第101回~第110回
第101回~第110回第101回 わが国技術の発信で、インフラ関連プロジェクトの獲得を!
第101回 わが国技術の発信で、インフラ関連プロジェクトの獲得を!リニアモーターカー(提供:JR東海) 経済産業省( http://www.meti.go.jp )は、本年6月策定の「産業構造ビジョン2010」で提言されたインフラ・システム輸出に関する総合的な戦略を官民連携で策定する目的で、「インフラ・システム輸出部会」を設置した。鉄道、航空宇宙、原子力、水ビジネスなどの主要団体トップや有識者が集まって、インフラ関連産業の海外展開のための総合戦略やインフラ・システム輸出を進めるにあたっての官民連携のあり方などについて意見交換していく。
産業構造ビジョン2010では、2020年までに海外分を含めて19兆7,000億円の新市場と18万7,000人の新規雇用を創出する目標を掲げている。その中でインフラ・システム輸出は重要な戦略分野の一つに位置づけられており、政府がインフラ関連プロジェクトの受注などに積極的に関わるべく、今回インフラ・システム輸出部会が設置された。
たとえば鉄道分野では、米国(全長1300kmのカリフォルニア高速鉄道網など)やメキシコ、ベトナム、中国、インドネシア、タイなどで高速鉄道の建設が計画されている。鉄道車両はCO2排出量が少ない大量輸送手段として世界的に重要性が見直されているが、自動車などによる輸送を鉄道で代替する「モーダルシフト」はオバマ政権が5年間で130億ドルを投入する方針を打ち出すなど、特に米国で急速に進み、新幹線(N700Iブレット)やリニアモーターカーなど日本の高速車両技術が求められている。
新幹線を見ると最新のN700系で時速300kmと高速化が加速する一方、この環境対策からは、安全性を確保した上でのメンテナンス周期の長期化が図られているが、鉄道の輸出においても、新幹線の開発で培った、安全で環境に優しい高速化の技術を全面に打ち出す必要があろう。
たとえば鉄道車両用軸受のうち車軸用軸受は、軸を直接支持し、また線路からの振動が直接伝わる過酷な環境下で使われ、かつ転がり疲れ寿命の長寿命化が求められている。そのため欠陥につながる介在物の少ない高清浄度鋼が使用されているほか、潤滑寿命の延長からは封入グリースの改良とともに、樹脂製保持器を採用して摩耗粉を抑制している。主電動機(モーター)軸受には60~90kmで中間給脂が行われているが、120万kmへのメンテナンス周期延伸のニーズに対し、長期グリース補給を維持できるグリースポケット形状などの工夫がなされている。センサー組込みによる運行中の軸受のモニタリングシステムなども、メンテナンス周期の長期化や安全性向上では重要な役割を担う。
このほか、列車の走行に必要な電流を流す電気的特性、パンタグラフとの接触力変動が少ない良好な接触を保つための機械的特性、摩耗しにくく破断することのない材料的特性が求められるトロリ線や、機械的特性や摺り板が摩耗しにくく破損せずトロリ線を摩耗させない材料的特性、風を受けることで発生する揚力が適切で、風を切ることによる騒音が小さいなどの空力的特性が求められるパンタフラフなど、高速車両の信頼性を高める技術は枚挙にいとまがない。すなわち、鉄道の輸出とは、これら車両の機械技術や安全で省エネな運行・管理のためのエレクトロニクス技術などを統合して提供する必要があるということだ。
ここにきて新幹線の技術をもとに製造された中国の高速鉄道の輸出が加速してきているようだが、日本が1964年以来の安全で信頼性の高い高速化技術を着実に積み上げてきたのに対して、中国は10年程度の経験しか持たない。コストはいざ知らず、統合力では圧倒的に日本がリードしているはずである。
これは鉄道に限らず原発や航空宇宙、水ビジネスなどでも同様であろう。多岐にわたる機械技術や電気・電子技術が集積されたこれら産業の輸出において、いかにわが国技術の優位性を前面に打ち出してプロジェクトを獲得し、先述の市場および雇用の創出につなげていくか、今回誕生した経産省インフラ・システム輸出部会の今後の取組みに、強く期待したい。
第102回 ラベリング制度の普及で、タイヤの安全性向上と低燃費化技術に拍車
第102回 ラベリング制度の普及で、タイヤの安全性向上と低燃費化技術に拍車提供:日本自動車タイヤ協会 自動車のタイヤ性能に関するラベリング制度の導入が世界的に進んできている。本年1月に運用を始めた日本に続き2011年には韓国で、2012年には欧州で導入が予定されているほか、米国でも導入が検討されている。同制度の性能要件であるタイヤの低燃費化への要求が新興国も含めて強まってきている。
タイヤの燃費への寄与率を10%と仮定した場合、転がり抵抗を20%低減したとすれば自動車の燃費は2%向上する計算となる。このため近年タイヤに対しても低燃費化の要求が高まっていることから、各タイヤメーカーではこれまで独自基準の性能評価による低燃費タイヤを販売してきた。これに対しタイヤラベリング制度は、統一された試験方法により実証されたタイヤ性能を消費者にわかりやすく示し、低燃費タイヤの普及促進を図るねらい。国内では日本自動車タイヤ協会( http://www.jatma.or.jp )が本年1月から業界の自主基準として乗用車用夏用タイヤを対象に「低燃費タイヤ等普及促進に関する表示ガイドライン(ラベリング制度)」の運用を開始している。
同制度では、低燃費を示す転がり抵抗係数(RRC、単位N/kN)を
(1)グレードAAA:RRC≦6.55
(2)グレードAA :6.6≦RRC≦7.7
(3)グレードA :7.8≦RRC≦9.0
(4)グレードB :9.1≦RRC≦10.5
(5)グレードC :10.6≦RRC≦12.0
の5等級で、制動の安全性を確保するウェットグリップ性能(G、単位%)を
(1)グレードa:155≦G、
(2)グレードb:140≦G≦154
(3)グレードc:125≦G≦139
(4)グレードd:110≦G≦124
の4等級で表示。転がり抵抗係数は「JIS D4234(乗用車、トラックおよびバス用タイヤ-転がり抵抗試験方法-単一条件試験および測定結果の相関): 2009(ISO28580)」により、ウェットグリップ性能は「EU 規則 Wet Gripグレーディング試験法(案)(TEST METHOD FOR TYRE WET GRIP GRADING (C1 TYRES))」により評価、ウェットグリップ性能110以上(グレードa~d)、転がり抵抗係数9.0以下の上位3等級(グレード AAA~A)を満たすタイヤを、「低燃費タイヤ」と定義している。
タイヤの転がり抵抗には、(1)走行時のタイヤの変形によるエネルギーロス、(2)トレッドゴムの路面との接地摩擦によるエネルギーロス、(3)タイヤの回転に伴う空気抵抗によるエネルギーロスがあるが、ゴム(粘弾性体)に加えられた力は、変形により熱に変換されエネルギーを消費してしまうことから、これらの要因のうち、タイヤの転がり抵抗にはタイヤ変形の影響が大きい。
これに対し横浜ゴムでは、タイヤの内部に貼り付けて自然と起こる空気漏れを抑制するインナーライナーに、樹脂の低透過性とゴムの柔軟性を高次元でバランスした従来品の5分の1の薄さの新素材を適用、タイヤの空気漏れによる転がり抵抗の悪化抑制と軽量化による燃費向上を図っているほか、接地摩擦によるエネルギーロスの低減からは、コンパウンドをナノレベルで解析、天然ゴム+低発熱ポリマーを適用し転がり摩擦抵抗を低減し低燃費性能を向上している。
提供:ブリヂストン また、ブリヂストンでは、ブロックを路面に水平に接地させトレッドショルダー部の無駄な変形を抑制したほか、従来のトレッドゴムに配合されていたカーボン同士が擦れ合ってエネルギーロスが発生していたのに対し、カーボン粒子をナノレベルで調整し分散、カーボン同士がぶつかり合って起こる発熱を抑制、エネルギーロスを低減し転がり抵抗を抑えている。
提供:日本自動車タイヤ協会 しかし一般的に、タイヤの転がり抵抗を低減すれば、濡れた路面での制動距離(ウェット制動距離)が伸びるというように、転がり抵抗係数とウェットグリップ性能はトレードオフの関係にある。つまり、適正範囲を超えて空気圧を上げたり材料技術などで転がり抵抗をやみくもに低減することは、トレードオフとなるウェットグリップ性能の低下、つまり自動車の安全性を損なうこととなる。そこで、転がり抵抗低減の一方で、タイヤのトレッドパターン(溝の形状)による排水性の改善など、ウェットグリップ性能の向上が図られている。
提供:日本ミシュランタイヤ たとえば日本ミシュランタイヤではセンター部に配置したストレートグルーブや独自のサイプ技術により、雨天時も優れた排水性とグリップ性能を発揮しているほか、横浜ゴムではゴムをしなやかにしてグリップ力を高めるオレンジオイルなどの配合により、ウェットグリップ性能を高めている。
タイヤによる燃料消費量低減の効果が大きいことから、ガソリン高の中国で価格が割高であるにもかかわらず低燃費タイヤが注目されるなど、その市場は確実に成長してきている。電気自動車においても自動車の安全性、操縦快適性などに関わるタイヤの役割は変わらない。むしろ、バッテリーやモータ・ジェネレータの負担軽減などからは、タイヤの転がり抵抗低減への要求は、より高まっていくことだろう。タイヤのラベリング制度が世界的に普及し、低燃費タイヤの需要が拡大していくなか、安全性を確保するウェットグリップ性能を向上した上での、タイヤの転がり抵抗低減のさらなる取組みに期待したい。
第103回 ACTA構想に技術製品の安全信頼性確保を期待
第103回 ACTA構想に技術製品の安全信頼性確保を期待 経済産業省( http://www.meti.go.jp )と外務省は8月16日~8月20日、米ワシントンで開催された模倣品・海賊版拡散防止条約(ACTA)の第10回関係国会合の概要を公表した。参加国は、我が国をはじめ、米国、EU、スイス、カナダ、韓国、メキシコ、シンガポール、豪州、ニュージーランド、モロッコ。今回の会合では、次回会合を本年9月に日本で開催し残された実質的論点を解決すること、署名の前に条約の全条文を公表することなどの合意をみた。
ACTA構想は、2005年に当時首相だった小泉純一郎氏が模倣品・海賊版拡散防止のための法的枠組みの必要性について発言したことを機にスタート、2008年6月には現在の11ヵ国が参加した関係国会合が開催、条文案をベースとした本格的な議論が始まった。そうした経緯からも、今回の会合でも、わが国がACTAの早期実現を目指し、今後も関係国との議論を積極的にリードしていく姿勢を示した。
模倣品・海賊版による被害は世界で年間80兆円に上り(世界税関機工および国際刑事警察機構資料より)、国際貿易に限定しても20兆円以上に達する(OECD資料より)という。ACTAが指摘しているのは、「模倣品は安全性や耐久性に問題を抱えているものが多くあり、こうした模倣品は誤って購入した消費者に危害を加える上に、企業の信頼を損なうおそれがある」ということである。模倣品が引き起こすおそれのある被害と商品分野の例として、加工精度や材料の品質が低劣なことによる装置・部品の故障・破壊の被害をもたらすベアリングや自動車部品を挙げる。
WBA京都設立総会(提供:日本ベアリング工業会) 実際にベアリングの分野では1990年代の終わりから、ブランド名を使用することでメーカー品と誤解を招きかねないようなベアリング製品がアジア、中近東、中南米、アフリカなどに多数流通、問題化してきている。これに対して、日本ベアリング工業会では、「こうした偽造品は、わが国ベアリングメーカーの知的財産権を侵害するばかりでなく、品質面で問題があるケースも多い。これらを使用した自動車や電気製品などは早期破損に繋がる可能性が高く、消費者や工場の作業者などを危険にさらすことになるほか、機械の突然停止による生産効率の低下、メンテナンスコストの増大など経済的な損失を招くことも少なくない」との危惧を表明、不正商品の生産拠点があると思われる中国に2000年11月末に第1次ミッションを派遣、以来2008年までに第8次ミッションを派遣し、中国政府機関に対して、不正なベアリングによる身体、生命への危険性を訴えながら、その製造・販売の撲滅に向け取締りの要請を行うなどの対策に努めている。
こうした努力が結実して海外の偽造品に対する抑止効果を発揮、偽造品の流通量は減少に向かってきていたが、2008年後半からの世界同時不況を契機に大量の在庫が発生したため、再び偽造品の製造が復活し始めたという。
一方、タイでは2005年ごろからタイ政府の強力なバックアップのもと、偽造品対策を始め、中国同様ミッションを派遣し、日本ベアリング工業会が現地で対策委員会を設け、偽造品の識別方法を伝授するなどして水際対策を強化、当時市場の20%を占めていた偽造品の流通を現在ではかなり低いレベルにまで抑えこんでいる。しかし、今なお中国からの偽造品流入ルートは存在し、タイにおいても、再び偽造品の流通が増えることが懸念されている。
日本ベアリング工業会では、「低価格が売りの偽造品は安価で劣悪な原料や部品が使用され、また製造現場から輸送に至るまでの品質管理がまったくなされていない。わが国製品の権利侵害を訴えるよりも、“偽造品は品質がまったく保証されていないため、ベアリングのユーザーにとって危険きわまりない”ということを前面に訴え偽造品対策に取り組んできた。これからも取組みを強化していく」方針だ。
こうしたベアリング産業の共通の利害問題に対して、日米欧のベアリング工業会が協調して関連法規に基づきながら効率的に対処する目的で、世界ベアリング協会(WBA:World Bearing Association)が2006年9月に京都でWBA設立総会を開催、WBA定款が採択されWBAが設立された。WBAでもこの日本ベアリング工業会の取組みが評価され、偽造品対策が強化されてきている。
しかし、効果を上げてきているとはいえ、先述のとおり特に中国においては「いたちごっこ」の様相を呈しており、業界団体だけの取り組みでは限界があるだろう。世界的な法的枠組みがどうしても必要だ。ベアリングなど技術商品の安全性・耐久性を確保するためにも、模倣品・海賊版拡散防止条約、ACTA構想の実現に強く期待したい。
第104回 海外生産シフトで求められる表面改質・加工技術
第104回 海外生産シフトで求められる表面改質・加工技術日本銀行 経済産業省では先ごろ、円高が企業活動、収益などに及ぼす影響について緊急ヒアリングを実施、結果をとりまとめた。対米ドルが1ドル=85.92円~84.55円、対ユーロが1ユーロ=111.16円~106.74円だった8月11日~8月24日の期間に、足下の円高の影響や、円高が継続した場合の影響、中小企業・下請企業への影響などについて、輸出製造企業を中心とした102社の企業を対象としてヒアリングを行ったほか、各経済産業局を通じ下請企業を含む中小企業98社から現場の「生の声」を聴取、概ね以下の産業界の意向が浮き彫りになった。
輸出型企業、たとえばトヨタ自動車では1円円高に振れると350億円の利益が飛ぶと言われる(1)対ドルの円高で製造企業の約6割強が、対ユーロでは約5割強が「減益」。円高が半年継続すれば、対ドルの円高で「深刻な減益」は1割から3割へと増え、収益の悪化はさらに深刻化。ウォン安により、特に新興国市場で日本企業は韓国企業との競争に苦戦する、と円高が企業の収益を悪化させている状況を示した。
(2)1ドル85円水準の円高が継続した場合、中小企業の約7割、下請中小企業の8割強が「減益」と回答。製造企業のうち4割が「生産工場や開発拠点等を海外に移転」、6割が「海外での生産比率を拡大」と回答。下請企業を中心に、取引先のコストダウン要請、海外企業に奪われ受注が取れなくなる恐れ、取引先の海外移転の影響を懸念する声が多くあり、1ドル85円の円高が継続した場合、国内産業の空洞化がさらに加速するおそれがあるとしている。
自動車など製造業ではすでに為替変動に左右されにくい海外生産へのシフトを進めているが、成長市場である新興国での円高による価格競争力の低下から、企業の海外生産拡大への意向が強まってきているようだ。
現地生産でコストメリットを出すには材料・部品の現地調達率の拡大が不可欠だが、特に中国やインドなど新興国で安定した品質の材料を確保するのは難しいと、某自動車メーカーの関係者は言う。
たとえば、多結晶体である鋼の疲労特性は結晶粒の微細化によって向上するが、この材料の微細構造の制御にばらつきがあるらしく、結晶粒の分散状態が悪く浸炭処理後に結晶粒が粗大化、形状精度のほか製品寿命の低下につながることもあるという。日本同様の仕様の材料が得られない状況に対し、機能に影響しない範囲で仕様を変更する現地リファイン材や現地のスタンダード材料を使おうとする現地調達の考え方がある。いずれにしても素材性能が確保できない状況で信頼性の高い部品としての性能を向上させるには、熱処理を含む表面改質技術や加工技術で不足する部分をカバーする必要があるとメーカーは考える。
イメージ図:ガイドブロックの外側の加工に比べ、内側のボール循環部の加工は製品性能を決める難しさがある(提供:THK) 新興国ではしかし、この加工技術でも安定した品質を得るのが難しいという。直動案内製品の関係者によれば、海外生産にあたっては先述の状況から耐久性や摺動性能に関わる材料については依然として日本から材料を供給した上で、ガイドブロックの外形の加工などは現地のメーカーに委託するものの、内側のボール転動面の加工は日本で行うとのことだ。ボールがなめらかに転がるための表面粗さの確保や転動面の耐久性に関わるダメージのない加工が現地ではまだ難しいようだ。
こうした材料や加工などの技術的な問題が多い中で海外生産を拡大しなければならない状況を止めるよう、円高阻止に向けた政府、日銀の方策に期待したいが、長期的にはやはり海外生産シフトは進む傾向にある。近年、グローバル生産の進展を象徴するように日本車のリコール問題が多発しているが、材料の性能を高めるリファイン技術とともに、それを補い信頼性の高い部品を作る表面改質や加工技術、耐久信頼性・安全性を裏付ける試験評価技術を含めた現地調達システムの確立が急がれるところだ。
第105回 インプラント医療機器を支える表面改質技術
第105回 インプラント医療機器を支える表面改質技術提供:瑞穂医科工業 経済産業省では先ごろ、「平成22年度医療機器分野への参入・部材供給の活性化に向けた研究会」を開催、本年度の活動を開始している。
世界的な高齢化が進展し医療機器市場の大幅な拡大が見込まれる中、2007年4月には文部科学省、厚生労働省および経済産業省によって「革新的医薬品・医療機器創出のための5か年戦略」が策定され、また2009年12月には「新成長戦略(基本方針)」が閣議決定され、ライフ・イノベーションによる健康大国戦略として、医療・介護・健康関連産業の成長産業化が謳われるなど、医療機器産業の活性化はわが国の成長において重要な役割を担っている。
わが国は世界に誇る優れた科学技術やものづくりの力を有し、近年そうした高度な工業技術を活かして医療機器産業への参入を目指す中小企業の動きが活発化してきている。一方で医療機器産業は薬事法をはじめ法律・制度の影響を大きく受ける産業で、また、国際的な規制や品質管理の問題など、医療機器分野への参入には高い障壁があるとの指摘もあり、医療機器産業への参入を促す環境整備が求められている。さらに、医療機器のリスクに対する懸念から、部材供給者が医療機器、特に埋込み(インプラント)型治療機器を中心とする医療機器への部材供給を躊躇しているとの指摘は顕著で、こうした部材供給問題も医療機器産業の活性化の阻害要因の一つとなっている。
こうした指摘に対し経済産業省では2007年度にインプラント型の医療機器などに対する材料や部材の提供を活性化するための方策について、関係業界と共同で検討を開始、2008年度には、現状把握とともに対策の基本的方向性について検討するために、「医療機器分野への参入・部材供給の活性化に向けた研究会」を立ち上げた。本年度は同研究会を継続開催するとともに、医療機器分野への参入方策および部材供給の活性化方策を検討する二つのワーキンググループを立ち上げ、具体的課題の抽出および対応方策に関する議論を深めたほか、医療機器産業の活性化および医療機器産業に参入する中小企業の支援を行う全国の医療機器クラスターを支援するための枠組み構築に向けた活動を展開した。
提供:瑞穂医科工業 整形外科で使用されるインプラント製品である人工関節で最も多い股関節でも、そのほとんどを海外メーカーが占めている。人工股関節は、生体適合性が高く耐摩耗性・低摩擦性に優れる超高分子量ポリエチレン(UHMWPE)製のソケットと、コバルトクロム合金や各種セラミックスなどでできたヘッドとの組合わせからなり、市場で多いのは、メタル・オン・ポリエチレン(コバルトクロム合金などメタルのヘッドとUHMWPEのソケットの組合わせ)だが、瑞穂医科工業では国産技術として潤滑性を持たせたメタル・オン・メタルのシステムを手がけている。メタル材料としては耐摩耗性に優れたコバルトクロム合金が主だが、コバルトイオンの溶出を防ぎつつ生体適合性と潤滑性を高めるコーティング技術として、DLC(ダイヤモンドライクカーボン)など様々なコーティングを適用する研究が行われているという。
しかし人工股関節に要求される寿命30年という長期使用を考えた場合、コーティングの密着性低下による耐久安全性の劣化が懸念される。そこで、微粒子を圧縮性の気体に混合して高速衝突させるという表面改質技術WPC処理を併用することでDLCコーティングの密着性を高める研究も産学共同で進められている。
提供:銀座大幸歯科 また、虫歯などで歯根がなくなった場合に使われる人工歯根というインプラント材料には、噛む力に耐える強度と耐食性、生体親和性に優れた素材が求められる。人工歯根としてはチタン合金母材に母材と同様なチタン材料をプラズマ溶射によって高密着力でコーティングされている。溶射によって表面多孔性構造(ポーラス)にすることによって新生骨が人口歯根表面ポーラスに侵入し、結合することが分かっている。
また同じ人工歯根の用途で、数~数十μmの二次粒子からなるハイドロキシアパタイト微粒子をショットピーニング装置により噴射して、人工歯根など生体内で使用されるチタン合金やステンレス鋼などの表面に埋入させて濃化層を形成させ、表面の生体親和性を高める試みがなされている。
こうしたわが国の高度な工業技術をインプラント製品に適用する上で、厚生労働省の承認を得てわが国のインプラント市場を拡大するための明確な評価基準の確立が求められ、現在、インプラント製品の評価法をJIS化する動きが広がっている。わが国の医療機器市場のさらなる拡大のためにも、生体材料のJIS規格化をすすめていくとともに、上述の表面改質技術などにより安全性が高められたインプラント製品の仕様の明確化と安全性の情報発信の強化がますます求められている。
第106回 わが国金型産業の競争力向上のビジネスモデルを
第106回 わが国金型産業の競争力向上のビジネスモデルを提供:富士テクニカ 自動車向け金型国内2位の富士テクニカ( http://www.fujitechnica.co.jp )は9月17日、政府が出資する企業再生支援機構の支援により、同3位の宮津製作所から金型関連事業を譲渡する形で本年12月中に事業統合することを決定した。自動車向け金型でそれぞれ9.0%、5.2%の国内シェアを持つた富士テクニカと宮津製作所が事業統合することで、すでにタイ大手自動車部品大手メーカーのタイサミットの傘下にあるシェアトップ(同13.5%)のオギハラを抜き、自動車向け金型国内最大手メーカーが誕生することとなる。
富士テクニカと宮津製作所はともに自動車向け独立系金型メーカーとして、国内自動車メーカーはもちろん、ゼネラルモーターズなど米国ビッグスリーや欧州の自動車メーカーとも取引が多い。富士テクニカは北南米に、宮津製作所は欧州市場での売上比率が高く、今回の事業統合でも顧客基盤の補完という統合シナジーが期待される。しかし、今回の事業統合に至った金型業界の置かれた状況としては、北米市場や国内市場が低迷する中での国内勢による消耗戦の展開や、新興国の自動車市場が拡大する中での地場企業の金型事業への参入と価格競争にともなう金型製品価格のグローバルでの大幅な下落がある。
このため富士テクニカでは今回、外部からの資本の受入れを含む財務基盤の強化と、日本の金型技術を結集し技術優位性を生かした事業モデルを策定することにより、新興国の金型メーカーとの差別化と国内企業間の過当競争の解消を図ることが必要との判断から、ともに金型業界のトップメーカーである宮津製作所との事業統合を決めたもの。
金属やプラスチックなどの素材に圧力を加え特定の形状の部品に成型するのに使われる金型は、大量生産において製品の品質・性能・生産性を左右する重要な要素でマザー・ツールとも呼ばれ、金型産業は日本の代表的な基盤産業の一つに位置づけられている。わが国の金型産業は、世界最高レベルの技術力を背景に、自動車をはじめ国内外の製造業全体の競争力向上に寄与してきた。日本の金型なしには車が作れないと言われた時代もあったが、1990年代以降の自動車・電機分野での海外生産に伴う産業空洞化の進む中、わが国金型産業は低迷し始めた。従業員20人未満の中小企業が9割を占めるという金型産業では、技術の流出により自らの商権を奪われることを懸念して、海外進出に二の足を踏む企業が多かった。
自動車パネルへの溶射技術の適用(提供:富士テクニカ) 確かに金型の守るべき蓄積された技術は多い。金型の生産では一般的だった放電加工から近年、切削による直彫り加工の適用が進んでいるが、高速・高精度加工を実現するためのビビリ抑制や耐久性向上などの工具技術、微小送り・位置決めの直動案内技術や5軸制御などの工作機械技術などが用いられている。また金型には、生産効率に関わる長寿命化や製品品質に関わる精度の維持といった要求から、耐摩耗性や耐焼付き・凝着性、離型性、耐熱性、耐疲労性など様々な表面特性が求められる。富士テクニカでもたとえば、自動車メーカーの省燃費化を目的とした軽量化のため、薄くて強度が出る高張力鋼板を成型するための高硬度な金型を作るべく、金型の摩耗を防ぐ皮膜を形成する溶射技術を使用条件に合わせて開発、自動車鋼板パネルを生産するメーカーでは摩耗による金型のメンテナンス頻度が減り、生産性を向上しているという。
さて、富士テクニカではこうした高い技術力を持つわが国の金型技術が新興国で価格だけによらない競争力を示すべく、国内工場に高い技術力・高い管理能力を集約させマザー工場としてさらなる強化・発展を図りつつ、中国やインドネシア、マレーシアなど海外製造拠点を早期に育成・強化し、グローバル・サプライチェーンの確立を目指したいとしている。新興国での現地生産により価格競争力を高める一方、国内拠点には研究開発機能を持たせ技術競争力を高める考えだ。
今回の富士テクニカと宮津製作所との事業統合に対して経済産業省では、(1)わが国が優れている品質・納期管理能力に加え、新興国に勝るコスト競争力を構築し、持続性ある雇用基盤の構築と、着実な再生が進展すること、(2)経営統合後の会社が、わが国を代表する競争力を身につけ、飛躍的に発展することや、他の金型企業ひいては他のものづくり企業においてもこうした取組みが進み、わが国ものづくりの競争力の向上、さらには、日本経済の成長につながることを期待していることを、企業再生支援機構に対し意見している。わが国で生まれ築き上げられた高い金型技術が、今後も世界の産業の生産を支え続ける、そんなビジネスモデルを金型業界に示していくことを今回の事業統合の成果として期待したい。
第107回 24時間換気システムの普及で求められるベアリング技術
第107回 24時間換気システムの普及で求められるベアリング技術提供:パナソニック 2003年7月1日に国土交通省によりシックハウス対策に係る建築基準法が改正されたことで、住宅には原則として常時作動する機械換気設備の設置が義務づけられるようになっているが、近年ファンモータおよびベアリングに対して24時間作動に伴う静音化や省電力化などの要求が強まってきている。
改正建築基準法(令第20条の8)では、内装の仕上げなどにホルムアルデヒド発散建築材料を使用しない場合であっても、家具などからもホルムアルデヒドが発散されるため、居室を有する全ての建築物に機械換気設備の設置が原則義務付けられており、この機械換気設備は原則として24時間作動で居室の空気を強制的に新鮮な外気と交換することを目的として設置される。給気と排気の両方をファンで行う「第一種機械換気方式」や排気のみをファンで機械的に行い、その結果生じる内外の気圧差を利用して給気口から給気することで換気を行う「第三種機械換気方式」などがあるが、いずれにしてもファンが常時回転しているため、建築物への換気設備の導入が進む中で、ファンモータ用軸受には居住空間における静音化と省電力化が求められてきていた。
こうした要求に対したとえばパナソニックの24時間換気システムの一つである天井埋め込み型換気扇を見ると、20 dB 未満の低騒音で消費電力を最大で3~5割低減するブラシレスDCモータを採用している(平成20年度省エネ大賞資源エネルギー庁長官賞受賞)。
提供:NTN これらファンモータにおける静音化のニーズに対しNTNでは先ごろ、信頼性、静粛性に優れ、転がり軸受との互換性がある「動圧軸受ユニット」を開発した。現在、家庭用換気設備向けにサンプル提出を進めており、2011年度中の市場投入を目指す計画だ。
NTNではすでに、焼結含油軸受の内径面に動圧溝を形成した動圧ベアファイト(焼結金属製動圧軸受)が2001年以降からHDD向けにスピンドルモータ・ファンモータなどで採用され、実績を残している。動圧軸受は軸と軸受が油膜を介して非接触で回転するため、静粛性に優れているものの、転がり軸受とは寸法や使用条件が異なることから、これまで転がり軸受から動圧軸受への置き換えには制約があった。一方で、改正建築基準法による全建築物への24時間換気システムの設置義務付けで家庭用換気扇の需要も増えているが、リビングルーム、寝室などにも取り付けられることから、特に静粛性に対する要求が高くなってきている。
そこでNTNでは、この動圧軸受の静粛性という特徴を生かしつつ市場ニーズに応えるため、小型換気扇など、軸受荷重が比較的小さく荷重変動が少ない用途向けに、転がり軸受と同寸法で互換性のある動圧軸受ユニットを開発した。動圧ベアファイトを軸受部に採用し、優れた静粛性に加えて転がり軸受同等のトルクを維持したほか、ハウジングとの組み合わせでユニット化したシンプルな設計としている。
一方、静粛性を阻害する要因として、フィルタが捕獲した埃などがファンモータ、さらには軸受内部などにはいることで、異音を発生させるという問題があった。
提供:日本精工 これに対し日本精工(NSK)では、室内換気システム、分煙機用ファン、天井埋込型換気扇向けなど需要が増えている室内換気システムの軸受として、低トルク化による省エネ化や塵埃環境での防塵性能向上による静音化に貢献する「低トルク高防塵シール付き深溝玉軸受」を開発、サンプル出荷を開始した。NSKでは本製品の売上として2013年度に1億円の売上を目指す。
室内換気システムは24時間稼動するため、軸受には低トルク化による省エネ性能が求められる一方、室内換気システムは夜間に寝室で稼動しており、異音の発生原因となる塵埃の軸受内部への侵入を防止するため、軸受には高防塵性能も求められる。
NSKではこれらにニーズに対し、様々な使用環境に合わせ2種類のシール付き軸受を開発した。
①接触タイプ
低トルク化のため、解析技術によりシールリップ剛性を最適化しシール接触圧力を標準品に対し約3割低減。シール接触による高防塵性能を損なわずに従来比で約3割摩擦損失を低減することでモータ消費電力を低減している。
②非接触タイプ
防塵性能向上のため、シールと内輪の非接触シール部を延長、径方向すき間だけでなく、軸方向すき間も極小化するため、ゴムシールを採用。非接触シールによる低トルク性能を損なわずに防塵性を向上、静音性能を約2倍向上している。
提供:ジェイテクト さらにジェイテクトでは先ごろ、24時間運転でのファンモータ用軸受の電食による音響寿命を含めた長寿命化を図るべく、「長寿命電食防止軸受」を開発している。電食とは、軸受の損傷形態の一つで、モータ回転時に軸受の内外輪間に電位差が発生し、内外輪転走面と転動体の間で、グリースの油膜を介して電流が流れることにより、軸受内部が損傷し、音響寿命に至る現象。
開発品では転動体にセラミックスを使用することにより内外輪転走面と転動体の間に電流が流れることを防止、グリースの長寿命化と電食防止を実現したほか、耐熱温度140℃の高温対応のゴム材質を用いたシールのリップ形状を最適化し、ゴムシールと内輪の接触を極軽接触とし、低トルク化を実現した。さらに、エステル油+エーテル油の基油にリチウム石けん増ちょう剤を配合した長寿命グリースを開発した。これにより雰囲気温60℃でのファンモータ寿命100,00時間以上の長寿命化を達成している。
すでにエアコンやHDDなど電機分野で鍛えられてきたわが国の軸受の静音化技術、省エネ技術は世界に誇る技術の一つだ。建築物での24時間換気システムの導入が進む中、静音化や省電力化を追求するファンモータ用軸受の開発はますます進みそうだ。
第108回 クルマの省燃費化を図るエンジンオイルが販売開始
第108回 クルマの省燃費化を図るエンジンオイルが販売開始提供:出光興産 出光興産( http://www.idemitsu.co.jp )は、API(米国石油協会)と日米の自動車メーカーで組織されるILSAC(国際潤滑油規格化認証委員会)の新規格に合格したガソリンエンジンオイルを新規格発効日の10月1日から全国一斉に系列サービスステーション(SS)で販売を開始した。JX日鉱日石エネルギーや昭和シェル石油などの石油元売りメーカーでも、新規格適合のエンジンオイルを11月から発売すると発表している。旧来規格と比べ省燃費性能をはじめ高温酸化安定性能、触媒被毒防止性能の向上が求められるほか、バイオ燃料対応性能が新たに求められている。
「機械の血液」と呼ばれる潤滑油には、油膜を作ることで摩擦・摩耗を抑え焼付きを防止する「潤滑作用」、ピストンリングとシリンダ間で油膜を作り燃焼ガスの漏れを防ぐ「密封作用」、燃焼により発生した熱を外部に逃がす「冷却作用」、燃焼や回転中に受ける応力を分散する「緩衝作用」、摩耗で発生した粒子(摩耗粉)を洗い流す「清浄作用」、金属部品の錆発生を防止する「防錆作用」などの機能がある。エンジン油は高速、高圧、高温などの環境下にさらされるピストンリングとシリンダーライナー、クランクシャフトとコンロッドのベアリング、動弁機構などエンジン部品の動きを円滑にし、エンジンの性能を引き出すとともに保護する。
旧来、このエンジン油の性能・品質を規定する規格としては、石油メーカーで組織されるAPIが制定するAPI規格が用いられてきたが、近年、自動車メーカーにおいてCO2削減、つまり省燃費性能の向上が重要課題とされる中、クルマの省燃費化システムをAPI規格が満足させられない事態が発生、1991年に日米の自動車メーカーからなるILSACが組織され、エンジンの構成部品の一つであるエンジン油に省燃費性能の規格を盛り込んだILSAC規格が作られることとなり、順次クルマの最新技術に適合したエンジン油が市場にリリースされるようになった。以降、ILSAC規格が改訂されるのに合わせてAPI規格も市場投入されている(ILSAC規格=API規格+省燃費性能)。
ILSAC GF-5規格は、省燃費性能のさらなる強化、市場におけるロバスト性向上、排出ガス適合性の強化、の三点を主眼に開発された。省燃費性能の強化では、新試験法により実際の運転状態をより反映させるよう、回転数、負荷、出力、油温、水温などの試験条件を変更して境界・混合潤滑領域となる高温・低回転条件の割合が増えたことで、エンジン油の違いによる燃費のバラツキが排除されている。ロバスト性向上では、主に清浄性を中心とした性能の強化が規定された。排出ガス適合性強化では、排出ガス後処理装置の触媒寿命を低下させるエンジン油添加剤中のリン(P)に関して、前規格のGF-4までその含有量が段階的に低減されてきたが、リンは摩耗防止の機能を持ち、リン含有量の低減は摩耗促進につながることから、リンの含有量はGF-4同等(最大0.08mass%)としつつ、リンの蒸発量(減少量)を規定、その目標値を11%未満(残存量89%以上)としている。
この厳しい規定をクリアすべく、石油メーカー各社では省燃費化につながる0W-20という低粘度化を図る高粘度指数(温度による粘度の変化が少ない)のベースオイルに加えて、粘度指数向上剤や低粘度下で懸念される油膜切れなどに対する摩擦調整剤など各種添加剤の適切な配合が行われている。今回発売された出光興産のエンジン油では、金属間のすべりをよくして省燃費性能を高める摩擦調整剤(FM)モリブテンの効果を最大限に引き出す添加剤処方を開発、同社従来オイル10W-30に対し、モータリングテストで約9%のトルク改善を記録、対10W-30燃費向上率が約8.4%だった同社SM/GF-4適合エンジン油に比べても2%上回っているため、さらなる燃費向上が期待できるとしている。
GF-5規格は、2011年までに製造されるすべての乗用車で省燃費性能を向上し排出ガスを低減するために施行される新しい政府規制を満たさなければならない米国はもちろん、日本、カナダ、韓国でGF-4と同様に新車に採用される見込みだが、中国では依然数世代前の規格が流通していることから、量的に拡大する中国向け車両に対して新規格に適合した0W-20といった低粘度オイルの工場充填が遅れるとの見方も強く、GF-5適合油の市場が予測よりも縮小することを危惧する声もある。
自動車メーカーと石油メーカーとの長年の協議のもと規定されたGF-5規格とそれをクリアすべく多額の費用と開発期間を投じて開発された新規格適合のオイルの普及と、それによるクルマの省燃費化、CO2削減が促進されることに期待したい。
第109回 ノーベル賞発表、基礎研究の深耕と応用展開を望む
第109回 ノーベル賞発表、基礎研究の深耕と応用展開を望む提供:チッソ スウェーデンの王立科学アカデミーは10月5日、2010年のノーベル化学賞を有機合成の革新的手法「クロスカップリング反応」を開発した鈴木章・北海道大名誉教授と根岸英一・米パデュー大特別教授、リチャード・ヘック・米デラウェア大名誉教授に、同じくノーベル物理学賞を炭素の新素材「グラフェン」を開発したアンドレ・ガイム・英マンチェスター大教授とコンスタンチン・ノボセロフ・同大教授に授与すると発表した。
液晶材料で多数活用されているクロスカップリング反応
ノーベル化学賞を受けた業績「有機合成におけるパラジウム触媒によるクロスカップリング」は、炭素を効率的に結合させる反応。複雑な化合物を作るためには、炭素原子同士を結合させなくてはいけないが、炭素原子は安定で容易に反応しない。パラジウム触媒によるクロスカップリング反応はこの問題を解決し、有機化合物炭素結合を組み替えて新たな有機化合物を合成するもの。液晶や有機EL(エレクトロルミネッセンス)などの製造技術に活用されている。
たとえば液晶は10~20種程度の有機化合物を混ぜ合わせた半透明の液体。これら有機化合物がクロスカップリング反応を用いて液晶材料として製造される。クロスカップリング反応が液晶の生産コストを下げ、液晶テレビの市場拡大に貢献したとも言われる。液晶材料の世界シェアで5割を占めるチッソに限らず、世界でクロスカップリング反応の恩恵を受けていない化学メーカーはないという。
摩擦・摩耗特性が期待されているグラフェン
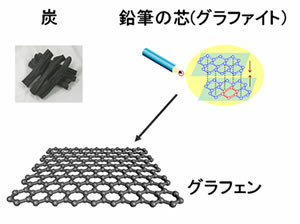
富士通研究所は東北大学らと共同で、一般的な半導体製造プロセスである化学的気相成長法(CVD)でグラフェン絶縁基板上に低温で直接形成する技術を開発、大基板の全面にトランジスタを形成することに世界で初めて成功した。従来のグラフェンの形成温度が800~1,000℃であるのに比べ、形成温度を650℃と大幅に引き下げたことで、さまざまな絶縁基板上に直接グラフェントランジスタを形成することが可能なほか、従来の1/10~1/100という低消費電力LSIや、それを利用したIT機器の実現で省エネルギー化に寄与していくとしている。また、日立製作所は東北大学と共同で、シリコンの10倍以上速い電子移動度が期待されるグラフェンを、CVD法を用いてサファイア基板上に作製する技術を開発した。通信基地局のネットワーク機器などに用いられる高速電子デバイスへの応用が期待されているという。
層状結晶構造のグラファイトの単層を1枚剥ぎ取った超薄膜であるグラフェンは、そうした電気的特性だけでなく、機械的特性、中でも優れた摩擦・摩耗特性が期待されている。潤滑油剤の適用が嫌われる電子機器の摺動部品などでの機械的特性を高める固体潤滑コーティングとしての研究もぜひ進めてほしいところだ。
わが国の二人の研究者がノーベル化学賞を受けた「パラジウム触媒によるクロスカップリング」のように、世界で適用されていく重要な基礎研究の深耕を進めるとともに、その応用展開によって新たなビジネス・産業の創生につながっていくことに期待したい。
第110回 製品品質向上と環境保全を図る産業洗浄技術
第110回 製品品質向上と環境保全を図る産業洗浄技術 日本洗浄技能開発協会と日本産業洗浄協議会、日刊工業新聞社は10月13日~15日、東京・有明の東京ビッグサイトで「2010洗浄総合展」を開催した。機械・電子部品の高品質を保つ部品洗浄など、最新の洗浄剤・洗浄システムなどが多数展示された。
金属部品の油汚れに用いられる洗浄剤
産業洗浄では、様々な部品や材料が品質・機能を確保する目的で洗浄されるが、その半分が金属部品との報告がある(2003年機械振興協会経済研究所)。落とすのは圧倒的に油汚れが多く、グリース・潤滑油剤を筆頭に、加工油、防錆油などが続く。つまり大半は金属部品の油汚れで、強力な洗浄力が求められる。
かつて、この金属部品の油汚れを落とす洗浄剤といえば、塩素系洗浄剤である1,1,1-トリクロロエタンが定番であった。極端な話、油まみれの部品を1,1,1-トリクロロエタンの液中にどぶ漬けしておけば、油汚れは跡形もなく除去されていた。しかし1995年をもって特定フロン・エタンはオゾン層保護を目的に生産が中止、ここから洗浄力の強力なエタンに匹敵しつつ環境負荷の小さい総合的な代替洗浄技術の開発が本格化したと言える。つまり洗浄剤、洗浄システムの合わせ技によって、環境に負荷を与えずに、製品の競争力向上からは機能に影響する洗浄品質を効率的に、かつ低コストに実現しなければならないという取組みである。
環境負荷の小さい洗浄剤の開発が本格化
金属加工部品の加工後の洗浄を例にとると、付着した油汚れと相溶することで脱脂洗浄を行う炭化水素系洗浄剤が多用されている。地下水汚染物質、有害大気汚染物質、オゾン層破壊物質、温室効果ガスのいずれにも該当せず使い勝手がよいことも、採用される理由だろうか。しかし、炭化水素系洗浄剤は従来、引火性があることから装置には防爆仕様が求められ、また相溶しない水溶性加工油の洗浄は不得手としていた。これに対し、たとえば日鉱日石エネルギーの「NSクリーン」では、パラフィン系炭化水素の単一物質で構成し非常に狭い沸点範囲を実現することで、引火しやすい軽質分を含まないため同等の平均沸点を持つ混合物に比べ引火点が高く、より安全性を高めている。また、水溶性加工油に対しても、特殊な界面活性剤を配合することで、被洗浄物に付着した水分を素早く引き離し、分離した水分は水滴となり比重差によってすみやかに沈降させるという。
洗浄の効果に加えて省エネ化が求められる洗浄システム
提供:カイジョー 洗浄工程で洗浄効果を高める手法としては、超音波洗浄が多用される。特に複雑形状の部品や止まり穴があるような部品では、物理的な作用がなければ洗浄液が汚れの部分まで浸透しにくいためである。超音波洗浄は主に(1)キャビテーション、(2)加速度、(3)物理化学的反応促進作用の三つの相互作用によるものとされ、特にキャビテーションをいかにコントロールするかが重要。キャビテーションは周波数が低いほど発生しやすく、また周波数が高くなるに従い加速度は大きくなる。これらの効果の違いから、それぞれの洗浄物や汚れの種類により周波数の使い分けがなされている。機械加工部品に付着した油の洗浄には、キャビテーションを利用した100kHz程度の周波数が選ばれる。
ものづくり基盤技術の一つとして様々な分野で活躍が期待される洗浄技術
こうした合わせ技によって産業洗浄技術は、自動車部品やベアリングなどの精密部品の品質・性能を保持し、はてはハードディスクドライブなど微細機構のマイクロコンタミネーションを抑制し信頼性を高めている。表面特性向上というでは、洗浄工程は機能性コーティングの母材への密着性を高める前処理としても重要な位置づけを占めるなど、ものづくり基盤技術振興基本法によりものづくり基盤技術の一つに指定される、重要基盤技術である。オゾン層保護のための特定フロン・エタン代替としてスタートした環境対応の洗浄技術はその後、地球温暖化防止、揮発性有機化合物(VOC)排出規制などに対応し、さらに化学物質全般の管理について国際的な協力体制のもと推進すべく、「経済的に実行可能な最良利用可能技術(EVABAT)」として検討が進められてきている。MEMS(微小電子機械)など微細機構の商業化とともに、微細なコンタミネーションの除去による表面機能や品質の確保が求められるといったように、産業の拡がりとともに産業洗浄のカバーする領域は常に拡がり続けている。環境保全と最先端分野での表面創成を実現する産業洗浄技術の合わせ技が、今後もますます求められている。