圧・高温化でも配管詰まりの原因となるスラッジの発生を抑え、エネルギー損失を抑えることができるという。
油圧機器とモーターのハイブリッド化による省エネ化
こうした油圧機器におけるメカニカルな省エネ化の取組みの一方で、油圧機器とモーターとのハイブリッド化による省エネ化も進められている。
コマツでは先ごろ、新型ハイブリッド油圧ショベルを開発、すでに日本で販売を開始し今後は北米、中国、中南米、東南アジア、欧州などへも販売を拡大する予定だ。独自ハイブリッドシステムにより、車体旋回の減速時に発生するエネルギーを旋回電気モーターで電気エネルギーに変換してキャパシター(蓄電器)に蓄え、発電機モーターを通じてエンジン加速時の補助エネルギーに活用することで、大幅な燃料消費量の低減を実現する。また、必要な吐出量を確保しながら、日米欧の排出ガス規制に対応したエンジンの回転を低く抑えるエンジン・ポンプマッチング制御を採用、燃費効率の良いところでエンジン回転とポンプの吐出量をマッチングさせることで燃費低減を図るという。
世界中の建設現場で使われる建設機械では、早くから生分解性の作動油を採用するなど環境対応への取組みがなされてきたが、さらに動力損失や使用電力を抑える技術的取組みが強まってきている。わが国の得意とする油圧ショベルなど建設機械において、わが国の誇る省エネ技術が搭載されることによって、建設機械の市場拡大が促進されるよう期待したい。
第125回 難削材の加工機械・技術が注目
第125回 難削材の加工機械・技術が注目高精度・高効率複合加工機(提供:森精機製作所) 日本工作機械工業会は先ごろ、2010年の工作機械の受注額が前年比2.4倍の9,783億円と大幅に増加したと発表、2011年の受注については3年ぶりの1兆円台となる1兆1,000億円となる見通しを打ち出した。中国などアジアをはじめ、欧州、北米、日本ともに需要が回復しているが、自動車や航空機などの精密部品、特に難削材の加工に適した日本の工作機械・加工技術が注目されているという。
航空機の機体材料はアルミニウムが大半を占めていたが近年は軽量化による燃費向上を目的に、CFRP(炭素繊維強化プラスチック)の比率が構造部材重量の半分を占めるまでに多用され、CFRPと相性が良いチタン合金も様々な部位で使用されるようになった。チタン合金は軽く、強く、錆びないという特性を持つ反面、熱伝導率が低く、靭性が高く、切削速度を上げると急激に工具摩耗が起こるため、難削材と言われる。このほか燃焼室回りに使用される耐熱性の高いインコネルなどのNi基合金の材料も同様に難削材である。
一方、航空機部品では軽量・高剛性化を図るべく、ねじなどによる締結方法をとらないため部品単体の形状が複雑となり、旋削機能も含めた高剛性で高精度な5軸複合加工機が必要となる。5軸複合加工機1台に工程集約できるようになり、工程間の搬送や段取り時間の削減、加工精度のバラツキを抑え、航空機部品の生産性向上に大きく寄与している。
5軸制御マシニングセンタ(提供:牧野フライス製作所) こうした難削材の加工に対して、たとえば牧野フライス製作所の5軸制御マシニングセンタ「T2/T4」では、高トルク(1000/1500N・m)の主軸により、重切削での耐久性と高速性、高精度といった高能率加工を実現、また200L/min(7MPa)のクーラントが切屑を速やかに除去するほか、難削材の重切削加工で発生する振動を高剛性の本体構造により低減することで、チタン合金の加工時間を従来の1/4に減らし、工具寿命を2倍に高めているという。
こうした難削材に対応する高剛性、高精度の工作機械構造が工夫される一方で、工具においても難削材の加工に対応する技術も進んできている。
提供:三菱マテリアルツールズ 三菱マテリアルでは先ごろ、高い比強度を持つ反面、炭素繊維が高強度であるため工具寿命が極端に短く、積層体構造であるために穴加工時にデラミネーション(層間剥離)が発生しやすいCFRPや、CFRPとアルミニウム合金の重ね板の穴加工に特化した「MCS形」を開発した。切刃デザインと新開発の多層微粒CVDダイヤモンドコーティングの採用により優れた穴精度と長寿命を実現したほか、独自の素材成形技術によるユニークなクーラント穴を付加することで、特にCFRPとアルミニウム合金の重ね板加工をする際の切りくず排出性が向上、高い穴精度を実現している。
日立ツールの「エポックDスレッドミル」では結晶粒子がさらに微細化したSi系ナノコンポジットコーティングをPVD(物理気相成長)処理、3800HVの硬度と1200℃の耐酸化温度を実現、1本の工具で高硬度材における下穴+ねじ切り加工を可能にしている。
航空機だけでなく、無害で耐摩耗性、耐食性、人体との親和性が要求される人工関節などのインプラント製品にも、コバルトクロム合金、チタン合金、セラミック系のジルコニアなどの難削材が用いられる。人工骨、人工歯などインプラント製品もまた形状が複雑なことから、工作機械にはCAMによる加工プログラムや、難削材に対応した機械剛性、高速、高精度加工が求められる。森精機製作所では旋削とミーリングを融合した高精度・高効率複合加工機「NT1000」を用いて、これまでエンドミル加工していた人工大腿骨コンポーネントのR 形状を、CBN砥石を使用して加工することで加工時間を大幅に短縮。難削材の加工にもかかわらず、エンドミルに比べて工具寿命が長く、工具費用を大幅に抑えることができるほか、ワークを2個取り付けることで加工効率が向上した、としている。
航空機、医療機器など複雑形状の難加工が必要とされるアプリケーションが増えてきている。中国、韓国などアジア勢の工作機械の生産が拡大してきているが、わが国の得意とする高精度・高速・高剛性で複合加工に対応するマシニングセンタや難削材加工での高能率化を実現するコーティング工具などの高付加価値技術で差別化を図り、工作機械産業のさらなる市場拡大に努めてほしい。
第126回 nano tech 2011/ASTEC 2011に見る、表面改質/計測・評価技術
第126回 nano tech 2011/ASTEC 2011に見る、表面改質/計測・評価技術 「nano tech 2011 国際ナノテクノロジー総合展・技術会議」や「ASTEC 2011 国際先端表面技術展・会議」、「METEC2011 第40回表面処理材料総合展」など9展が2月16日~ 18日、東京ビッグサイトで同時開催された。
グリーンナノテクノロジーでDLCなど薄膜技術を展示
今回の9展示会共通テーマは「グリーン・ナノテクノロジー 10-9がつくる環境力」。10のマイナス9乗メートルはナノメートルで、グリーン・ナノテクノロジーとは、ナノメートル(nm)レベルの薄膜や微粒子を使って、自動車関連の次世代二次電池、LED照明、新エネルギー技術、土壌・水質浄化など環境問題の解決に役立つ製品を創出する技術。
今回は主にASTEC2011 やMETEC2011でナノレベルの表面改質技術が、nano tech 2011でカーボンナノチューブなどのナノ粒子や、微粒子や薄膜の計測・評価技術が展示された。
出展されたグリーン・ナノテクノロジーとしては、たとえば潤滑剤に頼らずフリクションを低減することで省エネに、耐摩耗性を高めることで省資源化につなげるDLC(ダイヤモンドライクカーボン)膜がある。
接触角が大きく水を弾く撥水性ICF(提供:ナノテック) ナノテックでは単に硬質で摩擦係数が低いDLCにとどまらず、DLC薄膜の特性を物性により分類したICF(Intrinsic Carbon Film:真性カーボン膜)を開発、たとえばクロムめっきの代替や各種金属溶出防止膜として、高硬度、低摩擦係数、耐摩耗性で、めっきからの代替を可能にすべく大面積の成膜が可能な環境調和型ICFや、フッ素(F)ドーピングとコーティング条件の工夫で、水を弾く特性を持たせた撥水性ICFなどを提起している。
プラズマイオンアシストでは微細複雑形状に成膜でき流路側面、底面に均一な成膜が可能で、高い耐食性と金と同等の接触抵抗を持ち、燃料電池セパレーターなどへの適用が可能な高導電性DLCなどを出展した。
薄膜の計測・評価技術
DLCなど薄膜の計測・評価技術としては、0.01nmの押し込み分解能を持つためバルク材の影響を受けずに薄膜自体の機械的強度を測定できるナノインデンターなどが、東陽テクニカから展示された。
この機械的特性を非接触で測る手法としてまた、DLC薄膜からの反射光の偏光状態から、硬さや密度と相関性がある膜の屈折率や消衰係数が求められる分光エリプソメータなどの展示も見られた。
また、先の撥水性ICFなどのような膜の撥水性を見る手法として、解析ソフトウェアと組み合わせて、動的接触角(拡張/収縮、滑落・界面張力の測定や表面自由エネルギー解析も可能とする各種接触角計が、協和界面科学から出展された。
三次元顕微レーザーラマン分光装置(提供:東京インスツルメンツ) DLC薄膜に照射した光の散乱光(ラマン散乱光)を分光測定するラマン分光装置も展示、DLC膜の構造解析の中でも、DLC膜の諸特性に大きな影響を及ぼす水素濃度を把握しDLC薄膜を作り分けるのに有効な手法として、提案された。
第127回 ベアリングの大型化で期待されるメカ技術
第127回 ベアリングの大型化で期待されるメカ技術提供:Vestas社 航空機や建設機械など大型機械、さらにはそれらを加工する大型工作機械の需要が増加してきている。また、新興国の経済成長に伴う医療・福祉の向上などから、医療機器、中でもがんの早期発見につながるCTスキャン装置の市場が、グローバルで拡大基調にある。
ガントリの大口径化とともに大型化するCTスキャン用ベアリング
世界市場でのこうした大型構造物の増加に伴い、それら機械装置の回転機構を支えるボールベアリングもまた、大型化してきている。
こうした大型軸受の需要拡大に対して、ベアリングの追加加工を手掛ける日本軸受加工では、大型ベアリング専用の工場設置や設備投資を進めている。
ベアリングが高速回転することで温度上昇が起こり、軸受材料が熱膨張して適正なラジアルすき間が維持できないことがある。こうした事態に備えた軸受ユーザーからの委託により日本軸受加工では、軌道面をミクロン単位で研磨し、すき間の手直しを行っている。
また、高速回転に伴う発熱対策として、工作機械主軸の組み合わせアンギュラ玉軸受の間座の給油孔の加工なども、工作機械の仕様に合わせて行う。
同社の大型ベアリングへの加工は、大型工作機械のテーブル用ベアリングなどで実績がある。たとえば、独シェフラー社で外径4,000㎜強まで対応するアキシアル・ラジアル複合ころ軸受などがラインナップされている、あれである。
同社の伊藤正憲社長は、「CTスキャン装置のベアリングは現在、内径900㎜程度のものが多いが、内径1m超まで大型化した設計がなされてきている」という。
提供:NTN
CTスキャナ用低振動軸受(提供:NTN) CTスキャン装置では、患者が横たわったベッドがガントリ部に進入、その際にガントリ部が患者の周りを回転してX線撮影する。このガントリ部が大口径化することで、欧米人のように体格の大きな患者でも検査できるようになる。また、人体の患部がガントリ部の中央に位置するときに鮮明な画像が得られることなどから、大口径化により心臓を診る時などにはベッドをオフセットさせ患部が中央にくるよう位置決めできるようになる。確かに、ガントリの大口径化とともにベアリングは大型化する傾向にあり、精密画像を得るために振動を抑制したNTNの「CTスキャナ用低振動軸受」では、軸受外径が1,200㎜に及ぶ。
風力発電機では外径1,580㎜のベアリングも
また、風力発電機では、出力1.5MW級で外径1,000㎜程度だったベアリングが、国内最大級の出力2.4MW風車向けのベアリングでは外径1,580㎜に及ぶ(NTN)。
こうした大型ベアリングの加工の需要に対して、日本軸受加工では大型研削盤を導入、伊藤社長の設計により、外径、内径を同時に研削できる機械や、軸受の姿勢を90°変えられ、複合加工ができる機械なども稼働しているという。
風力発電機を開発する某社によれば、「風力発電機の高出力化に伴いそのベアリングもかつてない大型化が進展、経験のない大型化から予期せぬ故障もあった」としているが、この風力発電機ひとつをとっても、実際の使用にあたっては仕様に合わせた各種の加工や、使用条件に合わせた潤滑技術、潤滑剤を異物から守り機能させるオイルシールの技術、長期耐久性を実現する軸受の高清浄度鋼技術など、複合的な取り組みが必要とされる。もちろん1社のみで対応できることではない。先の日本軸受加工でも、熱処理など表面改質や、内・外輪への歯切り加工などは協力企業に外注するという。新しいアプリケーションには、既存の技術ネットワークだけでなく、新たな技術リソースも模索し、活用していかなくてはならない。
かつてないベアリングの大型化に伴う経験のない使用に対しては、中小企業の光る技が活躍する場面が、まだまだ多そうである。
第128回 PV EXPO 2011に見る機械加工技術
第128回 PV EXPO 2011に見る機械加工技術 「PV EXPO2011 第4回国際太陽電池展」が3月2日~4日、東京・有明の東京ビッグサイトで開催された。同展は、太陽光発電業界国内最大の国際商談展示会として、世界各国の太陽光発電システムのほか太陽光発電関連の製造装置、部品・材料、検査・測定・分析装置などが多数展示された。
太陽光発電協会がまとめた2010年の国内太陽電池セル・モジュールの出荷統計によると、2010年の国内総出荷は発電能力ベースで前年比205%の991,920kWとなり、2年連続で対前年2倍増となった。材料別では、結晶シリコン系(Si単結晶+Si多結晶)が2,090,156kW(前年比172.3%)、シリコン薄膜系が269,522kW(前年比186.3%)、その他が77,348kW(前年比262.8%)だった。材料別の構成比はSi多結晶が50.8%、Si単結晶が34.9%、Si薄膜が11.1%だった。
結晶シリコン系太陽電池の製造工程と主な評価機器(提供:堀場製作所) この市場の大半を占める結晶シリコン系の製造工程を見ると、大まかには電着バンドソーなどによりシリコンインゴットをブロックに切断した後、それをウェハにスライス切断(ウェハリング)し、ウェハを洗浄、続いてテクスチャーを形成し、その後pn接合形成(熱拡散)→酸化膜除去→反射防止膜形成→電極形成→硬化/焼成→封止という工程をとる。
太陽電池市場における競争がグローバルで激化する中、コスト競争力向上につながる生産性を高める加工技術が要求されている。
電着ダイヤモンドワイヤソー(提供:旭ダイヤモンド工業) ウェハリングを行う加工技術としては、たとえば旭ダイヤモンド工業が電着ダイヤモンドワイヤ「エコメップ」を出展していた。これは、高張力ワイヤにダイヤモンド砥粒を「電着」と呼ばれるめっき技術で付着させた固定砥粒工具。従来の石油系研削油と研磨材を用いて鋼線で切断する遊離砥粒方式に比べ、このシリコンのほか、LED基板であるサファイヤなど硬脆材料をスライスする切断時間を約1/3に短縮できるほか、切り代や加工歪みが低減され歩留まり向上が期待できるという。また水性切削液を使用するため切り粉の回収や再資源化が行え、トータルコストダウンが図れる。
クラレアクアでは、こうしたワイヤソー(ウェハリング)工程でシリコンの切り粉などが混じった切削液をフィルターで分離し、切削液を回収しリサイクルする機器を展示した。切削液が再利用でき加工にかかる費用が低減できることや産廃費用を圧縮できることなどから、装置を導入しても1年程度で償却でき、その後はそのままコスト削減に直結するとしている。
結晶系太陽電池の構造(提供:産業技術総合研究所) 結晶系太陽電池では、モジュール用ガラスのセル表面の反射率を低減し、受光した太陽光を閉じ込める(受光量を増やす)ため、エッチング装置(テクスチャリング装置)を使って、ウェハ表面に凹凸構造(テクスチャー)を形成する。
さらにこのテクスチャー形成に加えて、光の表面反射をより低減させる目的で、プラズマCVD装置を用いて、セル表面に複数の薄膜層からなる反射防止膜を形成する。
テクスチャーの三次元測定(提供:オリンパス) PV EXPOではこのテクスチャリング装置(ワイエイシイなど)や反射防止膜成膜装置(島津製作所など)などが出展されたほか、テクスチャー構造の観察・評価のための三次元形状測定器(オリンパスなど)や、反射防止膜の評価分析サービス(コベルコ科研など)などもアピールされた。
太陽電池の発電効率を高めるための加工技術は多様で、それぞれに計測評価の技術がある。太陽電池の市場規模は2010年の2兆円強に対して、2025年には4倍以上の8兆円強が見込まれているが、PV EXPO2011の展示を見て、こうした要素技術の急速な開発・実用化により市場規模が押し上げられていくものと実感できた。
第129回 東日本大震災の被害者救済と復旧を願う
第129回 東日本大震災の被害者救済と復旧を願う3月11日14時46分に始まった「東日本大震災」による被害が拡大している。国内観測史上最大のマグニチュード9の大地震と、波の高さが7mにも及んだ津波によって町は防備するまもなくのみこまれ、家屋が流され、火災に見舞われた。はじめに、震災で亡くなられた方々のご冥福を祈りたい。また、一人でも多くの方が救済されることを願っている。
記者は地震発生時、東京にあったため、JRおよび私鉄の全線が運行を止めたことで帰宅難民になった程度に過ぎない。しかし、幾多の震災を経て防災システムが整備されてきたとはいえ、あらゆる地震に対して万全の備えなどないということは実感できた。
その後の数回の余震を考えると、二次被害を抑えるべく電車を止め、線路の異常や車輪の浮き上がり、架線の摩耗など、点検を進め復旧に備えた鉄道関係者の判断を讃えたい。鉄道の安全神話はまずまず守られたといってよいのではないだろうか。
一方、原子力発電所の対応はどうだっただろうか。東京電力福島第一原子力発電所1号機が爆発し、周辺住民の約100名が被爆した。原子力発電機は放射性物質を①核分裂生成物を閉じこめた「ペレット」、②ペレットからじわじわと拡散する核分裂生成物を封じ込めつつペレットから放出された熱を外側の冷却材に逃がす「燃料被覆管」、③冷却材が封じ込められた一次圧力バウンダリ、④捨てる冷却材を封じ込める「原子炉格納容器」、⑤「原子炉建屋」という五つのバリアが機能する、安全なシステムのはずだった。このうち、高温・高圧下にあるペレットと燃料被覆管には特に注意が払われる。
ペレットは酸化ウランの粉末を圧縮して焼結したセラミックスでできており高温に強いが、薄い肉厚の金属のチューブである燃料被覆管はペレットの熱を素早く外側の冷却材に伝えることで自身が加熱されるのを防いでいる。今回は原子炉内の水位が下がり炉心が露出、燃料の温度が上昇し燃料被覆管が溶ける「炉心溶融」が起こり、水素爆発に至ったと見られる。
ここに至る経緯としては、冷却機能を補うはずのディーゼル発電機が作動しなかった、さらに冷却水を補充するためのポンプ車などの手配も遅れたようだ。こちらは原発ルネッサンスと叫ばれる中、強く求められる安全信頼性の回復に応えられなかった。今回の対応を振り返りながら、今後より徹底した安全対策が図られるよう生かしてほしい。
また、地震発生後30分も経たないうちに大津波が発生し、自動車よりも速いスピードで瞬く間に町をのみこんでいった。今回の未曾有の津波に対して対策の立てられようもなかっただろうが、これまでも声高に繰り返されているとおり引き続きの津波対策としては、高い堤防および防波堤の設置などハード面と、地震発生から津波発生に至るまでの早期の津波情報の提供や避難対策の充実などソフト面のさらなる強化が、国と地方自治体の課題と言えよう。
専門家によれば、今後3ヵ月はマグニチュード8の可能性もある大きな余震への注意が必要、としている。引き続き、できうる限りの防災対策を施していかなくてはならない。これ以上の人命を危険にさらすことはあってはならない。家屋や工場、生産施設などの損壊を招いてはならない。
あらためて被害に遭われた方々に追悼の意を表するとともに、今後一人でも多くの人命が救われることを、また被災地の少しでも早い復興がなされることを、ただただ願うばかりである。
第130回 メンテナンス活動から、ものづくり産業の復活・拡大へ
第130回 メンテナンス活動から、ものづくり産業の復活・拡大へ東日本大震災に伴う津波で建物が全壊した宮城県南三陸町志津川のガソリンスタンドで先日、地下タンクから足こぎ式ポンプを使ってガソリンをくみ上げる作業が行われた。地下タンクに吸引ホースを差し込んでペダルをこぐと、3回転で1Lのガソリンをくみ上げられるという。緊急車両や避難所の発電機などへの給油がなされた。
津波被災地のスタンドの多くで給油機が流失しているが、地下にあるタンクは破損していないものも多い。国内石油元売り最大手のJX日鉱日石エネルギーのENEOS系スタンドでも、東北地方にあるスタンドのうち1,000件程度の地下タンクで漏洩がないことが確認できており、系列のメンテナンス企業が復旧工事に取りかかり始めたという。
ガソリンスタンドの構造 ガソリンスタンドには地下5m程度の深さにそれぞれレギュラーガソリン、ハイオクガソリン、軽油、灯油のタンクが埋設され、各々から配管がなされ、燃料をくみ上げ給油する計量機(給油機)に接続されている。
今回の津波被害により地上にある給油機は流されているものの、破損していないタンクであれば配管工事と給油機設置で早い時期にガソリンスタンドを再開できるという。依然、東北地方での燃料供給が逼迫する中、メンテナンス作業が急がれる。
こうしたガソリンスタンドをはじめ、これまで円滑に稼働しているときには陰の立て役者であったメンテナンス事業の活躍が今まさに期待されている。原子力発電所の事故収拾は最たるものであろう。
メンテナンス作業をはじめ、冒頭に紹介した足こぎポンプによる給油活動に見るように、また自動車部品メーカーなどの工場復旧に向け自動車メーカーや工作機械メーカー、計測器メーカーなどが支援に動き、徐々にではあるが操業が再開されてきているように、できることから取りかかり、我々は前進していかなくてはならない。
震災による国民生活、産業界への打撃は確かにはかりきれないが、そうした先行きの不透明性からシュリンクするのではなく、一人一人が希望を持って、アクティブな活動を再始動したい。わが国のものづくり産業の復活、さらには成長に向けて。