“あの”ニュースに見るテクノロジー
“あの”ニュースに見るテクノロジー
メカ技術は市場のニーズとともに変化し、進化しています。本コーナーでは、編集部が「これだ!」と思ったニュースの中から、各種ニーズや対応するテクノロジーを探ります。
第001回~第010回
第001回~第010回第01回 自動車の軽量化手法
第01回 自動車の軽量化手法中古車販売のガリバーインターナショナルの調査では、排気量が2L前後から上のクラスの自動車を保有していた人が、軽自動車を含む1.5L以下の車に買い替える割合が増加しているという。燃料の高騰を受け、燃費の良い小型車を選ぶ傾向が鮮明になったわけだが、省燃費化では軽量化は大きな手法の一つだ。軽自動車はその車体重量から燃費は良いとされるが、普通車や大型車でも、ピストンのアルミ化、耐熱性や耐久性などの条件が厳しいバンパーやインパネの樹脂化(マツダでは生分解性樹脂化)など、自動車部品を軽量化しつつ、剛性も保持する技術開発が進んでいる。
たとえばNTNでは、高温になるエンジン補機ベルトに使用されるアイドラプーリとして、軽量で長寿命な「補機用高温樹脂プーリユニット」を開発した。樹脂プーリユニットは従来、放熱性が悪く軸受が高温になりやすいため、軸受のグリース寿命を著しく低下させるなどの問題があったが、軸受外輪の放熱面積を増加させ軸受外輪温度を低下させたり、長寿命グリースの開発などで、従来の樹脂プーリユニットと比べ2倍以上、鉄プーリユニットと比べても同等以上の軸受寿命向上と重量の65%低減を実現している。
また、ジェイテクトは、軽量化とアクスルユニットの組立工程の簡素化を実現した駆動輪用の「シール別体型ABSセンサ内蔵ハブユニット」を開発した。シールとABSセンサを別体とし、軽量化、コストダウンを実現している。
さらに、日本精工は、ハブユニット軸受に適用可能なハブユニット軸受内蔵型車輪速センシング用プラスティック磁石エンコーダを開発、従来のゴム磁石製品比25%の高磁力化を達成、磁気エンコーダのコンパクト化による軸受のダウンサイジングを図り軽量化に貢献しているという。
以上のように、軽量化を目的とする樹脂材料などへの置換えにあたっては、従来の鋼製材料に相当する、あるいは凌駕する剛性や耐熱性を補うべく技術開発が進んでいるようだ。
先のマツダの例のようなバンパーなどと違い、軸受のような可動部品に生分解性樹脂が使えるものかと疑問視されていたが、日本精工では、生分解性樹脂であり耐熱性に優れるポリビニルアルコール(PVA)系樹脂に、強度を向上させる繊維状補強材と柔軟性改良剤を配合することによって、適度な柔軟性が付与されポリ乳酸より引張強度、剛性をそれぞれ高め、融点が約200℃、120℃の高温下で1,000時間放置しても、劣化がほとんど生じないレベルまで耐熱性を向上、構造部材として実用に耐えるレベルを実現しつつ、土壌中を想定した環境では180日で60%以上生分解することが確認されている。同社では、軸受の構成部品である保持器・シールをこの高強度生分解性樹脂製とし、内部に生分解性グリースを充填した環境配慮型転がり軸受を試作、評価した結果、50%の低トルク化達成で省エネルギーに貢献することが期待できるほか、100℃、10,000回転、5,000時間の耐久試験で十分な耐久性が確認できたという。
軽量な材料は従来の鋼製材料に比べれば脆い。自然環境で分解される生分解性樹脂はなおのことだろうが、脆さと耐久性というトレードオフを見事に克服しつつある。こうした技術の一つ一つが自動車の軽量化、さらには省燃費化を支えている。今後もニュースを通じて、秀逸なテクノロジーを見てみたい。
第02回 乗降客の安全を守る可動式ホーム柵
第02回 乗降客の安全を守る可動式ホーム柵山手線が2010年の使用開始をめどに全駅に可動式ホーム柵(写真)を設置する。山手線全29駅設置で約550億円の投資が見込まれている。東京の新都心線など最近開通した地下鉄ではお馴染みだろう。列車のドアと連動して開閉するが、転落防止や列車との接触防止など乗降客の安全のために設けてあるので、たとえば電車のドアは抜けたがホームドアに挟まれた、なんてことはあってはならない。ここでは、センサー技術やそれに基く制御技術はもちろん、それを精確にレスポンスよく実行するメカ技術が重要だ。
ここで言うメカ技術の一つにリニアモーション技術がある。たとえば京三製作所のホームドアの構造を見ると(図)、ドア駆動はACサーボモータの回転をボールねじで直線運動に変換している。このボールねじの直線運動を支持するのが直動案内機構で、特にLMガイドやリニアウェイ、リニアガイドなどの商品で知られる直線転がり案内により滑らかな動きを実現している。
近年ではこうした直動転がり案内には、ボールベアリングと同様保持器の役割を果たす樹脂部品やメンテナンスフリーの潤滑部品が使われている。THKのLMガイドでは、ボールリテーナ付きとすることで、(1)ボール同士の相互摩擦がなくグリースの保持力も向上するため長寿命、潤滑における長期メンテナンスフリーを実現、(2)ボール同士の衝突がないため低騒音、(3)ボール同士の相互摩擦がなく発熱が低いため高速性・レスポンスに優れる、(4)ボールが均一に整列され循環するため滑らかな動作、といった利点があるとしている。可動式ホーム柵の場合はやはり相互摩擦がないことでの高速・高レスポンスや滑らかな動作という特長が利いてくるだろう。潤滑不良による摩擦の増加や摩耗に伴う故障もあってはならない。日本トムソンのリニアウェイでは、Cルーブという潤滑油内蔵部品から潤滑油が支給され長期間にわたり潤滑性能を維持し、5年または20,000kmのメンテナンスフリーを実現するという。また、日本精工のボールねじでは潤滑ユニット「NSK K1®」を装着することで5年間または10,000km以上のメンテナンスフリー化を図るとしている。
ホームでの人身事故は08年3月までの5年間で168件もあって、このうち今回導入を決めた山手線では37件と最も多かったという。こうした信頼性の高いメカ技術に支えられた可動式ホーム柵が早い時期に全線で導入されることを期待したい。
第03回 東京ビッグサイトで、エスカレータ急停止事故
第03回 東京ビッグサイトで、エスカレータ急停止事故東京・有明の東京ビッグサイトの上りエスカレータが急停止後に逆走し、10人が軽傷を負った事故で、エスカレータに乗っていた人の総重量が、荷重制限の約7.5tだけでなく、逆走防止用のブレーキ能力の限界である約9.3tも超えていた疑いの強いことが分かった。このため、自動停止後にずり落ちるように逆走したと見られている。
問題のエスカレータの構造は明らかにされていないが、一般にエスカレータはモータ+チェーンで駆動する。踏み板の両端に取り付けたタイヤ(回転体)がエスカレータ両端の案内レールの上を転がることで、滑らかに上下動する。ただし正常に動くかどうかは、積載荷重による。
製造元の日本オーチス・エレベータによると、事故時は荷重オーバーに伴い、電源が切れて自動停止したと同時に、下り方向に逆走するのを防ぐためディスクブレーキが作動したと見られる。しかし、ブレーキ能力の限界は1ステップ(横102cm、縦40cm)あたり120kgで、総重量では約9.3t。問題のエスカレータはステップが84段あり、階段状になっているのは上下部分の3段ずつを除く78段。建築基準法上の安全基準の計算式は、1ステップあたりの荷重制限130kg×78段×0.74の7,503kgで、これは2ステップに大人3人が乗る計算だが、事故当時は1ステップに3~4人が乗っており、重みを支えきれずに逆走した疑いが強いという。
先に紹介した構造から推察すると、上に向かい転がるはずのタイヤが、下に向かい滑らかに転がったことになる。いかに信頼性の高い機械であっても、設計値をはるかに超える条件では安全な稼働は望めない。はやって会場を移動する。イベントの性質からも事態は予想されたことだろう。エスカレータは人々の利便性を図り、また今後の高齢化社会ではますます普及していくであろう大量輸送機器である。事故原因の一層の解明と、関係者による利用上の安全管理の徹底を強く望む。
第04回 疾病の早期発見?CTスキャンの高速化競争
第04回 疾病の早期発見?CTスキャンの高速化競争フィリップスエレクトロニクスジャパンは、X線管球が体の周りを1回転する間に撮影できる画像を従来製品の4倍となる256枚に引き上げたコンピューター断層撮影装置(CT)を発売した。従来製品が1回転0.42秒だったのに対し、1回転あたり0.27秒で低被ばくの撮影が可能という。
肺がんなどの早期発見・早期治療につながる有効な手法として、CTの医療現場での採用が進み、その世界市場規模は3,300億円といわれる。
ヘリカルスキャン方式のX線CT装置では、X線管は対向配置されたX線検出器とともにガントリ内部で回転され、患者をベッドで送ることにより身体をらせん状にX線走査し、これにより身体の断面を0.5度などの細かいピッチで撮像できる。心臓のような動きのあるものを撮像する場合には、0.5秒に1回転など、X線管を搭載したガントリの回転数を上げることが求められている。
従来から回転機構の支持には真空環境下に置かれることから宇宙や半導体などで使われるような軟質金属の固体潤滑玉軸受が使われていたが、高負荷での高速化や静音性の点が課題となっていた。今回開発されたフィリップスのCTではボールベアリングに替えてエアベアリングを使うことで摩擦を低減し回転速度を高め、高速撮影により撮像時間を大幅に短縮したという。東芝メディカルシステムズのCT(写真は同社CTの一例)では、この支持機構に液体金属を作動流体とした動圧ハイブリッド軸受を適用、高速化、静音化を実現している。
ちなみに患者を載せたベッドを前後に移動する運動部には滑らかに送る直動転がり案内(THKのLMガイドなど)が使われ、振動や騒音を減らすことで患者への精神的な負担を軽減しているという。
第05回 北京五輪を終えて
第05回 北京五輪を終えて北京オリンピックが閉幕した。当編集部が応援した星野JAPANのメダル獲得はならなかったが、日本は金9、銀6、銅10の25のメダルを獲得した。今春『ハンマー頭部の加速についてのバイオメカニクス的考察』なる論文で中京大大学院から体育学博士号を受けたアテネ五輪金メダリストの室伏広治選手にも、科学的分析の結果を期待していたが、連覇はならなかった。2投目の80m71以外は80mを超えられず、5位。腰を痛めていたらしく、鍛錬と科学の力は残念ながら生かされなかった。
この室伏選手がハンマー投げ以外で五輪に挑んでいたことがある。氷上のF1といわれるボブスレー。長野五輪のことだ。室伏選手は、選手選考会であるコントロールテスト(60m走、20m走、立ち五段跳び、ベンチプレス、スクワットの5種目を計測し各タイム、距離、挙上重量を得点(各種目100点)で換算し、点数を算出して順位を決める)でただ一人500点満点を打ち出した。
堀切川一男氏開発の低摩擦ランナーと、ランナーを装着した長野五輪日本代表用ボブスレー 実はこのとき、ボブスレー日本チームには科学・技術面での指導者がいた。東北大学教授(当時山形大学助教授)の堀切川一男氏である。彼の専門はトライボロジー(摩擦・摩耗・潤滑の科学・技術)。ボブスレーの力学解析を行ってタイム短縮に効果的な新しいスタート方式である「蹴り乗り」を提案したほか、「低摩擦ボブスレーランナー(そり用の刃)」も理論的に設計、開発し、弱小だった日本代表チームを世界トップレベルに肩を並べるところまでレベルアップさせた。
しかし、室伏選手はハンマー投げに専念したいといった理由から長野五輪ボブスレーでの出場を断念、堀切川氏はのちに「あのとき彼が出ていれば、さらにいい結果が残せたのに」とこぼしている。ボブスレーは陸上の投擲種目の選手やスプリント種目の選手が適しているとされ、室伏選手並みの選手が三人いれば確実に金メダルが取れるともいわれている。
室伏選手のハンマー投げにおける科学的探究心は、ひょっとするとボブスレー選手時代のこの工学者との取組みの中で育まれたものかもしれない。4年後のロンドン五輪で成果を期待したい。
第06回 町工場の技術の結晶、人工衛星「まいど1号」が完成
第06回 町工場の技術の結晶、人工衛星「まいど1号」が完成大阪府東大阪市などの中小企業9社でつくる東大阪宇宙開発協同組合(SOHLA)が開発していた小型衛星「まいど1号」(SOHLA-1)が完成、最終点検のため宇宙航空研究開発機構(JAXA)・筑波宇宙センター(茨城県つくば市)にトラックで運ばれた。
「まいど1号」は一辺50cmの立方体で重さ約50kg。本体の組立て後、振動試験や管制設備のテストなどをしていた。温室効果ガス観測技術衛星「GOSAT(ゴーサット)」と一緒に今冬、鹿児島県・種子島宇宙センターからH2Aロケットで打ち上げられ、雷雲観測などの役割を担う予定だ。
衛星は通常、その目的に応じて個別にゼロから作り始め、開発に3?10年の期間と数億?数百億円のコストが必要とされる。これに対し東京大学中須賀氏のアイデアにより、衛星の各機能をモジュール化し、モジュール(機能)ごとに1枚の「パネル」を製作、各パネルをつなぎ合わせるだけで機能する新しい汎用小型衛星衛星「PETSAT:Panel ExTension Satelliteの開発が、町工場の技術を結集して東京大学やJAXA、大阪府立大学などの協力を得て、進められていた。
パネルは「CPU」、「太陽電池」、「メモリ」、「通信」、「姿勢制御」、「軌道制御」などの基本機能を担当するバスパネル、「光学」、「センサ」など個々のミッションに応じて異なるミッションパネルからなる。ある機能を実現するためパネルを必要な枚数だけ必要な形に組み合わせ、打上げ時には折りたたんでロケットに搭載する。こうしたモジュール化により大量生産、5,000万円?という低コスト化、1年以内という開発期間短縮を実現できるという。
しかし宇宙空間では真空、急激な温度変化など、機械の可動部は厳しい環境下に置かれる。打上げ時に折りたたんである「まいど1号」が宇宙空間で正常に展開しミッションをクリアするには、真空環境にある展開部分のヒンジの潤滑がうまく機能するかどうかは重要な要件だ。また、周囲に貼り付けた太陽電池を動力源とするこの衛星では急激な温度変化に伴い太陽電池パネルが剥落しないかという、接着性能の検証も必要だろう。
また、衛星の開発コスト低減にはめどがついたとしても、世界では通信などに使う中型・小型の商業衛星の1回の打上げ費用が数10億円規模なのに対し、H2Aロケットでの打上げ費用は100億円強という状況。日本の衛星ビジネスの飛躍のためにも、「打上げ費用を含めたユーザーの負担を1億円程度に抑えたい」としたPETSAT衛星の当初の目標へのアプローチに期待したい。
第07回 国産航空機の量産化に向けて?哨戒機が納入
第07回 国産航空機の量産化に向けて?哨戒機が納入 川崎重工業が、開発中の次期哨戒機「XP-1」試作機1号機を防衛省に納入した。提供:川崎重工業受注している2号機も年内に納入予定とのこと。大型機開発は、1970年に初飛行した輸送機C1以来となる。海上自衛隊では現在運用中のP-3C哨戒機80機をすべてXP-1に置き換える方針。XP-1は航続距離(8,000km)など性能が向上しているため、約70機で作戦能力の維持が可能としている。XP-1は、P-3Cを多少大きくした4発ジェット機で、長さ38m、翼幅35m、全備重量80t、高速飛行(830km/h)のため主翼尾翼は後退翼になっている。
哨戒機は、海上をゆっくり飛びながら不審船を発見したり海中深く潜航する潜水艦の動きを監視する役割をもつ。北朝鮮や中国の軍事力の脅威が言われるなか、防衛省は高性能次世代哨戒機の国産化機を決定、2001年度から川崎重工業が主契約企業となって開発に取り組んでいた。
哨戒機は役割上、飛行性能、レーダー探知性能などに加え、静音化が求められる。このためIHIが開発したエンジン「XF7」は、低燃費で低騒音仕様。エンジンの騒音は、P-3Cに比べて、巡航出力で10dB程度、離陸出力で5dB程度低減している。
航空機エンジンの低騒音化には、ファン騒音とジェット騒音の低減へのアプローチがある。ファン動翼は高い空力性能と低騒音化を併せ持つようベース動翼の翼先端側を前方に傾斜させた形状の「スウェプト動翼」としたことで、動翼前縁に生じる離脱衝撃波を弱め、ファン騒音で支配的なバズソー音を低減したという。また、排気ノズルの出口形状をギザギザにしてジェットの混合を促進させる「シェブロンノズル」に対し、排気ノズル形状をシンプル化(周方向5ヵ所に三角形状の小型ミキサを配置)した「ノッチノズル」にして推力を低下させることなくジェット騒音を低減している。
このほか、問題となったベアリングの耐久性向上に対しては、保持器の形状改良などで対応がなされているという。
川崎重工業ではこれを機に、機体の強度不足などで開発が遅れている、次期輸送機で民間転用の本命とされる「CX」の開発も急ぐ構えだ。
第08回 食の安全システムを覆した「事故米」
第08回 食の安全システムを覆した「事故米」大阪の加工米販売業「三笠フーズ」が、最も強い天然の発がん性物質といわれるカビ毒アフラトキシンや有機リン系殺虫剤メタミドホスに汚染された「事故米」を食用として流通させていた。食品衛生法では有害物質を含んだ食品は流通が禁止されているため、国ではこうした事故米を食用ではなく、接着剤など工業用原料に限定して販売を認めている。ところが三笠フーズでは、買い取った事故米を焼酎のほか、せんべいや和菓子の原料として転売していた。
食品・飲料の製造・加工機械では、食の安全を脅かす異物混入を徹底的に防ぐ取組みがなされている。たとえば今回事故米の使われた焼酎の精製では、ポンプで原酒を加圧する工程がある。往復動ポンプにはシリンダーとロッドにそれぞれシール(パッキン)があるが、摩耗はゼロとはいえず摩耗粉という異物が発生する可能性もあることから、シール材には食品衛生法に適合した材料が使われる。液中では潤滑剤が使えないため、自己潤滑性があるPTFEや超高分子量ポリエチレンなどの樹脂シールも使われる。
また、せんべい焼成機で型押しするスタンパーや裏返す機構などの揺動・回転部分に使われるベアリングにも、普通のSUJ2軸受鋼は使えない。水分にさらされ錆が発生すれば異物として混入する恐れがあるためだ。そこでマルテンサイト系ステンレスなど錆びにくい材料が使われる。軸受には通常グリースが封入されるが、HACCP(危険分析重要管理点)は潤滑剤に関し、(1)使用しない(2)漏れない・触れない対策をとる(3)偶発的接触が許容される潤滑剤を使用するという考え方を示している。このうち、軸受に封入されるグリースには、NSF(国際衛生財団)が設定するカテゴリーのH1認証を受けた食品工場用潤滑剤を使うことが一般的になっている。H1認証潤滑剤は、食品が接触する箇所での使用を認められたものである。完全に水中などで使用される軸受には自己潤滑材料が使われる。樹脂製転がり軸受の場合では、内輪、外輪にPPSやポリイミドが、転動体にガラスやセラミックスが使われるといった具合だ。
直動転がり案内もボールベアリングと同様の考え方となるが、中には米ぬかを使った「RBセラミックス」を使ってオイルフリー、耐摩耗、安全衛生を実現したすべり案内も登場している。
このように、稼働中に異物を混入させない取組みが事細かになされる中で、米が利用方法によって価格が極端に変わるという仕組み(せんべいや焼酎原料などの加工用米として流通する場合には5万円、工業用のりとして販売する場合は高くても1万円など)を利用した業者が、意図的に有害物質の混入した原料を食品加工の現場に流した。
先述の食品加工用潤滑剤の本格的な普及も国内では端緒についたばかりだ。食品加工関係者の地道な努力を踏みにじる、事故米転売業者の無節操さには怒りを覚える。食の安全を脅かす悪徳がまかり通ることのない、万全なチェック機能の働くことを願っている。
第09回 防災の月に、地震対策を見る
第09回 防災の月に、地震対策を見る9月1日は、1923年9月1日の関東大震災に因んで制定された「防災の日」だった。近年、地震予測の技術が進んでいるらしい。海溝型の大地震は50?100年の周期で同じプレートで起こることから、30年以内の震度5以上の大地震発生をほぼ正確に予測できるという。しかしマグニチュード(M)7.2を記録した岩手・宮城内陸地震のような、1000から1万年周期で起こると言われる内陸活断層に起因する地震については、30年というスパンでの評価予測は難しく、また2,000ヵ所あるという活断層の調査も現時点で109ヵ所と進んでいない。
予測の精度向上には引き続き取り組むべきだが、地震が起こったときの対策も必要だ。特に国内では戸建てで1,000万戸、マンションで150万戸で耐震性が不十分とされ、住宅の耐久性を高めるべく、構造そのものを頑強にし揺れに備える「耐震」、住宅土台部分に入れた装置で地震の衝撃をのがす「免震」などの施工が急ピッチで進められている。なかでも免震機構の採用はめざましい。
1995年の兵庫県南部地震で多くの民家を倒壊させたのは、直下型地震に多く見られる周期1秒程度の地震波。建物が揺れて往復するのにかかる時間を「建物の固有周期」というが、地震波の周期と建物の固有周期が一致すると、揺れが増幅される「共振現象」が起こる。建物が倒れなくても家具が倒れる可能性はきわめて高い。
これに対し免震機構は、地盤に固定した軌道台の上を建物が転がりやすべりの機構で軽く移動できるようにするものだ。地面が大きく揺れても、免震機構のうえに載った建物は置き去りにされた格好になり、結果的に揺れ(移動量)が小さくなる。つまり免震構造をとることで建物自体の揺れを少なくし、建物の被害や家具の転倒など、屋内の被害を劇的に減らせる。
たとえばTHKの免震システムでは、直動転がり案内「LMガイド」がX軸、Y軸ともに2列にして井桁に組み合わせた形。理論的に、地震動による横荷重が同じであれば免震装置の摩擦係数が低いほど建物に伝わる荷重(揺れ)は小さくなる。LMガイドは摩擦係数0.05?0.08と軽く動くため、この上に載った建物は地面の揺れに置き去りにされた格好で固有周期が延長され、揺れが小さくなる。堤供:THK
サーバーなど重要な機器の免震も必要だ。これに対して不二越の免震機構の一つでは、積載物を載せるための上プレートと床面に設置される下プレートの間に、単球式転がり支承を配置、地震の揺れに対してプレートが捻れないように、捻れ防止機能を有する独自のオルダム機構を採用し、この構造に地震の揺れエネルギーを吸収する摩擦ダンパ発生機能を織り込んだシンプルな構造としている。
日本は、微震も含めると年に2,098回(2007年気象庁まとめ)、日に6回近い地震がどこかで発生し、大なり小なりの被害を与えている。多くの人命や資産を地震から守るべく、地震予測の精度向上とともに、免震など防災メカニズムの導入促進に期待したい。
第10回 燃油高騰で自転車販売好調
第10回 燃油高騰で自転車販売好調ガソリン高騰などに伴う維持費の負担増から自動車を手放す層が増えてきている一方、代わって維持費の負担が少なく環境にも健康にもよい自転車の販売が好調という。自転車協会の調べでは、07年まで9年連続で前年割れだった国内出荷台数が、今年は1?6月で前年同期比11%増えた。通勤での使用も増えていることから、特に人力の負担を軽減する電動アシスト自転車の伸びが大きい。
周知のとおり、スポーツ自動車のスピードアップ(まくり?)、トルク伝達にはギヤチェンジの技術が利用される。ペダルに直結したチェーンホイールのチェーンリングから、駆動トルク(回転力)がチェーンを通じリヤホイール(フリーホイール)のスプロケットに伝わり自転車が進むわけだが、チェーンリングの歯数とスプロケットの歯数との比率(ギヤ比)がキーになる。たとえば歯数40のギヤと歯数20のギヤをつなげば、チェーンホイールが1回転したときのフリーホイールの回転数は2倍になる。つまりギヤの特性として、ギヤ比が高いほどフリーホイールの回転数は高くなるが駆動トルクは低下するため、坂道などでクランクを回す脚への負担は大きくなる。
これに対し電動アシスト機構では、坂道などで人が踏み込む力が強くなると、トルクセンサーが踏力を検知してアシスト量を決定、電動モータによりアシスト力を発生させる仕組み。たとえばパナソニック サイクルテックのスポーツ電動アシスト車「ハリヤ」のモータユニットは、ヤマハ発動機と三洋電機が共同開発したリチウムイオン電池を使いモータ効率を高めている。10°くらいの急勾配でもトップで登るくらいのパワーが出せ坂道を時速17?18kmで走れるというから、普通の自転車に比べるとかなり速い。ケーブルなどをフレーム内に収めアシスト機構(モータユニットも小さくまとめてあるため、電動アシスト車に見えず、ロードレーサーやマウンテンバイクをすいすい追い抜いて驚かれることも多いという。
国内で電動アシスト車をはじめ自転車の販売が好調な一方で、自転車政策の遅れが目立っている。人口当たりの自転車保有台数(02年)はオランダが1位で0.9人に1台、2位のドイツは1.3人に1台、日本は1.5人に1台で3位なのに、全国の道路のうち自転車が専用に走れる道路※の比率はオランダの17%、ドイツの5%に比べ、日本は0.2%(全国120万kmのうち約2,660km)に過ぎない。道路交通法で車道走行が原則とながらの専用道の整備の遅れが、歩行者との衝突事故などの急増につながっている。国土交通省は思わぬ「事故」でトップ不在のようだが、自転車先進国としての政策整備を急いでほしいものだ。
※自転車が専用に走れる道路には、「自転車専用道路」のほか、車道の一部を縁石などで区切った「自転車道」、白線などで色分けした「自転車レーン」がある。
第011回~第020回
第011回~第020回第11回 「第35回国際福祉機器展」が開催、メカが支える自律的生活
第11回 「第35回国際福祉機器展」が開催、メカが支える自律的生活9月24日~26日に東京・有明の東京ビッグサイトで「第35回国際福祉機器展H.C.R.2008」が開催された。(1)電動車いす、電動三輪・四輪車、床走行リフト、固定式・据置式リフト、車いす用福祉車両などの移動機器、移動補助製品(2)ベッド関連用品(3)入浴用リフトや滑り止め用品など福祉機器や、施設用設備・用品などが、国内479社、海外15ヵ国・地域51社より、22,000点展示された。会期3日間の来場者数は12万773人と多くの注目を集めた。
福祉用具(広義、福祉用具産業および共用品)の市場規模は、1995年に1兆3,508億円だったのが、一般製品のユニバーサルデザイン化や共用品の普及を背景として2000年に3兆1,762億円、2004年には3兆8,111億円と成長している。このうち、たとえば福祉車両が2000年度に2万9,005台だったのが2007年度で3万6,822台に増大しているなど機器や装置類の拡大が大きく、福祉機器においてもメカニカルが重要な役割を果たしていくことになる。
降りきったシートは車から離脱し、車いすに変身
福祉車両としては大別して、車いすと助手席の乗り降りをスムーズに行う「回転・リフトアップ機構」、車いすのまま後部エリアに乗り込む「リフター」や「スロープ」の機構、両足が不自由な場合にアクセルとブレーキが左手でハンドルが右手のみで行えるような「運転補助装置」など三つの開発が盛んに行われているようだ。
このうち助手席の回転・リフト機構を試してみた。90°強回転して車の側面を向いて床に近い位置に降りているシートに座ると、リモコンを渡された。スイッチを入れると、まずシートがゆっくりと上昇し回転しフロントガラスに向き直っていく。それから足がゆったりとできるよう少しスライドバックする。頭が当たらないように心持ちリクライニングになる。この完全に乗り込んだ状態でスイッチを押すと、降車の作業になる。少し前にスライドし、90°強回転して開いたドアの方に前進すると、ゆっくりと下降して床近くへ。リクライニングしてあるから頭もぶつからない。
だが、記者の座高のせいもあろうが、リクライニングしていない状態だと、車中へとシートが上昇していく際に少し頭がかするのである。回転するときにはひざがぶつかる。「これは自分だからよけられるけど、足の不自由な方はぶつかりますね。センシングして接触・衝突を避けることは検討してますか?」と聞くと、そこまでは考えていないと言う。課題だと思う。
ところで回転・昇降は直動機構とギヤにより行われる。回転はモータの動力を受けたギヤとベアリングにより、車内での前後のスライドはサーボモータの動力を受けたボールねじと直動案内により、回転は歯車機構により、昇降は直動システム+リンク機構によりスムーズに行われる。
トヨタでは降りきったシートがそのまま離脱し、車いすとして利用できるシステムもあった。これは便利である。
電動車いすの試乗コーナー また、電動車いすにも試乗してみた。実際、今回の展示会場でも電動車いすで移動している方が多く見られた。
試乗用に、上り下りのスロープが付いた広場が設けてあって、一通りの状況が体験できる。「ジョイスティックを前後左右斜めに、行きたい方向に動かすだけです」と係りの人に言われ、前の人を追いかけるように前進し坂を上る。静かに、スムーズに進む。下りにさしかかったところで、前の車いすとの間隔が詰まってきた。「止まるのはどうすれば?」と係の人に呼びかけると、「ジョイスティックを放せば止まります」との回答。確かにすぐに止まった。「電磁ブレーキ」というやつである。コイルに通電することで発生する電磁力で制動させる。ジョイスティックを放しコイルへの通電が切れたときに、スプリングの力で動作する無励磁型電磁ブレーキだろう。これは安心できる。
自律的な生活を目指すには、恐怖心や不快感が起こらないシステムが不可欠であり、今後もメカの活躍が期待される分野だと実感した。
第12回 国際航空宇宙展に見る高信頼性技術
第12回 国際航空宇宙展に見る高信頼性技術続けての展示会ネタで恐縮だが、「2008年国際航空宇宙展(ジャパンエアロスペース2008/JA2008)」が10月1日?5日まで横浜・みなとみらいのパシフィコ横浜で開催された。主催は日本航空宇宙工業会。期間中は4万2,160名が来場した。
今回は2013年の就航を目指す国産リージョナルジェット機「MRJ」をはじめ、AIRBUS A380、Boeing 787などの航空機の模型が注目を集めたほか、ロケット、衛星などの模型や、ターボファンエンジンを中心とするジェットエンジン模型などが多数展示された。
ジェットエンジン、特に主流の2軸ターボファンエンジンでは、最前部のファンと最後部の追加タービンを支える低速軸系とコンプレッサおよびタービンブレードを支える高速軸系の二つの回転軸で、それぞれ二つの円筒ころ軸受と一つの3点接触玉軸受が使われている。NTNではBoeing 777のGE90-115Bターボファンエンジンに搭載された主軸軸受を展示していた。
二つのころ軸受には、疲労強度向上のためのショットピーニング処理や振動抑制のための「スプリングフィンガー」という特殊形状が設けてある。3点接触玉軸受は負荷容量増大のため大径のボールをできるだけ多く組み込めるよう内輪を二つに分割している。いずれも材料は耐熱浸炭鋼M50が使われるが、この高硬度な材料が摩耗粉として出た際にアブレシブ(研削)摩耗→焼付きに至らないよう、摺動面に柔らかい銀めっき皮膜が施してある。
ちなみに某ジェットエンジンメーカーに、「高速性や耐熱性に優れるセラミックボールを使った軸受の採用はどうか」と聞いたところ、「研究開発は進めているが、セラミックスは金属材料のような試験・評価システムが容易でなく、費用も時間も数十倍かかることなどから、採用に至っていない」とのことだった。エンジニアリングセラミックスは機械的特性に優れるが、評価が難しく信頼性の確認ができないのが最大のネックになっているようだ。
航空機のランディングギヤ(着陸装置)は、ほとんどが飛行中は機体内に収納される「引き込み式」で、上げ下げはランディングコントロールパネルのギヤレバーで行われる。機体が離陸した際にパイロットがギヤレバーを上方に引き上げると油圧のピストンとシリンダで構成されたアクチュエータが作動しランディングギヤを引き上げ格納する。着陸時はギヤレバーを下げるとランディングギヤが展開される。
航空機でもフライ・バイ・ワイヤなど電動化が進んでいることから、THKではこのランディングギヤに、近年の射出成形機に見られるようなモータ+ボールねじを使ったアクチュエータを提案していた。「新規参入の決め手は、軽量化と操作性」とのこと。滑らかな動きが可能な直動システムの得意とするところだ。
川崎重工業では、日本精工が開発したハーフトロイダル式無段変速機(CVT)を使った航空機用主電源供給装置「T-IDG(Traction Drive Integrated Drive Generator)を出展していた。これは、エンジンのアクセサリ・ギヤボックスに搭載・駆動され、エンジン回転数に関わらず一定周波数400Hz(115V)発電ができるよう、発電機を一定回転数に保つための装置である。
「ハーフトロイダル型」と称されるトラクションドライブ無段変速機は高面圧下で大きなせん断力を発生するトラクションオイルによって動力を伝達する。向かい合った富士山型の入力ディスクと出力ディスクの間に高面圧で挟んだパワーローラーを傾けることで入出力ディスクの接触点半径を変化させ(介在するトラクションオイルにより)、入・出力間の速度を無段階に調節できる。エンジンからの駆動速度は約4,500?9,000rpmの間で変動するが、油圧制御によるこのトラクションドライブCVTが変速動作を常時行うことで、増速ギヤを介して24,000rpmの一定速度で駆動、400Hz一定周波数の交流電力を発電するという。
今回の展示会をのぞいて、大量輸送・航空機の高速で快適・安全なシステムも、こうした二重三重に安全性がチェックされた、信頼性の高い多数のメカに支えられているとあらためて実感した。空の旅が楽しみたくなった。
第13回 日系各社、欧州市場開拓へ
第13回 日系各社、欧州市場開拓へ材料高騰が長期化し、設備投資が鈍化、1万円台を割る株安、100円を割る円高の続くなか、日本自動車工業会は先ごろ、米国新車販売が1,400万台に届かないとの見通しを発表した。サブプライムローン問題に端を発する景気減速、原材料高、円高、リーマン・ブラザーズの経営破綻による金融不安の連鎖などが思いのほか響いている。とはいえ北米需要がこのまま低迷が続くとは思われず、各社とも09年後半から持ち直すとの見方を示しているが、並行して立ち遅れている欧州の自動車市場開拓に向かう。
? 環境意識の高い欧州では二酸化炭素(CO2)など温暖化ガスの排出量を1990年比で20%削減する数値目標を設定、排出全体の2割強を占める交通輸送部門の排出削減を加速させるため、EU市場での自動車各社に走行1kmあたりの平均CO2排出量を140gに削減することで、欧州委員会(EU)と日本自動車工業会(JAMA)で合意している。そこで燃費のよいハイブリッド車やディーゼル車、小型ガソリン車の採用が加速すると見られているが、中でもハイブリッド車に加え苦手の小型車に注力し始めたトヨタが注目されている。
提供:トヨタ自動車 11月から発売を開始するトヨタ「iQ」は、4人乗りにもかかわらず全長2,985?×全幅1,680?、ホイールベース2,000?、排気量996ccの超小型車である。ガソリンエンジン2種類とディーゼルエンジン1種類の計3種類があり、一部タイプでの走行1kmあたりCO2排出量は規制量を大幅に下回る99g。これを実現するメカは、直列3気筒アルミブロックDOHCエンジンでのエンジンオイル粘度適正化によるフリクション低減を図る簡素なヒートマネジメント機構、エンジンとディファレンシャルギヤの位置関係を反転させギヤをタイヤとともにエンジンの前方に配置するディファレンシャルギヤ反転、空間を有効活用したエンジン配置としフロントを短縮するため高い位置に置いたステアリングギヤボックスなど、5年の開発期間を投じての徹底的なダウンサイジングを図るものだ。
? トヨタでは小型化、軽量化、コストダウンなどのメカや機械要素のノウハウは今後の小型車開発に応用していくとしており、iQが成功するかどうかが今後の小型車戦略の鍵となると見られる。
? 北米市場回復に先立ち、日系自動車メーカーが先進の環境対応技術をもって欧州市場開拓にめどをつけることを期待してやまない。
第14回 HDD業界の再編に向けて
第14回 HDD業界の再編に向けて富士通がハードディスク駆動装置(HDD)事業の売却に向け、HDD世界シェア2位の米ウエスタン・デジタル(WD)と交渉しているとのニュースが報じられた。この事業買収が成功するとWDはトップシェアの米シーゲイト・テクノロジーを追撃する格好になる。折りしも富士通を主要納入先とする磁気ディスク(HD)事業でシェア3位のHOYAがトップシェアの昭和電工と同事業での統合を発表、シェア2位の富士電機デバイステクノロジーとの差を広げる形となる。HDD業界が新たな再編に動き出しているようだ。
さて、HDDでは、容量(記録密度)の増大と消費電流の低減が永遠のテーマである。日立グローバルストレージテクノロジーズでは先ごろ、HDDレコーダやセットトップボックスなどのデジタル映像機器向けに最大記憶容量1テラバイト(TB)までの幅広い容量レンジを持つHDDを開発した。据え置き型のパソコン(PC)からノートパソコンや携帯音楽プレーヤーなど可搬型に市場が広がってからは、バッテリーを長寿命化させる技術もますます求められてきている。
HDDのメカニズムとしては主に、記録媒体であるディスク(HD)と、それを回転させるスピンドルモータ、ディスク上で記録再生を行うヘッドスライダー、それを支えるサスペンション、ヘッドの位置決めを行うボイスコイルモータがある。
HDDでは、回転するディスク上に記録再生素子(磁気ヘッド)を搭載したスライダーを浮上させて記録再生を行うため、記録密度を向上させるには、ヘッドとディスクの浮上すき間を低減する必要がある。現在この浮上すき間は10nm(1nmは10億分の1m)を切るレベルまできており、ディスクとスライダーが接触する可能性が高まっている。この接触により磁気記録層にダメージを与えデータを破壊することのないよう、ディスクの記録層の上には数nm厚で耐摩耗性に優れるダイヤモンドライクカーボン(DLC)膜が、さらにその上に1分子層の潤滑油膜が施されている。一方のヘッドにもta-C膜などのカーボン系薄膜が処理されている。
さて、ディスクを回転させるスピンドルモータでは従来、高精度のミニチュア・ボールベアリングが使われていた。しかし高トラック密度化が進むなか、ボールなど軸受構成部品の微小な加工誤差などに起因する、磁気ディスク回転に同期しない磁気ヘッド移動方向の振れ(NRRO:Non Repeatable Run Out)が障害となってきた。一方、アクセスの高速化のための回転速度の向上や情報家電で必須となる静音化への対応も接触型のボールベアリングでは限界があった。たとえばトラック上で目的のセクターがヘッドに近づいてくるのを待つ時間(平均待ち時間)は、ディスクの回転数によって決まり、7,200回転で4.2?/秒、1万5,000回転で2?/秒という。つまり、高速回転にするほど待ち時間は短くなり、より速くデータにアクセスできる。
提供:ミネベア そこで登場したのが流体動圧軸受を使ったモータである。動圧軸受とは、回転軸とヘリングボーンという溝を加工したスリーブの間にオイルを封入、回転が始まるとヘリングボーン溝に沿ってオイルに動圧が発生し、油膜により非接触となったラジアル軸受ができる。また、回転軸と結合したフランジにもヘリングボーン溝が設けてあるため、回転軸を浮かせる方向にも動圧が発生し非接触なスラスト軸受が成立する。ボールベアリングと違い日接触のため音が静かで、3.5インチサーバーの1万5,000回転という高速にも対応する。さらに封入するオイルの粘度温度特性を工夫することで消費電流値を低く抑えることができる。
これらのメカニカルな技術などにより、HDDの命題である記録容量の増大と消費電力の低減、さらには信頼性向上が実現されているのである。
フラッシュメモリーがHDDを駆逐するという議論があったが、2012年のノートパソコン市場では、フラッシュを記憶媒体に使うものが約8,000万台なのに対し、HDD搭載のものは現在比4割増の約2億8,700万台(米ガードナー調べ)。HDDの活躍の場はまだまだ広がっていくようだ。HDDに関連する方々が正当な評価を受け、収益を確保できるよう、業界の健全な発展に期待したい。
第15回 国産風力発電の導入促進を
第15回 国産風力発電の導入促進を日本製鋼所が全国に保守網をもつ明電舎と組んで、国内での風力発電事業を本格化するという。国内最大手の三菱重工業は海外市場の開拓に注力、日本製鋼所が国内での風力発電機の新規設置では先行しているとはいえ、そのシェアは国内で2007年度に稼動した合計発電機18万5,750KWの1割に満たず(4,000KW)、8割以上を米国GEウインドやスペインのガメサなど欧米製が占める。 しかし海から陸に安定した風が吹く欧州の仕様の発電機は、山がちで風向きの変化が激しい日本では負荷が大き過ぎ、ブレードが折れたり軸受など部品の損傷といった事故が相次いでいる。そこで、日本の厳しい気候風土を考慮して設計された国産風力発電機が見直されてきており、その気運に乗って攻勢をかけようというわけだ。日本製鋼所では、新規設置シェア50%を目指すとしている。
風力発電機の構造
風力発電機用軸受(右はセラミックボール軸受、提供:ジェイテクト) 風力発電機は、羽根で風を受けてロータを介して主軸が回転、その10~30min‐1の回転速度を増速機により発電可能な1,200~1,800min‐1という回転速度まで増やし、発電機により発電する(誘導発電機)。現在の主流は、1~2MWのこのタイプだ。
ここでは、回転トルクを増速機に伝える主軸の軸受、増速機を構成するキャリア、遊星ギヤ、低速軸、中間軸、高速軸の各軸受、発電機用軸受が活躍している。
2007年度の故障・事故発生回数125回のうち自然現象が31%を占め、中でも落雷が多い。雷撃による軸受の被害は発電機用軸受の電食である。電食は、軸受周辺から軸受内部に電流が通過、ボールと軌道面の接触面にスパーク現象が発生し、軸受の軌道面、ボール転動面に生じる損傷。電食が進むと振動を引き起こし、軸受として機能しない。そこで電食防止のため軸受外輪の外径部から側面にセラミックスを溶射した軸受や、転動体としてセラミックスボールを使った軸受が採用されている。
日本の気候風土に適合した、安全性、信頼性を高める国産の風力発電機および風力発電要素技術が数多く採用されることに期待したい。
第16回 JIMTOF2008が開催、高効率・環境対応加工のメカ技術を披露
第16回 JIMTOF2008が開催、高効率・環境対応加工のメカ技術を披露 第24回日本国際工作機械見本市(JIMTOF2008)が10月30日~11月4日の6日間にわたり開催、累計14万2,000人が来場した。“地球に、未来に、優しいモノづくり”をテーマに、5軸制御マシニングセンター(MC)や旋盤とMCを組み合わせた複合加工機など工作機械、鍛圧機械、高速スピンドルや送り機構・テーブル機構など工作機器、MQL(最少量潤滑)などセミドライ給油機構など環境対応付帯装置、切削工具、研削・研磨工具、切削油、研削油など多くの製品・技術が展示された。
5軸MCは、これまでのXYZ軸の直線3軸に、AB軸の回転2軸を加え5軸としたもの。3軸加工機ではワーク(工作物)の複数回段取り替えを必要としていた複雑形状の加工や多面加工が、5軸加工機ではワークを載せたテーブルが回転することで1回のチャッキングでこなせる(ワンチャッキング加工)。
直線3軸の送り機構では、一般にサーボモータ+ボールねじの組み合わせで速度毎分50m以上、加速度0.5G以上、位置決め精度5μm以下の高速・高精度化が実現されている。ボールねじでは、新しいボール循環方式により毎分200mを超える高速送りと静音化を可能にした日本精工の「高速静音ボールねじ」なども搭載が進んでいる。
しかし半導体や光学素子など微細加工・超精密加工を必要とするアプリケーションでは、10nm(1nmは10億分の1m)オーダー以下の位置決め精度が要求されており、サーボモータ+ボールねじに替わって非接触構造のリニアモータによるダイレクト駆動を採用する送り機構も増えてきている。これに対して、リニアモータとボールリテーナ入りLMガイドなどの直線転がり案内(直動案内)との組み合わせで最高速度毎秒4m、加減速2Gを可能にしている(THK)。
一方、回転2軸の駆動ではウォームギヤなど減速機を用いる方法が一般的で、回転速度は毎分数十回程度でギヤのバックラッシュにより位置決め精度に限界があるなどの状態が続き、直線軸と回転軸の同期が必要な曲面加工では回転軸の性能限界が高速化を阻害していていた。これを解決するため、減速機を使わず直結して回転軸を駆動させるダイレクトドライブモーターを搭載して直線軸と回転軸の性能をバランスさせた5軸MCも森精機製作所などで出展された。
高効率な加工を実現するには、こうした「送り系」の高速化に加え、加工工具を高速に回す「主軸系」(スピンドル)の高速化が求められる。これに対しては、たとえばジェイテクトが、オイルエア潤滑で、dmn値250万の高速性能と従来タイプ軸受より昇温を15%低減する昇温性能を両立した円筒ころ軸受をリリースしているほか、NTNが、軸受側面にグリース溜り間座を設け、運転による温度変化でグリースから分離した基油のみが自動的に軌道面に給油される微量潤滑供給機構によりメンテナンスフリーで定位置予圧・dmn値190万を可能とするアンギュラ玉軸受を発表していた。また、日本精工は、極微量オイルエア潤滑や油吸引・排油システムなどの新技術により、世界最高速の毎分50,000回転のスピンドルを参考出品していた。
そのほか、MQLなど希薄潤滑下での耐摩耗など耐久性を高めたDLC(ダイヤモンドライクカーボン)コーティング被覆のエンドミルなど工具技術も含め、多くの機械要素技術の集積によって、マイクロマシンから航空・宇宙機器まであらゆる加工を実現する世界のマザーマシン・工作機械は高速、高精度、環境対応など多様なニーズに対応し続けている。
第17回 太陽光発電の効率向上
第17回 太陽光発電の効率向上太陽光発電の開発がヒートアップしている。民間調査会社の富士経済の調べでは、2012年の太陽電池市場は4兆6,000億円を上回り、07年の1兆2,000億円の3.9倍に拡大するとのこと。国内首位のシャープ、同3位の京セラ、4位の三菱電機など2010?2011年をめどに増産する計画だ。
太陽電池がかりに国内の住宅や公共施設、事業所の8割に導入された場合、国内総電力需要の約3割を賄えるという試算がある。この年間発電量は原油5,000万KL燃焼分に相当し、京都議定書による日本のCO2削減目標(2006年対比で約1.6億t)に迫る1.3億tのCO2削減につながるという。
しかしそれは太陽電池の変換効率が実用水準の10%以上であることが条件。つまりこのレベルを最低限押さえつついかに変換効率を高めるかに、各社ともしのぎを削っているのである。
太陽電池には結晶シリコン型、薄膜シリコン型、化合物型などがあり、変換効率は多結晶シリコン型で最高18.6%(三菱電機)、CISという化合物型で10?12%程度だが、薄膜シリコン型は9%程度だ。しかしシリコン原料の受給が逼迫するなか、原料の使用量が少なくてすむ薄膜シリコン型の開発が盛んで、微結晶シリコン薄膜を重ねるなどで10%以上という変換効率をクリアすべく取り組んでいる。
太陽光自動追尾システム(提供:テックオカザキ) ところでこの発電効率を高めるメカ技術がある。太陽光自動追尾システムである。
テックオカザキが開発した太陽光自動追尾システムでは、太陽光照射角分離分析センサーを搭載することでヒマワリの花のように太陽光を水平・仰角共に追尾、常に太陽光照射方向に太陽電池アレイ(ソーラーパネル)を正対させ、アレイが出力できる最大発電量を常に得る高効率太陽光発電を可能としている。
太陽光パネルは、太陽に対して正対しているときに、初めて太陽光線に対する太陽光パネルの最大発電量が得られる。一般的な住宅用太陽光発電システムは主に屋根に南向きに固定しているため、日中の一定時間(約2時間?3時間程度)しかその日の最大発電力を得ることができないが、この追尾システムを搭載することで、太陽光との正対時間が平均約6時間以上になる。季節、天候、気温条件の良い日なら、一般用固定式太陽光発電の約2倍の発電量(kwh)を得ることができるという。
太陽光追尾発電システムの駆動は、無段階リニアに(常時追尾)駆動し、日の出から日没までの太陽光の方位変化を捉え、太陽光と常に対面するように駆動する。水平駆動追尾範囲は270°で、四季による方位変化や世界の日照に対応できる。一方、仰角角度の太陽光追尾では、対面する仰角角度6?75°で無段階リニア追尾、強風時には20m/s(任意設定可能)で自動的に水平位置まで駆動する。最大垂直角度での耐風速は、60m/sという。
四季や温度、太陽光線により発電効率は変化するが、太陽光の水平方位変化を追尾することだけでも一般固定型太陽光発電システムに比べ約1.4倍程度、仰角角度も追尾することで1.7倍以上の発電効率が得られ、天候・気温によっては2倍近い発電量となることもあるという。
メカの詳細は明らかにしていないが、水平駆動、仰角駆動とも揺動アクチュエータとベアリングが使われていると思われる。駆動エネルギーを太陽光発電で得ることからモータアクチュエータであろう。
この太陽光追尾システムや、風力発電で風を最大限に受けるためブレードの角度を制御する可変ピッチや風車の向きを制御するヨー駆動装置などのように、新しい発電システムでも発電効率を高めるメカ技術が効力を発揮している。太陽電池自体の変換効率の向上とともに、こうしたシステムを強化するメカ技術の発展に期待したい。
第18回 「メカの血液」を可視化する
第18回 「メカの血液」を可視化するエンジン油可視化技術(提供:日産自動車)
日産自動車が、日本原子力開発機構とエンジン内の潤滑油(エンジン油)の流れを可視化する技術を共同開発している。原子力機構の中性子計測のノウハウを活用することで、従来難しかった装置内での潤滑油の流動状態を正確に把握、油の投入量を最適化し、関連装置を小型・軽量・簡素化しクルマの燃費向上につなげる考え。エンジン内部の油を解析する撮像システム・解析手法の開発は世界初という。
ベアリングが「産業の米」と呼ばれるのに対し、潤滑油は「機械の血液」と呼ばれる。潤滑油の機能は?油膜を作ることで摩擦・摩耗を抑え焼付きを防止する「潤滑作用」?ピストンリングとシリンダ間で油膜を作り燃焼ガスの漏れを防ぐ「密封作用」?燃焼により発生した熱を外部に逃がす「冷却作用」?燃焼や回転中に受ける応力を分散する「緩衝作用」?摩耗で発生した粒子を洗い流す「清浄作用」?金属部品の錆発生を防止する「防錆作用」などがある。エンジン油は高速、高圧、高温などの環境下にさらされるピストンリングとシリンダーライナー、クランクシャフトとコンロッドのベアリング、動弁機構などエンジン部品の動きを円滑にし、エンジンの性能を引き出すとともに保護するものである。
しかし近年、省燃費化やロングメンテナンス化などから、日米自動車工業会で組織したILSACの制定するエンジン油規格は、5W‐20、0W‐20など低粘度の傾向にある。低粘度化により粘性抵抗は低減できるが、一方で油膜切れによる摩耗防止性能の悪化が懸念される。こうした背景からも、エンジン油の流れが滞ってエンジン部品が摩耗することのないよう、必要以上の油量がエンジンに投入される傾向があったようだ。
日産は世界有数の中性子ビーム実験施設を持つ原子力機構東海開発センター原子力科学研究所の研究用原子炉を活用し、早期に潤滑油の可視化技術を実用化したいとしている。
異分野と見られるこうした技術の融合は、山積する環境や安全の課題解決にとって、今後ますます必要とされてくるであろう。
第19回 家事支援ロボットが本格化
第19回 家事支援ロボットが本格化提供:東京大学IRT研究機構 東京大学IRT研究機構が、掃除や洗濯をこなす生活支援ロボット「ホームアシスタント・ロボット(AR)」を開発した。同機構は、トヨタ自動車、オリンパス、セガ、凸版印刷、富士通研究所、パナソニック、三菱重工業が参画、ロボティクス(RT)と情報技術(IT)を組み合わせた「IRT」により少子高齢社会の問題解決を目指すもの。
今回開発したARは、車輪移動型で腰軸を持った双腕構成のロボット。サイズは幅650?×奥行き770?×高さ1,550?で、重量は130kg。広角ステレオカメラ、望遠ステレオカメラ、超広角カメラ(全方位カメラ)のほか、操作用の6軸力センサー、レーザーレンジファインダー、超音波センサーを備え周辺環境と自分の位置を認識、駆動輪2、補助輪4の計6個の車輪で移動し、首と頭部3、腕7×2、手指2×3×2、腰1、移動部2の32自由度で掃除や洗濯、食事の後片付けなどの作業を行う。動力源はバッテリで、稼働時間は30分?1時間程度。
手のひらをシャツに押しつけて、手首部分に搭載した6軸力センサーで確認。その後、3本の指を閉じてシャツを持ち上げる。洗濯機のところまで運び、ボタンを押して洗濯機のドアをオープン、洗濯機にシャツを入れたあとドアを閉め、スイッチを押して作動させる。
6軸センサーは、XYZ3軸に加えこれら3方向にかかる回転(ひねり)の6軸の力を検知する。これにより対象物の形状や重さなどの情報を把握、握る力を制御する。ARのハンド機構の詳細は明らかにしていないが、ハンドの動きを実現するメカとしては、手のひら部分にモータを置き、回転速度の速いモータ軸を減速したりモータトルクを大きくしたりするハーモニックドライブなどの減速機を経て、リンク機構が指の関節を動かすものがある。
ハーモニックドライブとは内側にある楕円形のウェーブジェネレータによって強制的に変形を起こすフレクスプラインと、それにかみ合うサーキュラ・スプラインと呼ぶ内接歯車から構成される。たとえばフレクスプラインの歯数が98枚、サーキュラ・スプラインの歯数が100枚の場合、2回分フレクスプラインが反時計回りに回転する。つまり2/100=1/50の減速費が得られる。コンパクトな減速機構としてロボットに多用されている。
IRT研究機構IRTシステム研究部門部門長の稲葉雅幸教授によると、ARの研究成果のポイントとして、特に変形するため操作が難しい柔軟物の認識と操作、またこれまでの成功の記憶に基づいて失敗したことを認識できる点が新しく、家庭内でロボットが使われる上で非常に大きな技術だとしている。
サービスロボットの市場は2025年に6兆円以上と予測されており、最近のニュースでは、米アイロボット社の掃除ロボ「ルンバ」が世界で250万台を売り上げたと報じられた。アイザック・アシモフ博士のロボットもので最初に登場するのは子守のロボットだが、いよいよ家庭で人に奉仕するロボットがお目見えする予感が高まってきた。
第20回 セミコン・ジャパン2008が開催、32nmプロセスを支えるメカ技術
第20回 セミコン・ジャパン2008が開催、32nmプロセスを支えるメカ技術半導体を中心とするマイクロエレクトロニクスの製造を支える装置・材料産業の総合イベント「セミコン・ジャパン2008」が12月3日から5日、幕張メッセで開催、約11万人が来場した。半導体は携帯電話やFPDなどのデジタル家電、カーエレクトロニクス、LEDなどさまざまな分野で適用を広げているが、共通して高集積化、小型、高速、低消費電力、低コストが求められる。それら半導体の性能は実は、各種製造工程におけるメカ技術によるところが大きい。
IC(集積回路)は写真と同じ原理で、石英板の表面に機クロムで回路パターンを描いたフォトマスク(レチクル)に光を当て、レンズによってこのパターンを1/4または1/5に縮小し、これをレジスト(感光材)が塗布されたウェハーに転写することで回路を形成する。露光済みのウェハーを現像し、不要な部分をエッチングで除去することで半導体を形成するまでのプロセスが、いわゆる「前工程」であり、ウェハー上に作られた半導体を製品として出荷するまでのプロセスを「後工程」という。
ICの高集積化とは電子回路パターンの線幅を微細化すること。現在は線幅32nmのプロセス確立に向け、特に前工程の中でもIC製造の中核技術である露光装置(ステッパー)の開発が激化している。
ステッパーで、レチクルのパターンを投影するレンズは1/4の縮小倍率では、レチクルステージはウェハーステージの4倍の速度でスキャン動作を行い、ウェハー上に微細なパターンを焼き付けていく。ステッパーでは1時間あたりに処理できるウェハー枚数をいう「スループット」の向上が課題であり、レチクルステージには露光を開始する位置に高速に移動し、高精度に位置決めする必要がある。
従来このステージには、サーボモータ+ボールねじ駆動と転がりの直線案内を組み合わせた機構が採用されていた。しかし、露光中の位置決め精度の誤差平均値は線幅の1/10以下とも言われ、現在の65nmプロセス、45nmプロセスではそうした接触機構の摩擦による振動などから、要求される位置決め精度、スキャン速度への対応が難しくなっていた。
そこで現在はリニアモーター駆動として、エアで浮上させ非接触としたエアベアリング案内のステージが主流となっている。このステージを使ったニコンのステッパーでは、1時間あたり200枚といったスループットを実現している。
※ステッパーではステッパー(ステップ&リピート)方式と、より高い解像度に対応するスキャン(ステップ&スキャン)方式がある(図)。
また、後工程でウェハー上の半導体を一つ一つ切り離す「ダイシング装置」で高スループット化に向けた開発が進んでいるほか、ウェハーの搬送装置でコンタミネーションの発生を抑えたクリーン仕様のボールねじや直動案内、多層配線のための平坦化CMP(ケミカル・メカニカル・ポリッシング)の回転機構など、32nmプロセスに向けた半導体製造技術は、多くのメカ技術に支えられている。
第021回~第030回
第021回~第030回第21回 初代新幹線「0系」が44年の歴史に幕―高速車両を支えるベアリング技術
第21回 初代新幹線「0系」が44年の歴史に幕―高速車両を支えるベアリング技術高度成長時代の象徴として登場し、「団子鼻」の愛称で親しまれた初代新幹線「0系」が11月30日に定期運転を終了、12月6日、13日、14日の新大阪?博多間臨時「さよなら運転」で、44年の歴史に幕を下ろした。
0系新幹線「ひかり」は東京オリンピック直前の1964年10月1日にデビュー。最高時速220kmで走り、特急で片道6時間半かかった東京?新大阪間を約4時間で結んだ。最高時速260Kmの仏TGVの営業開始は1981年からなので、当時の世界最高速車両だった。
0系新幹線の開発は開業の約10年前、1953年ごろから始まった。しかし実は第二次世界大戦後、GHQの指令で転がり軸受の使用が禁じられた。「転がり軸受は軍需産業であり、日本で手掛けてはならない」という主旨である。しかし転がり軸受は、高速車両の要となる技術。車軸には不可欠だ。そこで当時国鉄(現JR)技師長だった島 秀雄氏(新幹線の祖)が陳情、説得して、ようやく転がり軸受の使用が認められることになったのである。
当時の在来線の車軸軸受では封入したグリースによる潤滑が一般的だったが、0系では高速走行での信頼性を高める仕様として、タービン油による油浴潤滑方式を採用した。
ここで難しくなるのはオイルシールの技術。軸受が走行時に外気で冷やされ80℃程度なのに対し、オイルシールのリップ部分は、高速走行による摩擦熱に敏感に反応し、120℃まで上がる。シールからのある程度のオイルの漏れは許容していたようだが、大量に漏れてブレーキが効かないでは済まされない。もちろん軸受の潤滑不良による故障もまずい。当時は耐熱性、コスト、極圧添加剤への耐性などから、シール材料にアクリルゴムを使って、要求をクリアした。
以降、最新のN700系で300km/hと高速化が加速する一方、安全性を確保した上でのメンテナンス周期の長期化が求められてきている。高速運転での転がり疲労対策としては高清浄度鋼の使用や温度上昇を抑える軽接触タイプのオイルシールのほか、運行中の軸受のモニタリングシステムなども、メンテナンス周期の長期化では重要だ。
軸受、潤滑油、シールなど個々の要素技術は日々向上してきているが、その基盤に0系開発における高いレベルでの技術の積み上げがあったことを忘れてはならないだろう。産業界の活性化に向けた新たなスタートが求められる現在こそ、0系開発のフロンティア精神に学ぶところは多い。
あらためて「団子鼻」に、「ご苦労さま」と言いたい。
第22回 石油業界の再編?潤滑油開発の活性化を
第22回 石油業界の再編?潤滑油開発の活性化を 新日本石油(新日石、西尾進路社長)と新日鉱ホールディングス(新日鉱HD、高萩光紀社長)が先ごろ、経営統合を行うことで基本的合意に達した。石油精製販売、石油開発および金属の各事業を併せ持つ世界有数の「総合 エネルギー・資源・素材企業グループ」への発展などを目指す基本コンセプトをもとに、両社で本経営統合に向けた実行計画を立案し、2009年3月をめどに「経営統合に関する本契約」を締結、同年10月に統合持株会社を設立し2010年4月に中核事業会社を設立する予定。両社の2008年3月期の連結売上高は 新日石HDが7兆5,240億円、新日鉱が4兆3,395億円で、単純合計すると11兆8,635億円。国内ガソリン販売シェアが新日石とジャパンエナジー(新日鉱HDの石油部門)の合計で36.5%を占める世界10位内の石油会社が誕生することになる。だが将来的な意味合いとしては、燃料電池やヒートポンプなど新エネルギーに活路を見出す新日石と、半導体ターゲット材料など電子材料に強みをもつ新日鉱HDのシナジー効果による新たな
ビジネス創生に期待するところが大きいだろう。
統合の大きな背景としては、ガソリンなど石油製品の国内需要低迷による収益力低下への危機意識がある。石油元売各社とも、「国内市場の急速な縮小から単独での生き残りが難しい(新日鉱HD・高萩社長)」との認識を強めている。石油業界の収益悪化は、石油業界の設備過剰という構造的要因に起因している。1日あたりの原油需要は400万バレル程度だが、国内の製油所の原油処理能力は日量約480万バレルに及ぶ。両者では、「石油精製販売事業を中心に全事業部門でコストを点検し、聖域なき合理化・効率化を推進するとともに、経営統合によるシナジー効果で年600億円以上の統合効果を実現、継続的にその上積みを図って年1,000億円以上を目指す」としているが、設備過剰に対して「両製油所を含め統合から2年以内に日量40万バレルの処理能力削減を図る」(新日石・西尾社長)考えを示している。
ところでこの経営統合は、「メカの血液」である潤滑油の分野でも、大きなイベントであろう。新日石、ジャパンエナジーをはじめ石油元売会社は、エンジンオイルや油圧作動油など潤滑油のメーカーでもあり、添加剤こそ購入しているが鉱油系のベースオイル(基油)は基本的に精製し、グリースメーカーや加工油メーカーなど潤滑油専業メーカーに販売している。なかでもグループ3基油と言われる高度精製基油(高粘度指数基油)は、省燃費エンジンオイルの主要技術となっており、これをリードしているのが石油元売メーカーということになる。
近年、地球環境保全などから省燃費化などを狙ったエンジンオイルの日米自動車工業会規格(ILSAC規格)が3?4年周期で更新され、1試験項目で数千万円という取得費用も大きな負担となっている。今回のような統合でこうした負担がいくらかでも軽減され、地球環境保全に必要な開発の促進につながればと思う。
両社とも自動車用潤滑油、工業用潤滑油を幅広く扱っており、統合後には油種統一の方向に向かうと見られるが、新日石が極微量油剤潤滑(MQL)用切削油を手がけ、ジャパンエナジーがハードディスクドライブ用流体軸受モータ用潤滑油を手がけるなど、それぞれ独自分野を有している。重機からMEMSに至るまで、メカにとって潤滑油はその機能を支える重要な要素である。統合によるシナジー効果が、こうしたメカの多岐にわたる要求への対応に及ぶことを期待している。
第23回 2008年交通事故死、5,500人を下回る?シートベルト装着が奏功
第23回 2008年交通事故死、5,500人を下回る?シートベルト装着が奏功警察庁のまとめによると、わが国の2008年交通事故死者は前年比約10%減の5,155人だった。「2010年までに5,500人以下」という政府目標を前倒しで達成した。分析では、飲酒やスピードの出しすぎによる死亡事故が2?3割減少、後部座席シートベルトの着用率向上が奏功したとしている。
2007年6月14日に「改正道路交通法」が成立し、2008年6月1日から後部座席のシートベルト着用が、運転席・助手席と同様に義務化されている。
提供:タカタ 一般的な3点シートベルトは緊急時ロック式巻き取り装置(ELR、Emergency Locking Retractor)と呼ばれる装置を内蔵、衝突の衝撃で乗員の上半身が前のめりになるとその分のベルト引き出しをセンシング、それ以上ベルトが引き出されないようロックをかける。
自動車の衝突時にベルト(ウェビング)のたるみをとり除くことにより、乗員が前方に動き出す前に確実に固定し乗員の保護性能を向上する目的で装備されているプリテンショナー(図1、Pretensioner)という機構も標準装備となってきている。
提供:東海理化 プリテンショナーの作動には通常火薬を用い、火薬が爆発する際に発生するガスの力でウェビングを引き込む。衝突後10?15m/秒でプリテンショナーの作動が開始し、巻き取りは数m/秒内に完了する。
リトラクターの回転シャフトにトーション・バーを用いて、衝突時にそのバーを捻ることでウェビングを数cm引き出し、乗員の身体にかかる負担を軽減する「フォース・リミッター」(図2)という装置が働くタイプもある。
近年では、走行中に車間距離が不足するとシートベルトが軽く引き込まれ、追突が避けられないような状態でシートベルトが強く引き込まれる、センサー+モーター内蔵の「モーターライズドシートベルト」(タカタ)や、従来の衝突時に働く「プリテショナー&フォースリミッター機構」に、「モーターによるベルト巻き取り」を加えることにより衝突時の初期拘束性能が向上した、プリクラッシュセイフティシステム対応の「モーターリトラクタ付シートベルト」(東海理化)など、さらに先進安全的なシートベルト機構も登場してきている。
シートベルトは安価ながら効果が高いシステムといわれる。警察庁では2009年の目標を交通事故死者5,000人以下としているが、この信頼性の高いメカニズムを利用することで、不測の事故による生命の危機がいくらかでも減少できるよう、シートベルト装着率のさらなる向上を期待してやまない。
第24回 グリーン・ニューディールで経済活性化と雇用促進を
第24回 グリーン・ニューディールで経済活性化と雇用促進を 最近、「グリーン・ニューディール」という言葉をよく聞く。戦前の大恐慌時のニューディール政策にちなみそう呼ばれるが、「緑の内需」といった意味だそうである。米国のオバマ次期大統領は、今後10年間で15兆円を自然エネルギーやエコカーなどに投じて500万人の雇用を生み出すと提唱する。
EUでも2020年に自然エネルギーの比率を20%にする目標を立てる。英国では2020年までに風車7,000基を建設し16万人の雇用を創出すると報じている。実際、国連環境計画(UNEP)によると、風力発電事業だけで世界で30万人の雇用があるらしい。
風力発電の普及が遅れているわが国では、事業推進による雇用創出の効果はなおのこと大きいだろう。すでに本連載の第15回で報じたとおり、風力発電機は羽根で風を受けてロータを介して主軸が回転、その回転速度を増速機により発電可能な回転速度まで増やし、発電機により発電する(誘導発電機)とおり、過酷な条件でベアリングを含め多くのメカが活躍するシステムである。その普及・発展には、多分野の機械技術者によるところが大きいだろう。
わが国でもグリーン・ニューディールを意識した動きは出てきている。2009年度税制改正大綱では、「地球温暖化対策(低炭素化促進)のための税制のグリーン化」を掲げ、自動車関係諸税の見直しによる低炭素車の普及拡大を盛り込んでいる。「低公害車・低炭素車のうち、2009年4 月1 日?2012 年4 月30 日までの間に新車に係る車検を受けるものについて、自動車重量税の減免措置を講ずる。また、同期間に初回の継続検査等を受ける低公害車・低炭素車についても、自動車重量税の減免措置を講ずる」というものだ。
こうした背景もあり、電気自動車(EV)の開発や試験運用も進んでいる。たとえば三菱自動車では、電気自動車「i MiEV(アイ ミーブ)」を東京電力、九州電力、中国電力、関西電力、沖縄電力、北海道電力、北陸電力といった複数の電力会社や、北陸3県(福井、石川、富山)、神奈川県といった地方自治体と実証走行試験を実施、先ごろコンビニエンス・ストアのローソンにも試行配備している。三菱自動車では、2009年夏の国内市場投入に向け開発を進めているという。
同EVは、現在主流のガソリンエンジン車とは機構がまったく異なる。エンジンの代わりに小型の永久磁石式同期モーターを搭載、変速機を持たずにモーターから駆動輪(後輪)までドライブトレインが直結している。モーター特有の速い応答性を生かし駆動輪のスリップ制御を行い、減速時のエネルギーを回生ブレーキにより回生するため、減速回生時のスリップ率も制御し、加速域から減速域まで高い安定性を確保している。開発されたEV用リチウムイオン電池では、10・15モードで130kmの走行が可能で、さらに航続距離延長を狙う。いずれもガソリンエンジン車とは違うコンポーネンツを積んでいる。現状ガソリンエンジン車による省燃費化の開発も活発に進められており、EVが上市されたからといってガソリンエンジン車の市場が経済の要因を上回って急激に縮小することは考えにくく、これまでとは違う自動車および自動車部品の市場が創出されると考えても、間違いではなかろう。
年初から、主だった産業における生産・販売見通しの縮小などのニュースが取りざたされているが、今こそ自社の位置づけや得意とする技術を再認識しつつ、時流を見ながら今後の事業展開をじっくりと見据える好機だと考える。蓄積してきた技術が新しい産業の台頭によって完全に駆逐されることはないと信じる。また駆逐されることなく新しい産業でも重用され続けるよう、保有技術の研鑽と進化に努めたい。
第25回 日本の衛星打ち上げビジネス本格化?ロケットを支えるベアリング技術
第25回 日本の衛星打ち上げビジネス本格化?ロケットを支えるベアリング技術三菱重工が韓国航空宇宙研究院(KARI)からH-IIAロケットによるKOMPSAT-3の衛星打上げを受注、世界を相手にした衛星打ち上げビジネスが本格化する。成功率9割以上というH-IIA ロケット打ち上げの実績と信頼性の高さが評価され、今回の受注につながった。
H-IIAロケットのエンジンでは、エンジン性能の一層の向上と大幅な軽量・長寿命化、信頼性の向上が要求されている。ロケットエンジン用ターボポンプの小型・軽量化では、液体水素(-253℃)や液体酸素(-183℃)の極低温推進剤を燃焼器に供給するターボポンプの高速化が必要になるほか、現在の多段式ロケットにおける上段用ロケットエンジンでも、その重さや性能が衛星などの打上げペイロードに大きく影響するため、回転数が100,000rpm級のターボポンプが有利になる。
これに対し宇宙航空研究開発機構(JAXA)では、液体水素の中など潤滑剤が使えない状態で、120,000rpmの回転を実現するロケットターボポンプ用「外輪片案内軸受」(写真)を開発、搭載している。この軸受は、高速性能や冷却性能に優れる外輪片案内方式を採用した、窒化ケイ素セラミック玉を用いたハイブリッドセラミック玉軸受を開発し、液体水素を使った性能試験で、高速性の指標となるDN値(軸受の内径(?)×毎分の回転数(rpm))が300万で、回転数が120,000rpmという世界最高速を達成している。ポイントは三つだ。
第一に、軽量で極低温下でも耐摩耗性に優れる窒化ケイ素セラミック玉を使用することで、高速回転時に発生する遠心力荷重が鋼玉に比べ約60%減少でき、軸受の発熱や摩耗を抑えられる。窒化ケイ素セラミック玉は、鋼玉に比べPTFE潤滑膜が厚く付着するため高い荷重を支えることができる。
第二に、特殊な表面処理により潤滑性を高めたガラス織布強化PTFE保持器を使用して、極低温でも玉や内外輪に付着させたPTFE潤滑膜で軸受を潤滑する
第三に、外輪片案内方式の軸受を採用することで、軸受トルクが従来の外輪両案内軸受の約1/2になるため、超高速回転で問題となる摩擦発熱は、回転数120,000rpmで4kW程度と大幅に減少できる。特殊な平円ポケット形状を採用して、高速回転する、外側の案内面が片側しかない保持器の振動発生を抑えている。
H-IIAロケットは設計の簡素化や製造作業・打ち上げ作業の効率化により、最高約190億円であった打ち上げ費用を最新モデルで90億円未満)と1/2以下に抑え、世界市場の相場である100億円未満を実現している。信頼性が高く、世界的にも優れたコストパフォーマンスを誇る技術で、打ち上げビジネスという、わが国では新しい産業が、いま本格化へ。宇宙へと広がるビジネス。ここで紹介したベアリングをはじめメカ技術の活躍する場が創出されつつある。
第26回 米国オバマ大統領始動、科学技術での景気浮揚に期待
第26回 米国オバマ大統領始動、科学技術での景気浮揚に期待提供:在日米国大使館 バラク・オバマ氏が第44代米国大統領に就任した。環境対策を兼ねた「グリーン雇用」のため、今後10年間で1,500億ドル(約15兆円)を投資する方針を表明しているが、中でも「科学技術・イノベーション政策」として、基礎研究への投資拡充を掲げていることは、腰をすえた科学技術振興政策として期待したい。
すでに公表されているオバマ政権の科学技術政策メンバーとしては、科学技術担当大統領補佐官に環境・エネルギーを専門とするハーバード大学教授のジョン・ホルドレン氏を、大統領科学技術諮問委員会共同議長として同氏と、1989年にノーベル生理学医学賞を受賞しているハロルド・バーマス氏、ゲノム専門のマサチューセッツ工科大学教授のエリック・ランダー氏を指名した。また、海洋大気局局長に環境・海洋を専門とするオレゴン州立大学教授のジェーン・ルブチェンコ氏を、エネルギー省長官に1997年にノーベル物理学賞を受賞しているスティーブン・チュー氏を指名している。この顔ぶれからも基礎研究の充実と次世代へのイノベーションに向けたオバマ大統領の強い意志がうかがえる。
「脱石油」を中心とする風力発電など代替エネルギーの技術開発のほか、ES細胞、iPS細胞などライフサイエンス研究など、われわれのテーマとする人と環境に貢献する技術の創生と、それらに基づく雇用の創出にむけた動きからは目が離せない。
ところで、オバマ氏の選挙中に、ミシガン大学機械工学科のジョン・ハート准教授が、ナノ・リソグラフィーを用い1億5000万本のカーボンナノチューブ(CNT)を使ってオバマ氏の顔を作った。ハート氏は「カーボンナノチューブはその電気特性と熱特性など次世代材料として期待度の高い材料だが、商業的利用に、大量のナノチューブをまとめる効果的な方法が必要」と語ったというが、オバマ大統領の科学技術信仰政策への期待がこめられたセリフであろう。カーボンナノチューブはMEMS(微小電気機械、マイクロマシン)など微細・微小なメカの潤滑要素としても注目されている。
わが国でも先ごろ、米国はじめ各国にならいグリーン・ニューディール政策の模索を表明しているが、こうした基礎研究の強化とも歩調をそろえた、堅実で力強い取り組みであってほしいものだ。
第27回 バイオ燃料の市場が拡大へ?求められるバイオ対応技術
第27回 バイオ燃料の市場が拡大へ?求められるバイオ対応技術石油業界がこの4月からサトウキビやトウモロコシなどから作るバイオエタノールとイソブテンを合成したバイオETBE(エチルターシャリーブチルエーテル=エタノール)をガソリンに混ぜた、バイオガソリンの販売を本格化させる。
日本は、1997年に締結された国際条約「京都議定書」で2008?2012年(第一約束期間)には1990年との対比で「温室効果ガス」の排出量を6%削減することとしている。京都議定書では、植物を原料とするバイオ燃料を燃焼させた場合には、次世代の植物が光合成によってそれを吸収して育つため、大気中のCO2の総量を増加させないという考え方(カーボンニュートラル効果)から、バイオ燃料の燃焼によって排出されたCO2を温室効果ガス排出量として計上しないことにしている。
そこで石油業界では、2007年4月27日から首都圏(東京都、神奈川県、埼玉県、千葉県)50箇所の給油所で一斉にバイオETBEを3%配合したレギュラーガソリン(バイオガソリン)の試験販売を開始、2008年春からはその数を順次100箇所に増やし、本格導入に向けた取組みを進めていたが、2010年度にはETBEの使用量を08年見込みの約80倍となる84万kLに増やす目標を掲げている。 一方、食用油や廃食用油にメタノールを加えて作った脂肪酸メチルエステル(FAME)が、軽油代替のバイオディーゼル燃料である。ゴミ収集車や路線バスの燃料として自治体を中心に使われている。全国バイオディーゼル燃料利用促進協議会(JAROA)によると、2007年度の国内生産量は約6,200kLだが、自家用に生産する事業者もありこの自家消費も含めると国内生産は約1万kLにのぼるという。
バイオディーゼル燃料をそのまま使う「B100」では自動車の部材の腐食や燃料系統の目詰まりを引き起こしやすいことから、2006年3月の揮発油等の品質の確保等に関する法律(品確法)改正で、バイオディーゼル燃料をの混合比率を5%とした軽油(B5)の品質規格が定められているが、東京都では2007年から混合比率10%のバイオディーゼル燃料(B10)によるハイブリッドバスの試験運転も始めている。
潤滑油協会(JALOS)が、自治体、運送業、バス会社などバイオディーゼル燃料を保有する事業所を対象に調査したエンジン油の使用状況の実態調査(2007年)では、何とB100が圧倒的に多く、品確法規定のB5はわずか。JALOSによる台上エンジン試験結果では、FAMEのB5軽油を使用したエンジン油劣化への悪影響確認されず、使用実態の調査結果でもエンジン油の交換間隔は3万kmまたは6ヵ月と一般軽油と同等だったのに対し、B100を使った車両のエンジン油交換間隔は5,000km前後が多くを占め、長くても1万kmだった。
同調査では軽油との違いとして、その弱いスス生成傾向から排気煙(黒煙の発生)が良好という意見が多い一方で、主にB100で出力の悪化やエンジン始動性の悪化、さらに燃料フィルタの詰まりやインジェクタの詰まり、エンジンの異常、特にピストンリング周りの異常などが挙がったという。
ディーゼルエンジンは国内ではトラックなどの長距離運行、バスなどの高頻度運行に使われ、その燃料とエンジンを保護するエンジン油には高信頼性とロングライフ性能(酸化安定性)が求められる。部品・材料へのニーズも同じである。特に欧州ではディーゼルエンジン乗用車、さらには混合比率の高いバイオディーゼルを使った乗用車の割合も高まってきている。将来的には、欧州市場、ひいては世界市場の攻略では混合比率の高いバイオディーゼルへの潤滑油やエンジン部品、シール材などの技術対応が強く求められるであろう。世界的に政策的に広がりつつあるバイオ燃料という市場に対して、メカ技術の研鑽に期待がかかっている。
第28回 エレベータの安全性向上で、保全、新設の市場あり
第28回 エレベータの安全性向上で、保全、新設の市場あり国土交通省は、エレベータなどで起きた重大事故の原因を専門に調べる事故対策委員会を設置する。事故機を調査し原因究明、結果を早期に公表して再発防止に役立てる狙いという。ここ数年、たしかにエレベータの事故が増えてきている。エレベータの法定耐用年数は17年で、国内ではモダニゼーション対象となるエレベータは10万台規模に達していて、毎年約1万台が積み上げられていくという。エレベータの新設台数が約2万台と頭打ちとなっている一方で、修理・改修市場は強含みとなっているのである。
提供:日本エレベータ協会 一般にエレベータのかごは、昇降路上部に設置された巻き上げ機によりメインロープを介して駆動される。かごは、ガイドレールに沿って走るように、ローラとばねサスペンションを組み合わせた案内装置により案内される。これら機構のうち、労働安全衛生法では、事業者はエレベータについて1ヵ月ごとの1回定期に、(1)安全装置、(2)ワイヤーロープ、(3)ガイドレールなどについて自主検査を行わなければならないとしている。
また国土交通省社会資本整備審議会の建築分科会建築物等事故・災害対策部会での検討の結果、昨年4月1日付けでエレベータの定期検査報告制度が改正された。(1)ブレーキパッドの摩耗について、摩耗の程度を測定し検査結果表に測定値を明記(測定値により結果の判定を行う場合)するとともに、結果の判定基準を明確化する。(2)ワイヤロープの損傷については、目視により一定の基準(おおむねJISの基準を告示に規定することにより判定基準の法令上の位置づけを明確化)を満たしていることを検査する、というもの。ワイヤロープや、ブレーキパッド、ガイドレール、ローラなどの部材や潤滑、状態監視機器、計測評価機器などを包括したメンテナンス市場に関わる技術・製品への需要は高まりを見せてきている。
一方、東芝エレベータが台湾・台北市の世界最高層ビル「TAIPEI101」向けに納入した分速1,010mの世界最高速エレベータなど、新設エレベータでは高速化とともに安全な運行と同時に快適性、つまり走行中の振動や騒音を抑える技術が求められている。
一般的なエレベータではローラガイドによって、かごをレールに沿って走行させるとともに走行中の振動を吸収して乗り心地を確保しているが、このローラ式ではレールの表面状態などにより振動や騒音が発生してかご内に伝わることがあり、特に高速エレベータではこれらの乗り心地が確保されにくい。
そこで、東芝エレベータでは、磁気浮上技術によりガイドレールとの機械的な接触をなくし、レールの表面状態の影響を受けずに低騒音な案内装置とし、乗り心地を改善する磁気ガイドシステムの開発を進めている。
少子高齢化の進む背景からも、公共輸送の利便性を図るエレベータの安全性を確保する保全のシステム、また安全性とともに高速輸送を可能にする新規なシステムへの重要性はますます高まってきている。
第29回 安全性と環境を両立する低燃費タイヤの開発に拍車
第29回 安全性と環境を両立する低燃費タイヤの開発に拍車経済産業省( http://www.meti.go.jp )と国土交通省( http://www.mlit.go.jp )は、運輸部門のエネルギー消費効率の向上を目的に、自動車で使用されているタイヤについて「低燃費タイヤ等普及促進協議会」を設置、今後のタイヤに関する省エネ対策として転がり抵抗の測定方法の規格化などに取り組む。
わが国運輸部門のエネルギー消費量は近年減少傾向に転じているものの、全体の約2割を占めている。また、国際エネルギー機関のレポートによれば、自動車の燃料燃焼により発生するエネルギーの約20%がタイヤの転がり抵抗によって消費されており、現在一部の新車で自動車の燃費基準達成に向けた燃費性能改善策の一環として自動車メーカーが転がり抵抗を下げた低燃費タイヤを選択したり、またタイヤメーカーが独自の低燃費タイヤの生産・販売を行うなどの取組みがなされている。
一般にタイヤの転がり抵抗とブレーキ性能(特にウエット路面でのブレーキ性能)はトレードオフの関係にあり、転がり抵抗を増やしたハイパフォーマンスタイヤでは制動距離が短く、転がり抵抗を下げた低燃費タイヤでは制動距離が長くなる。これはトレッドゴムの粘弾性に依存する性質で、単に転がり抵抗を下げて低燃費化を図ろうとするだけでは安全性が損なわれることになる。
提供:HONDA そこで、たとえばHONDAではタイヤ設置面を解析し、ブレーキには外側・内側の二つのトレッドショルダー部が主に機能し、定常走行時の燃費にはトレッドセンター部が大きく寄与することを解明。その3分割したトレッドのそれぞれの部位に最適なゴム材料を配することで、同じ転がり抵抗係数を持つタイヤに比べて制動距離を5m短縮、トレードオフの関係にある転がり抵抗と制動性能を高次元で向上させ、燃費も1.5?2%低減させている。
しかし、将来的には安全性を確保した上でタイヤの転がり抵抗を半減することが要求されており、自動車メーカー、タイヤメーカー、材料メーカーの共同による開発が必要とされている。「低燃費タイヤ等普及促進協議会」設立を機に、関連業界が一丸となった安全性、環境保全改善の取り組みに期待したい。
第30回 ASTEC2009展開催、機械を長寿命化、円滑にする表面改質技術
第30回 ASTEC2009展開催、機械を長寿命化、円滑にする表面改質技術ASTEC 実行委員会(事務局:ICSコンベンションデザイン)は2月18日?20日、東京・有明の東京ビッグサイトで「ASTEC 2009 国際先端表面技術展・会議」を開催、約4万7,000人が来場した。
ASTEC展では、表面改質技術とそれにより改質された表面を測定・評価する技術が多数展示された。機械部品にとって表面改質技術は、潤滑油剤と併用され、あるいはその代わりに使われ動きを滑らかにする潤滑性・低摩擦特性を与え、ロングライフにする耐摩耗性を付与する省エネ、省資源の技術である。
提供:ナノテック 特に今回出展が多かったのはDLC(ダイヤモンドライクカーボン)コーティングとその試験・評価機器。DLCはダイヤモンド状炭素の名のとおり、ダイヤモンドに近い硬度(耐摩耗性)と炭素に近い低摩擦特性を持つ。その耐摩耗性と離型性などから非球面レンズなど光学部品の金型などのほか、潤滑性と耐摩耗性などからHDD(ハードディスクドライブ)のディスク保護膜などに、しゅう動特性などから自動車動弁系部品(日産自動車)などに、耐摩耗性や低摩擦特性などから4WD電磁クラッチ(ジェイテクト)などに適用が広がってきている。
しかし、DLCと一口に言ってもシリコン(Si)含有DLCや水素フリーDLCなど様々で、物性も広い範囲で異なる。DLCの事業化にいち早く取り組んでいたナノテックでは近年、その膜の物性を制御して機能を明確にしたICF(Intrinsic Carbon Film、真性カーボン膜)を開発、医療分野では生体適合性ICF、エネルギー分野ではシリコン材料に代わる太陽電池用ICFなど、機能性コーティング膜で新分野を開拓する。
提供:不二WPC また、不二WPCで出展していたのは、金属製品の表面に目的に応じた材質の微粒子を圧縮性の気体に混合して高速衝突させるという表面改質技術WPC。微細で靭性に富む緻密な組織が形成され表面を強化すると同時に、 表面性状を微小ディンプルに変化させることで摩擦・摩耗特性を向上させる。固体潤滑剤の二硫化モリブデン粒子をWPC処理したピストンスカートやエンジンベアリングなどはフリクション低減や耐久性改善が図られている。
表面改質技術は母材にない特性・機能を表層に付与する。高価な材料を使わずにその表面だけ性質を変え必要な機能をもたせることができる、低コスト化にも貢献する技術で、HONDAで採用されているWPC処理ピストンやセミドライ加工用として採用されるDLCコーティング切削工具など、 環境負荷低減にも有用である。トータルコストダウンは常変わらぬ製造業での命題だが、特にこの不況下にあってはプラスに転じる取り組みの一つでもある。数ミクロン、時には数ナノの膜が機械システムを機能させる表面改質技術。その研究開発を支える試験・評価機器も含めて技術の深化と適用の拡大を望む。
第031回~第040回
第031回~第040回第31回 FC EXPO 2009開催、環境と安全に貢献するメカ・加工技術
第31回 FC EXPO 2009開催、環境と安全に貢献するメカ・加工技術
「FC EXPO 2009 第5回国際水素・燃料電池展」が2月25日?27日、東京・有明の東京ビッグサイトで開催、自動車用および定置型燃料電池を中心に多数の技術が展示された。
提供:JHFC 燃料電池は、燃料流体の水素ガスと、酸化用流体(空気に含まれる酸素)とを電気化学的に反応させることにより発電を行う。自動車で主流の固体高分子型の燃料電池の場合、各発電体部分は、固体高分子からなる電解質膜を酸素側電極と燃料側電極とで挟み込んだ構造を有し、酸素側電極には酸素を供給するために空気が供給され、燃料側電極には燃料流体が供給され、電気化学的な反応により発電が行われる。
提供:JHFC 発電に際しては、固体高分子型の燃料電池では、イオン交換膜でありプロトン伝導体膜として機能する電解質膜中をイオン(プロトン)が移動し、酸素側電極の酸素と反応して電流が発生し、同時に酸素側電極では水が生成される。燃料電池の発電体部分は、電解質膜・電極複合体またはMEA(Membrane and Electrode Assembly)と呼ばれ、この電解質膜・電極複合体を燃料流体流路や空気流路が形成されたセパレータで挟み込んで発電セルとし、300枚にも及ぶ発電セルを積層することで積層構造(スタック構造)の燃料電池が構成されている。
航続距離を延ばすためには多くの水素を貯蔵しなくてはならず、一般的には35MPa(350気圧)、将来的には70MPa(700気圧)という高圧で圧縮した水素を積むことになる。水素ステーションから車載タンクへ、車載タンクから発電セルへ、流量をコントロールしながら受け渡しする機器では、高圧水素雰囲気下でのバルブやシール、軸受など機械部品の信頼性が求められる。
提供:トヨタ自動車 たとえばトヨタFCHV-advでは70MPa高圧水素タンクを搭載、衝突を検知した瞬間にタンクのバルブを閉じ水素の漏れを防ぐ構造としている。センシングとともにバルブシールなどが滑らかに動く必要がある。九州大学では摩擦摩耗特性に優れるPTFE(四フッ化エチレン)などのシール材料の水素中での特性を調べている。
一方、加工技術も重要である。発電セルのセパレータには、燃料流体流路や空気流路が形成されている。裏表で直交した溝形状となっているのは、表面積を増やし水素を効率よく通過させるため。耐食性に優れるステンレス材料で高精度な流露を確保するには、プレス加工の後にバリの処理などが不可欠で、ここでは独自の砥粒を用いた特殊なブラスト加工などが適用されている。
提供:JHFC? 燃料電池車は水素と酸素の化学反応により発電を行い、そこで発生した電気エネルギーでモーターを回して走行する。従来の内燃機関と比べエネルギー効率が高く、エンジン音もなく、大気汚染の原因となる窒素酸化物(NOX)や硫黄酸化物(SOX)、粒子状物質(PM=すす)の排出が極めて少ものの、取り扱いの難しい水素を制御し安全性を確保するには、その特殊環境下で機能を発現するメカ技術と部品を形成する加工技術、材料技術によるところが大きい。電気化学的にエネルギーを生み出す燃料電池でもメカの活躍する場面は多そうである。
第32回 小型農機市場で技術革新?自ら作る食の安全
第32回 小型農機市場で技術革新?自ら作る食の安全提供:Honda Hondaが、鍋物でおなじみのカセットコンロ用ブタンガスを燃料とする小型耕運機「ピアンタ FV200」を3月3日に発売した。同社によれば、「食の安全」への関心の高まりや団塊世代の支持を背景に国内のガーデニングおよび家庭菜園市場は3,000万人以上に上ると言われる。市民農園の数もこの10年ほどで倍増、これに伴い小型耕運機市場も近年徐々に拡大し、05?08年でトラクターなど大型農機の出荷台数が2割程度縮小する一方で、小型農機市場は2004年の11万6,000台年から、2013年には約18万台に成長すると試算されている。Hondaは従来のガソリンエンジンなどから燃料交換を容易にしたことで、この成長する小型耕運機市場を掘り起こす考えだ。
小型耕運機は、耕運爪が車輪と同じ軸に取り付けられた車軸型、前に取り付けられたフロントロータリー型、後ろに取り付けられたロータリー型などがあるが、いずれもエンジンの回転とともに耕運爪が回転し、土を耕す。抵抗棒を上下させることで耕す深さや前進のスピードを制御する。
従来はガソリンエンジンや高出力タイプでディーゼルエンジンが使われてきたが、「給油時に手が汚れる」「保管が難しい」などが課題となっていた。これに対し家庭用カセットガス燃料は購入・使用・保管が容易で、装填もカセットコンロと同様に簡単。ビギナーでもより手軽にガーデニング(家庭園芸)や家庭菜園が楽しめる上、同排気量のガソリンエンジンに対し作業時間あたりのCO2排出量を約10%低減しているという。
Hondaの新製品は、ガソリンタイプとほぼ同じ仕様で、総排気量49.4 cm3の空冷4ストローク単気筒OHVエンジンは連続定格出力/回転数(kW[PS]/rpm)が1.0[1.4]/4,600、最大出力/回転数(kW[PS]/rpm)が1.1[1.5]/5,000で、遠心クラッチの採用により、スロットルレバーを握ると耕幅350/200?(内爪時)、爪径 250?のローターが135 rpmで回転し、放すと止まる。カセットボンベ1本(内容量250g)で約1時間稼働でき、約32坪(106m2)の耕運作業が可能なほか、スロットルレバーから手を放すとエンジン回転数が自動的に下がるため、低燃費を実現するとともに騒音を低減するとしている。
ビジネスとしての農業への回帰が取りざたされる中、こうした小規模な農作業から本格化を試行する層もいるかもしれない。微増とはいえ拡大する小型耕運機市場で、ビギナー層取り込みに有用なこうした技術のエッセンスは他分野でも転用できそうである。
第33回 宇宙エレベーター実現へ活動が本格化
第33回 宇宙エレベーター実現へ活動が本格化任意団体の日本宇宙エレベーター協会(JSEA、 http://jsea.jp/ )が、宇宙エレベーター実現に向け研究情報の発信など活動を本格化する目的で社団法人化する。現在宇宙分野の研究者ら約200人の会員を年内に300人超に、3?5年をめどに500人以上に引き上げたいとしている。
地上400kmの高度を周回する国際宇宙ステーションが時速28,000km、地球を1日で19周するほどの速度が必要なのに対し、赤道上空の静止衛星は地上36,000kmの高度で時速10,800km、24時間で地球を1周している。地球が1日で1回転するのと同じスピードで回っているため止まっているように見えるのが、静止衛星と呼ばれるゆえんである。
宇宙エレベーターは、静止衛星から地上に向けてテザー(ベルト状のワイヤー)を垂らし地上に届け、そのテザーを自走式のクライマー(昇降機)が上り下りする仕組み。だが、テザーをどんどん伸ばして地上に近づけていくだけでは、テザーの重みで全体の重心が地球に近づき落ちてきてしまう。そこでいつも全体の重心が釣り合うように静止衛星の上にもテザーを伸ばしていく。静止衛星は頻繁に軌道修正するため、テザーの端部、地上の基部はそれを受けて移動可能な人工島が考えられ、移動式のメガフロート(浮き島型の人工島の一種)や浮遊型の海上石油掘削基地のようなものが使われる。
原理はこうだが、実際に宇宙エレベーターを建設するには課題が多い。まずは、引っ張り強度が同じ重量で鋼鉄の180倍必要という、テザーの材料。軽く強い材料としてカーボンナノチューブ(CNT)が注目され、2007年現在、必要な強度の1/3程度まで実現するCNTの量産技術が確立されてきているという。
そのテザーを上り下りするクライマーはモータと摩擦車を使って自力で動く機構が提案されている。これらメカは、(1)太陽からの電磁波や放射線、熱による影響、(2)隕石やスペースデブリの問題、(3)高空に存在する原子状酸素の問題、(4)振動の問題、(5)地磁気による誘導起電流の問題など多くの宇宙空間に特有の課題にさらされながら、輸送運動の信頼性を確保しなければならない。
ロケットは重量のほとんどを燃料が占め、スペースシャトルが低軌道に29tの貨物を打ち上げるのに用いる燃料は1,900tで、効率は1.5%程度という。そのため、現在H2Aロケットの場合で貨物1kgあたりの輸送コストは105万円と言われる。これに対し宇宙エレベーターでは、モータ駆動による昇降でロケット燃料が不要となることから20t程度の貨物を頻繁に上昇でき、仮に年間50回ほどの上昇を行った場合、1kgあたり1万円、年間100回となれば同5,000円の低コスト輸送になる。この宇宙への安価なアクセスは、月や火星への人類の進出も可能にする。重力がそれぞれ地球の1/6、1/3の月や火星には、スケールの小さな、より低コストの宇宙エレベーターが建設できるという。
本年8月8日、9日に千葉県船橋市の日本大学二和校地で宇宙エレベーター協会が主催する「第1回宇宙エレベーター技術協議会」が開催される。こうした取り組みを通じて、宇宙への気軽な進出を容易にする宇宙エレベーターの技術が着々と確立されていくことに期待したい。
第34回 若田宇宙飛行士、ISSに長期滞在、実験・研究をスタート
第34回 若田宇宙飛行士、ISSに長期滞在、実験・研究をスタート写真提供:NASA 若田光一宇宙飛行士が搭乗したスペースシャトル「ディスカバリー」は、日本時間3月18日に国際宇宙ステーション(ISS)にドッキング、若田さんらクルーがISSに入室した。宇宙空間という特別な環境を利用して、地球・天体の観測や、宇宙での実験・研究などを行うISSで、若田さんは日本人初となる長期滞在をスタートさせた。今後約3ヵ月間にわたり宇宙に滞在し、様々な実験を行う。約3ヵ月後のミッションで運ばれる「きぼう」日本実験棟船外実験プラットフォームと船外パレットをISSへ取り付け、「きぼう」を完成させた後、帰還する予定。
日本の有人実験施設「きぼう」は、船内実験室と船外実験プラットフォームの二つの実験スペースからなる。船外実験プラットフォームは、宇宙空間を長期間利用する実験や天体観測・地球観測などに使われる予定で、船外環境をそのまま使用することができるISSの中でも独自の施設。ロボットアームは、この船外実験プラットフォーム/船外パレット上にある実験装置や搭載機器の交換作業、各種実験支援または保守・保全作業の支援を行う。
ロボットアームは、主に「親アーム」、その先端に取り付けられる「子アーム」と、「ロボットアーム操作卓」から構成される。親アーム、子アームは共に六つの関節を持っていて、人間の腕と同じような動作が可能。本体の親アームは、船外実験装置など大型機器の交換に使用し、先端の子アームは、細かい作業を行うときに使用する。
さて、日本の産業用ロボットは世界でも最高水準の技術を擁するが、宇宙空間で使われるロボットアームは生産ラインで使われるのとは条件が違う。宇宙空間は真空で、原子状酸素や放射線などに曝され、地上のメカのような普通の潤滑油・グリースが使えない。
たとえば軽量・省スペースで1/160という大きな減速比を実現する、ロボットアーム関節に使われる宇宙用ハーモニック・ドライブ減速機は、低蒸発でトルク損失を軽減する宇宙用真空グリース・オイルが適用されている。これは、合成炭化水素油MAC(Multiply Allkylated Cycropentane)をベースにしたものである。宇宙用ハーモニック・ドライブ減速機のベアリング保持器は、その潤滑剤を含浸するのに適しているフェノール樹脂で作られている。
また、宇宙空間に直接曝される部位の軸受には宇宙用グリース・オイルが使用できないため、二硫化モリブデン(MoS2)焼成膜による固体潤滑が多く使われている。
ところで、若田さんは日本時間17日のスペースシャトル「ディスカバリー」搭乗中に、自ら開発に携わったロボットアームを操作し、カメラ付きの検査用延長アームを駆使して、打ち上げ時の衝撃でシャトルの機体が傷ついていないか、点検作業を行っている。延長アームは、2003年打ち上げ時の断熱材損傷が原因で起きたスペースシャトル「コロンビア」の空中分解事故を受け開発されたもので、今回は帰還時に船体を高熱から守る耐熱材をアーム先端にあるカメラとレーザー装置で点検した。
若田さんは以前、ロボットアームの操作はパイロットの操縦に似ているといった発言をしており今回も見事なアーム操作を実現したが、地上と同様のアームのモーション・コントロールを実現するには潤滑を含め機械要素技術側の課題も多いだろう。ミッションの安全信頼性を確保する上で、宇宙環境で機能・耐久性を実現するメカ技術のレベルアップが引き続き求められよう。
第35回 自動回転ドアの挟まり事故を防ぐ安全設計
第35回 自動回転ドアの挟まり事故を防ぐ安全設計2004年3月に東京・港区の六本木ヒルズ森タワーで大型自動回転ドアに児童が挟まれ死亡した事故に関して、問題の自動回転ドアのメーカーである三和タジマが、衝撃力低減や空間確保など安全性により配慮した製品を開発、市場に投入する。同社では、工学院大学教授・畑村洋太郎氏の協力を得て事故機を動態保存するなど、理念である「安全、安心、快適の提供で社会に貢献する」ことをめざし事故原因の検証とそれらに基づく開発を進めていた。事故以来自粛していた販売を5年ぶりに開始する。
事故当時の自動回転ドアにおける安全設計は、センサーでぶつかったことを検知し機械を止めるというもので、ぶつかったときの衝撃力や機械がすぐに停止しない場合の非難手法などが施されていなかった。
これに対し三和タジマでは今回、センサー検知エリア、制動距離などの基準値および点検要領を「ガイドライン」、「安全対策マニュアル」と「東京都建築安全条例」に沿って明確化、人や障害物をセンサで検知するやすぐに回転を停止するほか、万が一扉と方立の間にはさまれた場合には、その負荷を瞬時で感知し回転方向と逆側へ折れ、衝撃を低減しつつ非難空間を確保する機構「戸先折れ戸機構」を採用した回転自動ドアを開発した。回転部(扉・センターコア)の材質も従来のステンレス製からアルミ製に変更しぶつかった際の衝撃力を低減する。
こうした安全対策を施した回転自動ドア「レボフォート」は、国土交通省・経済産業省の「自動回転ドアの事故防止対策に関するガイドライン」と日本工業規格「JIS A 4721自動回転ドア・安全性」に適合するとともに、1分間に2.5回転の動作で、内径φ3,600?の1区画定員2人のタイプで1時間あたりの通行可能人員が約1,200人、φ4,200?の定員3人のタイプで同約1,800人、φ4,800?の定員4人のタイプで同約2,400人という高効率な建物での入退出を可能にしている。
特に高層ビルの場合、省エネや空気圧の関係から回転ドアを利用する利点があり、高層ビル建設に伴う自動回転ドアの潜在的な需要は非常に多い。回転ドアの利点を活かしつつ、「安全、安心、快適の提供で社会に貢献する」、より安全性の高い自動回転ドアの開発・市場投入を望む。
第36回 建設機械のハイブリッド化が進展
第36回 建設機械のハイブリッド化が進展2月に発売開始のHonda「インサイト」がすでに受注台数2万台を超えるなど自動車業界でのハイブリッド競争が激化してきている一方、コマツなど建設機械各社においても、ハイブリッド化が進んできている。ただし、自動車のハイブリッド化がガソリンエンジン+発動機(モーター)なのに対し、建機の場合はディーゼルエンジン+モーターである。建機のハイブリッド化は、2011年から窒素酸化物(NOx)や粒子状物質(PM)の一層の削減を目的に日米欧で導入される第4次排出ガス規制に対応しつつ、CO2排出量の削減を図る動き。
掘る・埋める・ならす・吊る・運ぶなど土木工事や建築工事に不可欠な建設機械は、(1)熱効率が良く経済性に優れる(2)耐久性に優れる(3)低速回転でも高トルクが出せる(4)数馬力?数万馬力にまで対応ができるので、同一現場で稼動する大型建機からミニ建機まで同じ燃料で稼動できるなどの理由から、その動力源にはディーゼルエンジンが採用されている。ガソリンエンジンと比べると熱効率が高く燃料消費量が少ないためCO2の発生が少なく、またその燃焼特性から一酸化炭素(CO)や炭化水素(HC)の発生も非常に少ない一方、NOxやPMの発生が避けられず、ディーゼルエンジン単体でも電子制御・高圧噴射システム(コモンレールシステム)の搭載などにより、これら物質のさらなる抑制が実現しているが、ハイブリッド化によりエミッション低減でのブレークスルーを目指す構え。
?提供:コマツ コマツが2008年6月に建設機械として世界で初めて発売したハイブリッド油圧ショベル「PC200?8 ハイブリッド」を例にとると、新開発の旋回電気モーター、発電機モーター、キャパシター(蓄電器)と、ディーゼルエンジンを併用した「コマツ・ハイブリッド・システム」により、通常型「PC200?8」と比較して約25%の燃費低減を実現している。同ハイブリッド・システムは、車体旋回の減速時に発生するエネルギーを電気エネルギーに変換、キャパシターと呼ばれる蓄電器に蓄え、発電機モーターを通じエンジン加速時の補助エネルギーとして活用する。
建設機械の車体旋回動作には通常油圧モーターを使用するが、ハイブリッド式では旋回電気モーターにより旋回減速時に発生するエネルギーを回収する。ハイブリッド式では、回生エネルギーをエンジン加速の電動アシストとして活用するため、エンジンは燃費効率の良い低速回転域で使用できるほか、作業の待機時(デセル時)も超低速回転に抑えることができ、大幅な燃費低減を実現する。
ハイブリッド自動車と比較すると、自動車では発進加速の際に大容量の電気エネルギーを必要とし、その後比較的安定したエンジン回転で使われるのに対し、建設機械の場合は掘削作業などで短時間のうちに頻繁なエンジン回転が変動する。この頻繁なエンジン回転に追随してアシストするため、キャパシターを搭載している。自動車に使われるバッテリーは化学反応を伴い、放充電に時間を要するため、十分なアシストが得られないが、キャパシターであれば効率よく回収・蓄電し、また瞬時に放電することが可能となる。
建機他社でもコベルコ建機が、バッテリー方式を採用した7tクラスのハイブリッド油圧ショベル「SK70ハイブリッド」を本年6月に市場投入する。ディーゼルエンジンの余剰エネルギーをバッテリーに蓄積しておき、高い負荷が掛かった際にエネルギーをエンジンに供給する機能を搭載、燃料消費の平均50%低減とエンジンの小型化を実現するという。
住友建機もこの6月、油圧ショベルのマグネット仕様では世界初となるハイブリッド機「LEGEST HYBRID」を発売する。マグネット仕様機は、主にスクラップ作業に用いられ、機械の稼動時間が長いことからエネルギーを回収する機械本体の旋回頻度が高く、ハイブリッド化に適する。同マグネット仕様機は発電電動機、インバータ・コンバータ、旋回電動機・旋回減速機を住友重機械グループで開発、現行のマグネット仕様機に比べ20%の燃費向上を達成している。
米キャタピラー社でも電気駆動式のブルドーザーやダンプを2009年中に市場投入予定。電気駆動式ブルドーザーの詳細としては、27tクラスを最初に発売、ディーゼルエンジンと発電機、モーターの併用で、従来の機械式ブルドーザーより燃費を20%低減。摩耗のあるトランスミッション(変速機)を用いないことからメンテナンス費用の低減が期待されるとしている。またハイブリッド式油圧ショベルは、キャタピラージャパンの兵庫県・明石事業所を中心に開発中で、2011年に発売する予定。
日立建機は油圧ショベルのうち最も需要が多い中型機種(重量20t級)でハイブリッド型を国内販売する。油圧ショベルが旋回してブレーキをかけたり、アームを降ろしたりする際のエネルギーを電気に変換して蓄積、これを駆動エネルギーとして再利用する。年間800時間稼働させた場合、燃料代が約44万円分削減できるという。
これらハイブリッド建設機械は、環境対応の次世代建機であるとともに、現在の不況下でランニングコストを大幅に低減する経済的なシステムとして期待される。
第37回 INTERMOLD 2009が開催、金型加工技術が一堂に!
第37回 INTERMOLD 2009が開催、金型加工技術が一堂に!
日本金型工業会は4月8日~11日、「INTERMOLD 2009(第20回金型加工技術展)/金型展2009」を東京・有明の東京ビッグサイトで開催した。同時開催は「金属プレス加工技術展2009」。288社・団体が出展、3D-CAD(部品・金型のモデリング)、CAM(金型加工用データ作成)、CAE(金型成型シミュレーション)から、放電加工機やマシニングセンタ(MC)など金型加工用工作機械、エンドミルなど切削工具、金型や工具向けの表面改質技術など、金型の設計・製造から樹脂・金属プレス金型成型による素材加工までの最新技術・製品を展示した。
デジタルカメラの非球面レンズや液晶ディスプレイ用導光板など高精度・微細で複雑形状が求められる成型加工では、金型加工には高速・高精度化とともに、生産性向上からは金型寿命を向上する耐久性が求められる。また携帯電話などサイクルの早い製品向けの金型では、短納期、低コストの製作が求められる。
開発期間の短縮やコスト低減では、サイバネットシステムが板厚分布、残留応力などの解析結果を車の衝突解析モデルにマッピングするといった発展的応用が可能な板成形解析ソフトウェア(CAE)「eta/DYNAFORM」を出展、成形初期段階で製品が持つ潜在的な不具合を検証するためのアプリケーションBSEと、金型設計のためのダイフェース、バインダー、余肉をパラメトリックに作成するアプリケーションDFEを持ち、CADにフィードバックなしでシミュレーションの結果(しわ、割れ、板厚減少など)のパラメータスタディーを可能にしている。
高精度で複雑な形状の加工では、グラファイトなどの電極材料からの放電で導電性のある金属を研削する放電加工に加えて、近年は高能率の除去能力を持つエンドミルを用いた、高速・高精度回転、高速・高送りの5軸制御マシニングセンタなどによる切削加工の適用が進んでいる。牧野フライス製作所では、5軸制御型縦型MCを出展、主軸回転は通常仕様で1万4,000 min‐1まで対応しているが、回転する主軸内部に温度制御した多量の冷却油を送り込み主軸自体を内側から冷却する軸芯冷却や、主軸内側に送り込んだ冷却油をベアリングのインナーレースに開けた穴から供給するアンダーレース潤滑を採用することで、主軸の熱変位を抑え3万min‐1まで対応している。傾斜軸・回転軸に超高トルクDDモータを採用、重量ワークの高精度な位置決めや1万8,000°/min(50min-1)の高送り・高加減速性を実現している。
提供:牧野フライス製作所
オーエスジーは近年増加傾向にある微細電極用グラファイトの加工に最適な超硬エンドミル「DGエンドミルシリーズ」を出展、独自のダイヤモンドコーティングで抵抗を下げるとともに丸みの少ないシャープな切れ刃を実現、ボールエンドミルではR部と外周部のつなぎをなくしたシームレス形状により仕上げ面の段差を防ぎ加工面向上を実現する技術を紹介した。
表面改質技術では神戸製鋼所が、UBMS(アンバランスド・マグネトロン・スパッタリング)装置により高硬度、低摩擦係数DLC膜の高密着コーティング技術、真空中のアーク放電を利用したイオンプレーティングプロセス(AIP)により緻密で高硬度、高い機密性、多元系合金組成も可能な硬質皮膜コーティング技術と、それら手法により一般機械部品から樹脂成型金型、打ち抜き金型、切削工具、自動車部品などに対応する各種「BELCOATコーティング」を紹介した。
新興国を中心に安価な中国製金型の供給が進む一方で、高精度、高品質加工向けの金型では日本製の金型は依然世界の市場での評価が高く採用され続けている。そこでは、金型設計・開発の工期を短縮するCAD・CAM・CAE、高速・高精度回転と高速・高送りで高能率加工を実現する工作機械、加工の高能率・高精度を実行する加工工具、加工工具と金型の耐久性を高めるコーティング技術など、多くの差別化を図る機械関連技術が活躍している。
第38回 モーション・エンジニアリング展開催、機械の性能向上と長寿命化を支える機械要素
第38回 モーション・エンジニアリング展開催、機械の性能向上と長寿命化を支える機械要素 日本能率協会( http://www.jma.or.jp )は4月15~17日、千葉・幕張の日本コンベンションセンター(幕張メッセ)で駆動・伝達・制御に関する専門技術展「第18回モーション・エンジニアリング展」を開催した。今回は78社・学校/193小間の規模で出展、来場者数は1万1,509名だった。
メカトロニクス・エレクトロニクスの要素技術・関連製品の総合展示「TECHNO-FRONTIER 2009」の一つとして開催される同展では、転がり・すべり軸受や直動転がり案内、すべり案内、ベルト、チェーン、変速機、クラッチ、ブレーキ、シールなどの最新技術・製品が多数展示された。特に技術に着目すると、産業のニーズがうかがい知ることができる。
ベアリング関連の技術を見てみよう。たとえば今回ジェイテクトがdmn値100万に対応できる高速モータ用玉軸受のための樹脂保持器を出展した。転がり軸受のボールを保持する保持器には、金属よりも自己潤滑性が高い樹脂(エンジニアリングプラスチックス)が使われている。しかし樹脂性保持器では、高速回転中の発熱により剛性が低下するとともに、遠心力が加わることでクリープによる変形寸法が大きいという課題があった。
これに対し同社では、ポリアミドイミドとポリフェニレンスルフィドのアロイ材に強化繊維として炭素繊維を適用することで200℃の高温・高速回転下で使用できる材料を開発、さらに変形の解析結果をもとに、開口側爪内径側に傾斜させることでボールとポケット面の接触による偏摩耗を抑制するとともに、PCDとポケット(ボールの保持部)径の最適化で保持器と内輪・外輪の接触を抑制している。この形状から、グリースの飛散を防止し潤滑性も向上する。ハードディスクドライブなどのファンモータなどでは、そうした高温・高速下での信頼性向上に加えて、樹脂本来の長所である長期的な騒音低減にも役立つという。
また、NTNは昨年グループ企業となった仏SNR社との共同開発となる内径8?の「小型回転センサ付軸受」を展示していた。回転角度最大0.47° (軸受型番608の場合:760パルス/回転)の回転検出が可能で、事務機器の小型・軽量化や高精細化、回転制御機器の省エネルギー化などに貢献するもの。
小型センサの技術は、機械・装置の省スペース化と稼動の信頼性を実現する。併せて出展していた「磁気式鉄粉センサ」はベアリング製品とは独立した技術である。現状、自動車トランスミッション付近のオイル中の摩耗粉を監視する用途で提案中という。つまりトランスミッションの異常摩耗などを見るわけだ。間接的にはオイルの劣化が進めばベアリングにも悪影響を及ぼすため、機械の血液であるオイル管理の省スペースのシステムといえよう。
産業の米と言われるベアリングを支える材料・設計技術、センサなどの周辺技術。機械・システムにおいて高速・高温・高圧など使用条件が過酷化する一方で、環境面・コスト面などからメンテナンスフリーのニーズは高い。そこでの信頼性を向上するのがベアリングなどの機械要素であり、それらを支える基礎技術の開発からも目が離せない。
第39回 自動車販売を牽引するハイブリッド車戦争
第39回 自動車販売を牽引するハイブリッド車戦争提供:トヨタ自動車
提供:Honda 本年2月に発売開始したHonda「インサイト」が発売から1ヵ月半で2万台を超え、5月に発売する第3世代「プリウス」は09年生産計画を49万5,000台(トヨタ車販売台数の5台に1台の計算)とするなど、ハイブリッド(HV)車の競争が激化している。
HV車は、発進や加速などエンジンの効率が悪くなる場面(ガソリンの消費量が高い)でモーターがエンジンをサポートする仕組み。通常走行時はコンピューター制御でエンジンとモーターの動力分布を最適配分、加速時にはバッテリーからモーターに電力を供給し、減速時は回生エネルギーとしてバッテリーに電力を蓄える。加速時に電力でエネルギーアシストすることにより、ガソリン消費量が節約できるというもの。
Honda「インサイト」は1,300ccで、現行のトヨタ「プリウス」よりも44万円安い189万円という低価格と、1Lで30kmという省燃費が売り。しかしインサイトでは、プリウスのようなモーターだけの「EV走行」ができず、発進時からエンジンが回転する。エンジンを主役に、発進加速時など大きなパワーが必要なときは、モーターがアシストするのである。信号などでの停車時は、アイドリングが自動的に停止。ストップ&ゴーの多い街中でも軽快でクリーンに走れる。
Hondaハイブリッドシステム「IMA」によるエンジン負荷の大幅低減をはじめ、空力性能の追求、ボディ骨格のほとんどに強度の高い高張力鋼板を採用するといった軽量化の徹底などにより、JC08モード走行では26.0km/L、10・15モード走行では30.0km/Lの低燃費を実現。全タイプで「平成22年度燃費基準+25%」を達成している。
一方、5月に発売するトヨタの新型「プリウス」では、インサイトの軽量化とは対照的に、これまでのエンジン排気量1,500ccから1,800ccに大型化、一部車種では太陽光パネルなどの装備もあり45kg以上重い。加速力を高める一方で走行時の出力とトルクに余裕ができるため、高速走行時のエンジン回転数を抑制できる。
また、モーターにはトルクを高めるリダクションギヤを搭載、大きな出力を得つつも、モーター全体を小型・軽量化できる。発電機も軽くした。
こうした工夫で、燃費は現行プリウスに比べ1割程度向上した1Lあたり38kmの世界最高レベルを実現している。
HV車の開発が急速に進む中、現行のニッケル水素電池に比べ体積、重量を半分以下に抑えるリチウムイオン電池や、エンジンとモーターの駆動を適正化する電子制御技術、車体の軽量化を図る小型・高出力モーター、アシスト力を大きくしながら小型・軽量化した電動パワーステアリング(EPS)、燃費向上の鍵を握る回生ブレーキなど、自動車部品の技術開発も進められている。
過去にトヨタ「カローラ」と日産「サニー」の間で繰り広げられた販売競争が「CS戦争」と呼ばれたのにならい、今回のトヨタ「プリウス」とHonda「インサイト」の販売合戦は「PI戦争」などとも呼ばれているが、いずれにしても09年国内需要が2年連続で500万台割れが確実視され、北米も1,000万台以下に縮小される可能性が高まる中、この自動車部品も巻き込んでのHV戦争が市場活性化の起爆剤になることを期待したい。
第40回 EV普及による波及効果に期待
第40回 EV普及による波及効果に期待三菱自動車と富士重工業が7月にいよいよ電気自動車(EV)を発売する。三菱自は「i-MiEV」の初年度販売目標を2,000台、富士重は「プラグインステラ」で同170台と見込んでいる。京都市が充電スタンドを市内の公共施設や市営駐車場に38ヵ所設置、東京都と神奈川県で1台あたりそれぞれ30万?40万円、70万円を購入助成するなど普及を後押しする動きも活発化してきている。
さてEVはモーターを動力源とし、バッテリーからの電力のみで駆動する。「i-MiEV」でみると、軽自動車「i(アイ)」をベースに、高性能リチウムイオン電池と小型・軽量のモーターを搭載している。この永久磁石式同期モーターが、エンジンの代わりとなって動力を発生させる。モーターは0rpmから最大トルクを発生可能で、内燃機関のように変速機を持たなくてもすべての走行領域をカバーできる。最高出力47kW、最大トルク180N・m、最高回転数8500rpmのモーター1個と、総減速比6.066の固定減速機とディファレンシャルギヤを組み合わせ左右後輪を駆動するシングルモーター方式により、ベース車の駆動力をまかなっている。
このパワートレインでの動力性能は、発進加速、追い越し加速ともにベース車よりも良好な結果が得られている。アクセルを踏むと同時に変速機のキックダウンによるエンジン回転速度上昇もなくスムーズに力強く最高速度130km/hまで加速できる。静粛性も高く、50km/hからの全開速時の車外騒音をエンジン車と比較すると、5dBも低いという。
また停車中のアイドリング騒音もなく、特に発進時など静か過ぎて歩行者が気づかないという指摘もあり、走行が確認できる音作りが電気自動車特有の新たな課題といわれている。だが、通常ガソリン車ではエンジンの空気を吸入する力を利用しブレーキ踏込力を助けているのに対し、EVでは電動ポンプで吸い込む力(負圧)を作り それを負圧タンクにためてブレーキを利かせているというから、タイヤの摩擦音とこのエア圧縮音で確認できるのではないかとも思う。課題はやはり、エアコンやABSブレーキサーボ、パワーステアリングの電動を支えるバッテリーの消耗だろう。航続距離は1回7時間の充電で160kmと改善されてきているが、さらなる延長が求められる。
技術やコストの課題は残されているが、両社のEVとも、電力会社や郵便事業会社などが導入を決めており、各社の販売計画を上回る可能性も見込まれている。この新しい市場が創出されるにあたって、前述のとおり充電設備の整備も進んできている。たとえばEV住宅。トステム住宅研究所が発売した戸建て住宅では、大型の太陽光パネルを屋根に取り付け自家発電しつつ、EV充電用200Vコンセントを駐車場に標準装備した仕様となっている。国内最大級のショッピングセンター「イオンレイクタウン」でも巨大な太陽光発電パネルを持つエコモールの一角にEVの急速充電スタンドが設けられている。
また、法人向け車両リース・レンタカーを手がける高栄企業はエコカー専門レンタカー店のネットワークを広げてきているが、ここでは小型の風力発電装置を設置、事務所や各充電スタンドで使う電力をまかなっている。
EV元年。EVの普及が、こうした新エネルギー市場拡大の一翼を担うことに期待したい。
第041回~第050回
第041回~第050回第41回 機械保全の水際対策、監視・診断技術
第41回 機械保全の水際対策、監視・診断技術世界各地で猛威をふるい国内でも約50名の感染者が確認されている新型インフルエンザの水際対策として、NECでは本社ビル入口に「赤外線サーモグラフィシステム」を設置、新型インフルエンザ対策の実証実験を重ねてきたという発表があった。同システムは、新型インフルエンザ症状の特徴である38℃以上の高い発熱を、非接触・高速で温度計測し異常温度を検知した場合警報を発するもので、同社グループ企業のNEC Avio赤外線テクノロジーが手がけている。同システム25台が日本政府を通じてメキシコ政府に送られ、空港の検疫所などで使われる予定だ。
NEC本社に設置した赤外線サーモグラフィシステム、提供:NEC 赤外線サーモグラフィとは、対象物から出ている赤外線放射エネルギーを検出・可視化して、温度測定・温度計測・温度分布の画像表示を行う装置。
(1)面の温度分布として捉え、可視化情報として表示できる
(2)対象物から離れたところから非接触で温度測定ができ、動いているものや、危険で近づけないものでも、簡単に温度計測できる
(3)リアルタイムで温度計測ができる
といった特徴から、今回のような熱計測だけでなく、実は機械の非破壊検査、劣化診断、品質保証や保全管理などでも使われている。
機械用途としては、切削、研削、軸受、モーター、タイヤ、熱処理、配管、熱処理、ボイラーなど多岐にわたる。たとえば回転機械の診断では、軸受の異常な温度上昇を早期に発見、軸受の焼付きによる機械の突然停止を予防する。軸受の温度上昇などの故障因子から、軸受の取付けや潤滑などのデザインの見直しにもつながる。
1966年に英国で鉄鋼所の潤滑管理を見直すことでGNPの1%超の経費を削減できるというジョスト報告から、摩擦・摩耗・潤滑に科学的・技術的に取り組む「トライボロジー」という概念が生まれた。自動車エンジンでのトライボロジー技術の適用では低フリクション化による燃費改善が図られているが、機械の管理に適用することで故障・突然停止を予防できる。
赤外線サーモグラフィのほか、軸受診断では異常振動を検知する振動計や材料の亀裂の発生や進展などの破壊に伴って発生する弾性波を早期に検知するAE(アコースティックエミッション)などがあるが、機械の安定稼動、長寿命化を図り、ランニングコストを低減できるほか省エネ、省資源、地球環境保全にも貢献するこうした監視・診断技術が、機械保全の水際対策として活用されていくことに期待したい。
第42回 優れたメカによる省エネ家電の選定・購入を!
第42回 優れたメカによる省エネ家電の選定・購入を!
エコポイント対象商品のロゴ 5月15日から、省エネ家電の「エコポイントの活用によるグリーン家電普及促進事業」(エコポイント制度)が始まった。今回のエコポイント制度は、地球温暖化防止、経済の活性化、地上デジタル放送対応のテレビの普及を目的として、省エネ性能の高いエアコン、冷蔵庫、テレビの購入者が購入額の一部をポイント数として受け取り、次の買い物のときにポイント分を値引きしてもらえる仕組み。
家庭部門のCO2排出量のうち、約7割弱が電化製品によるものとなっており、約5割がエアコン、冷蔵庫、テレビで占められている。また、エネルギー効率の低い旧型品を省エネ型製品に買い換えることで、適正にリサイクルがなされれば、より高い環境保全効果が期待できる。こうした観点から、優れた省エネ性能を客観的に判別でき、かつ、家電リサイクル法において買い替えの際にリサイクルすることが定められた電化製品を対象とすることが適当であり、省エネ性能を5つの星で表した「省エネ統一ラベル」で4つ星相当以上のエアコン、冷蔵庫、テレビをエコポイントの対象とすることとしたもの(省エネルギーセンターの省エネ製品情報( http://www.eccj.or.jp/labeling_program/ )を参照)。エアコンは出力数、冷蔵庫は容量、テレビは画面のサイズによってポイント数が異なり、最大(46V以上)で3万6,000円分のポイントが付与される。ポイント交換は8月からになる見通し。
家庭内消費エネルギーの約25%とトップを占めるエアコンの省エネ技術を見てみよう。
たとえばルームエアコンで省エネ大賞通算8回目の受賞となった東芝の「大清快」PDRシリーズは、省エネ性能向上のため、全損失の約60%を占める部品間のしゅう動損失と漏れ損失の低減に取り組んだ。
ロータリーコンプレッサーの圧縮機構部はベーンによって仕切られたシリンダー内をローラーが回転することで吸い込みと圧縮を繰り返しており、部品間のしゅう動部で損失が発生している。そこでこの損失改善と漏れ損失改善のため、薄型シリンダーを採用するとともに、上下のシリンダーで独立に2本あった吸い込み管を1本化し、内部の仕切り板で分岐させるという方式「1サクション方式ツインロータリーコンプレッサー」を採用した。この方式により吸い込み抵抗を増大させずにシリンダーの薄型化に成功、2007年度搭載コンプレッサーに対し約2.8%の効率改善を達成した。
これらの改良で、冷房と暖房をそれぞれ3.6ヵ月、5.5ヵ月使用したと仮定して算出される期間消費電力量は、10年前の「大清快」から約34%低減された。通年エネルギー効率(APF。1年間、1kW当たりの冷房・暖房能力)は6.2ポイントとなり、同社ではこれを業界トップの数値としている。削減された電力量をCO2排出量に換算すると、1台で杉16本が吸収する量に相当するという。
省エネ化により地球環境保全に貢献するエコ家電。優れたメカにより消費電力低減、CO2排出抑制にも貢献する本物のエコ家電を見極めつつ、地球環境保全と消費拡大に貢献していきたいものである。
第43回 ガンの早期発見・低侵襲医療を図る内視鏡技術
第43回 ガンの早期発見・低侵襲医療を図る内視鏡技術提供:富士フイルム 富士フイルムが鼻から挿入する高画質・広角タイプの経鼻内視鏡を開発した。口から挿入する従来の経口内視鏡検査に比べて、経鼻内視鏡は嘔吐感が少なく、会話もできることから、医師からも患者からも「コミュニケーションをとりながら、安心感のある胃の検査ができる」、「麻酔が最小限に抑えられ日常生活に早く復帰することができる」などと好感され、採用が進んでいる。今回の開発ではさらに、140°という広い視野角で観察範囲を拡大したほか、モニター画面の表示画像も約1.5倍とし、胃ガンの早期発見に貢献するとしている。
提供:オリンパス 内視鏡のシステムは、ビデオスコープとビデオシステム本体(カラーモニター、ビデオプロセッサー、光源装置)の二つに大別される。ビデオスコープは、操作部、挿入部、先端部、接続部(コネクター部)からなり、接続部(コネクター部)がビデオシステム本体につながり、伝達される画像はモニターで観察、このモニターには最先端技術のCCDと極細スコープで高精度画像が送られる。
操作部には、内視鏡の湾曲を上下左右に制御するアングルノブ、送気送水ボタン、吸引ボタンや処置具を挿入する鉗子口がついている。管の中でワイヤーが二硫化モリブデンなどの固体潤滑剤により滑らかに動くことで、不快感の少ない観察や処置が可能になる。
内視鏡の先端部には、臓器内部の粘液や血液で先端レンズが汚れたときに水や空気を噴出して洗い流すノズルや、対物レンズを通じて画像をとらえるための超小型高性能カメラ(CCD)などが埋め込まれている。
一般に経口内視鏡は管の外径が約9?で、内視鏡が舌のつけ根を通り、のどに触れることから、挿入による不快や吐き気を覚えることが多い。これに対し、開発された経鼻内視鏡の先端部の外径は約5.9?と鉛筆よりも細いため、嘔吐感の少ない負担の少ない手法として、「93%の患者が次回も鼻からの内視鏡検査を希望する」というアンケート調査結果も報告されるほど、採用が進んでいるという。
提供:オリンパス また、オリンパスではマイクロマシンの技術を応用、コップ一杯くらいの水で飲み込むだけで小腸の状態をリアルタイム観察できるカプセル内視鏡を開発している。カプセルは消化管の蠕動(ぜんどう)運動によって、飲んでから1?2時間くらいで胃から小腸に達する。カプセルは動作している間、毎秒2コマの割合で撮影を続け、画像を送信、画像データは体につけたアンテナを通じて受信装置に記録され、検査終了後にドクターがそれを見て診断を行う。錠剤大のカプセルのため、違和感も少ないという。
体内の汚れが付着しないよう、カプセルの表面ができるだけ滑らかな状態を保つよう厳しい管理で作りこむ。薬剤の安全性を確認する必要がないよう、表面に特殊な薬剤を塗ることはしていない。腸内を進んでいくにつれて、汚れが自然と後ろに掻き出されていくようなカプセル先端の形状が工夫されている。
ガンは早期に発見・治療をすることで、治る可能性も高くなる。従来の経口内視鏡などでみられた不快感を軽減し、負担の少ないこうした内視鏡の技術が登場することにより、気楽に、より早く検査を受ける患者が増えてくる後押しとなることだろう。ガンの早期発見につながる低侵襲の医療技術の進展に期待したい。
第44回 事故の原因究明でクレーンの安全性向上を!
第44回 事故の原因究明でクレーンの安全性向上を!6月3日東京都板橋区のマンション建設現場で、タワークレーンの台座が落下し、作業員2名が死傷するという事故が発生、台座を支柱に固定していた2本のカンヌキが支柱から外れたために落下したと見られている。作業者2名とも作業台にいて、長さ35mのアームを回転させる旋回台と作業台の間に挟まれていた。台座は旋回台や作業台からなり、事故当時は工事を終えたクレーンを解体するため、高さ24mの支柱の最上部にあった台座を下げる作業を始めたところだった。
タワークレーンのクライミング装置は、上部カンヌキを有するクレーンの旋回台、下部カンヌキを有する作業台、昇降シリンダーで構成され、上下のカンヌキでクレーン本体の全質量を交互に支えている。これらの台座は通常、支柱に等間隔に開いた穴に差し込まれた上下2本の鉄製のカンヌキで支柱に固定されている。台座を下げるには、下部の作業台のカンヌキを抜き、昇降の油圧シリンダーを伸ばした状態で、元の位置より下方の穴にカンヌキを差し込む。次いで、上部の旋回台のカンヌキを抜いて油圧シリンダーを縮め、下方の穴にカンヌキを移す、という尺取虫のような動きを繰り返す。カンヌキの大きさは直径約10cm、長さ約20cmで、一方のカンヌキを抜くともう一方に台座の重さ約13tの荷重がかかるため、各台に取り付けられたカンヌキの抜き差しも油圧シリンダーにより行われる。このカンヌキの抜き差しと昇降の油圧シリンダーの伸縮は作業台にいる作業者の操作で行われる。
昇降の油圧シリンダーの機能により、カンヌキが一方でも差し込まれていれば台座が落下することはないという。通常カンヌキの抜き差しを行う油圧シリンダーには、穴とカンヌキの位置を検知するセンサーが装着され、事故が起きた機種でも、カンヌキが2本とも抜けるのを防ぐ安全装置もあった。ところが、何らかの原因で2本ともカンヌキが抜け、台座は落下した。
カンヌキ脱着の油圧シリンダーやセンサーの不具合か、カンヌキの金属疲労などによる破壊か。タワークレーンの落下による災害は、10年前にも発生している。やはりカンヌキが2本とも抜けたことによるものだ。こうした事故が二度と起こることのないよう、機械・材料面から、作業のマニュアル面から、事故解明に向けた徹底的な調査、検証を行い、人命を守る、安全性を向上するシステムの構築に努めたい。
第45回 省エネ・高効率生産のための設備保全の促進を!
第45回 省エネ・高効率生産のための設備保全の促進を!稼動率が低下している生産工場で、省エネ化を図る設備保全への取り組みが増えてきている。設備保全の取り組みは省エネだけでなく、設備の突然停止につながる設備要素の異常を事前に予防し、経済的損失も抑えるという「予防保全」からも意義は大きい。
予防保全と省エネの観点では、機械の運動を実行する機械要素のロスや摩耗を抑えエネルギーロスなく円滑に作動させる、潤滑油の管理も欠かせないだろう。
たとえば新日本製鐵での潤滑管理活動を見ると、大きく油漏れ管理と潤滑系診断を実施している。
油漏れ管理としては、シリンダーのパッキンや配管のホース、ポンプのオイルシールなどが対象となる、各種の疲労寿命試験をクリアしたパッキン、ホース、オイルシールを適用することで単品ではコストアップになっても、機器のロングライフ化とトータルコストダウンにもつながる。
また、使用油をサンプリングして行う潤滑系診断としては金属摩耗粉を分析するフェログラフィー法、摩耗粉など油中のコンタミの粒径や個数を計測するパーティクルカウントなど汚染分析法などがある。いずれも潤滑油の劣化を早期にとらえ機器の異常を未然に防ぐ技術である。
故障が発生した後の事後保全に対して、予防保全として潤滑管理を実施することを「メンテナンス・トライボロジー」ともいう。「トライボロジー」については先に述べたが、1966年に英国で国策として生まれた摩擦・摩耗・潤滑の科学技術の総称。英国内の鉄鋼所の適切な潤滑管理を実施することで、当時の英国のGNPの1%以上(当時の金額で年間5,000億円)を節減できるという調査報告から、各国でトライボロジーの視点から設備管理、製品・技術の研究・開発が行われてきている。
提供:新日本製鐵 総合潤滑管理システムを事業とする日本システムサービス(本社・札幌市)の磯谷喜冶社長は、「2008年現在でわが国の給与水準(高卒者の平均給与)は、トライボロジーの調査報告がなされた1966年当時の約15倍程度で、一方、現在の我国に於ける工業規模および潤滑油の総消費量は英国本国の約2.5倍。先の潤滑管理による節減費用5,000億円を現在のわが国に当てはめると、年間で5,000億円×15×2.5=18兆7,500億円にも達することになる」と語り、トライボロジー運動の再燃を呼びかける。
自動車をはじめ少しずつ生産が拡大してきている今こそ、本格的な立ち上げに向けて、省エネと生産の効率化、経費節減に貢献する設備管理システムの導入・促進を望む。
第46回 鉱山開発の需要拡大で、求められる機械要素技術
第46回 鉱山開発の需要拡大で、求められる機械要素技術低迷が続いていた鉱山機械用の超大型タイヤ需要が、中国やロシアなどの資源国で需要回復傾向にある。鉱山開発が勢いを取り戻し始めている。ブリヂストンでは北九州に建設した幅1m以上、直径3m以上といった建設・鉱山車両用大型・超大型ラジアルタイヤ用の新工場を当初予定の9月から3ヵ月前倒しし、6月17日から稼働させた。同社では「世界的な鉱物資源の生産増加に伴い、ここ数年大型・超大型ORRの需給バランスは大きく乖離している。中長期的に見ても需要は伸長する見込みで、また、昨今の厳しい事業環境下においてもこの分野は堅調に推移している」と生産前倒しについて説明している。
さて、鉱山機械としてはまず鉄鉱石、石炭を含んだ地層を掘り起こす、油圧ショベル、それらを集積場に運搬する大型のダンプトラックがある。油圧ショベルでは駆動用油圧減速機や旋回装置などにベアリングが使われている。大型ダンプトラックにはトランスミッションや車軸などに多数ベアリングが使われている。
採掘された鉄鉱石などは粉砕機によりある程度の大きさに粉砕される。たとえば大きな筒の中で鉄球を鉱物にぶつけて砕くボールミルでは、筒の両端の支持用に内径500?を超える自動調心ころ軸受や円筒ころ軸受が使われる。高荷重、衝撃荷重、粉塵に耐える必要性からだ。
砕かれた鉄鉱石などは長いもので20kmにも及ぶコンベヤで、大きさを揃える篩い分け工程に輸送される。コンベヤベルトを支えるコンベヤローラは深溝玉軸受が多数使われるほか、コンベヤ駆動用のモータや減速機が接続されたドライブローラには大型の自動調心ころ軸受が使われる。
提供:日本精工 日本精工では自動車用ハブユニットで実績のあるシールユニット構造をコンベヤローラ軸受に適用、高密封シールと軸受を一体化することによって、雨、泥水、粉塵などの異物が侵入しやすい環境下で低トルクと密封性を両立させた、信頼性の高いコンべヤローラ軸受を開発している。高密封シールにより、野外で使われるだけに、機械への異物侵入を防ぐだけでなく、環境へのグリースの流出を防いでいるのである。
地球資源を有効に活用するための資源開発。だからといってその作業のための機械のロスや環境負荷は見逃されるものではなく、鉱山機械においても省エネ・省資源が求められている。鉱山開発の市場拡大とともに、耐久性があり、環境負荷低減を図るベアリングや歯車、タイヤ、ベルトなどの機械要素技術が活躍する場が増えつつある。
第47回 CO2削減の切り札ヒートポンプの市場拡大を!
第47回 CO2削減の切り札ヒートポンプの市場拡大を! 空気中などに無尽蔵に存在する熱を汲み上げて利用するヒートポンプは、燃焼を伴わないシステムのため二酸化炭素(CO2)を排出しないことから、またその熱効率の高さから注目されている。ヒートポンプを使った給湯システム「エコキュート」は年間50万台の市場に拡大、政府は2010年までに520万台普及という目標を立てる。
燃焼方式の暖房器具では、消費した電力1に対し得られる熱エネルギーが1なのに対し、ヒートポンプを使った冷暖房や給湯システムでは、必要な熱エネルギーを1とすると、その5/6を空気から取り出した熱エネルギーで賄える。つまり、消費電力が必要な熱エネルギーの6分の1で済む。このエネルギー消費量の少なさが、ヒートポンプの最大の特徴であり、またヒートポンプが日本中の空調・給湯・加温機器に普及した場合、日本全体で1年間に排出するCO2の約10%を削減できるとの試算があり、ヒートポンプシステムは地球温暖化対策の切り札とも言われている。
ヒートポンプは、熱交換器に大気中の熱を取り込み、冷媒のCO2を膨張させて大気中の熱を吸収、その熱をコンプレッサーで圧縮してさらに高温にし、高温になった熱をタンクユニットの水に伝えてお湯にするもの。CO2は地球温暖化係数が1/1000以下と低い自然冷媒だが、高圧側で10MPa以上と動作圧力が高く、またHCFCやHFCなどのフロン冷媒とは異なり、摺動面に塩化物やフッ化物などの冷媒による固体潤滑膜を形成しないため、圧縮機内部の摺動部では摩耗量の増加が懸念される。三菱電機が2005年から市場に投入しているCO2冷媒適用の高圧シェルタイプシングルロータリー圧縮機では、負荷される荷重が大きく接触応力が高くなるベーン先端とローリングピストン外周部の摩耗量増加をする抑制するため、ベーンに対し優れた摺動特性を持つDLC?Si(シリコンを含有させたダイヤモンドライクカーボン)を適用している。
麻生太郎首相は先ごろ、2020年までに最終エネルギー消費に占めるヒートポンプなど再生可能エネルギーの比率を今より倍増し、世界最高水準の20%まで引き上げたいと明言した。経済産業省総合資源エネルギー調査会第33回新エネルギー部会の試算では、2020年にヒートポンプ利用によって得られるエネルギー導入量が原油換算で2,361万kLとしている一方、同試算のベースとなった「長期エネルギー需給見通し」では、2020年の日本の最終消費エネルギー量は、原油換算で3億9,000万kLと見積もっている。つまり2020年の再生可能エネルギー導入量に対し、その約3割を担うことがヒートポンプに期待されている。ヒートポンプや太陽光発電など太陽起源の再生可能エネルギー利用技術は日本の得意とする技術。これらの普及により、CO2排出量削減とともにわが国の経済発展に寄与することを期待したい。
第48回 カテーテル治療拡大に向け、安全性の高い技術を
第48回 カテーテル治療拡大に向け、安全性の高い技術を 米医療機器大手のボストン・サイエンティフィック社が2014年までに次世代ステント製品を投入するなど日本での心疾患治療用機器の事業を拡大すると発表した。国内でのカテーテル治療の拡大に向け、国内外のメーカーの開発競争が始まっている。
心臓カテーテルは、心臓の検査や治療に用い、からだの動脈や静脈を通して心臓の中や心臓の周囲の血管までカテーテルを挿入、それによって血管内の圧力を計測したり、カテーテルを通して薬剤・造影剤などを投与するもの。狭心症や心筋梗塞の場合、冠動脈にカテーテルを挿入し、造影剤を注入することで血管の狭窄や閉塞を発見することができ、必要に応じてその狭窄や閉塞を治療できる。
カテーテルが挿入しやすいよう、また内部のガイドワイヤーとの摩擦を減らして動かしやすいよう、欧米では潤滑性の高い生体適合性のポリマー材料が被覆されている。
さて、先端には小さな風船がついていて、冠動脈が狭窄したり閉塞したりしている部分でその風船を膨らますことで良好な血流を回復させるバルーンカテーテルを使って狭窄などを解除すると共に、ステントと呼ばれる金属でできた筒状のものを冠動脈内に留置する「ステント留置術」もある。日本ではステント留置術が現在主流である。
この埋め込み型ステントは、耐食性の高いステンレスやコバルト-クロム(Co-Cr)などの金属材料を網状の筒に加工した器具で、カテーテルを介して患部に挿入され、梗塞部で拡張することで物理的に血管を広げ、拡張後は欠陥内部に留置されるため、高い生体親和性と、絶え間なく拍動する血流による物理的負荷に耐えうる機械特性が求められ、ステント材料表面にそれら特性を付与するコーティングを処理している。
この表面処理層はステントの大きな変形に追従して表面から剥離しないことが重要で、たとえばトーヨーエイテックではCo-Cr系ステントへのDLCを提案し,その耐剥離性を向上させるためにSi濃度を傾斜させる方法を開発したほか、冠動脈薬剤ステントへの適用としてCo-Crステント表面にDLCを成膜し、プラズマ処理による官能基の修飾後、薬剤を含む生体適合性ポリマーを被覆したものを開発した。生体内で薬物が放出された後,ポリマーは体内に拡散し,残ったDLCは高い生体適合性をもって残存する。こうしたステントへのDLC被覆を先に欧州で事業展開を開始しているという。
国内でカテーテル治療、ステント留置術が普及してきており、日本ステントテクノロジーなどがDLCコーティングを施したステントを上市しているものの、埋め込み型ステントの多くは輸入品が大半。国産の良好な製品・技術が開発されることで、患者の安全・安心の確保とともに、新しいビジネスと市場が形成されていくことに期待したい。
第49回 火災事故抑制に集客施設のスプリンクラー設置を望む
第49回 火災事故抑制に集客施設のスプリンクラー設置を望む提供:ミナカミ 7月5日大阪市此花区の雑居ビル1階にあるパチンコ店入り口付近から出火、店内にいた95人の客や従業員のうち、客3人と従業員1人が死亡し、客らビルにいた19人が重軽傷を負った。犯人は危険物取扱者の資格を持ち、揮発性が高く、火を近づけただけで一気に燃え広がる性質のガソリンをばら撒き、火をつけた。安全管理の知識を犯罪に逆用する行為に怒りを覚える。
大阪市消防局によると、市消防局から消防車など51台とヘリコプター1機が出動、出火から約20分で火はほぼ消し止められたが、パチンコ店の1階部分443m2がほぼ全焼した。今年3月に市消防局が店の立ち入り検査を実施した際には消火器や火災報知機など、消防法令で定められた設備は設けられていたが、スプリンクラーは設置されていなかった。この6階建て雑居ビルは延べ床面積が2,384m2で、消防法令が設置を義務付ける床面積3,000m2に達していなかったためだという。
提供:ミナカミ スプリンクラーは、屋内の火災により生ずる熱または炎を感知し、天井などに設置されたスプリンクラーヘッドから自動的に放水して、初期消火を行う設備。閉鎖型と開放型があり、劇場、講堂など天井が高く、ヘッドの取り付け位置が8m以上ある場所では開放型スプリンクラー設備が用いられるが、一般的なビルの場合には閉鎖型スプリンクラー、中でも湿式タイプが用いられる。湿式閉鎖型スプリンクラーは配管内に水が充満している方式で、スプリンクラーヘッドの感熱部の可溶片が、熱のために溶けてシール部分が開き、湿式流水検知装置が作動して放水する仕組み。
安全工学の専門家によれば、同店にスプリンクラーが設置されていたら火の急激な広がりを抑制でき、消防が着くまでに全焼することはなかっただろうとしている。機械では一時はコストアップになっても軸受管理や潤滑管理のシステムを導入することで、生産性向上やメンテナンス費用削減でトータルコストダウンを図り、また稼動の信頼性向上を図っている。同様に遊技施設においてもスプリンクラー設置には導入コストがかかっても、安全性のシステムを構築されることで客が安心して時間を過ごせ、ひいては店に対する信頼性を高めビジネスの安定・向上につながるものと考えられないだろうか。
法の制約がないとはいえ、今回出火したパチンコ店のように多くの人が集まる場所では、スプリンクラーのように火災事故が起こった場合の被害を最小限にする、安全性向上のシステムを徹底させることを強く望む。
第50回 住空間で活躍し始めた清掃ロボット
第50回 住空間で活躍し始めた清掃ロボットkat 2009年7月21日(火曜日)第051回~第060回
第051回~第060回第52回 患者の安全性と医療従事者の作業軽減を図るシリンジポンプ技術
第52回 患者の安全性と医療従事者の作業軽減を図るシリンジポンプ技術提供:テルモ テルモが、装置に注射器(シリンジ)を正しく装着できるよう、液晶表示部にシリンジ装着手順がイラストで表示され、確実な装着をサポートするシリンジポンプ「テルフュージョンシリンジポンプ35型」を発売した。シリンジポンプは、シリンジに充填された薬剤を一定流量で持続的に投与する装置で、手術中や術後の患者への薬剤投与量を精密に管理する時に使用されるが、 シリンジがポンプに正しく装着されていない状態で、ポンプが患者より高い位置に設置されている場合、薬剤が急速に注入されてしまう「サイフォニング」現象が起きる可能性が高いことが問題となっていた。新製品ではシリンジの装着が誤っている時にエラー音で知らせるだけなく、シリンジをワンタッチ着脱でき、正しく装着されるとOKサインで確認できる。テルモでは新製品がサイフォニングによる医療事故の防止につなげることができるとして、医療機関に採用を促していく構えだ。
シリンジポンプはモーター回転によりボールねじが回転し、それにより直線運動案内を行うスライダーがシリンジのプランジャ(押し子)を押すことで、薬剤を送り出す仕組み。送り検出センサーなども手伝って、流量0.1mL/h ステップ(0.1 ~ 100.0mL/h 時)、流量精度±3%以内(1.0mL/h 以上の流量で注入開始して1 時間以降の1 時間ごとの精度)を実現するボールねじ、スライダーの機械的レスポンス、精度が求められる。たとえば日本精工では、医薬品などの製造や研究開発の機器、システムを集めた展示会「インターフェックス」で、ボールねじとリニアガイドをユニット化した「モノキャリア」と高精度モーターの組合せで微量の液体を脈動なく一定量送るシリンジポンプを参考出品したが、これは使用者でのボールねじとスライダーの組み付け作業を軽減、シリンジポンプの薬剤投与の高精度化を狙うものであろう。
シリンジの思わぬ装着ミスによりサイフォニングという医療事故が起こる可能性がある。今回の新製品のような、患者の安全性をより向上し、医療従事者の作業上の、精神面の負担を軽減する技術開発に引き続き期待したい。
第53回 日本実験棟「きぼう」が完成、若田飛行士が帰還
第53回 日本実験棟「きぼう」が完成、若田飛行士が帰還国際宇宙ステーション(ISS)に船外実験プラットフォームと船外パレットを取り付け日本実験棟「きぼう」を完成させた若田光一宇宙飛行士が、4ヵ月半ぶりにスペースシャトル「エンデバー」で元気に帰還した。
きぼう(提供:JAXA) 日本の有人実験施設「きぼう」は、船内実験室と船外実験プラットフォームの二つの実験スペースからなるが、今回若田さんのロボットアームの操作により取り付けられた船外実験プラットフォームは、船外環境、つまり微小重力、高真空などの宇宙曝露環境を利用して、科学観測、地球観測、通信、理工学実験、材料実験などを実施できる多目的実験スペース。
ロボットアームの機構や操作については第34回で触れたので詳細は省くが、「親アーム」とその先端に取り付けられる「子アーム」からなるロボットアームのうち、今回は重量4,100kgの船外実験プラットフォームという大型機器のため親アームが使われた。若田さんはまず貨物室に搭載されている船外実験プラットフォームをISS側のロボットアーム(SSRMS)で把持して取り出した。そのままの姿勢で直接取り付けられる位置にないため、いったんスペースシャトル側のロボットアーム(SRMS)に受け渡した後、SSRMSの位置を移動し、再度SSRMSで船外実験プラットフォームを受け取り、「きぼう」船内実験室のEFBMに結合させた。船外実験プラットフォームの。親アームの先端速度仕様は対象物7,000kg以下で20㎜/sとなっているが、10㎜/s程度の作動で5時間半がかりで行った。
ARED(提供:JAXA) さて、今回注目したいメカは、無重力空間で長期滞在した後に起こる筋力の低下を食い止めたという改良型エクササイズ装置(Advanced Resistive Exercise Device、ARED)。AREDは、スクワットやウェイトリフティングなどの動きで筋力トレーニングを行うための装置。鉄アレイのトレーニングだと持ち上げてしまうと負荷が減るが、AREDは常に負荷がかかっている。ISSに滞在するクルーの1日のスケジュールには、筋力の低下を防止するためAREDを使用したエクササイズが組み込まれており、若田さんはさらに骨粗しょう症の薬も1週間に1回の割合で飲んでいたことから、筋力低下と骨量減少を防止したと見られている。長期滞在に伴うクルーの健康面でも成果をあげたといえよう。
ISSの運用は2015年に終了する予定。「きぼう」を利用して実験を行う残り5年程度で、宇宙空間という真空環境を利用した、いかに多くの研究成果が出せるか今後に期待したい。
第54回 省エネ「打ち水技術」で環境にやさしいヒートアイランド対策を
第54回 省エネ「打ち水技術」で環境にやさしいヒートアイランド対策を提供:能美防災 京都市役所に今月、霧状の水滴を頭上から噴出し気温を下げるミストシャワーが設置された。気化熱が周囲の熱を奪う現象により気温が3℃前後下がるという。ミストシャワーは六本木ヒルズなど東京都心のほか、観測史上最高の気温40.9℃を記録した埼玉県熊谷市などで実績があり、ヒートアイランド現象を和らげる効果が期待されている。京都市では今月中に温度の変化などを測定して市内での普及策を検討していく予定だ。
経済産業省中部経済産業局が公募した地域新生コンソーシアム研究開発事業として、名古屋大学、中部電力、能美防災、川本製作所、トーキン、清水建設の6社が共同開発し、2005年の愛・地球博の「グローバル・ループ」、六本木ヒルズのメインエントランス「66プラザ」、秋葉原クロスフィールド、新丸の内ビルなどで導入実績のある「ドライミスト」で、ミストシャワーの機構を見てみよう。
ドライミストのミストは自然現象の霧(直径数μm~数十μmの水滴が1cm3の空気中に数個~数百個含まれる)状の水滴を言い、ドライは触れても濡れた感じがしないことを意味する。実際には、蒸散が容易で「化粧落ちしない≒水滴をほとんど意識させない」を目標とした平均値16μmのミストを発生させる。
提供:清水建設 ドライミストのシステムでは、クスノキ林が真夏に気化する量(蒸散量)7.5 mL/分・㎡を基準として採用している。この量の蒸散による冷却効果がすべて空気の温度を下げるのに使われると仮定すると、1分間あたり、高さ7mの空気柱に2℃の温度降下を与える。そこで同システムでは、100m×100mの空間を想定し、15kW(1.5W/㎡)の高圧ポンプユニットにより水道水を加圧、3.6m間隔で設置された消火用ノズルから、蒸散が容易な平均粒径16μmのミストを作り噴霧、クスノキ林相当分の霧を散布する。
システムを構成するドライミストノズルは、ノズル一つで3.0L/h(圧力6MPa)の噴霧能力を持ち、複数個を組み合わせて噴霧空間に適切な量のミストを散布するが、噴霧の停止時の液垂れを防止する機能を備える。高圧ポンプユニットは水を加圧して吐出するため、給水が不安定な場所にも適用できる。電動弁は6MPaの高圧水の閉止・通水を高レスポンスで行う高圧用電動弁を採用している。環境条件を観測する屋外用温湿度計、風速計、降雨センサーなどにより、設定温度以下になった際、観測ミストが過飽和になって湿度が高くなりそうな際、人が涼しさを感じられる一定の風速がある際、わずかな降雨でもミストが不快感を与えるような状況になる際には、ミストの噴霧を自動停止する。
ドライミストが温度を下げる能力は、家庭で使用するエアコンのわずか1/20程度のエネルギーで済むということから、一般の空調システムによる冷房が苦手な高齢者などを対称に家庭用ドライミスト冷房も登場してきている。ミストシャワーは、発生させた霧が気化するときに周辺の熱を奪う「打ち水効果」を狙う日本古来の発想に基づく独自技術。省エネとヒートアイランド効果の緩和が図れる日本発の技術が世界的に普及することを期待したい。
第55回 人工心臓の信頼性を支える軸受技術
第55回 人工心臓の信頼性を支える軸受技術提供:サンメディカル 体内埋め込み型補助人工心臓の事業化が進んできている。旭化成は先ごろ、ミスズ・サンメディカルが開発した体内植込み型左心室補助人工心臓「エヴァハート(EVAHEART)」について、日本を除く全世界で事業展開を進める。一方、旭化成とサンメディカルの合弁会社となるエヴァハートUSAは、北米地域でのエヴァハートの臨床開発・許認可取得・販売を担当、日本国内では、引き続きミスズ・サンメディカルが単独で事業を進めていく。
人工心臓の研究は1957年米国の動物実験から始まった。最初は心臓をまるごと置き換える空気駆動型の「全置換人工心臓」から始まり、1981年に臨床試験を実施している。次に、心臓は残したままで腹腔に補助的に埋め込む拍動(心臓の動きを模倣した「拍動流ポンプ」)型「補助人工心臓」の臨床試験が1987年から始まった(第1世代)。しかしサイズが大きく体重80kg以上の患者にしか適さなかった。そこで、2000年ごろから接触回転型の機械軸受を採用した超小型の軸流型補助人工心臓の臨床試験が行われた(第2世代)。形も大きさも単2乾電池級の超小型補助人工心臓であり埋め込みが容易なため、臨床試験はすでに世界で計3,000例を超えている。しかし接触回転型は摩擦による血栓が発生し10年程度で植替えが必要になる可能性があった。
これに対し、植替えが要らない非接触回転型の第3世代補助人工心臓の臨床試験が2004年から始まっている。磁気軸受を採用したテルモのデュラハート(DuraHeart)、ダイヤモンドライクカーボン(DLC)コーティング羽根車を有した流体動圧軸受採用のベントラシスト(VentrAssist)、ポンプ軸シール部分の血液凝固とモータ発熱を抑えるため、独自開発のメカニカルシールを採用し純水をポンプ・モーター内部に循環させるエヴァハートなどだ。デュラハート、エヴァハートともに日本から生まれた遠心ポンプ型の補助人工心臓で、いずれも軸受技術が製品の寿命と信頼性を支えている。
提供:テルモ たとえばテルモのエヴァハートでは、最大の課題である血栓の発生を防ぐべく、元京都大学工学部教授の赤松映明氏とNTNが共同で考案した磁気浮上型遠心ポンプ方式を採用している。従来型の「定常流ポンプ」では、血液を全身に送り出す羽根車を支持する軸受やシール部がポンプ室にあると、この部分が血流を妨げ、結果的に血栓が発生しやすくなり、また軸受部の摩擦によって赤血球の細胞膜が破れ、溶血が生じてしまう。そこで遠心ポンプの内部で回転して血液を押し出す羽根車を、NTN開発の磁気軸受により浮かせて非接触で回す方式である。羽根車の位置をセンサで検出、電磁石で羽根車を浮かせ、ポンプ室から機械式軸受やシール部をなくすことでこれらの問題を解決、日常動作時はもちろんのこと、耐久試験で運動負荷をかけて激しく振動させた時にも羽根車が浮上安定性を保つことが確認されている。2004年にはドイツで補助人工心臓の臨床試験をスタートし、 2007年にCEマークを取得、2007年に欧州で販売を開始した。現在、米国さらには日本での実用化を目指し準備を進めている。
国内での心臓移植の実施件数は欧米に比べてはるかに少ない上、移植までの待機時間は最短でも2年かかると言われ、長期にわたり使用できる補助人工心臓が求められている。わが国軸受技術のさらなる進歩により、埋め込み型補助人工心臓の製品寿命の延長と生体埋め込みでの信頼性を高めることで、患者のQOL(Quality of Life)向上に貢献していくことに期待したい。
第56回 レアメタル確保に向け海洋資源開発ロボ開発へ
第56回 レアメタル確保に向け海洋資源開発ロボ開発へ提供:JAMSTEC。写真は、自律型無人探査機と同じ原理の深海巡航探査機「うらしま」 経済産業省は先ごろ、「レアメタル確保戦略」を取りまとめた。ハイブリッド車モータ用など高性能磁石に使われるレアアースやリチウムイオン電池のリチウムやコバルト、液晶画面に使われるインジウムなど、レアメタルはわが国の誇る工業製品の製造に必要不可欠な素材だが、中国の急速な経済成長などにより国際的な需給逼迫や供給障害が発生する可能性が懸念されている。今回の戦略では、単位あたりのレアメタル含有量の多い携帯電話、デジタルカメラ等の小型家電、超硬工具などの使用済み製品について、リサイクル・システムの構築や既存システムを活用した回収促進に着手するとともに、リサイクル技術の研究開発を通じたレアメタルの回収・再利用といった 「リサイクル」のほか、「海外資源確保」、「代替材料開発」、「備蓄」の四つの施策とともに、資源国との多面的関係の強化、人材育成、技術力の強化、ユーザーを含むレアメタル・サプライチェーン産業の一体的取組といった関連する対策に取り組むことなどを謳っている。
こうした中、省資源国のわが国ながら、周辺の深海底では、地下深部に浸透した海水がマグマなどにより熱せられ海底に噴き出し、それが冷却される過程で熱水中の銅や鉛、亜鉛、金、銀などが大量に沈殿して作られた海底熱水鉱床や、コバルト・リッチ・クラストなどの鉱物資源やメタンハイドレートなどのエネルギー資源が多量に埋蔵されている可能性が明らかになってきており、海洋資源の探査に注目が集まってきている。海洋研究開発機構(JAMSTEC)では海洋資源の本格探査に向け、実証試験専用探査ロボットの開発に乗り出している。自動的に潜航する「自律型」と「遠隔操作型」の2タイプの探査ロボットの開発と探査ロボットを搭載する支援母船の改造で40億円の予算を計上した。
海底熱水鉱床などの資源探査は、海底地形や火山活動分布により、その存在地域を推定する方法が一般的。無人探査ロボットは、未発見の海底熱水鉱床を広域で効率的に探査するほか、鉱床の資源量を高精度で把握できる。
自律型は、機体に探査センサや内蔵したコンピュータにあらかじめ設定したプログラムで位置を計算しながら航走する。また、遠隔操作型は機体から垂らしたケーブル先端のセンサを探査に応じて自由に交換できるほか、鉱物を含む試料を採取する機能を持つ。現行の潜航最大深度3,500kmの深海探査機「うらしま」をベースに、水深4,500km目標など探査機能を高めていく。
提供:JAMSTEC たとえば「うらしま」の推進器はモータ、減速機、プロペラで構成されているが、大水深での高い水圧に耐え、できる限り小型軽量とするため、モータと減速機を収納した容器を油で満たし、圧力調整用ブラダを設け、海水の圧力と容器内部が均等になるような方式としている。音響通信の障害だった減速機からの機械ノイズが発生しないよう、特殊な斜歯歯車を製作し使用しているが、前方障害物探査ソーナーや高度ソーナー等の音響機器を多用していることからは、さらなる音響ノイズの発生をねらって燃料電池の搭載も検討されているという。
海洋研究開発機構ではこのほか、日産自動車と共同で、日産が一般車の車庫入れや縦列駐車を助けるために実用化した技術をベースに、海底探査機の前後左右と下側が見渡せる画像認識技術の開発を開始、今後10年をめどに商業化をめざすとしている。レアメタル確保に向けた海洋ロボ開発では、先述の歯車の低ノイズ化など機械要素やシステムの技術の転用もできそうである。わが国産業発展を支える資源開発のための研究開発の進展に期待したい。
第57回 鳩山新内閣へ、景気回復に向け産業界との密な対話を
第57回 鳩山新内閣へ、景気回復に向け産業界との密な対話を 第45回総選挙において、民主党が単独過半数(241議席)を大幅に上回る308議席を獲得、鳩山由紀夫・民主党代表が次期首相となることが確実となった。産業界としては、閉塞感のある経済環境打破への期待をこめた政権交代の後押しという意味合いが強いだろう。
そんな中、日本自動車工業会、石油連盟など産業界の代表団体が懸念するのは、2020年までに2005年比30%(1990年比25%)の二酸化炭素(CO2)を削減するという民主党のマニフェストである。これは麻生首相が決めた中期目標2005年比15%削減(1990年比8%減)を大幅に上回る。京都議定書の2008年~2012年度の排出量の平均値を基準年(1990年)比6%削減する目標に対し、2007年度の排出量は逆に同9%増えている。これは、産業部門で1990年比2.3%減という一方で、商業・サービスなどの業務部門や家庭部門がいずれも同40%以上増えているためだ。だからこそ健闘している産業部門では、民主党の掲げる1990年比25%、2005年比30%という突拍子もない数値に疑念を抱いているのである。
本年6月に麻生首相がCO2排出量削減の中期目標として2005年比15%減を決めたのを受けて産業界では、たとえば鉄鋼なら約2割省エネ化を図るコークス製造技術をコークス炉6基に導入することを想定、発電では原子力発電所を9割新設し現在の稼働率60%程度を80%程度に引き上げるなど個々に対策を打ち出したが、産業界では現状、CO2の2005年比10%以上の削減は技術的に難しいとの見解が大勢を占める。
民主党としても掲げた数値の根拠として、全量買取りを前提とした太陽光発電や風力発電、バイオマスなど再生可能なエネルギーの開発を想定しているのだろうが、太陽光発電の30年保障といった耐久信頼性や、日本の風土に合った発電効率が高く安全な風力発電の設置拡大など、再生可能なエネルギーの開発も一朝一夕に改善されるものではない。長期政権を続けてきた自民党との関係をもとに政策要望してきた日本経団連など産業界にとって、民主党との対話の経験はまだ少なく、そのマニフェストに産業界の声が反映されているとは言いがたい。国民に選ばれた政党としてマニフェスト厳守は重要であろうが、必ずしも子ども手当てや高速道路無料化が支持されているわけではない。エコカー支援策の効果もあって8月の新車販売台数が13ヵ月ぶりに前年同月を上回るなど、ようやく景気回復が踊り場に差し掛かってきた時期だけに、鳩山新内閣にはぜひとも産業界との対話を密にして産業界の現実を認識してもらい、企業のR&D活動の火を消すような、企業の体力をそぐような方向に政策を進めることのないよう、自動車関連諸税の見直しなど市場活性化、さらには本格的な景気回復へと導く舵取りを期待したい。
第58回 世界トライボロジー会議が京都で開催、省エネ技術を次世代につなぐ
第58回 世界トライボロジー会議が京都で開催、省エネ技術を次世代につなぐWTC Ⅳ附設展示会のようす 前にも述べたが、摩擦・摩耗・潤滑の科学技術を「トライボロジー」と呼ぶ。1966年にピーター・ジョスト氏が英国の製鉄所で潤滑管理を徹底させることでGNPの1%超を節減できるとの報告を行い誕生した科学技術で、エンジンの摩擦を減らすことで自動車の燃費を向上したり、逆にブレーキの摩擦を高くコントロールすることで安全性を確保するのも、生産機械の潤滑を管理することで突発の故障や事故による効率の低下を防ぐのも、このトライボロジーの技術である。
そのトライボロジー分野最大のイベントである世界トライボロジー会議(WTC Ⅳ)が9月6日~11日、京都の国立京都国際会館で開催、海外50ヵ国1地域から、約1500人が参加した。WTCは、国際トライボロジー評議会(International Tribology Council)が統括し、4年ごとに開かれるトライボロジー分野最大のイベント。1997年のロンドン、2001年のウイーン、2005年のワシントンD.C.に続く第4回目で、日本ではもちろん、アジアでも初の開催となる。
今回の会議では、シンポジウムとして、持続可能な発展を実現するトライボロジー(エコ・トライボロジー)、トライボロジーの大規模数値シミュレーション、人と調和するトライボロジー、アジア太平洋地域の工業におけるトライボロジー的課題の四つのメインテーマで、ミニシンポジウムとして、次世代エネルギーのための水素のトライボロジー、次世代に向けた潤滑剤の先進技術、トライボロジーのためのダイヤモンドライクカーボン(DLC)、合成潤滑油の使用によるエネルギー節減、超マイルド摩耗とトライボケミカル反応、トライボロジーの歴史、フルードパワーのトライボロジー的側面、自動車省燃費のためのトライボロジー、情報記録装置のためのトライボロジー、潤滑グリースの革新的研究、摩擦の科学、新分野におけるトライボロジーの課題の12のテーマで、テクニカルセッションとして、トライボロジーの基礎、表面工学、加工および機械要素、潤滑および潤滑剤・添加剤、マイクロ-、ナノ-、分子トライボロジー、トライボシステムの6のテーマで口頭発表があり、ポスターセッションと合わせて922件の発表がなされた。
また附設展示会として「世界の省エネ・環境技術展」が開催、自動車・機械や自動車部品・機械要素(ベアリング、シールなど)、潤滑剤・添加剤、試験・分析機器、研究・出版などが92小間の規模で出展した。一般公開とし、近郊の小・中学生を招き、摩擦体験などのトライボロジー教室といったイベントも設け、次代を担う若い世代のトライボロジーへの関心を深める工夫も見られた。
7日に行われた開会式典では、まず開会の挨拶に立った木村好次・WTC Ⅳ実行委員会委員長(東京大学・香川大学名誉教授)が「1997年のロンドン、2001年のウイーン、2005年のワシントンD.C.に続いて4回目の開催となるトライボロジー分野で世界最大のイベントとなるWTCの開会式を、秋篠宮殿下ご臨席のもと執り行えることを大変喜ばしく思う。環境問題という世界的危機に対し各国の協調が求められる中、トライボロジーには、機械の効率化によるエネルギーの節減を図る技術革新が求められている。自動車からIT、重工業などの技術の発展とともに、克服すべきトライボロジーの課題は次々に生まれていく。本会議では、21世紀のさらなる技術革新に向けたトライボロジーの適用など、国を越えて情報を交換していただき、トライボロジーの国際協調を進める契機としてほしい」と語った。
続いて日本トライボロジー学会会長の町田尚氏(日本精工顧問)が「トライボロジーは機械要素の効率化を図りエネルギーを節減することにより世界的課題であるCO2削減に貢献する技術。トライボロジーは、持続可能な社会のためのキーテクノロジー。今回発表される922件という研究を効率よく利用し、持続可能な社会とリソースの実現、地球環境保全に役立ててほしい、またこの機会に、次代を担う若者と一般の方々にトライボロジーの重要性を理解していただくとともに、各国のトライボロジー学会や関連団体との協調により、持続可能な社会とエネルギー節減によるCO2削減につなげていきたい」と述べた。
さらに共同主催者となる日本学術会議会長の金沢一郎氏の挨拶に続き、国際トライボロジー評議会プレジデントでトライボロジーの産みの親のピーター・ジョスト氏が「トライボロジーは日本においても自動車からITなどのナノテクノロジーに至るまで高性能化、産業の発展、利益の創出に貢献してきたが、これからはエネルギー節減による環境改善やクオリティー・オブ・ライフなど人と環境にやさしいグリーン・トライボロジーはトライボロジストの責務」と強調した。
来賓の挨拶に立った秋篠宮殿下は「40以上の国・地域が参加する世界トライボロジー会議の開会式に出席できて、また第4回WTCがアジア・パシフィック地域で初めて日本をホスト国に開催されることをうれしく思う。トライボロジーは相対運動する表面に関する摩擦・摩耗・潤滑の基礎的な研究であると認識している。トライボロジーは自動車、コンピュータ、橋や人工関節に至るまでの最先端分野の基盤技術であり、持続可能な社会と人類、エネルギーとリソースの節減を通じ環境保全を図るキーテクノロジーと思う。機械や材料、物理、化学、医療などの幅広い分野における、研究者とエンジニアの協調と努力の結集により、その適用範囲は広がり、またその成果は様々な分野の新技術開発へと適用されている。今回は最新の研究発表に加えて、小学生、中学生といった次世代を担う人々に向けた啓蒙的な教室も企画されているという。京都議定書のかわされたこの場所で持続可能な社会に貢献するトライボロジーについて活発な議論が行われるとともに、次世代を担う人々や参加者全員がこのトライボロジーという省エネ・省資源の科学・技術に関心をもっていただき、継続的な地球環境保全に関わっていくことに期待している」と賜った。
身近なところではベアリングによる摩擦低減でエアコンの電力消費量を3割抑えているといったように、トライボロジーは機械・機械部品の摩擦面の設計、コーティングなど摩擦面材料や潤滑剤の開発で摩擦をコントロールし摩耗を軽減することで、エネルギーと資源の節減、環境保全に貢献し、家電から自動車・鉄道車両・航空機、産業機械、加工システム、精密情報機器、宇宙機器、生体関連に至る広範な分野で適用され、その経済効果は国内で年額8.6兆円に上るとの試算もある。WTC Ⅳ開催を機に、トライボロジーというコンセプトがより産業界に浸透し、省エネ・省資源のシステムが設計・開発されていくことに期待したい。
第59回 材料・機械要素技術で水ビジネスを牽引
第59回 材料・機械要素技術で水ビジネスを牽引提供:荏原製作所 過去50年間の世界の人口増加が2倍だったのに対し、BRICsをはじめとする新興国の経済発展や地球温暖化などから、水の需要は4倍(OECD調査)になっており、世界的な水不足が深刻化してきている。水資源確保の対策として、中東では海水淡水化プラントの建設投資が活発化し、北アフリカの産油国、スペイン、北米、中国・沿海部などでも海水淡水化プラントの建設ラッシュが始まっている。この海水淡水化の技術のなかでも省エネに優れる逆浸透膜(RO膜)が今後20%以上の伸びが予想されており、この水処理市場においてわが国メーカーは海水淡水化向けRO膜で世界市場の70%のシェアを占め、また前処理で使われる精密除濁膜(MF、UF膜)市場でも40%のシェアを占める。2025年に110兆円市場が予想される水ビジネスにおいては、日本に技術優位性があるといえよう。
さて、RO膜を使った海水淡水化では、海水に高圧をかけRO膜と呼ばれるろ過膜に通し淡水を作り出す。平均的な塩分3.5%の海水から日本の飲料水基準に適合する塩分0.01%の淡水を得る場合には、55気圧以上の圧力をかけてろ過する必要があるとされ、加圧にはタービンポンプやプランジャーポンプなどの高圧ポンプが使用される。
提供:荏原製作所 たとえば荏原製作所では、プラント運転コストの1/3がポンプを動かす電力費であるとして、海水淡水化プラント向け動力回収装置とポンプを開発中だ。動力回収装置はプラント内の水流から得たエネルギーを送水の動力に活用するもので、RO膜方式の海水淡水化プラントに搭載、送水ポンプの負荷を抑える。現在、水流から直接動力を得る「水車型」の装置が多いが、荏原が開発中の「容積型」は、膜を通過した水の水圧を回収し、膜に海水を送る動力に利用する。水圧の回収と送水はピストンを介して行う。
立型軸流ポンプ・斜流ポンプの軸受としてはすでに水中ゴム軸受が採用、金属シェルの内面にゴムを密着加硫し、ゴムには一定本数の溝をつけて潤滑水を通して使用されている。しかしピストン式では水圧機器と同じ使用環境になろうか。たとえば平成14年度~19年度の経済産業省の温室効果ガス削減技術開発のナショナルプログラム「低摩擦損失高効率駆動機器のための材料表面制御技術の開発プロジェクト」では、水圧機器を対象にμ(摩擦係数)をコントロールして駆動機器のエネルギー効率の向上を図る研究を行っている。油圧機器の場合には作動媒体の作動油そのものが潤滑・防錆効果を持つため摺動部分には一般的には表面処理などを施さない炭素鋼などが使用されているが、水圧機器では水そのものが低粘度であることから流体潤滑膜の形成能が低く、潤滑作用をほとんど持たず、油圧機器に使用されている未処理の金属系材料をそのまま水圧機器に使用することはできない。そこで、安価で加工性に優れる金属系材料を基材とし、水潤滑性を有する表面処理を適用することで水圧機器摺動部分に低摩擦・摩耗特性を付与することを目標にして、自己潤滑性を有するDLC(ダイヤモンドライクカーボン)膜を選定、UBM(Unbalanced Magnetron Sputtering)法により形成した皮膜の形成条件と皮膜構造と水環境中における摺動特性の関係を調査した。Siを含有したDLC膜が膜の耐はく離性が高く、耐摩耗性も良好という結果だった。また、DLCの摩擦係数低下に及ぼす水の影響も様々な研究で明らかにされてきている。
水環境で使われる機械要素としては、長期信頼性の面から防錆性も必要になるだろう。食品機械などでは錆に強いステンレス製軸受などステンレス材料の実績が多いが、樹脂材料では自己潤滑性もあり機械的強度も高いPEEK(ポリエーテルエーテルケトン)も水力発電機などで実績を持つ。しかし、ボルト・ナットなども含めた機械要素全体がコストアップにならないよう、安価な炭素鋼に物質置換型高周波誘導加熱ピーニングシステムなどで表層部のみに高耐食性ステンレス鋼の性質を持たせる表面改質の研究も進んできている。
日本に技術優位性がある水ビジネスでは、さらに海水淡水化システムの電力を風力発電や太陽光発電で賄う構想もある。同じく日本に技術優位性がある材料・表面改質や軸受など機械要素技術を活用して、水ビジネスの拡大とともに、わが国産業界が市場を牽引していくことに期待したい。
第60回 補助ブレーキ義務付けで、エレベータのさらなる安全性向上を
第60回 補助ブレーキ義務付けで、エレベータのさらなる安全性向上を新安全基準の認定を取得した補助ブレーキ 扉が開いたままエレベータが動いた場合、自動的に運転を止める補助ブレーキの取付けを義務付けた改正建築基準法施行令が9月28日に施行、同日以降に着工する建物から適用が始まった。2006年に東京都港区のマンションで男子高校生がシンドラーエレベータ社製のエレベータに挟まれ死亡した事故は、ブレーキ不良で扉が開いたまま急上昇したのが原因だったことから、国土交通省が昨年9月に補助ブレーキを義務付けるよう政令を改正した。エレベータかごを吊るロープを挟み急停止させるロープブレーキを取り付けたり、ロープ巻上げ機の電磁ブレーキを二重化するなどの対策を取った機種がすでに国交省の認定を受けている。
今回の施行に先立つ5月、シンドラーエレベータでは2006年の死亡事故に関する技術説明会を開催、事故原因とされるブレーキ制止力の低下を招いたブレーキライニングの摩耗について、「ブレーキ装置の部品であるソレノイドの電気故障によりブレーキドラムとブレーキライニングが擦れる状態が長く続いたため」という見解を示していた。
提供:三菱電機 エレベータのブレーキには、動力が切れたときや、走行中にドアが開きドアスイッチが切れた場合に作動する電磁ブレーキと、ドアスイッチかごおよび昇降路の出入口のドアが全て閉じた状態でなければ、運転回路を働かせないスイッチがある。まず、ロープ式の一般的なエレベータでは、まず電気的にかごを減速、停止させ、ブレーキはこの停止したかごが動かないよう巻上機を固定する役割を果たす。ブレーキはまた、停止時に、スプリングの力でブレーキパッドがブレーキドラムを押さえつけ、エレベータのかごを保持する仕組みになっている。エレベータが動く場合は、ドアが閉じたことを示すスイッチが入り、安全が確認された後、ブレーキの電磁力でスプリングを押し開き、ブレーキを開放する。もし電源が切れた場合は、電磁力がなくなるため、スプリングの力で強制的にブレーキがかかる。
大手メーカーで新安全基準に対応する機種の認定取得が進む一方で、試験塔など大規模な試験設備を持たない中小企業での認定取得は遅れているというが、今回対象となっている新規物件だけでなく、国交省の昇降機等事故対策委員会では「国内で70万台程度という既設のエレベータにも普及を図ること」を意見、既設エレベータへの補助ブレーキ取付けも数年後には義務付けられる見通しとなっている。中小企業も含めたエレベータメーカー、ブレーキなどの部品メーカー、材料メーカーが一丸となって、さらなるエレベータの安全性向上に取り組んでほしい。
第061回~第070回
第061回~第070回第61回 モーダルシフトの加速で、高速鉄道車両の需要が増加
第61回 モーダルシフトの加速で、高速鉄道車両の需要が増加時速350kmのefSET(提供:川崎重工業) 鉄道車両はCO2排出量が少ない大量輸送手段として、世界的にその重要性が見直されている。自動車や航空機による輸送を鉄道や船舶による輸送で代替する「モーダルシフト」が進展し、国土交通省では2005年に38.1%だったモーダルシフト化率(500km以上の産業基礎物資以外の雑貨輸送量のうち、鉄道・船舶で運ばれる輸送量の割合)を2010年度までに50%に引き上げる目標を掲げている。
特に都市間移動の主要交通手段として、時速250km以上の高速鉄道の導入が検討され、現在米国、ブラジル、ロシア、インド、ベトナムなどが具体的に新規建設計画を進めている。今後20年ほどの期間に世界で1万km前後の高速鉄道路線が増設される予定で、これに応じた高速鉄道車両の需要が見込まれ、高速車両用の軸受の開発競争が激しくなってきている。
鉄道車両用軸受には、モータ(主電動機)に使用される主電動機用軸受、モータの出力を車軸に伝える駆動装置に使われる駆動装置用軸受、車体重量を支える車軸軸受がある。これら軸受は、いずれも鉄道の走行に大きく関わる基幹部品として高信頼性が要求される一方、メンテナンス周期の延伸が求められている。
車軸用軸受は、軸を直接支持し、また線路樹脂製保持器を採用した車軸用軸受(提供:NTN)からの振動が直接伝わる過酷な環境下で使われ、かつ転がり疲れ寿命の長寿命化が求められている。そのため欠陥につながる介在物の少ない高清浄度鋼が使用されている。また高速化に伴うシール摺動部の発熱を抑えるため、軽接触タイプなどの低発熱シールが使用されている。潤滑寿命の延長からは、封入グリースの改良とともに、従来の鋼製保持器から海外メーカーで一般的な樹脂製保持器を採用して摩耗粉を抑制している。
グリースポケット形状を工夫した主電動機用軸受(提供:日本精工) 主電動機のブラシレス化に伴い唯一の摺動部品となった主電動機用軸受では、その寿命が主電動機のメンテナンス周期を左右するようになっている。主電動機軸受には60~90kmで中間給脂が行われているが、120万kmへのメンテナンス周期延伸のニーズに対し、長期グリース補給を維持できるグリースポケット形状などの工夫がなされている。主電動機内を流れる電流により転動体と軌道面接触部が溶融する電食を防ぐため、セラミック製の転動体を用いたり外輪に樹脂やセラミック被膜を施すなど、絶縁対策がとられている。
ところで、鉄道車両用軸受に関する規格は、欧州委員会の「欧州高速鉄道ネットワークの相互運用性に関する規格」に基づいて、鉄道車両用車軸軸受に関する規格「EN規格」が制定されている。欧州各国はもちろん中国市場で標準採用されており、このEN規格に準拠した鉄道車両用軸受の開発が進んでいる。
鉄道車両では、カナダのボンバルディア、ドイツのシーメンス、フランスのアルストムがそれぞれ世界シェア20%近くを持ちビッグ3と言われる一方、日本企業は合わせて10%程度のシェアだが、急追すべく海外に活路を見いだそうとしている。新幹線以来の高速車両開発で培った車両および軸受の高信頼性技術が、世界市場でますます活躍していくことを期待したい。
第62回 高機能フィルム市場拡大で注目されるウェブハンドリング技術
第62回 高機能フィルム市場拡大で注目されるウェブハンドリング技術提供:東海大学・橋本 巨研究室 ロームでは先ごろ、厚さ0.3㎜で曲げられるフレキシブル有機EL(エレクトロ・ルミネッセンス)照明を開発、巻き取りできる基板を使用しているため、ロール・ツー・ロールでの量産が可能という。近年、紙やフィルム、鋼材などの産業だけでなく、こうしたフラットパネルやフレキシブル回路、太陽電池など最先端技術分野でも、シート基材からロール・ツー・ロール基材へと移行傾向にあり、ウェブハンドリング技術の重要性が増している。ウェブハンドリングとは、新聞などの印刷物や写真フィルム、磁気テープなどの情報記録媒体、金属薄膜、液晶モニターに用いられる光学フィルムなどの柔軟で長尺の媒体である「ウェブ」を搬送し、途中処理工程を経て最終的に巻き取る技術。製紙・印刷技術やフィルムなどの搬送工程で多くの成果を上げてきたが、近年は先述のとおり、フレキシブル電子デバイスの研究・開発が活発化してきている。中でもフレキシブル有機薄膜太陽電池は、ウェブハンドリング工程による生産で、既存の太陽電池パネルよりも安価に生産できるとして実用化が期待されている。
ウェブハンドリング(提供:橋本 巨研究室) ウェブハンドリングシステムではウェブはローラを介して搬送され、最終的に巻き取る。このとき、ウェブとローラ間、またはロール層間に巻き込まれる空気層が問題になり、ウェブ浮上量・空気層圧力分布・ウェブとローラ間およびロール層間の摩擦特性などが問題とされる。ウェブは巻き取られて次の処理工程に受け渡されるが、巻き取られたロールにスリップやしわなどが発生し、経済的損失を引き起こしているのが現状。このような不具合は巻き取る際の速度や、ウェブの張力が適切でないことが原因と考えられていることから、東海大学・橋本 巨教授の研究室では、どのような条件で型崩れやしわが発生するか調べ、その防止法に関する研究をトライボロジー(摩擦・摩耗・潤滑の科学・技術)の観点から行っている。
接触に伴うこうした問題に対し、ソーラーリサーチ研究所では空気を噴出することによりフレキシブル太陽電池、偏向板、フィルムなどを浮かせた状態で懸垂する非接触搬送装置で構成される保持装置と、ワーク進行と同調して走行する非接触支持走行装置を採用した。フィルム送出部ではフロートチャックを用いた空気流による送出機構により、搬送課程ではフィルム先端部に垂れ下がりを生じさせることなく搬送できる。非接触搬送装置により、フィルムにキズ、汚れ、ストレス、静電気の付着が起こらないという。
提供:TDK ウェブ側でもロール・ツー・ロール機構への対応が進む。TDKでは、記録メディアで培ったウエットコーティング技術を応用展開した独自3層構造により、高い透過率を確保しながら、優れた柔軟性・屈曲性・摺動性を有する透明導電性フィルム「フレクリアTM」を開発、デジカメなどに搭載されるタッチパネル向け上・下電極用途や、電子ペーパー、電磁波シールド用途などに利用できるとしている。
ウェブハンドリング関連市場はフレキシブル太陽電池など環境保全に関わる高機能フィルムの市場拡大で、2015年には30兆円市場とも目されている。ロール表面の摩擦係数や表面粗さの制御による摩擦挙動のコントロールや、先述のようなウェブ側の摺動特性改善、さらにはエア搬送、エア巻き取りのような比接触ハンドリング技術も含め、拡大するロール・ツー・ロール市場に対応するウェブハンドリング技術の進展に期待したい。
第63回 東京モーターショーが開催、エコカーを支えるベアリング技術
第63回 東京モーターショーが開催、エコカーを支えるベアリング技術 日本自動車工業会( http://www.jama.or.jp )は、千葉市・幕張メッセで「第41回東京モーターショー2009」を開催した。期間は10月23日から11月4日の13日間(一般公開は10月24日から)で、10ヵ国・1地域から2政府・2団体・108社が参加し、ワールドプレミア(世界初の発表)が39台、ジャパンプレミア(日本初の発表)が21台出展される。世界的な不況による車需要の減少などを理由に、出展者数は前回2007年開催の241社から半減、海外からの出展も英ロータスと独アルピナの2社のみ。日本勢がメインのショーということもあり、テーマはが“楽しさと環境の両立”をシンプルに表現した「クルマを楽しむ、地球と楽しむ。」としたこともあって、本年トヨタ自動車「3代目プリウス」とHonda「インサイト」が投入されたハイブリッド車と、三菱自動車「i-MiEV」と富士重工業「ステラ」が投入され幕を開けた電気自動車(EV)など、エコカーが前面に出た出展となった。
ハイブリッド車では、トヨタ「PRIUS PLUG-IN HYBRID Concept」が注目を集めた。3代目プリウスをベースとし、駆動用バッテリーにはこれまでのニッケル水素電池に替えて、初めてリチウムイオン電池を搭載、家庭用電源などからの外部充電を可能とする、年末にも投入予定のPHV(プラグインハイブリッドハイブリッド車)のコンセプトモデル。燃費性能55km/L以上(CO2排出量42g/km以下)、満充電でのEV走行距離20km以上を目標値とし、充電時間は100Vで約180分、200Vで約100分を目標としている。
2010年にも投入予定の日産自動車の5人乗りEV「リーフ」ではEV専用プラットフォームを採用、床下に薄いラミネート型バッテリーを車体中央のホイールベース間に搭載するとともに、ゆったりとした運転席と後部席のスペースを確保している。広い室内空間を可能にしている。蓄電容量や出力を倍増したリチウム電池により、一度の充電で160km以上の走行が可能としている。
こうしたエコカーのオンパレードに対応して、部品各社もさまざまな対応技術を展示している。
提供:トヨタ自動車 1996年発売の初代プリウスでモーター出力がシステム電圧288Vで33kWだったのが、3代目プリウスでは650V、60kWと出力密度は6倍に向上、小型・軽量化を実現している。さらにモーターのトルクを増幅することで大きな駆動力を発生し、パワフルな走りとシームレスな加速をもたらすリダクションギヤにより、モーターの小型化と高出力化を測っている。また、駆動用モーターに大電力を供給し、高出力バッテリーへの充電も行う発電専用モーター(ジェネレーター)でも、集中巻きによるコイル形状の工夫により小型・軽量化を達成。エンジンからの動力を車輪(出力軸)と発電機に分割して伝達する動力伝達機構(プラネタリーギヤ)では、エンジン、モーター、ジェネレーターを結合し、それぞれを最適に制御することで、シームレスな加速を生み出す電気式の無段変速機として機能している。こうしたアプローチにより3代目プリウスでは、1.8Lガソリンエンジンながら2.4L車並みの加速性能を実現しつつ、JC08モード走行燃費で、32.6km/L、10・15モード走行燃費で、38.0km/Lを達成している。つまりハイブリッド車の出力向上、燃費向上では、小型・軽量化を実現する駆動用モーターとそのトルクを高めるリダクションギヤ、駆動用モーターに大電力を供給する発電専用モーターの高速回転化が進められている。
次世代ハイブリッド車の燃費向上を目的に駆動モーターや発電機構の小型・軽量化が進められる一方で、小型化による出力低下を補うため、高速回転のニーズが高まっている。日本精工では次世代ハイブリッド車の モーターおよび発電機構用玉軸受として現行18000rpmの回転数を1.5倍となる30000rpm以上に高めた。高速対応技術としてはまず、軸受の潤滑油入り口に油流を制御するプレートを設置、これにより、超高速回転時の大きな遠心力が発生する環境下でも、潤滑が枯渇しやすい内輪側に潤滑油を確実に供給、摩擦による発熱を低減した。また、軸受内部の溝寸法や玉径などを最適化することで超高速回転下でも摩擦と発熱を抑制、焼付きを防止したほか、玉および内輪と保持器間のすき間を調整することで保持器の振動を抑制し、接触部の摩耗を低減した。さらに、軸受の超高速回転時に保持器にかかる遠心力による変形を防止するため、保持器円環部を厚くし、保持器の強度を向上させた。
ジェイテクトではハイブリッド車の変速機(リダクションギヤ)向け軸受として、高速回転時の遠心力による保持器の変形を抑え、従来比3.3倍の50000rpmという高速回転対応を可能とした。樹脂製保持器部品2対を玉の両側から弾性嵌合することで、遠心力による変形を抑えた。
ハイブリッド車では(アイドリングストップシステムにおいても同様であるが)、頻繁に起動・停止が繰り返されることからエンジンベアリングやピストンリングなどの摺動部で潤滑膜が形成されにくい。これに対し大同メタル工業では、特にエンジンベアリングのうち主軸受に使われるアルミニウム合金軸受で、耐摩耗性に優れるアルミニウム-すず-シリコン系合金(Al-Sn-Si)のSiの粒子径を適切な大きさにコントロール(Siを塊状化)することで耐摩耗性を高めている。
一方、省燃費エンジンの革新技術も展示された。たとえばマツダの直噴エンジン「マツダSKYコンセプト」では、フリクション低減手法の積上げを地道に行った。たとえばピストンリングの低張力化を図りつつ、相手材となるシリンダライナの追随性を高めシール性能の向上と低フリクション化を図った。また、エンジンベアリングを薄幅、薄肉化しつつ油だまりとなる溝加工などを施し、潤滑性・耐久性を高めながら低摩擦化したほか、ベルトがプーリと接触する面積を広く取ったりプーリ位置を最適化することで、ベルトのテンションを下げ、フリクションを低減した。こうしたフリクション低減と最適な混合気の形成を図った上で、直噴システムが持つ噴霧形成の自由度を活用して、極限まで膨張比を高めた。次世代直噴インジェクター、高機能吸排気可変バルブタイミングシステムなどの技術を採用し、現行2.0Lエンジン比で燃費・出力(トルク)を約15%改善。アクセラクラスの車両に搭載した場合で、現行デミオ並みの低燃費を実現するという。
次世代EV対応として、NTNや日本精工などベアリング各社でも車軸軸受(ハブベアリング)にモーター、荷重センサー、電動ブレーキなどを組み合わせてホイールを制御する「インホイールモーター」などの開発も進んできているが、本年エコカー補助金制度などの後押しもあり市場が急速に拡大したハイブリッド車に向けた、部品開発競争激化の現状の一端が、今回のモーターショーからもうかがえる。
第64回 風力発電機用軸受のビジネスが活発化
第64回 風力発電機用軸受のビジネスが活発化NTN宝達清水製作所(提供:NTN) 風力発電機の市場が世界的に拡大基調にあるなか、軸受各社では風力発電機向け事業を強化する動きが活発化してきている。
風力発電機用主軸軸受で世界シェア3位のNTNは10月26日、風力発電機向けなど超大形軸受を製造する子会社、NTN宝達志水製作所(石川県宝達志水町)を稼働した。発電機のブレード(主翼)とロータの回転を支える主軸軸受の直径は1~3mにも及ぶ。新工場設立により、これら超大形軸受の旋削、熱処理、研磨、組み立てまでの全工程を一貫生産できる体制を構築、既存の桑名工場(三重県桑名市)と合わせて、超大形軸受の生産能力が倍増するという。
提供:三菱重工業 風力発電機はブレード、タワー(支柱)、ナセル(発電を起す本体)からなる。ブレードで風を受けてロータを介して主軸が回転、その10~30min‐1の回転速度を増速機により発電可能な1,200~1,800min‐1という回転速度まで増やし、発電機により発電する(誘導発電機)。回転トルクを増速機に伝える主軸の軸受、増速機を構成するキャリア、遊星ギヤ、低速軸、中間軸、高速軸の各軸受、発電機用軸受がそれぞれ活躍している。
ロータ主軸用軸受では常に変化する風によって荷重、モーメントや回転速度が大きく変動する。特に突風の際の過負荷による変形量や隙間管理が重要で、ブレードやギヤボックスの振動によってフレッティングコロージョンが発生する危険がある。このため軸受選定とすき間およびはめ合いの適正化と適正なグリース選定が重要となる。軸受鋼としては通常、焼入れ性の良いSUJ3やSUJ5などが使用されている。サイズが大きいため熱処理歪みの小さいことが求められることもある。
提供:日本精工 風力発電機の増速機は高所に設置されメンテナンスが難しいことから、増速機用軸受には高い信頼性と長期の寿命保証が求められるほか、発電効率の向上を目的とした風力発電機の高出力化•大型化が進められており、負荷能力の高い軸受のニーズが高まっている。荷重負荷能力の高い軸受として、増速機用軸受には従来から総ころ円筒ころ軸受が使用されているが、総ころ円筒ころ軸受は転動体同士が回転中に直接接触することで高速回転の場合は焼付きや摩耗が発生し、それが高速回転実現化の障害になっていた。特に増速機用軸受では歯車群と高粘性の潤滑油が共通化されるため、歯車の摩耗粉など異物混入の潤滑条件になりやすく、異物混入潤滑環境下での長寿命化対策が求められていた。これに対し増速機用軸受でシェアの高い日本精工では、転動体材料に浸炭窒化熱処理技術を採用することにより、耐焼付き性と耐摩耗性を向上しつつ、転動体の端面形状の最適化によりアキシアル荷重負荷能力を飛躍的に向上、総ころ円筒ころ軸受で許容回転速度は約2.5倍(同社従来品比)へと向上している。
セラミック玉絶縁軸受(提供:ジェイテクト) 発電機用軸受は特に日本で多い落雷や、帯電による軸受内部の電流通過によるスパーク現象(電触)の防止対策のため、寿命が長く信頼性の高い軸受鋼や肌焼鋼をベースにセラミックスの絶縁被膜処理を施した軸受やセラミックス製の転動体を使用した軸受など)が用いられている。
こうした軸受の材料・表面改質での技術開発が進められているほか、風力発電機用軸受世界シェアトップのSKFや2位のシェフラーでは状態監視(メンテナンス)技術などメンテナンス技術、潤滑技術、ハウジングデザインも含めた事業展開を進めている。
風力発電機は発電コストが最も安い再生可能エネルギーとして導入が進み、2008年に世界で前年度比41%増の3132万KW分が設置、2013年にはその3倍の発電能力が見込まれている。すでに欧州でメンテナンス需要が高まってきているほか、設置場所などの問題から普及の遅れている国内においても、小型ではゼファーやループウイング、大型では三菱重工や日本製鋼所グループなど日本勢の奮闘で、発電能力も徐々に増えてきている。特に模索が始まった洋上発電においては、軸受の海水による耐食性向上、メンテナンス期間の延長など、要求性能は厳しさを増す。風力発電機の普及拡大を支える軸受の材料、表面改質、ユニット化、メンテナンスを含めたトータル面での技術のさらなる進化に期待したい。
第65回 太陽電池普及に向け、長寿命・高信頼性の材料・表面改質技術開発が加速
第65回 太陽電池普及に向け、長寿命・高信頼性の材料・表面改質技術開発が加速提供:シャープ 家庭などの太陽光発電の余剰分を電力会社がこれまでの2倍、1kWあたり48円(事務所や学校など非家庭用は同24円)で買い取る制度が、11月1日からスタートした。期間は買い取り開始から10年間。温室効果ガスの排出削減を進めるため、太陽光発電の普及を進めるねらいで、制度導入を当て込み太陽光パネルの購入者が急増、電機メーカーは増産体制に入っている。太陽光発電設備の価格は平均185万円程度(経済産業省調査)だが、経済産業省の試算では、国や自治体の設置補助を受けた場合、余剰電力を売った収入や電気代の節約効果を考えると約10年間で元が取れるとしている。
しかし、この試算には、故障に伴いメンテナンス費用を負担する場合が考慮されていないだろう。実際に太陽電池モジュールは配線材や封止材の破損、太陽電池セルと配線材の接触不良などによる故障が多いという。こうした故障を防ぎ、高信頼性・町寿命の太陽電池の実現をめざし、材料技術開発が進んでいる。
提供:三菱樹脂 太陽電池は太陽電池セルとそれを搭載するパネル材で構成されるが、パネル材の主要構成材料としてセルモジュールを封止する封止樹脂と、セルモジュールおよび封止樹脂を保護する保護フィルム(バックシート)がある。たとえばバックシートには屋外環境への耐性が求められ、PVF(ポリフッ化ビニル樹脂)フィルムやPET(ポリエチレンテレフタレート)フィルムが使われている。特に水蒸気の浸入によるセルの劣化を防ぐため耐加水分解性が求められ、PVFコスト競争力と供給力が高いが同性能で若干劣るPETフィルムでは、同性能を強化するコーティング加工などがなされている。アルミホイルをラミネートしたフィルムやシリカ(SiO2)を蒸着したフィルムなどがある。
最近開発が活発化している、軽量で設置の自由度が高いフレキシブルなフィルム太陽電池では、表面ガラスの代わりに透明シートが使用され、耐加水分解性を含め耐久性が特に求められる。耐久性の向上という点では、耐摩耗性に優れつつ、シリコンと同様の半導体特性を持つ炭素系材料、DLC(ダイヤモンドライクカーボン)を表面に被覆したフィルム太陽電池などの開発も進んできている(ナノテックなど)。
産業技術総合研究所の太陽光発電研究センターでは先ごろ、先述の太陽電池モジュールの不具合要因を明確化し、信頼性、長寿命の太陽電池モジュールの実現をめざし、化学メーカー、部材メーカーを中心とする民間企業31社と共同で、「高信頼性太陽電池モジュール開発・評価コンソーシアム」を発足した。三洋電機やシャープなどの太陽電池パネルメーカーが加盟する太陽光発電技術研究組合が連携機関として参画し意見交換を進め、現在の太陽電池モジュールの寿命は20年程度だが、2倍の40年をめざすとしている。
太陽電池のさらなる普及に向け、高信頼性、長寿命を実現する材料・表面改質などの技術開発の進展に期待したい。
第66回 建設機械の耐久性・環境対応を支える潤滑油技術の普及を!
第66回 建設機械の耐久性・環境対応を支える潤滑油技術の普及を!提供:コマツ 建設機械大手のコマツでは、2009年度中にインドネシアのアダロ鉱山で、ジャトロファから自社製造するバイオディーゼル燃料B20(軽油へのバイオディーゼル燃料の混合率20%)でダンプトラックを走らせるプロジェクトを始める。100台規模で稼動させる場合、年間8000tのバイオディーゼル燃料が使われ、CO2換算で約2万t(同社国内事業所の年間排出量の約10%に相当)の削減になるという。戸外で使われる建設機械には環境負荷低減が求められている。
さて、建設機械ではディーゼルエンジンを回して油圧ポンプを駆動し、油圧作動油をブームシリンダやアームシリンダ、バケットシリンダといったアクチュエータに送り、車体各部を作動させる。そのため建設機械においては、ディーゼルエンジンと言ってもトラック・バスのそれとは、油圧機器と言っても設備機械のそれとは違って、より高温・高荷重の運転を強いられる。つまりその高負荷運転に耐えつつ、環境対応を両立するエンジン・油圧機器の技術として、それら機械の血液である潤滑油の技術が活躍している。
ディーゼルエンジンの潤滑油(ディーゼルエンジン油)では2000年に、長期排出ガス規制に対応し、日本独自の要求を盛り込み日本のエンジンに適合した規格としてJAMA(日本自動車工業会)の提案により新しい動弁摩耗評価試験などを盛り込んだ「JASO DH-1」が誕生している。
提供:日立建機 ディーゼルエンジンを搭載している建設機械においても、一般にDH-1適合のエンジンオイルが推奨されている。しかし、建設機械ではディーゼルエンジンを回して油圧ポンプを駆動することで作動油に圧力を発生させ、コントロールバルブを介して作動油をブームシリンダやアームシリンダ、バケットシリンダ、旋回モータなどのアクチュエータに送り、圧力を力に変換することで車体各部を作動させる。そのため、バスやトラックのエンジンが数10%という負荷率なのに対し、建設機械のエンジンは実に80%という高負荷率に及ぶ。
提供:ジャパンエナジー このため、高負荷運転にさらされる建設機械の純正オイルとしては、DH-1規格に基づき、各種添加剤配合技術により、動弁系摩耗の防止やピストン清浄性の向上、酸化安定性向上によるロングライフ化などを実現、エンジン・油圧機器の寿命延長・トラブル抑制やエンジンオイル消費量・燃料費の低減などを実現している。先ごろジャパンエナジーがDH-1規格適合の建設機械用ディーゼルエンジン油を発売したが、これはトラック・バス用のDH-1油と建設機械用DH-1油は別物であるとのメッセージであろうか。
2005年に施行された新長期規制は、トラック・バスでPM(粒子状物質)が85%、NOX(窒素酸化物)が40%、HC(炭化水素)が80%削減されるという、世界一厳しい排出ガス規制と言われた。これに対しディーゼルエンジンでは、クールドEGR(排気ガス再循環装置)やコモンレール式燃料高圧噴射などエンジン自体の改良に加え、DPF(排出ガス後処理装置)などの装着が必要になり、JAMAとPAJ(石油連盟)では、耐摩耗性など耐久性能に関わる基本的な要求はDH-1規格と同様としつつ、排出ガスの後処理装置への適合性を高めたディーゼルエンジン油規格「JASO DH-2」を設定した。
提供:出光興産 DPFはPM捕捉フィルタを触媒により燃焼除去して再生するが、エンジン油中の金属系添加剤は燃焼できず堆積し、フィルタの目詰まりを引き起こす。また、NOX浄化触媒では、硫黄やリンが触媒寿命に対する劣化因子になる。そのため、DH-2規格では、これら後処理装置を劣化させないよう、金属分として硫酸灰分、硫黄、リンを減らす規定(ケミカルリミット)を盛り込んでいる。
建設機械のディーゼルエンジンにおいても近年、欧米を中心とするTier3規制や日本国内の建機指定制度・オン/オフロード第3次排出ガス規制など、NOX、PMなどの排出規制は厳しさを増しているが、これらに対してはEGRでの対応が主流でDPF搭載の必要がなかったことから、現状はDH-1規格適合油をベースとしたものが採用されている。
しかし、PMとNOXの両方を従来比で90%削減するといったTier4規制(2015年までに段階的に導入)に向けDPFの搭載が不可欠となる中、DH-2規格に適合したエンジン油をベースとする建設機械用エンジン油の開発が急がれている。ベースとする、というのは、金属系添加剤が果たす耐摩耗性や酸化安定性という建機に必要な耐久性能が劣るバス・トラック向けのDH-2規格油をそのまま建機に使用した場合、早期のオイル劣化やベアリング部(特にEGR部)の腐食・摩耗の増加、シリンダ、メタルの腐食・摩耗の増加が懸念されるためである。
そこで建設機械メーカーでのDH-2規格油への切り替えでは、エンジン各部の酸による損耗を防ぐアルカリ価の不足に対し強アルカリ分の添加剤を配合したり、非リン系摩耗防止剤を増量したり、酸化防止効果のある添加剤の使用量を増加するなど、添加剤技術の細かな積み上げで建設機械に必要な耐久性能を確保する対応を図っているのが現状のようだ。
一方、油圧システムと言っても、一般設備機械のそれと建機に搭載されるそれでは、使用条件の過酷さがまるで違う。設備機械では使用圧力7~21MPaが主流なのに対し、建機では需要の多い油圧ショベルとホイールローダがそれぞれ35MPa、42MPaと高圧で使われる。また前者の使用温度範囲が通常30~55℃程度なのに対し、建機では60~100℃と高圧・高温環境で稼動している。にもかかわらず、油圧作動油の需要の6割程度を占める建設機械において、使用条件に合致した作動油の品質規格は従来存在しなかった。
そこで、①建機の使用条件に合致し、油圧機器の寿命延長につながる品質規格②圧力35MPa、油温100℃の条件で建設機械に共通に使用可能な規格を目標に、世界的なシェアを誇る(油圧ショベルでは80%以上)日本の建機メーカーが主体となる日本建設機械化協会(JCMAS)において、建設機械用油圧作動油の共通規格化が進められ、2004年に「建設機械用油圧作動油 HK規格」と「建設機械用生分解油圧作動油 HKB規格」が定められた。
従来の耐摩耗性作動油には極圧剤兼酸化防止剤として、一般にZn(亜鉛)系の添加剤が使われているが、この添加剤は150℃以上で熱分解しやすく、また酸化防止剤としての役割を果たした後は不油溶性の物質(スラッジ)に替わるという性質がある。建設機械の高温・高圧下ではそれが一層加速されてスラッジの生成を早め、オイルフィルタの目詰まりや制御バルブの誤作動などのトラブルが発生しやすくなる。これに対し、たとえば高粘度指数(高VI)基油に油性剤とリン系摩耗防止剤を組み合わせた非Zn系の処方にすることで、高温・高圧下でのスラッジ発生を抑え、建設機械用作動油としての要求性能をクリアしている。
生分解性油圧作動油についても、HKB規格制定により、建設機械用としての要求性能が保たれてきている。植物油ベースの生分解性油圧作動油では、酸化安定性の不足から数百時間程度の寿命だったものが、合成エステル系ベースの生分解性油圧作動油では、高温・高圧下で1000時間程度の運転も可能になっている。とはいえ、生分解性油圧作動油では耐久性に関わる添加剤でも毒性のあるとされるものは一切使えないことから、どうしても一般作動油に比べ性能が劣り、欧州のような規制なしには普及が難しいと見られている。
JCMAオンファイル(提供:潤滑油協会) ディーゼルエンジン油規格DH-1およびDH-2、建設機械用油圧作動油規格HKおよびHKBはともに、規格に適合したオイルの品質確保と広く流通させるための届け出システム「オンファイルシステム」として運用され、規格適合作動油のグローバルでの入手性が向上し、粗悪作動油によるトラブルの回避が可能な環境にある。オンファイルシステム運用の円滑化と政策面での支援などにより、建設機械の稼動に合致したこれらのオイルの使用が進み、建築機械の環境対応、省エネ化、ロングライフ化が一層進むことに期待したい。
第67回 国際ロボット展に見るメカ技術
第67回 国際ロボット展に見るメカ技術kokoroのアクトロイド 日本ロボット工業会と日刊工業新聞社は11月25~28日、東京・有明の東京ビッグサイトで、国内外の産業用・民生用ロボットと関連機器を一堂に集めた「2009国際ロボット展」を開催した。今回のテーマは「RT 次代への挑戦-Challenge for the next-」で、開催規模はIR(産業用ロボット)やSR(サービスロボット)、RT(ロボットテクノロジー)などのメーカーおよび大学・研究機関など、192社64団体856小間。
ファナック「ゲンコツロボット」 産業用ロボットの課題として、わが国生産拠点の海外流出に歯止めをかける生産性の向上、つまり加工・組立て作業の自動化率の向上が挙げられる。こうした点で今回注目を集めたのが、パラレルリンク機構を採用した小型組立てロボット「ゲンコツロボット」だろう。4軸タイプは手首軸の先端回転軸は、3000°/secの高速回転動作が可能で、掴んだ部品の向きを瞬時に切り替えることで、部品の整列や実装を高速に行う。6軸タイプ(手首複合3軸)は、3軸手首を持つ6自由度構造を実現、つかんだ部品の向きを変えたり、斜めに挿入したり、捻りを加えたりといった複雑な動きが可能になっている。
回転ジョイントとリンクにより機械を駆動するパラレルリンク機構の6軸加工機は国内でも1990年代後半に各社で上市されたが、(1)その構造から重力による変形の影響を受けやすく、特に稼動域の端近くで駆動する場合に送り駆動系と比べ運動精度は大きく劣る、(2)シリアル機構工作機械に比べ切削力などの外乱に対する剛性が小さいなどの理由から、現在一般の工場で稼動しているパラレル機構工作機械は極めて少ない。
これに対しゲンコツロボットでは、人間の手の動作と同じ柔軟な動作を行うことが可能で、携帯電話のように微細で複雑な電子部品から構成される機器の組立てにも柔軟に対応できるとしており、パラレルリンク機構の利点がロボットでは生かされそうである。
THKローラリテーナ入り直動案内 もちろん複雑な動きを必要とする作業ばかりではなく、単軸ロボットが活躍している場面は多い。ここでは作業性向上のため高速性や高精度のほかメンテナンスフリーといった要素も重要である。THKでは、ボール(およびローラー)リテーナ入りの直動案内とボールリテーナ入りのボールねじを組み合わせた電動アクチュエータなどを出展した。リテーナ(保持器)を組み入れたことで、ボールとボールとの接触を避け、低摩擦化による高速性や、摩耗の低減による高精度化や長寿命化などを可能にしている。
また、自動車の組立工場などで主流の多関節ロボットでは関節部分の回転速度とトルクのコントロールに減速機が用いられている。ナブテスコでは小型、軽量ながら剛性に優れ、過負荷に強いのが特長。このため加速性能がよく、滑らかな動き、正確な位置決め精度が得られ、ロボットの制御性を格段に向上させることができるコンポーネントタイプの精密減速機やそれをベースにして、サーボモーターと簡単に取り付けができグリースを密閉したギヤヘッドタイプ精密減速機などを出展した。
日本トムソンのクロスローラベアリング また、その関節部にはラジアル荷重、アキシアル荷重、モーメント荷重などの複雑な荷重がかかる。これに対し日本トムソンでは、これらの荷重をひとつの軸受で受けるべく、円筒ころを直交に配したクロスローラベアリングなどを展示した。
一方、介護や福祉など重労働や地雷処理など危険な作業を担うサービスロボットは、人間と強調して動く場面が多い。そこでISO13849のパフォーマンスレベルeと呼ばれる高い安全基準への合致も求められる。つまり人間をサポートするメカ技術のほか、人間に危害を加えることを避けるセンシング技術が求められる。日本精工「ヒューマンアシストガイダンスロボット」
二つのセンサ技術を応用した日本精工の階段認識昇降ロボット これに対し日本精工では、平地や傾斜面、多少の凹凸面での移動が可能な車輪型移動ロボットで、グリップを介して人の行きたい方向を察知し、進路上にある障害物を自律認識して回避しながら進むヒューマンアシストガイダンスロボットを展示した。また、これをサポートするため、不意の障害物に対する緊急回避を可能にするセンサ技術として近接覚センサ技術を、進路の状態を把握するセンサ技術としてリアルタイム円錐走査センサ技術を出展した。わが国の視覚障害者は約30万人で盲導犬を使いたい人が約1万2,500人いるのに対し、盲導犬の数は現在約1,000頭しかいない。日本精工ではこの技術を将来的に、車椅子、盲導犬や介護犬の代用などへの応用が可能な、人間をアシストする自律移動ロボットへとつなげたい考えだ。
THK参考出品のロボットハンド そのほかTHKがボールねじ+リンク機構をを応用したロボットハンドを出展するなど、今回の国際ロボット展の出展では、メーカーが新規なロボットおよび要素技術を披露して来場者から適用の可能性を探ろうという意味合いも多かったようにうかがえる。わが国の生産力を向上させ、また人間をアシスト・サポートするロボット技術の今後の進展に期待したい。
第68回 セミコン・ジャパン2009、半導体関連分野に対応するメカ技術
第68回 セミコン・ジャパン2009、半導体関連分野に対応するメカ技術 半導体を中心とするマイクロエレクトロニクスの製造を支える装置・材料産業の総合イベント「セミコン・ジャパン2009」が12月2日~4日、千葉市の幕張メッセで開催された。同展では、LEDや太陽光発電などの需要拡大に合わせ回復基調にあり、さらに市場を広げつつある半導体分野で求められる高集積化、小型、高速、低消費電力、低コスト化のニーズに対して、露光装置から材料、加工技術、計測評価技術など、多くのソリューションが示された。
ArF液浸スキャナー(提供:ニコン) ICの高集積化とは電子回路パターンの線幅を微細化することで、現在は線幅32nm、22nmのプロセス確立に向け、特に前工程の中でもIC製造の中核技術である露光装置(ステッパー)の開発が激化している。露光装置最大手のオランダASMLは、真空紫外光の193nmより一桁以上短い13.5nmの極紫外線(EUV)を用い解像力を大幅向上するEUVリソグラフィを採用した装置で、ニコンはフッ化アルゴンエキシマレーザー(ArF)を使いレンズとウェハーの間を液体で満たすことで、従来と同じ露光波長を使いながら解像度を高める液浸リソグラフィーで2回露光(ダブルパターニング)を採用した装置で高集積化に臨む。
ステッパーで、レチクルのパターンを投影するレンズは1/4の縮小倍率では、レチクルステージはウェハーステージの4倍の速度でスキャン動作を行い、ウェハー上に微細なパターンを焼き付けていく。ステッパーでは1時間あたりに処理できるウェハー枚数をいう「スループット」の向上が課題であり、レチクルステージには露光を開始する位置に高速に移動し、高精度に位置決めする必要がある。
従来このステージには、サーボモータ+ボールねじ駆動と転がりの直線案内を組み合わせた機構が採用されていた。しかし、露光中の位置決め精度の誤差平均値は線幅の1/10以下とも言われ、現在の45nmプロセスではそうした接触機構の摩擦による振動などから、要求される位置決め精度、スキャン速度への対応が難しくなっていた。そこで現在はリニアモータ駆動として、エアで浮上させ非接触としたエアベアリング案内のステージが主流となっている。このステージを使ったステッパーでは、1時間あたり200枚といったスループットが実現されている。
腐食環境対応耐食組合わせセラミック軸受(提供:ジェイテクト) また、ウェハーでは配線前のベアシリコンおよび配線後のデバイスウェハーで平坦化CMP(ケミカル・メカニカル・ポリッシング)処理が行われ、高容量化のための多層配線がなされるが、この研磨および研磨後の洗浄工程では回転機構に使われる軸受がCMPスラリーや洗浄液などにさらされる。このためこうした箇所では、軸受鋼に比べ腐食に強いステンレス軸受や、さらには窒化ケイ素などのセラミック軸受が活躍している。クリーン環境の保持から、また潤滑剤が機能しない環境であることなどから、固体潤滑としてPTFEの保持器を使うなどの工夫がなされた軸受製品も展示された。
電着ダイヤモンドワイヤ(提供:旭ダイヤモンド工業) 加工技術では、シリコンウェハーの切断のほか、LEDの基板となるサファイヤの切断として有効な、電着ダイヤモンドワイヤなども出展、注目を集めた。
2020年に2009年比10兆円増の31兆円市場になるという半導体産業だが、さらに2020年に20兆円市場が見込まれるLED、同じく5兆円市場が見込まれる太陽電池など、半導体市場を押し上げる要因は多い。電気自動車の航続距離を延ばすキーテクノロジーとなるSiC(炭化ケイ素)パワー半導体などでは加工の効率化などが問題となっている。こうした課題を解決し半導体の市場をさらに拡大させる、メカ技術の発展に期待したい。
第69回 わが国洋上風力発電の実用化に向けて
第69回 わが国洋上風力発電の実用化に向けて提供:戸田建設
戸田建設は先ごろ、京都大学、佐世保重工業、日本ヒュームと共同で、長崎県佐世保市において、世界で初めて、鋼・プレキャスト(PC)コンクリートのハイブリッドスパー(けた)構造による、浮体式洋上風力発電施設用プラットフォームを開発、全長125m、出力2,000kWの実用化に向け、全長12.5mの1/10モデルの実海域実験で有効性を確認した。自力で浮く構造のため、水深50m程度の比較的浅い海域から100m以深の海域まで、広い海域で対応可能な形式が有効なほか、PC部材のプレキャスト化と造船所のドックの活用により、既存施設で短期間での建造が可能で、大型クレーン船が要らず、建造後の曳航、設置が短期間で済むこと、繋留位置の変更により移設が比較的容易なため、設置箇所の経年的な風況変化やエネルギー需要に変化生じた場合でも、柔軟に対応できるという。
風力発電機の設置が世界的に進む中、わが国では、陸地における風力発電の適地が減少傾向にあり、比較的風況の良い山岳部でもアクセス道路の整備などのコスト負担が増加しているため、世界第6位の排他的経済水域を保有する海洋国家としての立地と、洋上が陸上に比べ風況が3割良好とも言われることから、洋上風力発電の実現が期待されている。しかし水深が10m未満の遠浅海域が広い欧州では着床式の洋上風力発電の実績が多い一方、日本は遠浅の海域が少なく海底が複雑な地形をなしていることなどから、水深の影響を受けにくい浮体式洋上風力発電施設の実現が求められている。大水深域まで含めると、洋上発電でわが国のエネルギー需要をほぼ賄えるとの文部科学省の試算もあり、わが国初の浮上式風力発電技術への期待は大きい。
ところで欧州の着床式洋上風力発電では通常、タワーエレベーターを配置し管理と作業のためのヘリポート、クレーン、スカイクライマーを設置しブレードの調査や補修用に遠隔監視操作を行っている。軸受などのメンテナンスではヘリコプターを出動、地上100m程度のヘリポートに長さ60mくらいのブレードを避けながらヘリポートに着陸し、2~3名の保守要員が2~3日がかりで作業を行い、その費用は数百万円に及ぶという。そのため、風力発電機のメンテナンス期間延長に貢献するメカ技術が強く求められている。
組合わせセラミック軸受(提供:ジェイテクト) 風力発電機用軸受は特に、ジェネレータに用いる軸受で電食による損傷が発生しやすく、故障の原因の一つとなっている。そのため絶縁機能により電食を防止しまた塩水腐食にも耐え軸受の耐久信頼性を高める、軌道輪に非磁性ステンレス鋼、玉に窒化けい素セラミックス、保持器に固体潤滑であるフッ素系樹脂を用いた組合わせセラミック軸受などが採用されている。ジェネレータ用軸受は氷点下から約60℃の温度環境下、回転速度2,700min-1、グリース潤滑下で稼動しているが、組合わせセラミック軸受により、同社一般軸受に比べ約3倍のグリース寿命を延長しているという。
そのほか増速機ギヤで、鉱油系潤滑油剤に比べ広範な温度領域、高荷重下などで長期にわたり優れた潤滑性能を発揮する合成油ポリアルファオレフィン(PAO)をベースオイルに使ったギヤ油などの開発も進み、メンテナンス期間の延長に貢献してきている。
浮体式洋上風力発電システムではメンテナンスが着床式に比べ容易になると思われるが、洋上風力発電で避けられない電食や塩水腐食を防止する先述のようなメカ技術は、必要不可欠だろう。わが国洋上風力発電の実用化、設置促進を後押しする機械技術の進展に期待したい。
第70回 環境分野を核に、成長市場でのビジネス展開が加速
第70回 環境分野を核に、成長市場でのビジネス展開が加速デンマーク大使館提供 コペンハーゲンで開催されていた国連気候変動枠組み条約締約国会議(COP15)は、最大の焦点だった2020年までの各国の削減目標の義務付けが盛り込まれないまま、19日に閉幕となったが、新興国も含めた主要国のCO2排出削減に向けた枠組み作りへの取組みは確実に始動している。新興国を中心とする成長市場での環境保全に根ざした需要の取込みに向け、潤滑、軸受など機械を支える要素技術メーカーの現地での研究開発、生産、販売が活発化してきている。
出光興産は先ごろ、ブラジルのサンパウロに潤滑油販売子会社を設立、2010年1月1日から営業を開始する。南米地域の中核であるブラジルは、2007年度のオートバイ生産台数が世界4位となる170万台、自動車生産台数は2008年度で世界6位の320万台に達しているほか、2010年~2014年までの国内総生産は、米ドルベースで年率5.6~16.4%の伸長が見込まれている。現在、ブラジルの潤滑油需要は日本の約7割にあたる140万kLだが、今後環境性能を有した自動車用潤滑油、CO2冷媒を用いた冷凍機用潤滑油など高機能潤滑油の需要が大きく成長すると見込んで、新会社設立を決めた。ブラジルをはじめアルゼンチン、ペルー、チリなど南米諸国での販売を強化、2015年には売上高21億円をめざすという。
NTNでは早くから、新興市場向けの低価格車用等速ジョイント(CVJ)、CVJとハブベアリングで構成されるモジュール部品であるハブジョイントの商品群を開発しているが、2011年からブラジルの日系自動車メーカー向けにハブベアリングの量産に乗り出す。傘下のSNR社のブラジル工場で製造・供給する。将来的にはCVJの現地生産も検討するという。
日本精工では、2013年3月期までに新興国で拠点を整備する。同期の中国での売上高を、2009年3月期比75%増の1,000億円と見込むほか、2009年3月期に約1,300億円だった新興国での売上高を2013年3月期には約2,300億円とする計画。生産・販売拠点の整備・拡大のほか、中国に続きインドにも研究開発機能を持たせていく。成長市場での生産が進む中、現地生産した製品の評価から、将来的には市場ニーズに合わせた製品・技術の研究開発期間を早める狙いだ。
中国で家電向けなどの受注が好調なミネベアは、現地調達率を上げ生産体制を整える。同社では中国で厳しさを増す排水処理規制に先行して完全クローズド水処理設備(排水再利用装置)を導入、政策的に現地生産を円滑化させつつある。
ジェイテクトは先ごろ13機種の工作機械を発売したが、ここにも成長市場への対応がうかがえる。鉄道車両の車軸の加工に適した複合研削盤は高速鉄道の整備が進む中国やブラジルなどで販促を進めるという。
各社の拠点整備・拡充や製品・技術の投入は、自動車では新興国の旺盛な需要に対して、産業用ではクリーンエネルギーとして需要拡大が見込まれる風力発電に対して、主に進められている。特に風力発電市場はメンテナンス需要も含め新規ビジネスとして期待がかかる。
機械の稼動を円滑にする要素技術・製品の開発を促進し、それらをグローバルに普及させていくことで、わが国の景気復興を後押しするとともに、財政支援だけでなく技術的なサポートにより、新興国の地球温暖化防止の活動強化へとつなげてほしい。
第071回~第080回
第071回~第080回第71回 省エネ、創エネシステム躍進に機械技術の飛躍を願う
第71回 省エネ、創エネシステム躍進に機械技術の飛躍を願うフィルム太陽電池(提供:産業技術総合研究所) 今年は家庭用を中心に省エネ、創エネのシステムが普及、拡大した。省エネといえば従来の照明に対し6~7割消費電力を節減できるというLED(発光ダイオード)照明の販売競争が活発化した。創エネというと、家庭用ヒートポンプ式給湯器や家庭用燃料電池、何より新買取制度で需要が急増している太陽光発電などであろうか。こうした新エネルギーシステムにおいてメカの活躍の場が大きいことは本欄で何度か触れた。
LEDについては今後取り上げることになろうが、たとえば基板材料となるサファイアは難削材のため、ダイヤモンド粒子を表面に固定したピアノ線ワイヤーで切断する。従来の研削液を使ってワイヤーで切断する方法に比べ3~5倍加工能率が高いという。
ヒートポンプは本欄第47回で触れたとおり、熱交換器に大気中の熱を取り込み、地球温暖化係数が極めて低い冷媒のCO2を膨張させて大気中の熱を吸収、その熱をコンプレッサーで圧縮してさらに高温にし、高温になった熱をタンクユニットの水に伝えてお湯にする。CO2は高圧側で10MPa以上と動作圧力が高く、フロン冷媒と異なり摺動面に塩化物やフッ化物などの冷媒による固体潤滑膜を形成しないため、圧縮機内部の摺動部では摩耗量の増加が懸念される。あるロータリー圧縮機では、負荷される荷重が大きく接触応力が高くなるベーン先端とローリングピストン外周部の摩耗量増加をする抑制するため、ベーンに対し優れた摺動特性を持つDLC-Si(シリコンを含有させたダイヤモンドライクカーボン)が適用されている。
太陽光発電ではやはりシリコンウェハーを薄く切断するのにダイヤモンド砥粒付きワイヤーソーが使われ加工能率を高めているほか、第17回で紹介したような積極的に太陽光を追いかけ発電効率を高める太陽光追尾式発電システムでは、対応の動きに合わせてモーターを駆動、精密減速機でパネルの角度を調整し、常にパネルに光を集める。さらに軽量で設置の自由度が高いフレキシブルなフィルム太陽電池として印刷技術を使った塗布変換型有機対応電池(三菱化学)のほか、耐久性(耐摩耗性)に優れつつ、シリコンと同様の半導体特性を持つ炭素系材料、DLC(ダイヤモンドライクカーボン)を表面に被覆したフィルム太陽電池などの開発も進んできている。この量産においては、第62回で紹介した、ロール・ツー・ロールでフィルムなどの柔軟・長尺媒体「ウェブ」を搬送し、途中処理工程を経て最終的に巻き取るウェブハンドリング技術も、安価に信頼性の高いシステムとして開発が進められていくであろう。
この太陽電池は元来わが国が得意とする技術だったが国を挙げての取組みが先行したドイツに抜かれる形となった。しかし、市場が活発化した現在、従来のような太陽電池メーカーのみが争う市場ではなく、材料や表面改質、加工、ロール・ツー・ロールも含めた製造装置、評価装置など周辺技術を含めた市場の広がりを見せている。
このように、省エネ・創エネ技術の進展とともに、活躍の場を広げている機械技術のさらなる発展に、来年も引き続き期待したい。
第72回 新成長戦略の早期実行に向け技術開発の促進を
第72回 新成長戦略の早期実行に向け技術開発の促進をプラグインハイブリッド車(提供:トヨタ自動車) 政府は先ごろ、「新成長戦略(基本方針)~輝きのある未来へ~」を策定、経済産業省として成長戦略を速やかに実行に移す観点から、戦略分野ごとに、予算、法律、税制など、今年度および来年度に着手すべき施策を「早期実行プロジェクト25」として取りまとめた。わが国の強みの発揮として「環境・エネルギー」と「健康(医療・介護)」を、フロンティアの開拓として「観光・地域活性化」と「アジア経済戦略」を、成長を支えるプラットフォームとして「科学・技術」と「雇用・人材」を主要な戦略分野として位置づけて需要を創出、GDP成長率で名目3%、実質2%を上回る成長(2020年度までの平均)、名目GDPで2009年度473兆円(見込み)から2020年度650兆円程度への拡大、失業率で3%台への低下(中期的)を目指す。
ここで、環境・エネルギーでは、太陽光発電システムやパワー半導体、高効率照明としてのLEDなどグリーンイノベーションの集中的研究開発投資と事業化促進や、エコカーやエコ住宅などの推進などを挙げ、医療ではがんの超早期診断・治療機器の総合研究開発の推進などを挙げている。
これまで本欄で取り上げたように、太陽光発電ではより発電効率を高めるための太陽光追尾システムなどが、太陽光パネル基板やLED基板などの加工ではダイヤモンド砥粒電着のワイヤソーシステムなどが、エコカーとしてハイブリッドカーでは燃費向上を図る小型・軽量の駆動モーターや発電機構での小型化による出力低下を補う高速回転化などが、がんの早期診断につながるCTスキャンではX線管を搭載したガントリの回転数向上などが、その先端の治療システムとしてはアクチュエータ・ロボットによる遠隔手術などが、研究開発すべきメカ技術として注目されてこよう。
こうした新技術を普及する上で、すでにエコカー減税の6ヶ月間延長という税制措置が決まったが、特にわが国医療分野での問題として新技術の普及を阻害している法律の側面にも着手しようという今回の取り組みへの政府の力強い姿勢に期待しつつ、予断を許さない経済環境ながら産業界の新技術開発への継続・強化を求めたい。
第73回 エコシップを支える材料・部品開発を促進
第73回 エコシップを支える材料・部品開発を促進提供:商船三井 造船各社や海運各社で、国際海事機関(IMO)が検討を進めている国際海運(外洋船)の二酸化炭素(CO2)と窒素酸化物(NOx)の排出削減を図るエコシップの開発・導入が進んでいる。
三菱重工業では日本郵船などと共同で、プラントや重量物などの大型設備を運ぶモジュール船について、送風機で送られた空気により船の前方から細かい気泡を噴き出して船底を覆い、航行時の船体と海水との摩擦を減らす「空気潤滑システム」を開発、高効率プロペラなど省エネ装置も採用し、同型船と比べて約10%燃費が向上燃料となる重油の消費を節約し、CO2の排出量も削減できる。
同社ではまた、三洋電機と商船三井と共同で、太陽電池とリチウムイオン電池とを組み合わせたシステムで、船舶におけるCO2排出量の削減を目指す取組み(船舶SES)を進めている。太陽電池(最大200kW予定)とリチウムイオン電池(最大3,000kWh予定)とを組み合わせたシステムで、従来船舶に搭載されているディーゼル発電機とのハイブリッドで電力供給を行い、船舶全体から排出されるCO2を削減する技術の確立を目指す。太陽電池パネルで創り、二次電池に蓄えられた電力は、主に停泊中に使用される。停泊中のディーゼル発電機を停止することで、ゼロエミッション化に寄与すると見られている。本システムを装備した「ハイブリッド自動車船」は2012年の竣工を予定している。
IHIの子会社の新潟原動機では、IMOが現行のNOx規制に対し15~22%のNOx削減を義務付けている次期NOx規制に対応した巡視船用高速ディーゼルエンジンを開発している。強度、延性に優れたダクタイル鋳鉄の使用、吸気室の一体化やアルミ合金などの軽合金部品の多用により、高剛性で小型・軽量化を図っている。高効率過給機を装備したほか、直接噴射式を採用して燃焼系統を最適化、高出力、低燃料消費を達成した
IMOの調査では国際物流の9割を担う外洋船のCO2排出量は全世界の約3割に相当する8.7tで、これはドイツ1国分のCO2排出量に相当するという(2007年度調べ)。こうしたことから国際海運船に環境税を課金してCO2削減につなげようという提案も出ている。外航船ではどの国の排出量として換算するかという課題もあり、エコシップの建造・運航が今後促進すると見られている。海運・造船主要国であるわが国のエコシップ開発が進み、上述のとおり、軽量・高剛性の材料や燃焼の高効率化を図るエンジン部品、太陽電池や風力などのハイブリッド化にともなうシステム部品など、船舶の省エネ化を支える材料・部品の市場が拡大していくことに期待したい。
第74回 原子力発電所の建設加速で求められる軸受の信頼性
第74回 原子力発電所の建設加速で求められる軸受の信頼性提供:木村洋行
提供:東京電力 発電段階でCO2をまったく排出しないで大量の電力を安定して供給できる原子力発電のプラント建設が進んできている。ロシアが2030年までに国内で20基超の建設を計画しているほか、米国でも同年までに約30基の建設を予定している。国産炉政策を進める中国のほかプルサーマル発電の導入が進むわが国など、世界で53基の建設が進み、141基が計画されている(世界原子力協会発表)。
さて、原子力発電はウラン燃料を燃やして熱エネルギーを得て、水を沸かし蒸気の力でガスタービンを回転させて発電する仕組み。世界で稼働する原子力発電所の約6割がPWR(加圧水型炉)、約2割がBWR(沸騰水型炉)を占める。いずれの方式でも原子力で電気を安定して作るには、原子力発電用タービンが安定して高速回転を実現することが求められ、その回転を支える軸受の信頼性がますます要求されてきている。
タービン発電機は軸方向に長く、軸を水平に寝かせたものが9割を占める。このタービンの回転軸(ローター)の荷重と回転を支えるジャーナル軸受としては、軸受すき間内に発生した潤滑油膜で荷重を支持するすべり軸受(油膜軸受)が使われている。この油膜軸受では特に潤滑管理技術が、軸受の信頼性向上、ひいては原発の安全な稼働をささえている。
地震などにより潤滑油の軸受への供給に不具合が起こると、巨大な荷重を支えている軸受油膜の形成が保たれないと軸受の摩耗、ついには損傷に至ることがある。そこで供給される潤滑油の圧力を、一定に制御する応答性の高い自力式の「潤滑油圧力調整弁」などが適用され、軸受油膜の形成を確保しているが、軸受技術としては潤滑油を効率的に供給し保持するためのグルーブを形成するといった方法がとられる。代表的なキングスベリーLEG(Leading Edge Groove)ベアリングをみると、低温の潤滑油を直接パット表面に送り込むため、パットの表面温度を効率的に下げるとともに、給油量の低減と排油効果によって軸受内の攪拌ロスを最小限に抑えている。
一方で、1000℃近い高温の熱を利用して50%以上という発電効率を実現する「高温ガス炉」ガスタービン発電システムでは、ターボ圧縮機および発電機の軸はHe ガス雰囲気内で使用するために、水や油などの液体潤滑剤を必要としない無潤滑の磁気軸受で支持することになる。しかしこれまで実績のある最大級の磁気軸受支持ロータは質量が35tで、回転数が600rpmの低速回転ロータだった。高温ガス炉ガスタービン発電システム(GTHTR300)では、使用するターボ圧縮機ロータおよび発電機ロータは質量がそれぞれ46t、 67t と重く、定格回転数が3,600rpmの高速回転機のため、軸受負荷容量および回転数が高い高速・高剛性の磁気軸受設計が検討された。
原子力発電はCO2を排出しない発電機構として需要が増えてきているが、過去の事故などから稼働率が60%と低迷するわが国で周辺住民の理解を得て発電所建設が本格化するには、さらなる安全性、安定運転の裏付けが何よりも求められよう。今回取り上げた軸受技術のほか、原子炉制御棒の駆動機構、再循環ポンプ、タービン鍛造翼、発電機のギヤや軸受など、原発の安全性を高めるメカ技術の信頼性向上への期待はますます高まってきている。
第75回 トヨタのリコールに学ぶ、グローバル展開での安全性確保を!
第75回 トヨタのリコールに学ぶ、グローバル展開での安全性確保を! トヨタ自動車が米国でアクセルペダルの不具合による約230万台のリコール(無償の回収・修理)を発表、「カローラ」や「カムリ」など8車種の生産・販売を一時中止した。リコールの台数は世界で約460万台に上ると見られ、業績を回復しつつある自動車業界に影を落としている。
不具合は二つで、一つはアクセルペダルの先端部分がマット表面のくぼみに引っかかり戻らなくなる恐れがあるというもので、トヨタでは薄いマットに交換し、アクセルペダルの長さを短くする措置を取った。もう一つは、アクセルペダルの戻り具合を調整する「フリクションレバー」の表面が使用で摩耗し、そこに暖房の熱が流れ込んで結露すると、調整機能が働きにくくなり、ペダルの戻りが遅くなったり、戻らなくなったりする可能性があるというもの。「レクサス」が暴走してクラッシュ事故を引き起こしたことなどから、北米での批判が高まった。
中央は円盤状のスロットルバルブ
矢印部分がスロットルレバー 車の速度調整はドライバーがアクセルペダルを操作することで吸気量を変化させて行う。ワイヤー式ではアクセルを踏み込みアクセルワイヤーが引っ張られるとスロットルレバー(報告のあったフリクションレバーであろう)の回転軸が回り、それと同軸のスロットルバルブが回転して開かれ吸気量が増大し速度が上がっていく。アクセルを戻すとリターンスプリングによってスロットルレバーの回転が戻り、スロットルバルブが閉じて吸気量が減り速度が下がっていく。今回の不具合は、このスロットルレバーの摩耗した部分に結露がたまったことで、すべりが生じ戻りの回転が正常に行われなかったということであろう。いずれにしても十分な調査と公正な報告を待ちたい。
今回不具合を起こしたのは米国部品メーカーCTS社製のフリクションレバーだったが、トヨタをはじめ現地生産では多くの部品を現地調達に頼らなければならない。特にこれからの新興国の市場開拓の上では、自動車部品メーカーも含め、現地でのビジネスの円滑化、またコスト低減から、現地の材料や部品を調達し生産を進めるシステム作りが必要となってくる。そうした低コスト化に対応した上で、製品の信頼性を確保しなければならない。今回のリコールを教訓に、現地での材料や部品の信頼性を評価し、安全性向上につながる製品性能を確保する体制作りに努めてほしい。
第76回 相次ぐクルマの安全神話崩壊に、品質管理の徹底を!
第76回 相次ぐクルマの安全神話崩壊に、品質管理の徹底を! トヨタ自動車が、米国でアクセルペダルの不具合に関してカローラなど8車種でリコール(回収・無償修理)を実施したのに続き、ハイブリッド車「新型プリウス」でブレーキが瞬間的に利かなくなるという苦情が国内外で出ている。
アクセルペダルの不具合は、アクセルペダル内部のフリクションレバー部が摩耗した状態で、低温時にヒーターをかけることなどで当該部分が結露すると、最悪の場合、アクセルペダルがゆっくり戻る、または戻らないという現象であることは本欄で前回報告した。トヨタでは米国時間1月21日にリコールを行うことを決定、アクセルペダル内部にスチール製の強化板を挟み、これによりアクセルペダルの不具合の原因となるフリクションレバー部とペダルアーム部の接点に隙間を設けるとともに、ペダルの戻る力となるバネの反力を強化する改善措置を施すことを決めた。
今回の、プリウスのブレーキの不具合は低速で滑りやすい路面などを走行中に、一時的にブレーキが利かなくなるというもの。ブレーキを軽く踏んだ状態でABS(アンチロック・ブレーキ・システム)が作動すると油圧ブレーキの利きが遅れる可能性があるという、ABSの制御ソフトの問題としている。ABSは車輪速センサが車輪のロックを検知すると、ペダルのブレーキ圧を自動的に少し抜くことで車輪のロックを防ぎ、高い制動力とステアリング操作を両立させる。
プリウス回生ブレーキシステム プリウスでは、エンジンブレーキ時やフットブレーキによる制動時には、モーターを発電機として作動させることにより、車両の運動エネルギーを電気エネルギーに変換してバッテリーに回収し、再利用する「回生ブレーキシステム」を採用している。特に加減速を繰り返す走行パターンでエネルギー回収の効果が高く、フットブレーキ時にはECB(電子制御ブレーキシステム)の油圧ブレーキと回生ブレーキを協調制御して回生ブレーキを優先的に使用し、より低い車速までエネルギー回収を行っている。このコンピュータ制御の問題ではないかということだ。
2月5日に開かれた記者会見で豊田章男社長は、社長をヘッドとする委員会により、(1)今回のリコールに至った要因を検証しながら、「設計品質」、「製造品質」、「販売品質」、「サービス品質」の全工程において、再度間違いがなかったか点検を実施する、(2)各地域でのユーザーからの情報収集と現地現物を充実すべく、技術分室を増強する(3)品質管理のプロを育成すべく主要地域において「品質教育機能」拠点を設置する、などの取組みを行うことを明言した。
車輪がロックした状態で思い切りブレーキを踏むとクルマの姿勢が乱れ、最悪の場合はスピンしてしまう。ABSはそうした事態を未然に防ぐ安全装備の代表格だ。今回の苦情は、そのシステムが瞬時にせよ逆にブレーキ性能を脅かす可能性があることを突きつけた。アクセルペダルの不具合に続く、わが国自動車産業の景況を好転させつつあるエコカーの代名詞である「プリウス」でのブレーキの不具合。世界に誇る日本車の安全神話を揺るがすこの一大事に対し、豊田社長の明言したような自動車各社の品質管理がグローバルに徹底されることに期待したい
第77回 新幹線事故に保全管理の徹底を望む
第77回 新幹線事故に保全管理の徹底を望む提供:JR東海 東海道新幹線で架線が切れて停電し、東京-新大阪間全区間で運転を見合わせ、約15万人の足に影響が出た事故が、実はパンタグラフ部分のボルト付け忘れが原因だった。架線に触れる長さ1,9mの舟体とこれを支えるアーム部分をステンレス製ボルト4本で固定する構造だが、今回壊れた1基はボルトが4本とも付いていなかった。車両基地で摩耗した舟体を交換する際にボルトを付け忘れたという、何ともお粗末な事件だった。
さて、パンタグラフにおいて電気は、架線→すり板→舟体(集電舟)→上枠→下枠→台枠→車両の主回路に流れる。架線、特にパンタグラフが擦れて電気を流すトロリ線には、列車の走行に十分な大きさの電流を流すという電気的特性のほか、パンタグラフとの接触力変動が少ない良好な接触を保つための機械的特性、摩耗しにくく破断することのない材料的特性をバランスよく備えるよう、銅心に銅被覆して強度を高めたCSトロリ線などが開発・適用されている。
一方、パンタグラフにも同様の電気的特性、機械的特性のほか、すり板が摩耗しにくく破損せずトロリ線を摩耗させない材料的特性、風を受けることで発生する揚力(上に浮き上がる力)が適切で、風を切ることによる騒音が小さいなどの空力的特性が求められ、これに対応した新幹線用シングルアーム形パンタグラフが開発されている。前述のトロリ線と直接、高速で摺動する「すり板」では、摩擦特性に優れるカーボンに金属を含浸またはカーボンと金属を混合して焼結する方法でカーボンの摩擦特性に機械的強度の向上と電気的抵抗率の低減が図られたカーボン系すり板が開発、適用されている。
こうした高速走行での長期耐久性を持たせたパンタフラフとトロリ線を設計・開発する上で、ボルトの付け忘れという単純ミスにより、アームが跳ね上がり高圧電流の流れる補助吊架線が切れると異常事態は想定外だろう。トヨタ自動車のリコール事故など、団塊世代の技術者が抜けたことで想定外の事故が表面化してきているのでは、とも言われるが、それ以前の問題だ。関係者にあっては、1964年の開業以来高速性と安全性を実現し、海外に輸出されつつある新幹線の技術も、大量輸送の安全性を守る点検・保全作業の徹底で支えられているということを再確認する必要があろう。
第78回 HDD需要拡大で求められる機械部品・材料開発
第78回 HDD需要拡大で求められる機械部品・材料開発提供:日立グローバルストレージテクノロジーズ HDD(ハードディスク駆動装置)の需要が拡大している。パソコン向けのほか、カーナビゲーションシステムの車載器、HDDレコーダーなど向けなどが増えているうえ、ウインドウズ7の発売を機に、米国や中国などで低価格パソコンの発売が急拡大した。ノートパソコンだけでなく、当初SSD(メモリー媒体の記録装置:ソリッド・ステート・ドライブ)の搭載が進むと見られていたネットブックでも記憶容量あたりのコスト優位性からHDDが主流を占めるなど、その世界需要は2010年度で前年度比11%増の6億2,000万台と見込まれている。
HDDの機構系としては、記録媒体であるディスク、それを回転させるスピンドルモータ、記録再生を行う磁気ヘッド、それを支えるサスペンション、ヘッドの位置決めを行うボイスコイルモータなどがあり、これらHDD部品では日本メーカーのシェアが高い。スピンドルモータでは世界シェア7割強の日本電産やミネベアなど日本勢が全量供給している。ディスク(HD)は世界シェア25%の昭和電工や富士電機デバイステクノロジー、HOYAが、ヘッドは世界シェア3割強のTDKが、サスペンションは世界シェア4割のニッパツが手がけるといった具合だ。HDDの需要拡大はこれら部品を手がけるメーカーの生産をフル稼働させているが、さらにそれらを構成する部品・材料・表面改質の需要も押し上げる。
流体軸受スピンドルモータ(提供:日本電産) たとえばサーバ向けで15,000回転という高速スピンドルモータでは、トラック密度化が進む中、かつての玉軸受に見られる回転非同期振れがない流体軸受が使われている。流体軸受のスリーブでは、動圧を発生させるヘリングボーン溝の加工技術や作動オイルの技術が今なお開発・改良されている。
ピボットアッセンブリー(提供:ミネベア) また磁気ヘッドを取り付けたアクチュエーターの支点部分に使用されるピボットアッセンブリーはミネベアが65%の世界シェアを持ち、個々に組み込まれるミニチュア玉軸受の世界の生産量を2割引き上げ2億4,000万個体制にすることを決めたが、ここでは攪拌抵抗が少ないグリース技術や高速回転での耐久性を高めるボールや保持器の技術が必要とされる。
記録容量を高める決め手はヘッドとディスクの間のスペーシングを低減することだが、現在10nmを切るすき間でヘッドとディスクのクラッシュによる記録層の消失を避けるため、ヘッドおよびディスクに低摩擦で耐摩耗性の高いDLC(ダイヤモンドライクカーボン)などのカーボン系保護膜がコーティングされ、ディスク保護膜の上には1分子層の潤滑油膜が形成されている。現在4~3nmの保護膜についても1nm薄くするだけで記録容量増大に利いてくることから、富士通研究所とフェローテックでは2nmの保護膜を形成するFCA(フィルタード・カソーディック・アーク、真空中でのアーク放電によりプラズマ化したカーボン粒子を表面に堆積させる薄膜形成法)成膜技術の研究開発を進めている。
もちろんこうした薄膜を形成するだけにとどまらない。この薄膜が必要とされる保護膜としての機械的特性を備えているかを評価する必要があり、ナノインデンターなどの評価機器も需要が高まってきている。さらにこうしたHDD記録密度の向上に伴いその信頼性に対して加工に伴う残留成分や潤滑油膜などからの揮発成分といったマイクロコンタミネーションをコントロールすることが重要になってきており、HDD技術をリードするわが国から先ごろ、イオン性のマイクロコンタミネーションを測定・評価する改訂案が提起され10年ぶりに新スタンダード(イオンコンタミ測定)が成立した。これにより関連する計測システムの需要も生まれている。
SSDとの競争でコスト低減の要求が厳しいHDDでは、付加価値となる記録密度向上が常に必要不可欠で、それには上述のような様々な部品・材料技術の開発が求められている。新興国向けではさらなるコスト低減をふまえた独自開発も必要になるだろうが、わが国の独創的な部品・材料技術の集積により常にHDDの市場創出・拡大を推進していくことを期待してやまない。
第79回 海外市場獲得に動くわが国宇宙産業
第79回 海外市場獲得に動くわが国宇宙産業提供:JAXA 経済産業省は先ごろ、高い技術を誇りつつ諸外国と比べ国際受注の実績が乏しいわが国宇宙産業企業の海外市場開拓を図るべく、IHIやIHIエアロスペース、NEC、三菱電機など産業界もメンバーに加えた「宇宙産業ミッション団」をエジプトおよび南アフリカに派遣した。宇宙利用は発展途上国を含めて世界的に拡大、すでにアフリカでは、ヨーロッパ企業によるエジプトの通信放送衛星の受注、中国によるナイジェリアの通信放送衛星の受注、ロシアによる南アフリカの衛星の打上げ受注など、宇宙分野の国際競争が始まっている。
宇宙産業の国内市場規模は約7兆円で太陽電池や燃料電池などへの技術の波及効果も期待されているが、日本の宇宙機器産業(人工衛星など)の売上げの9割は官需で、欧米の約6割(残り4割が民需)というバランスに比べて偏りが大きく、わが国衛星メーカーは国内民需(スカパーJSat、放送衛星)も受注できていないのが現状。また宇宙機器の市場規模も、日本が2,600億円なのに対し、米国が3兆8,000億円、欧州が8,700億円と差が大きい。
一方、人工衛星の活用は近年、通信・放送や地球観測分野を中心に発展途上国でも進められており、打ち上げられる衛星は全世界で1999年から2008年まで128機だったものが2009年から2018年の間に260機程度まで拡大することが見込まれている。
こうした現状を踏まえ、衛星技術を保有する各国が発展途上国などへの売り込みを積極的に行っており、中国は衛星の提供を見返りにナイジェリアなどから資源を獲得することに成功しているほか、フランスも大統領自らのトップセールスの展開などの施策によりベトナムなどから衛星を受注することに成功している。
また、アフリカでも宇宙利用の需要は拡大しており、衛星単体で数十~百億円、地上の利用システムまで含めればより大きな市場拡大が見込まれるが、日本はこれまでデータ利用レベルの技術協力にとどまっており、衛星受注などの大型商談には至っていない。
経産省では、国内宇宙機器産業は国際競争力が乏しく、宇宙利用サービスを支える衛星システムはほぼすべて海外製であり、結果として宇宙利用が拡大しても、産業のバリューチェーンとして、宇宙機器産業と宇宙利用サービス産業の間で事実上分断されていると分析した。日本は世界で4番目に自国ロケットによる衛星打ち上げを実現したが、2009年1月に韓国の衛星打ち上げを受注するまで、商業打ち上げの実績はなかった。
こうした現況をふまえ経済産業省では、日本企業の国際進出を支援する技術施策として、世界最先端の商用衛星並みの性能・低コスト(30億円)・短納期(開発期間3年)を実現する高性能小型衛星(SASKE)の研究開発(ASNAROプロジェクト)に取り組んでいる。
たとえば地球観測用衛星では、小型化、高機動化(衛星姿勢を要求に応じて迅速に変える)、搭載センサの高性能化が要求されている。三菱電機では、小型化に向け先進的構造技術や電気推進系(ホールスラスタ)などの、また高機動化に向けコントロールモーメントジャイロやその開発を支える3軸衛星シミュレータ、宇宙用潤滑技術などの技術革新を挙げている。さらに、衛星搭載用センサの高精度化に寄与する機械系技術として、センサ駆動系などに用いる標準アクチュエータ、センサ指向精度の要となる可動鏡、センサへの擾乱を少なくする磁気軸受ホイールなども適用しているという。
(提供:USEF) また、小型衛星の打上げ手段として、特定の射場を必要とせず、打上げ機会の増加などを可能とする「空中発射システム」の研究開発システムの検討を進めている。空中発射システムは航空機にロケットを取り付けて離陸し、公海上でロケットを切り離し、さらに衛星を分離して軌道に乗せる技術。地上の大がかりな打ち上げ施設を必要とせず、地元漁業関係者らとの協議が必要な打ち上げ時期の制約が減ることなどから、低価格で機動的な打ち上げが可能になる。
提供;JAXA
次期固体ロケットの研究開発も進んできている。M-Vロケットは全段固体で惑星探査にも使用できる世界最高性能の多段式固体ロケットだが、総合的に見ると運用のコストがかさんでいたため次期固体ロケットではM-Vロケットの約3分の1程度を目標にコストの削減を図ろうと計画している。また、地上設備や打ち上げオペレーションにかかる時間を、M-Vロケットの4分の1程度になるようにコンパクト化。このために、ロケット搭載系の点検は機上で自律的に行い、地上系の手間を省く。ロケットの搭載装置は、現在ではロケットごとに固有のものを作っているが、次期固体ロケットではロケットに依存しない搭載系を目指している。
地球観測衛星の需要動向を見ると、過去5年間で年平均15%伸びており、2017年までに世界全体で34億ドルに達すると予測されている(Euroconsultレポート)。資源探査(石油・ガス・レアメタル)などに使う地球観測衛星を調達する発展途上国では、衛星のデータ利用に限らず、衛星の開発技術の獲得に対するニーズが大きい。このため、衛星に加えて、地上運用局、利用技術、技術教育、打上げまで含め、「システムとして売る」ことが必要となってきている。海外展開で立ち後れているとはいえ、わが国の宇宙技術は「システムとして売る」に足りる実績を持っている。今回のような官民合同ミッションにより、わが国宇宙技術の世界におけるプレゼンスが高まり、市場獲得に向け拍車がかかっていくことに期待したい。
第80回 エコカーの安全性向上でEPSの市場が拡大
第80回 エコカーの安全性向上でEPSの市場が拡大提供:ジェイテクト 自動車のさらなる燃費向上、安全性向上のニーズを反映して、電動パワーステアリング(EPS)の需要が拡大、メーカー各社が増産に乗り出している。約40%の世界シェアを持つジェイテクトは2013年の生産台数を1,500万台規模に倍増、また15%程度の世界シェアを持つ日本精工は2012年の生産台数を800万台と2.7倍に引き上げる考えだ。
自動車の操舵機構としてこれまで主流だった油圧式パワーステアリング(HPS)では、エンジンの力でオイルポンプを動かし、発生させた油圧で操舵力をアシストする仕組みとなっている。これに対しEPSは、必要な操舵力や回転速度、車速などをセンサーで検知し電子制御により、モーターを動かしてアシストする。常にオイルポンプを動かしているHPSに比べ、モーターを動かすだけのEPSでは、3~5%の燃費向上を図れる。特にハイブリッド車やEV車ではエンジン駆動がなくてもアシストが必要となるため、EPS化が不可欠となってきている。また操舵トルクの軽減だけでなく、トルクをアクティブに電子制御することで車両姿勢の安定化やレーンキープの補助を可能にするEPSは、最近国内外で取りざたされる安全性確保の面でも、有効である。従来小型乗用車を中心に採用が進んでいたEPSだが、燃費向上を目的に中型乗用車や大型乗用車でのニーズが拡大、さまざまなメカ技術により、省燃費性能と安全性向上が図られ、適用が広がってきている。
提供:日本精工 日本精工では先ごろ、直進走行中に路面の傾斜などによる車両の直進走行感(オンセンター感)の低下を検知して、自動的に直進走行感(オンセンター感)を補正する制御機能を備えたEPSを開発した。オンセンター感とは、車両が直進走行時に、ドライバーがハンドルに力を入れなくてもまっすぐに走行でき、また、ハンドルを左右に切ったら、ハンドルからの反力を感じることで車両の動きを把握できる手応えをいう。直進走行感向上機能付きEPSは、ハンドルの操作力を軽減するEPSに電子制御技術を応用、路面の傾斜や車両・タイヤの経年劣化などによる偏りを検出し、直進走行感を高める補正を自動的に行う制御機能を持つ。ドライバーのハンドル操作の負担を軽減し、安心で快適なドライビングに貢献する。
提供:日本精工 また同社は、安全性向上の観点から、EPSの電子制御技術を活かし、タイヤグリップロス状態検知機能を持ったEPSを開発している。タイヤの路面グリップが失われそうな状態になると、操舵トルクを補正することでドライバーに知らせグリップ状態での操作を促す。さらにグリップが失われたときには、グリップが回復するように操舵力を補正することで、ドライバーが正確なハンドル操作を行えるように支援する。これにより、特に滑りやすい路面での走行安定性を高めることに貢献するとともにドライバーに安心感を与える。
提供:ジェイテクト ジェイテクトでは、高出力化と車両搭載性の向上を同時に実現するデュアルピニオンEPS(DP-EPS)を開発している。EPSは、モーターと減速機の配置により、コラム式(C-EPS)、ピニオン式(P-EPS)、ラック式(R-EPS)の3種類に大別され、車種の特徴に応じて最適なタイプが採用されている。P-EPSはエンジンルーム内にアシスト機構(電動モーターと減速機のユニット)を配置し、ハンドル軸をアシストするEPSで静粛性に優れ、主に軽自動車から小型車クラスに搭載されている。開発品では車両搭載性向上と高出力化の要求に対し、アシスト機構をハンドル軸と分離し、2箇所のピニオンがラックと噛み合う構造とすることでアシスト機構の設計自由度を広げ、小型高強度減速機の採用などの技術を織り込むことで、従来のP-EPSに対し車両搭載性を向上し、20%増の高出力化を実現した。これにより、中型車クラスへの搭載も可能な出力を実現した。
提供:ジェイテクト EPSの要素技術開発も進んでいる。自動車操舵安定性向上志向から、ハンドルとギヤボックスをつなぐ連結軸である「インタミディエイトシャフト」で、高速直進走行時での安定性を得るための高い剛性感や、走行状態や路面状況で外乱による上下振動のスムーズな吸収などの要求が高くなってきている。これらのニーズに対しジェイテクトでは、ベアリングの設計を応用してガタのない直動型のボールスライド構造を採用して「高剛性ボールスライド式インタミディエイトシャフト」を開発した。ハンドル回転方向のねじり剛性が高く、ハンドルのあそびが低減され操舵安定性が向上するほか、ボールの転がりにより全操舵トルク領域で軸方向変位をスムーズに吸収できることで、外乱による軸方向変位を吸収し、正確なトルクを伝えスムーズな走行が可能となる。
高速走行性能と安全性をともに向上すべく、高速走行時の小さなハンドル操作をタイヤへ伝え、車の操縦性をより向上させるねらいで、日本精工では高速走行時のハンドル操作のダイレクト感が向上する自動車ステアリングジョイント「エクセオスジョイント™」を開発している。開発品では、ベアリング技術開発で培った摩擦コントロール技術、予圧技術、生産技術などを応用して、作動トルクを従来品と同レベルに抑えて、回転方向のガタ(バックラッシュ)をなくしハンドル操作のダイレクト感を向上している。
ハンドルの回転運動を左右の直線運動に変換し前輪の向きを変えるステアリングギヤシステムでは、構造がシンプルでスペースをとらず操舵感がシャープとされる「ラック&ピニオン式」が多く採用されているが、このピニオンギヤには軽量化が図れ摺動特性に優れるエンジニアリングプラスチック、ポリアミド(PA)樹脂製などが使われているが、さらに寸法安定性が高い上、長期間使用した際のバックラッシの増加量が著しく小さい、摩擦・摩耗特性のバランスがよいポリアセタール樹脂(POM、ポリプラスチックス社製など)も多用されている。
もちろん、EPSの高出力対応やさらなる省燃費化のための小型・高出力・低騒音のブラシレスモーターなどモーターの技術とモーター制御技術などの開発も進んでいる。エコカーの普及拡大に伴うEPSの需要拡大は、各EPS部品・コンポーネントの需要も押し広げており、それらの技術の研鑽により自動車の燃費向上と、安全神話の復権に貢献するEPSのさらなる市場拡大につながることを願う。
第081回~第090回
第081回~第090回第81回 新幹線車両事故防止に、さらなる軸受の信頼性技術を望む
第81回 新幹線車両事故防止に、さらなる軸受の信頼性技術を望む提供:JR西日本 3月3日、山陽新幹線N700系「のぞみ56号」(博多発東京行き)の車内に白煙が充満、床下の点検により台車の一部から油漏れが発生しているのを認め、約7000人の足に影響が出た事故に関して、解体調査を実施したJR西日本は、台車のうち破損した部品は、モータの動力を車軸に伝達する歯車を格納するアルミ製歯車箱(ギヤケース)内で、小歯車の軸受が破損し、歯車箱内に金属片などが残っていたことを報告、この状況から、小歯車の軸受が破損したことにより、軸受のころが大歯車側に回り、内側からギヤケースを破ったものと推定している。同社では今後も小歯車の軸受の破損原因について、鉄道総合技術研究所などの協力を得て調査していくとしている。
駆動モータの動力を車軸に伝える駆動装置には小歯車と大歯車があり、高速仕様の円すいころ軸受が多く使用されている。特に小歯車軸受では車両走行時の振動の影響を受け、保持器各部に繰り返し速度が速い様々な応力が発生する。このため保持器の板厚を挙げて合成を挙げ発生応力を低減させる手法や、保持器表面に軟窒化処理を施し耐摩耗性と疲労強度を向上させる手法などがとられている。
また、歯車装置用軸受は、歯車箱に封入された潤滑油により油浴潤滑されるが、潤滑油の攪拌による温度上昇が大きく、内輪内径寸法の拡大による内輪クリープを防ぐため、軸受内輪に寸法安定化の熱処理が施されている。
この潤滑油は次の重要部検査か全般検査まで使用されるが、それまでの間、機械の回転や摩擦で生じる熱で劣化するほか、部品の摩耗による金属粉や外部からは水分や塵埃が混入し劣化する。そのため劣化の判断基準を設けて管理が行われている。一定期間走行してきた潤滑油を採取し粘度や混入した金属分の量などを調べ、ある値を超過したら交換することが望ましいと考える。磁石を用いた分析方法(フェログラフィー)により、油中に混入した軸受からの摩耗粉を捕集して調べることで歯車装置の状態を知ることができる。摩耗粉の量や形状により検査時に解体して調べる必要があるかどうか判断することも可能となっている。
JR西日本では、最終的な原因が判明するまでの間、以下の対策を実施するとしている。
車両の摩耗品ならびに車体などの状態および作用について行う検査で、2日以内に実施する仕業検査、車両の集電装置、走行装置、電気装置、ブレーキ装置、車体などの状態、作用および機能について、在姿状態で、30日以内もしくは走行距離が3万kmに至るまでに実施する交番検査で油の汚損が認められた場合には、従来の点検に加え、磁気栓の状況を確認するとともに、以後の交番検査ごとに歯車箱内の潤滑油中に混入した歯車・軸受などの摩耗粉を永久磁石に付着させて、良好な潤滑油状態を保つための磁気栓の確認(フェログラフィー分析)を継続していくとしている。
提供:鉄道総合技術研究所 先述の通り高速新幹線(350km/hレベル)の歯車装置で使用されるギヤ油の温度は、150℃前後と極めて高温になることと見られることから、鉄道総合技術研究所では近年、従来の鉱油系ギヤ油に代わり、高速新幹線の歯車装置用合成ギヤ油を開発した。合成油は鉱油と比較して熱・酸化安定性に優れるため、新幹線の高速化に十分に耐えうるほか、耐熱性だけでなく、優れた耐劣化性も備えているため、検査周期延伸による省メンテナンス化に寄与することも期待されている。
高速車両の過酷な使用条件に耐える高信頼性の軸受が、こうした長寿命の潤滑油技術のもとで破損したことについて、JR西日本には徹底的な調査に基づく原因究明とそれに基づき大量輸送の高信頼性を確保するべく安全対策のフィードバックを実施してほしい。
第82回 月面探査ロボで注目される固体潤滑技術
第82回 月面探査ロボで注目される固体潤滑技術提供:JAXA 「月探査に関する懇談会」(座長:白井克彦 早稲田大学総長)では2020年ごろをめどに高度なロボットによる無人の月探査、さらには人とロボットとの連携による月探査を検討しているが、宇宙航空研究開発機構(JAXA)では先ごろ、一般からも広く募集する「月面ロボットチャレンジ」を実施、4月16日まで応募を受け付けている。将来の月面探査/有人月面拠点建設において月面ロボットがクリアすべき技術課題についてアイデアを募るもので、規定課題は主に、「クレータ中央丘岩石採取」と「拠点モジュールの埋設」の二つ。採択された場合には、JAXAとの共同研究として予算が付き、最終的には、試作機によるデモンストレーションまで実施する予定となっている。いずれにしても月面での過酷な使用条件に耐えるロボットとしては、摺動部分の潤滑、特に固体潤滑剤によるメンテナンスフリー・長期稼動というコンセプトは必須となってくるであろう。
宇宙空間では10-5Pa以下の真空、微小重力、原子状酸素などの環境にさらされるが、さらに月では大気がないため昼の部分の表面温度は110℃(赤道付近)、夜の部分は-170℃といった過酷な温度変化、表面を覆う砂状物質(レゴリス)の静電付着・侵入といった問題に、月面ロボットは対応しなければならない。
真空環境では液体潤滑剤の蒸発が避けられず、潤滑剤の選定には蒸気圧、周囲への汚染を考慮しなければならない。また、微小重力下では、摺動部から生じる摩耗粒子の浮遊に対する対策が必要となる。さらに高度100 km以上では紫外線により酸素分子が解離され原子状酸素となるが、原子状酸素は非常に酸化作用が強く、酸化による潤滑効果の劣化も検討が必要になる。先述の月面の広い温度変化に対応できる潤滑剤も求められる。レゴリスの熱伝導率が低いことから月面を1mも掘ると昼夜にかかわらず一定温度になることから、今回の課題にあるような拠点モジュールの埋設が必要となるが、一方でロボットの可動部分へのレゴリスの侵入機会が増えることになる。レゴリスは研磨作用も持つとされていることから、潤滑油への混入による潤滑作用低下は大いに懸念される。
宇宙機器は上述のとおり極限環境での使用を余儀なくされるため、液体潤滑は非常に飽和蒸気圧の小さな高分子体パーフルオロポリエーテル(PFPE)などが部分的に使われるほかは、多くの場合、二硫化モリブデン(MoS2)など層状構造物質では、銀(Ag)など軟質金属、四フッ化エチレン樹脂(PTFE)やその複合材の高分子材料などの固体を用いた固体潤滑法が、安定した潤滑特性と清浄性により宇宙機器の潤滑法として用いられている。アウトガスが極端に制限される場合や経年変化を極力防ぎたい場合は、固体潤滑剤の中でも特に蒸気圧が低く、化学的安定性に優れる軟質金属が多く用いられる。
たとえば転がり軸受は月面ロボットでも作業アームなどやホイール部分など回転・揺動の可動部分に必要となるであろうが、一つの衛星で見ても転がり軸受は50個以上用いられ、その90%以上で固体潤滑法が採用されているという。MoS2とPTFE系保持器の組み合わせにより摩擦係数0.001以下のものが実用化されており、 109オーダーの総回転数を維持したという報告があるほか、軟質金属被膜は、MoS2に比べ摩擦係数は高く、耐荷重能は低いという欠点があるもののアウトガスや摩耗はMoS2に比べ少なく2.9×108の寿命を実現したと報告されている。
固体潤滑剤の代表としてはMoS2が多用されているが、近年低摩擦や高硬度を両立する固体潤滑技術としてダイヤモンドライクカーボン(DLC)の適用が広がっている。こうした最新の固体潤滑の技術を交えて編集した『新版 固体潤滑ハンドブック』が先ごろ発刊された。書籍・文献コーナーで紹介しているので参照されたい。固体潤滑剤の関係者は「固体潤滑剤を適材適所で使うには、機器の使用環境に合わせて、前処理も含めた処理方法を適切に選ぶべき」としているとおり、こうした貴重な文献も利用しながら固体潤滑技術を有効に用いることで、わが国の月面ロボ開発に役立ててほしい。
第83回 もんじゅ運転再開に向け、さらなる安全性確保の取組みを!
第83回 もんじゅ運転再開に向け、さらなる安全性確保の取組みを! 1995年のナトリウム漏れ事故以来停止している高速増殖原型炉「もんじゅ」(定格出力28万kW、福井県敦賀市)の運転再開について、文部科学省の中川正春副大臣は先ごろ、同省が目標とした2009年度内(3月中)の再開は難しいものの最終調整段階にあることをほのめかした。事業見直しの声もある一方で、クリーンエネルギーとされる原発に回帰する「原子力ルネサンス」の急速な流れの中で、現在主流の軽水炉に代わる夢の原子炉として、運転再開に向けて着実に動き出している。
高速増殖炉 高速増殖炉は、軽水炉(熱中性子炉)と異なり、燃料のプルトニウムにエネルギーの高い(高速)中性子を打ち込んで核分裂を促し、炉内の燃えにくいウラン238を燃えやすいプルトニウム239に変えることで、発電するとともに消費した燃料以上の核燃料を新たに作り出す。高速増殖炉では増殖のために中性子が使われるため、軽水炉より多くの核分裂と中性子を発生させる必要があり、炉心で大量に発生する熱を取り出すのに、熱伝導性がよく、中性子を減速しにくいナトリウムが冷却材として使われる。
1995年12月の事故は、ナトリウムが配管から漏れ空気と反応して火災が起きたもの。放射能漏れはなかったが、ナトリウムの取扱いは高速増殖炉の根幹をなす技術だとして、事業主体の動力炉・核燃料開発事業団は解体、改組、もんじゅは稼働停止となった。この二次冷却系ナトリウム漏洩漏事故は、二次冷却系温度計さや管部で流力振動が発生、高サイクル疲労により破損したことが原因だったことから、二次冷却系温度計を改良型温度計に交換する措置がとられている。温度計さや管部について、長さを短くし剛性を増すことで流力振動を防止するとともに、テーパ状とすることで応力集中がない形状のものに交換したほか、高感度の漏洩検出器による早期検知、さらには信頼性の高い金属ガスケットを取り付け、漏洩抑制の機能を持たせている。
また、地震が多発する日本において、プルトニウムを燃料としナトリウムを冷却材に使うもんじゅの地震に対する備えはどうか、耐震設計と熱応力設計との相反する条件の妥協のもと設計された高速増殖炉もんじゅは軽水炉より地震に弱いのではないか、という周辺住民らの懸念に対して、日本原子力開発機構では耐震工事を実施した。
免震で使われるオイルダンパーの例(提供:大林組) たとえば昨年6月~11月まで地震時の既設設備の信頼性を向上する目的一環として、原子炉補助建物屋上に設置している排気筒について、排気筒支持構造鉄塔頭部に制震装置「オイルダンパー」を取り付け、耐震安全性を向上させている。排気筒支持鉄塔頭部の支持枠をオイルダンパーの付いた支持枠と交換、また5ヵ所ある支持点のうち2ヵ所については支持点の拘束を開放して筒身にかかる力を分散させる。オイルダンパーは、シリンダー内に封じ込めたオイルの粘性によって、地震の揺れ(振動エネルギー)を吸収する仕組みで、高層建築物の免震システムとしても採用されている。
「もんじゅ」の耐震安全性評価について日本原子力開発機構は、改訂された「発電用原子炉施設に関する耐震設計審査指針」に基づく評価に、活断層評価の審議及び新潟県中越沖地震の知見なども反映して基準地震動を見直した結果、基準地震動を600 ガル(水平方向最大加速度)から760 ガルに引き上げ、これに基づき原子炉建物、安全上重要な機能を有する施設、ナトリウムを内包する主要な設備等の耐震安全性評価の対象とすべき全施設の評価を実施し、耐震安全性が確保されていることを確認。これらの評価結果を取りまとめ本年2 月に原子力安全・保安院に報告し、3 月に原子力安全・保安院で当該報告に対する評価結果がまとめられ、同時に原子力安全・保安院の評価結果について、原子力安全委員会で妥当との確認が行われたとしている。
日本の原発は現在54基で、総発電量の約25%を占める。2020年までに温室効果ガスを1990年比で25%削減、2050年には同80%削減するという日本の地球温暖化対策において、原発の役割は大きい。特に高速増殖炉は、発電しながら同時に消費した燃料以上の燃料を生産できることから、原子力発電の燃料であるウラン資源の利用効率を飛躍的に高めることができ、エネルギー資源の輸入に頼らず安定したエネルギーを得ることができることなどから期待は大きい。しかし、高速増殖炉は実験炉、原型炉、実証炉、実用炉(商業炉)と段階的に開発が進められるが、原型炉段階のもんじゅでは2015年までに設計の確からしさを確認し、経済的な運転、保守・補修技術を確立するためにデータをまとめ、2025年ごろまでに次の段階の実証炉、2050年ごろまでに商業炉の完成につなげる計画だが、道のりは遠い。もんじゅでは将来的に炉心や燃料に関する研究開発などを行う計画も検討され、日本の研究開発だけでなく国際的な共同研究開発を行う役割も期待されているが、まずは稼働に伴う安全性・信頼性を福井県、敦賀市の地元に、また国に認めてもらい、その有用性とエネルギー政策上での重要な役割を理解してもらえるよう、安全性向上に対する関係者の引き続きの取組みが求められよう。
第84回 改正省エネ法、改正環境確保条例で高まる省エネ、創エネ技術
第84回 改正省エネ法、改正環境確保条例で高まる省エネ、創エネ技術新丸の内ビル(提供:三菱地所) 1年間のエネルギー使用量 (原油換算値)が合計で1,500kL以上の事業者を特定事業者と指定しエネルギー使用量の国への報告を義務づける「改正省エネ法」が、4月から施行された。使用量を把握した後、事業者はエネルギー消費効率を年平均1%ずつ改善していくことが努力目標となる。「エネルギーの使用の合理化に関する報告」いわゆる「省エネ法」は石油危機を契機に1979年、内外のエネルギーをめぐる経済的社会的環境に応じた燃料資源の有効な利用の確保と、工場・事業場、輸送、建築物、機械器具についてのエネルギーの使用の合理化を総合的に進めるための必要な措置を講ずることなどを目的に制定されたが、今回の法改正により、これまでの工場・事業場単位のエネルギー管理から事業者単位(企業単位)でのエネルギー管理に変わる。これまでは大手企業が規制対象となったが、事業所(工場や店舗、テナントなど)をまとめて規制値を超える中小企業も、フランチャイズチェーン(FC)も、オフィスビルも規制対象となる。
一方、東京都は4月から「環境確保条例」を改正、エネルギー使用量が1,500kL以上の大規模事業所を対象に、CO2排出総量削減義務と排出量取引制度を国に先行して導入する。産業部門だけでなくオフィスビルなどの業務部門も削減対象とする世界初の都市型キャップ・アンド・トレード制度で、第1削減計画期間の2010~2014年度に工場が6%、オフィスビルは地域冷暖房の利用状況に応じて6%か8%の削減義務率を適用される。
提供:山武 いずれも共通するのはエネルギー使用量を管理することで、OKIや山武、富士フイルムなどでエネルギー消費を可視化するシステムが開発されている。
また、オフィスや店舗では使うエネルギーの大半が照明や空調ということから、消費電力を大幅に抑える発光ダイオード(LED)照明や、平日の昼間の運転は中央熱源による冷温水で空調を行い、夜間や休日などの運転はヒートポンプ運転で行うことで、熱負荷の状況と熱源の運転状態に応じた経済的な運転を可能にするヒートポンプ式空調機などの導入が進んできている。さらに工場では、使用するフォークリフトをハイブリッド車にすることで、回生エネルギーを回収・蓄電し電力消費とCO2排出量を大幅に抑えているという。
提供:二叉風力開発 さらに、今回の両規制で対象となるエネルギーは化石燃料や熱、電気を対象とし、廃棄物からの回収エネルギーや風力、太陽光などのクリーンエネルギーは対象とならないため、太陽光発電の導入も進む。オフィスビルではテナントに省エネ努力を求めつつ、創エネに努める。たとえば東京駅前の新丸の内ビルでは、青森の二叉風力開発などのグリーン電力を親会社の出光興産から購入、使用電力をまかなう計画だ。
東京都に続き、2011年には埼玉県でも大規模事業所を対象にしたCO2排出量規制が始まる。それらは厳格な数値目標を掲げ継続的な省エネやCO2削減を要求しており、上述のような省エネ・創エネの機器・システムのアレンジ、導入がますます求められるだろう。それに伴い、そこで使われる風力発電用軸受など各種機械部品やLED用サファイヤ基板など各種材料の需要拡大に拍車がかかっていくものと見られている。
第85回 患者の不安感を軽減する低侵襲手術
第85回 患者の不安感を軽減する低侵襲手術提供:NTN 4月7日にプロ野球・巨人の木村拓也・内野守備走塁コーチ(37)が「くも膜下出血」のため死去した。くも膜下出血は、脳を覆うくも膜と軟膜のすき間に出血を起こす病気で、多くは脳の動脈にできた動脈瘤が破裂して起こる。動脈瘤ができる理由や破裂する時期などが不明で難しいとされるが、脳ドックのMRI(磁気共鳴画像)やCT(コンピューター断層撮影)の撮像でまだ破裂していない脳動脈瘤が見つかることも少なくないという。そうした疾病の早期発見の技術のほか、各種の低侵襲手術も登場してきている。
くも膜下出血が起きてしまうと治療法がなく、再び破裂しないようにする手術がとられる。手術には、動脈瘤の根元をクリップで挟んで血液が入らないようにする「ネッククリッピング手術」と、カテーテルを使って動脈瘤の内部を詰める「血管内治療によるコイル塞栓術」の2種類がある。
脳動脈瘤クリップ(提供:瑞穂医科工業)
ネッククリッピング手術で用いられる脳動脈瘤クリップは、生体親和性と耐久性・耐摩耗性に優れるチタン合金製などで、一生頭の中に入ったままでも問題がないといい、チタン合金製は手術後の検査、CTや特にMRIで画像が乱れることがない。血管を把持する部分の表面には血管から滑って外れる現象(スリップアウト)を防ぐために複数のピラミッド形状の穴が形成されているが、たとえば新潟大学・新田勇教授らはスリップアウトを防ぐのに最適な形状かどうかの検討を進めるため、レーザ加工機を用いて異なる種々の把持部表面を作製し,それぞれの摩擦特性を評価する研究を進めている。
コイル塞栓術 血管内治療によるコイル塞栓術では、太股の付け根の動脈から血管内に細いカテーテルを通し、先端を脳動脈瘤まで誘導する。このカテーテルを用いて脳動脈瘤の内部に極めて細いプラチナ製のコイル(マイクロコイル)を少しずつ詰めていき、内部を塞いで出血しないようにする。治療は手術室ではなく血管撮影室で行われ、開頭手術と異なり患者の体にメスを入れずにすむ低侵襲手術で、この十数年で普及してきた新しい治療法である。
適切な力でコイルを挿入するにはコイル挿入位置を決めるカテーテル先端の高度な位置決め技術が重要で、二人の医師でカテーテルとワイヤを操作することが多いが、操作する医師同士の意思疎通が非常に重要となるほか、医師一人で治療しなければならない場合もあり、これら課題の解決が求められていた。
提供:NTN これに対しベアリングメーカーのNTNでは先ごろ、名古屋工業大学大学院の藤本研究室、名古屋大学大学院医学系研究科脳神経外科の宮地准教授グループと共同で、先に開発した脳動脈瘤治療用センシングシステムに加え、一人の医師による脳動脈瘤コイル塞栓術を高度に支援する装置を開発した。
同装置では、一人の医師がフットスイッチにより連動したモータで指先では実現できない送りムラのない一定速でのワイヤ送り出しを行いつつ、両手操作でカテーテルを位置決めできる。ワイヤの送り出しにより変化するワイヤ挿入力は脳動脈瘤治療用センシングシステムで測定され、従来の視覚表示に加え、音程(聴覚)情報に変換されて医師に伝達される。この構成により、医師は術中に映し出されるコイルのX線画像を常に監視しながら、コイルとカテーテルを同時に操作できるという。
くも膜下出血の発症リスクが高いのは40~50代という働き盛りで、家族を支えわが国の経済を支える大切な層の一つだ。一人でも多くの人命を守るため、疾病の早期発見の技術やこうした低侵襲手術の技術がさらに発展していくことを期待したい。
第86回 風力発電の市場変化で求められる潤滑油技術
第86回 風力発電の市場変化で求められる潤滑油技術提供:三菱重工業 世界風力エネルギー会議(GWEC)が発表した2009年末の風力発電導入量は世界全体で昨年度比約31%増の1億5,790万kWとなり、1年間の増加量では、1位が風力発電を環境対応型エネルギーの柱に位置づける中国の1,300万kW(2008年比207%)、2位がグリーンニューディール計画を掲げる米国の1,000万kW(2008年比140%)となった。日本は18位となる18万kWで、本欄で何度も訴えているとおり、引き続き政策も含めた今後の導入促進が期待される。
この傾向に見られるように、デンマークのヴェスタスを筆頭に一時は約7割のシェアを占めていた欧州勢は、米ゼネラル・エレクトリック(GE)、印スズロンエナジー、中国シノベルなどの追撃により、2008年度にはシェアを4割程度まで落としてきている。特に市場が一様にピークアウトを迎え、また金融危機の影響でプロジェクトファイナンスを組むことが難しい欧州に対し、中国やインドなどの新興国は建設のキャパシティーが巨大な市場としても成長してきている。こうした市場を中心に風力発電機の定格出力は、主流が2MW級以上と大型化が進んできている。一方で、極地に近い地点やこれまで以上に温度変化が厳しい場所に立地せざるを得ない状況が増えてきており、こうしたニーズに対応して機械を正常に稼働・維持する各種機械要素とその潤滑油技術の高性能化がますます求められてきている。
提供:NEDO 風力発電機では、ブレード(羽根)で風を受けてロータを介して主軸が回転、その10~30rpmの回転速度を増速機により発電可能な1,200~1,800rpmという回転速度まで増やし、発電機により発電する。これら機械要素に対応する風力発電機用潤滑油としては主に、主軸軸受のグリース、増速機のギヤ油、発電機軸受のグリースがあり、増速機や発電機を収納するナセルが地上数十mという高さに設置されメンテナンスが容易でないことから、共通してロングライフ化(メンテナンスフリー)が求められる。風力発電機が新設されて5年以内に部品交換が必要となる風車は10~20%に上るといわれるが、特に増速機やベアリングのトラブルが多く、上述の装置の大型化や厳しい温度条件での使用という傾向もあって、増速機用潤滑油のさらなる性能向上が求められている。
大型化し風車の出力が2倍になると主軸トルクは2.8倍になると言われ、増速機のギヤや軸受に多大な応力がかかるようになってきているため、風力発電機増速機用ギヤ油では、歯面の損傷防止(摩耗や焼付きの防止)の機能、つまり耐摩耗性がますます重要になってきている。そこで潤滑油には極圧添加剤が用いられることになるが、風車においてはこの極圧添加剤が歯面のマイクロピッチングや軸受の疲労損傷を招くことがあるほか、酸化劣化を受けてスラッジ(夾雑物)を生成することもあるという。スラッジはフィルターを詰まらせ潤滑機能を低下させるばかりでなく、フィルターの交換という保全作業も発生させる。これに加えシベリアなどの極地に設置される局面も出てきたことから、-45℃といった極低温からの温度領域でも粘度特性を低下させず潤滑し続けることが求められている。
そこで適当な極圧添加剤や酸化防止剤などを選定し歯車の焼付き防止やスラッジ防止に有効な配合にするほか、低温から高温までの粘度特性に優れた高粘度指数(高VI)のベースオイル、特にポリアルファオレフィン(PAO)が基材として必須となってきている。
この風力発電機用潤滑油は、発電機の市場を牽引するのが欧米勢であることから英国BPや米エクソンモービルなど欧米のメジャー系が高いシェアを占める。某メジャー系によれば、「風力発電機増速機用ギヤ油の規格を見ても、欧州メーカーのインハウス規格が採り入れられたものが多く、一つの試験をクリアするのに数千万円の試験機が必要になるなど莫大な初期投資がかかることから、なかなか後発のメーカーには入りにくい市場」という。確かにある種の潤滑油添加剤が軸受の疲労損傷を招くことから、独FAG(現シェフラー)やスウェーデンSKFといった軸受大手が軸受の性能を保証すべくギヤ油に関しての自社規格を発行、風力発電機トップのヴェスタスがFAG規格に合格した潤滑油を採用することを決め、風力発電機他社もこれにならっている。
そのため欧米の発電機が市場の多くを押さえる国内でもまた、メジャー勢の潤滑油が多く流通している状況が続いているが、近年は三菱重工業を筆頭に国内風力発電機メーカーも開発を加速、国内でも出光興産など石油元売りや協同油脂などグリース専業メーカーを中心に風力発電機用潤滑油剤の開発が進んできている。使用条件が過酷化する風力発電機の性能、耐久信頼性を発現する潤滑油の国産化をベースに、わが国の風力発電ビジネスの活性化に拍車がかかっていくことを期待したい。
第87回 赤外線サーモグラフィ診断の人材育成・市場拡大に向けて始動
第87回 赤外線サーモグラフィ診断の人材育成・市場拡大に向けて始動提供:NEC Avio赤外線テクノロジー 日本赤外線サーモグラフィ協会が4月22日に発足した。赤外線サーモグラフィの広範な科学技術分野への普及を図るとともに、正しい測定方法を身につけた技術者の養成を目的として発足したもの。理事長には、神戸大学教授で、日本非破壊検査協会「赤外線サーモグラフィによる非破壊評価特別研究委員会」主査の阪上隆英氏が就任した。
赤外線サーモグラフィは、赤外線を検知して温度や熱を可視化する技術を利用した装置および測定方法。インフルエンザなどの発熱性疾患の検知から、プラントの異常発熱や構造物の欠陥による温度変化を重大な事故に至る前に検知する予防保全まで幅広い分野で利用され、10年前は数百億円程度だった世界市場(赤外線カメラ・モジュールカメラを含む)が現在1,000億円超の規模にまで拡大している。市場を牽引しているのは電力・電気設備の保守保全、発熱異常監視、建物診断に代表される非破壊検査などだが、国内では建築基準法(定期報告制度9改正により赤外線診断の適用範囲が広がり、また2009年には原子力施設の保全技術指針に赤外線サーモグラフィ法の適用が制定、さらには本年4月から改正省エネルギー法が施行されたことにより熱エネルギーの漏れ診断を熱計測により行うなど、さらなる用途拡大が見込まれている。同協会はこうした状況を踏まえ、赤外線サーモグラフィを正しく使用するための診断技術者向けのセミナーの実施や資格・規格の制定・整備のニーズに対応していく必要があると見て、設立された。
理事長である阪上教授はJAXAとの共同開発で、実際に赤外線サーモグラフィを使ったH-IIBロケットの検査、さらには次世代宇宙構造物の材料検査の研究を進めている。ロケットではわずかなキズやひび割れの存在も許されないため、見えない部分の損傷や欠陥を調べるために、綿密な非破壊検査が行われる。超音波を使っての検査が主流だが、巨大なロケットの1点1点に超音波を当てるには相当な時間と手間がかかる。
そこで、赤外線を使った新しい非破壊検査方法の出番となる。これは赤外線カメラで撮った画像から、構造物表面の欠陥を見つけだす検査方法で、ロケットはもちろん、トンネルなどの大きな構造物の非破壊検査に適している。強力なフラッシュランプを使って瞬間的に検査物に熱を与え、その情報を赤外線カメラでとらえてコンピューター画面に画像表示する。強力な熱があたった検査物の表面は瞬間的に温度が上がるが、内部に欠陥があるとその状態によって温度変化が起きる。その画像データを数値化していくことで欠陥の大きさや深さまでを測定できる、というものだ。
阪上教授は「赤外線による検査方法は特に材料の表層部を調べるのに適している一方、超音波は深い部分の検査に向いているため、これらの検査を組み合わせることで、より精度の高い検査の実現が期待される」と語る。阪上教授が主査を務める日本非破壊検査協会「赤外線サーモグラフィによる非破壊評価特別研究委員会」でも赤外線サーモグラフィによる非破壊評価技術のさらなる発展と普及を目指し、NDIS原案作成、ISO原案作成への国際協力等の標準化活動ならびに赤外線サーモグラフィによる非破壊試験技術者認証制度立ち上げに向けての準備作業を進めているという。
赤外線サーモグラフィによる工業的非破壊検査は、遠隔から広範囲を測定でき、効率的・視覚的に異常を検知できること、スクリーニング検査に威力を発揮することなど、他の手法にはない特徴を持つ。高度成長期につくられた様々な機器・構造物の経年劣化による破壊が問題となり、稼働中の機器・構造物を遠隔から 効率的に検査できる非破壊試験法に注目が集まっており、先述の特徴を持つ赤外線サーモグラフィによる非破壊試験法への期待も大きい。
赤外線サーモグラフィによる軸受の監視 日本赤外線サーモグラフィ協会の設立パーティーに出席した横浜国立大学名誉教授で原子力安全委員会で委員を務める白鳥正樹氏は「原子力発電所では耐震安全性から状態監視により不具合を見るが、多くの場合、超音波やAE(アコースティックエミッション)など音でとらえている。熱をとらえる手法のほうが可視化で瞬時に不具合がとらえられるだろう。世界的な『ニュークリア・ルネッサンス』で原発建設ラッシュの続く中、赤外線をキーワードにした発展の余地も多い」と語っている。
赤外線サーモグラフィによる軸受の状態評価などの研究も進む一方で、データとの相関性がとらえにくいため導入に踏み切れないとの声もある。そうした意味合いからも、今回赤外線サーモグラフィを正しく使い正確な測定・評価をする技術者の育成に向けて動き出したことは、機械・設備を健全に稼動させ、トータルコストダウンや省エネに貢献するだけでなく、特に原子力発電所のような設備では安全信頼性の確保につながる。日本赤外線サーモグラフィ協会設立にあたり、赤外線サーモグラフィの技術者が増え、機械・設備の管理手法が確立されるとともに、適正な適用により市場を伸ばしていくことに期待したい。
第88回 トラクションドライブ式CVTの適用拡大に向けて
第88回 トラクションドライブ式CVTの適用拡大に向けてハーフトロイダル式CVT(提供:日本精工) 自動車技術会は先ごろ、「平成22年度自動車技術会賞」の受賞者を発表、自動車工学および自動車技術の向上発展を奨励する機械要素技術としては今回、日本精工の宮田 慎司氏、ミュンヘン工科大学のBernd-Robert Höhn氏、Klaus Michaelis氏、Oliver Kreil氏(ミュンヘン工科大学)による「トロイダル形無段変速機のトラクション接触面内部における発熱解析」が論文賞を受賞、トロイダルCVTの適用拡大に向けて、動力伝達効率向上の取組みが評価された。表彰式は5月19日~21日に横浜市のパシフィコ横浜で開催される自動車技術会春季大会会期中に行われる。
左:フルトロイダルCVT、右:ハーフトロイダル式CVT トロイダルCVT(トラクションドライブ式無段変速機)は、入力ディスクと出力ディスクの二つのディスクに挟まれたパワーローラの傾き角度を変えることで、無段変速を実現する。トロイダルCVT の原理は1877年米国のCharles W.Huntにより考案された。この構造は現在フルトロイダル型と呼ばれる形式のもので、ジェイテクトがこのフルトロイダルCVTの出力軸に遊星ギヤによる減速機構を使用しクラッチを使わず回転をゼロにできるIVTの開発を進めている。
提供:日本精工 これに対し日本精工が製品化し開発を継続しているのが、1960 年代にKraus が動力伝達を行う接触点でのスピンに着目、スピンを減らすことができるハーフトロイダルCVT。接触点の面積を増加できるだけでなく、伝達効率の改善や耐久性の向上や小型化が図れるというメリットがある。日本精工では1978年に、このハーフトロイダルCVTの原理をベースに、高圧下で固化したオイル(トラクション油)のせん断力により動力を伝達するトラクションドライブについて、トラクション油を担当する出光興産とともに本格的な研究に着手、21年の歳月を費やし1999年に世界で初めて量産市販車である日産セドリック、グロリアに「エクストロイドCVT」として採用された。従来の自動変速機(AT)に対して燃費を10%向上、日産では当時、「無段変速による滑らかで静粛性に優れた変速と、従来のベルト式CVTでは不可能な280PSターボエンジンへの無段変速機の搭載がはじめて可能になった」と評価した。
提供:出光興産 ここであらためて、ハーフトロイダルCVTの機構を見てみよう。動力を伝達する歯車の歯を限りなく小さくすることができれば、極めて滑らかな動力伝達が可能になる。このためハーフトロイダルCVTでは、歯車の代わりにディスクとパワーローラを使う。油圧で押しつけられたディスクとパワーローラの接触面の圧力は最大ヘルツ圧力1~4GPa(≒1~4万気圧)の超高圧状態となる。ディスクとローラの間に介在するトラクション油は、このような超高圧の接触面を通過する1/1,000~1/10,000秒というほんの一瞬で粘度が増大しガラス状に固化してパワーを伝達、通過後に圧力から開放されるとサラサラの潤滑油に戻る。形成された厚さ1μmのガラス状油膜の剪断抵抗が入力ディスク→パワーローラ→出力ディスクと順次牽引する力となって現れ、タイヤ駆動力を伝達する役割を果たす。これが「トラクションドライブ」と呼ばれる動力伝達機構である。
一方、ディスクとパワーローラは先述の高面圧で転がり接触をしているため、接触面の耐久性が問題になる。日本精工では、非金属介在物を限りなく取り除いたCVT用の超高清浄度鋼「CVT鋼」の開発や、特殊な熱処理技術により、異物の噛み込みによる圧痕を無害化する応力緩和特性に優れた残留オーステナイトという柔らかい金属組織を増やしつつ硬さを維持する材質を実現。高荷重、高温、高速という厳しい環境下でも高い信頼性と性能を実現している。
ディスクとパワーローラ、トラクション油をキーテクノロジーとする変速機構のため、伝達トルクを増やすためにはディスクとパワーローラの圧接力を増やしトラクション油の伝達力を上げる必要があるが、トラクションによって発生した熱がトラクション油の設定された温度域を超える状態になると、トラクション油の粘性が下がり伝達効率(剪断抵抗)が下がる。トロイダルCVTの伝達効率は、運転中の接触部の発熱による温度上昇により大きく変化するわけだが、トラクションの接触部は運転時に生じる微小滑り領域でスピン運動を伴いながら発熱を伴うため、予測が困難だった。今回の自動車技術会賞を受賞した論文は、トラクション接触部の接触面内部の温度上昇量を、二円筒転がり試験機を用いたモデル実験で実測するとともに発熱を考慮したトラクション接触面内部の温度上昇計算式を示し、実測データと検証を行ったもので、これにより、トロイダル形CVTの伝達効率の正確な予測に貢献するものとして評価された。自動車の燃費改善では、大型自動車用のCVTにも、さらなる伝達効率向上が求められており、こうした大型車にも対応できるトロイダルCVTは、燃費改善の手法の一つとして期待されている。
ハーフトロイダルCVT適用の川崎重工業「T-IDG」 製造コストなどの問題などからその後の量産車での搭載は進んでいないのが現状だが、川崎重工業がエンジン回転数に関わらず一定周波数400Hz(115V)発電ができるよう発電機を一定回転数に保つため、日本精工のハーフトロイダル式CVTを使った航空機用主電源供給装置「T-IDG(Traction Drive Integrated Drive Generator)を開発するなど、トロイダルCVTの産業での実績は着実に積み上がってきている。富士重工業の新型レガシィでチェーン式CVTが搭載されるなど、高トルク対応の新しいCVT技術も登場してきているが、伝達効率向上やコスト低減の試みなど、機械要素と潤滑油の技術の粋であるトロイダルCVTの適用拡大に向けたさらなる取組みに期待したい。
第89回 ものづくりのノウハウ導入で植物工場の低コスト化を!
第89回 ものづくりのノウハウ導入で植物工場の低コスト化を!提供:キユーピー 日照不足などの天候不順から野菜が異常に高騰したことなどもあって、「植物工場」が注目されている。植物工場とは、施設内で植物の生育環境(光、温度、湿度、二酸化炭素濃度、養分、水分など)を制御するなど、栽培に適した環境を人工的に作り計画的に植物を生産するシステムをいう。天候や土などの自然環境に左右されず、野菜や花を大量生産し、安定供給を図るもの。たとえばキユーピーが開発を進める植物工場「TSファーム」では、三角パネルと噴霧耕を利用した立体水耕栽培で、定時、定量、定品位のサラダ菜やリーフレタス、ホウレンソウ、ハーブなどの工業的な生産を試みているほか、サンドウィッチを扱うサブウェイでは、未来型ファーストフードとして植物工場を併設した店舗を提案、地産地消をさらに進めた「店産店消」というスタイルを提唱している。
提供:エスペック 植物工場には閉鎖環境で太陽光を使わずに人工光のみで生産を行う「完全制御型」と、温室などの半閉鎖環境で太陽光の利用を基本にして雨天時の補光や夏期の高温抑制技術などを行う「太陽光利用型」がある。完全制御型を例にとると、一般に人工光の照度、日長、温度、湿度、養液PH/EC、液温、CO2などを自動制御して、栽培に最適な環境を維持する。そこでは主に、各種センサ、コントローラ、CO2供給装置や養液供給装置を含む栽培装置、各種光源、空調などが稼働している。
ムービングベンチ(提供:エスペック) しかし完全制御型植物工場では100gのレタスを作るのに約150円とコスト高になるという課題がある。そのコスト試算例を見ると、設備償却費などが38%、人件費が31%、水道光熱費が16%、その他が15%で、意外に人手がかかっていることがわかる。そこでロボットなど自動化を進め、コストを圧縮する試みが進められている。現在、栽培した作物の収穫や包装、苗の移植作業はほぼすべて手作業で行われるが、苗を栽培パネルに植込む作業ロボット自動植機では、定植作業の大幅な省力化が図れる。そのほか人件費を抑える自動化として、を支えるツールとして、搬送機能を備えたムービングベンチや、植物の生育に合わせ間隔を広げる搬送機構を備えたスペーシング装置などの搬送装置の導入も進んできている。これら搬送装置では、食物となる製品を扱うため、半導体製造装置で使われるようなクリーン化技術が適用されている。真空仕様のサーボモータや低発塵仕様のボールねじや直動案内などである。
1974年にわが国初の植物工場の研究に着手した日立製作所では、コスト圧縮にはこうした自動化のほか、ものづくりの技術を導入することで解決できるとしている。温度管理に省エネのヒートポンプを使ったり、光源に効率的なLEDを使ったりという具合である。農林水産省と経済産業省は農商工連携の推進のため、農商工連携促進法を制定、今後3年で生産コストを30%、植物工場を3倍に増やすことを目指している。食糧自給率の低いわが国において、内需型産業である農業にわが国の得意とする製造業の技術を導入することは、新しい内需型産業の創出にもつながる。引き続き、ものづくりのノウハウを融合した、コストパフォーマンスのよい食品工場の普及に期待したい。
第90回 自動車技術展に見る自動車の軽量化技術
第90回 自動車技術展に見る自動車の軽量化技術 自動車、部品、材料メーカやテスティング、CAEソリューション、カーエレクトロニクスの最新製品・技術が一堂に介した「自動車技術展:人とくるまのテクノロジー展 2010」が5月19日~21日、横浜のパシフィコ横浜で開催、70,947名が来場した。
今回の展示では、販売が好調なハイブリッド自動車(HEV)や、発売が始まった電気自動車(EV)の市場をにらんだ製品・技術が多数展示されたが、内燃機関も含め一様に、軽量化による低燃費化技術がアピールされた。
エンジン技術の軽量化ではたとえば、不二WPCがアルミピストンの耐久性と摺動特性を向上する表面改質技術として、潤滑性・耐摩耗性が高いダイヤモンドライクカーボン(DLC)コーティングとその密着性を向上する微粒子ピーニング(WPC)を複合処理する手法を展示した。
また、エンジン周りの金属部品について樹脂化による軽量化がいくつか提案されていたが、たとえばダイセル・エボニックでは、エンジンオイルポンプ用のギヤロータで軽量化のほか静粛性、耐油性に優れるポリエーテルエーテルケトン(PEEK)樹脂の適用を提案した。
トロイダルCVT
右:油の攪拌抵抗を低減したパワーローラ軸受保持器今回「トロイダル形無段変速機のトラクション接触面内部における発熱解析」で自動車技術会の論文賞を受賞した日本精工では、パワーローラ軸受保持器を平板からドーナツ型に湾曲、トラクション油の攪拌抵抗を低減することなどで、実用領域での伝達効率を向上するとともに、バリエータの小型化を図り軽量化し、数%の燃費向上につなげるとして、近い将来の再度の車載を目指している。
また、NTNは、インホイール型小型モータ内蔵アクスルユニット、電動ブレーキユニット、多軸荷重センサを組み合わせたインホイールモータ式の次世代EV向けユニットを出展した。小型モータの高速回転を生かしながら1/11の高減速比でトルクを増幅してタイヤに伝えるサイクロイド減速機を納めたユニット化などにより、従来の開発品に比べ3割程度の軽量化を実現している。
材料・表面改質技術や加工技術のほか、CAEなど解析技術や試験・評価技術など様々な技術・手法により支えられた、内燃機関のさらなる燃費向上とCO2削減、またHEVやEVの一充電あたりの走行距離延長につながる軽量化技術のさらなる発展に期待したい。
第091回~第100回
第091回~第100回第91回 環境・人にやさしい水圧技術の市場開拓に向けて
第91回 環境・人にやさしい水圧技術の市場開拓に向けて提供:三菱重工業 油圧・空圧・水圧機器の業界団体である日本フルードパワー工業会は先ごろ、東京都港区の東京プリンスホテルで通常総会を開催、新会長に就任した宮内壽一・甲南電機社長は総会後の懇親会の挨拶で、「わが国の機械産業のものづくりを支える重要な基盤技術であるフルードパワー技術においても、CO2削減は大きな課題。省エネ化技術、中でも水圧技術の開発を強力に推進したい」と語った。
水圧システム、ADS(アクア・ドライブ・システム)は水道水の圧力(適正水圧は0.25~0.4MPa)で機器を動かす。ADSは水道水を作動流体として使用するため、油圧に代わる環境に優しい、低コストなフルードパワーとして、研究開発が活発に行われている。現時点では事業としての数字が現れていないが、徐々に適用を広げ、2012年には1,100億円の市場規模となるとの予測もある。現在主流の油圧機器が2,600億円程度、水圧機器が2,300億円程度の市場を持つことから、フルードパワー全体としてはその段階では7,000億円の市場を形成することとなる。
しかし水圧機器では、作動流体となる水が、油圧機器の作動流体である作動油と違い低粘度(油が50mm2/sなのに対して、水が1mm2/s)で潤滑性に乏しいため、摺動面の設計が問題となる。
特にシール技術である。水圧ポンプなどでは、流体である水の内部漏れや外部漏れの増加により作動効率が低下するとともに、摺動面では流体の粘度が低いことで固体接触しやすく、摩擦損失、ひいては焼付きを引き起こす。
水潤滑水圧ポンプや水圧シリンダなどを幅広く手がける三菱重工業では、水圧機器内部隙間の漏洩量大(油圧比50倍)で低効率となる問題に対し、隙間管理を適正化し、低摩擦シールを採用することで克服、油圧システムからの代替を進めている。
シールメーカーではたとえばKYBと早くからADSの開発に参画していた阪上製作所では、水圧機器用シリンダシールとして、密封流体の水の潤滑性が劣ることや乾燥しやすく摩擦・摩耗、耐久性の面でデメリットとなることから、水潤滑に適したシール形状・材料や摺動面の潤滑保持の工夫、負荷の大きさに合わせたシールやウェアリングなどの摺動部材の選定に留意している。特に大気側にあたる潤滑・水膜の保持されにくいロッド部のシールとして、水の循環ポートなどを設けたほか潤滑保持リングを併用することなどで往復動の摺動耐久性を向上している。
提供:KYB。水圧リフト。風呂場での適用も検討。 こうした漏れや貧潤滑への対応の一方で、水圧機器ならではの用途展開も進む。たとえば、介護機器として、身障者を風呂まで運ぶ簡易リフト。風呂場で使う目的のため、漏れもある程度許容される。また食品機械であれば、万が一、作動流体である水が漏れた場合も製造現場、さらには加工品である食品に対して衛生面でのリスクを回避できる。
世界的に水ビジネスが市場を拡大する中、こうした水圧機器はコンポーネントの一つとして有用な技術となるであろう。先ごろ、機械システム振興協会が日本フルードパワー工業会に委託して進めた調査研究「新水圧システム(ADS)を用いたロボティクスの新機軸応用に関するフィージビリティスタディ(F/S)」が終了し報告書がまとめられ、他国での実用例やわが国で推進する上での課題などが示されたが、引き続き産官学一体となって、シール技術など効率・耐久性の向上につながる技術に磨きをかけつつ、水圧機器の利点を生かした用途開発に努めてほしい。
第92回 「産業構造ビジョン2010」が示す、ものづくり産業の方向性
第92回 「産業構造ビジョン2010」が示す、ものづくり産業の方向性提供:三菱重工業(Approved by Taiwan High Speed Rail Corporation) 経済産業省の産業構造審議会産業競争力部会がこのほど、昨年12月30日に閣議決定された新成長戦略(基本方針)を踏まえ、日本の産業の行き詰まりや深刻さを踏まえ、今後わが国がどう国富を稼ぎ、雇用を増やすかについて議論し、最終報告書「産業構造ビジョン2010」を取りまとめた。日本経済を再び成長の軌道に乗せるには、国を挙げて産業のグローバル競争力強化に乗り出すことが必要で、そのためには政府・民間を通じた(1)産業構造の転換、(2)企業のビジネスモデルの転換、(3)「グローバル化」と「国内雇用」の関係に関する発想の転換、(4)政府の役割の転換という、四つの転換が必要不可欠と指摘した。
まず産業構造の転換とは、自動車のみの一本足打法から、インフラ関連/システム輸出、文化産業、環境・エネルギー課題解決産業、医療・介護・健康・子育てサービス、(ロボット、宇宙などの)先端分野といった、外的なショックにも柔軟に対応できる多極的な構造(八ヶ岳構造)へと中長期的に産業構造を変革させること。たとえばインフラ輸出では鉄道が先行しているが、ここではわが国の得意とする車両の高速化やメンテナンスフリーに貢献するベアリング技術や、架線やレールの材料・固体潤滑技術、安全制御に関わる油圧・空気圧技術などのメカ技術が適用されている。また、欧米に比べビジネス化が出遅れている医療技術だが、高分子量ポリエチレンなどの材料やダイヤモンドライクカーボン(DLC)などコーティングなどが支えるインプラントから、転がり軸受や流体軸受、直動案内が支えるCTやMRIなどの画像診断技術など、技術ベースで見ればわが国が先行している。つまり、これら八ヶ岳構造といっている多様な産業構造を支えるわが国のメカ技術は、すでに確立されているといえよう。
こうしたわが国の先行する技術を事業でも勝ち組にするための転換が、企業のビジネスモデルの転換、グローバル化と国内雇用の関係での発送の転換、政府の役割の転換である。ものづくり大国であるわが国がグローバル競争で生き残るには、とりもなおさず先端技術の開発力の維持・強化は必要であるが、どの基幹技術をブラックボックス化し、どの部分をオープンにして国際標準化を目指すかという使い分けを戦略的に進めるといったビジネスモデルの徹底的な洗い直しを行わなくてはならない。その上でグローバル化=国内雇用の減少という図式を転換し、他国に輸出するためのビジネスインフラを高水準に整備すべく国内雇用を創出する、という発想にあらためようというわけである。先述した鉄道のほか、材料、潤滑、コーティング、軸受やハーモニックドライブ減速機など機械要素技術、制御技術で技術優位性を持つ宇宙産業、安全信頼性のメカ技術、設備診断・管理技術などで実績のある原子力発電産業など、インフラ輸出の対象となる技術・産業は少なくない。
このグローバル化と国内雇用創出を両立するには、政府の役割は欠かせない。宇宙産業の分野ではすでに、ヨーロッパ企業によるエジプトの通信放送衛星の受注、中国によるナイジェリアの通信放送衛星の受注、ロシアによる南アフリカの衛星の打上げ受注など、国を挙げての受注合戦が始まっている。経済産業省でも先ごろ、官民で構成する「宇宙産業ミッション団」をエジプトおよび南アフリカに派遣したが、わが国では、戦後から1980年代初頭まで行われていた「護送船団方式」と称される個別産業保護的な政策への反動として国は企業活動の自由を保証、市場機能を無批判に肯定する議論や、産業政策における国の役割をすべて否定するような議論も台頭、官民の連携が失われていった。しかし、日本工作機器工業会で会長を務めるTHK社長・寺町彰博氏が言ったように、明らかに「わが国の技術が活躍できるはずの医療分野での政策の遅れが目立つ」といった状況がある。しかし、ある経済産業省幹部によれば、民主党政権に代わってから医療政策の遅れによるわが国医療ビジネスの遅れという危惧感が共有され、厚生労働省との足並みも揃いつつあるという。
突然の菅直人首相への交替による政府のベクトルの乱れも危惧されるものの、ものづくりに関わる企業としては先述の四つの転換を試みつつ、ものづくりの復権に向けた意識を官民が共有しながら、世界に誇るわが国のメカ技術、ものづくり産業がグローバルに事業ベースでも勝ち組となり、2020年に150兆円という新分野の産業創出、258万人という雇用創出につながっていくことを期待するものである。
第93回 洋上風力発電普及に向けたベアリング技術のブレークスルーを
第93回 洋上風力発電普及に向けたベアリング技術のブレークスルーを 新エネルギー・産業技術総合開発機構(NEDO)と東京電力はこのほど、千葉県銚子市沖3km、水深11mの地点にローター直径約90mの風力発電システム(出力2,000kW以上)を1基設置、洋上風力発電の実証事業を共同で開始する。国内の陸地では風力発電に適した地点が限られていること、陸上部と比べて風が強く1.5倍程度の発電量が期待できること、さらには陸上で問題になっている風車の低周波音や騒音の被害を避けられることなどから、洋上風力発電への期待が高まっている。NEDOでは、この6月から2014年3月までの4年間で、日本の気象条件に適したシステムの開発を目指す。
こうした中、洋上での使用にともなう風力発電機要素部品の塩害対策などが検討されているが、腐食や水素脆性を防止する風力発電機用ベアリングの新規材料が登場してきている。たとえばイスマンジェイでは7月から、風力発電機用軸受向けに直径5cmのシリコン合金「メラミックス」製ボールの量産を始める。同材料は、安定生産が難しいとされていた幻のセラミックス・β-サイアロンの特性を持つシリコン合金で、セラミックスの軽さと特殊鋼の強度、非磁性、高耐食性といった特徴を持つもの。
風力発電機では回転トルクを増速機に伝える主軸の軸受、発電可能な回転数まで増やす増速機用の各軸受、発電機用軸受が使われているが、このうち発電機用軸受では一般に、通常の軸受鋼を使った場合、落雷などにより軸受内部のボールと軌道面の接触面にスパークが発生、軸受の軌道面、ボール転動面に生じる損傷(電食)を引き起こす。この電食対策や洋上での腐食、水素脆性などへの対策として、ボール軌道面にセラミックスの絶縁コーティングを施したり、窒化ケイ素製のボールを使用するなどの手法が用いられている。しかしセラミックスコーティングは長期使用によるはく離が、また窒化ケイ素のボールは被加工性の悪さからコスト高となることや機械的強度などが懸念されていた。
これに対し上述のシリコン合金メラミックスでは、独自開発の外部エネルギーを必要としない制御型燃焼合成装置により、埋蔵量の多いシリコンと窒素から合成した結晶を粉砕機で500nm程度まで超微細化することで、セラミックスの軽さ・耐腐食性、非磁性に加え特殊鋼並みの強度を持たせている。非磁性であることから前述の電食を防止できるほか、軸受鋼に比べ半分以下の重さとなることから高速回転での遠心力による負荷が小さくなり、発電機の寿命も延びるという。
イスマンジェイでは、シリコン合金製ボールの生産をまず月に2,000個からスタート、風力発電機用軸受向けに欧州に出荷を開始、数ヵ月後には生産規模を同1万個に拡大する計画。「セラミックスでは焼結助剤が切削抵抗となり研削性が落ちるのに対し、焼結助剤を用いないメラミックスでは研削効率が約60%上がる。その優位性から使用量が増えれば価格競争力もついてくる。洋上での使用にともなう腐食や水素脆性の防止なども含め、風力発電機用ベアリングボールとしての要求項目をクリアすることになるだろう」(同社副社長・松下昌史氏)。
政府は先ごろ、洋上風力発電機を設け、2020年までに原子力発電所10基分に相当する1,000万kW以上の電力を生み出す構想を打ち出した。ローター直径120mの大型風力発電機が2,000基以上稼働する計算となる。
風力発電機では増速機や発電機を収めるナセルの位置が地上60~100mという高所に置かれることなどから、軸受のメンテナンスコストが数百万以上かかると言われるが、洋上発電ではさらに管理・保全が容易ではない。メンテナンス期間延長を図るこうした軸受材料のブレークスルーが求められている。
第94回 「はやぶさ」が7年ぶりに帰還、実証技術の産業利用へ
第94回 「はやぶさ」が7年ぶりに帰還、実証技術の産業利用へ提供:JAXA 6月13日深夜、小惑星探査機「はやぶさ(MUSES-C)」に搭載されていたサンプル回収カプセルがオーストラリア・ウーメラ立入制限区域に無事着陸、はやぶさは2003年5月のM-Vロケット5号機による打上げ以来、7年ぶりに地球に帰還した。はやぶさのミッションは、近地球型小惑星「イトカワ」(大きさ約500m)から地表のかけら(サンプル)を採取し、回収カプセルで地球に持ち帰るという、世界初のサンプル・リターン技術の確立。地球上でサンプルの分析が行えるため、回収される量が少なくてもその科学的意義は極めて大きいとされる。これまでのサンプル・リターン計画は、非常に大型のロケットが必要とされることから断念されてきたが、高性能化した推進機関「イオンエンジン」の採用により、形状が約1m×約1.6m×約2mで太陽電池パドルの端から端までが約5.7m、燃料を含む質量が510kgという小型軽量の探査機が完成、実現できたもの。
「はやぶさ」には主に、イオンエンジンという新しい技術を使って惑星間を飛行するミッションのほか、自律誘導航法、小惑星「イトカワ」のサンプル採取、推進剤を使用せず地球の重力を利用して軌道の方向や速度を大きく変更する「地球スイングバイ」、回収カプセルを地球に持ち帰る「再突入カプセル」というミッションがあるが、これらに大きく関わっているのも、NECが開発したイオンエンジンの利用によるところが大きい。
提供:JAXA イオンエンジンはキセノンという気体をイオン化し、電気的に加速して噴射する仕組み(電気推進エンジン)。燃料の効率が非常によいことから、将来の月・惑星探査でも重要な技術として期待されており、「はやぶさ」には、マイクロ波を用いた無電極放電によるプラズマ生成利用した新開発のイオンエンジンが4台搭載されている。
「はやぶさ」は数々のトラブルに見舞われ帰還が危ぶまれた。「はやぶさ」には、小型のロケットエンジンでガスを噴出させその反力で機体姿勢制御と詳細位置制御を行う「化学推進スラスター」が12基実装されているが、たとえば2005年11月に2回目のイトカワへのタッチダウン(微小な重力しかないイトカワからサンプルを採取するため、1秒間程度だけイトカワに着陸すること)を行った後、化学推進スラスターが燃料漏れで全基使えなくなった。これにより姿勢制御が不全になったため、想定外の使われ方だったが、イオンエンジンの燃料であるキセノンガスを中和器から噴射して姿勢を制御することに成功した。しかし、燃料漏れに伴うアウトガスの排出作業などにより帰還が3年間延び、イオンエンジンは設定より長時間稼働しなくてはならなくなった。
また、円盤の回転する力によってコマの姿勢が安定するような原理で、衛星の姿勢を安定化させ、向きを変える「リアクション・ホール」が3基搭載されているが、そのうち2基が故障した。上述のとおり、通常の姿勢をコントロールする化学推進スラスターは使えない。そのため、帰還に向け姿勢を安定させながら正しく軌道をコントロールすべく、イオンエンジンを噴いては止め、軌道を精密に計測して、どれぐらい軌道に修正をかけるかを決めてはさらに噴射する、という作業が繰り返された。
提供:JAXA そのイオンエンジンも想定外の環境変化や長時間稼働により、2009年11月、4基ともに異常が報告されたが、JAXAがイオンエンジン4基について中和器の起動確認や流量調整などを実施、スラスターAの中和器とスラスターBのイオン源を組み合せることで、2台合わせて1台のエンジン相当の推進力を得るクロス運転に成功、「はやぶさ」の2010年6月の地球帰還計画が維持されたのである。
「はやぶさ」の帰還に沸く中、そこに満載された世界初の技術の産業利用が始まろうとしている。NECではすでに静止衛星の軌道制御用などでイオンエンジンのビジネス化を推進し始めている。静止衛星は放置すると軌道が少しずつずれて南北にふらふらするようになるため、スラスターで軌道を修正し続けて静止軌道に留める(南北制御)。この作業にイオンエンジンを使うと、推進剤の消費量が小さいため衛星を長期間使えるようになるという。世界最長となる惑星間空間で累積4万時間の運転を達成し「はやぶさ」のミッションを成功させた高信頼性を売り物にしてマイクロ波放電方式イオンエンジンで参入しようとしている。
イオンエンジン以外でも、重さ数gの金属球をイトカワの表面に撃ち込んで飛び散った粒子を採取する回収技術や、再突入中に受ける最大の空力加熱量がスペースシャトルより何十倍も大きく、表面が数千度という高温になることに耐える再突入カプセルの断熱材技術など、産業分野で転用できそうな技術・アイデアは多いと見られている。発表されてはいないが、予想外の長時間稼働での機械の信頼性を確保した潤滑技術なども、半導体分野など真空応用への展開が可能であろう。トラブルを乗り越えた「はやぶさ」の高信頼性技術の応用展開を期待するとともに、「はやぶさ」のがんばる姿から、わが国ものづくり産業の力強さが再認識された。
第95回 機械要素技術展にみるドライ潤滑技術
第95回 機械要素技術展にみるドライ潤滑技術 機械要素、加工技術を一堂に集めた専門展「第14回機械要素技術展(M-Tech)」が6月23日~25日、東京・有明の東京ビッグサイトで開催された。今回は、従来からのモーション技術、モータ、油空圧機器、機構部品・関連製品、ねじ・締結技術、ばね、機械材料・加工技術、表面処理・改質、試験・計測機器/センサ、バリ取り・表面仕上げ、工具の11の専門フェアに加えて、洗浄、大物・厚物加工、微細・超精密加工、部品供給・検査の四つの専門フェアが新設、さらに医工連携の流れを受け、医療機器を開発、製造するための部品、装置などの専門展「医療機器 開発・製造技術EXPO」が新設された。この医療機器に代表されるように、今回の展示では、機器を無潤滑で稼働させる技術が目立った。
提供:THK たとえばTHKでは、油が使えない高真空環境下(~10-6[Pa])での仕様に最適な特殊環境用オイルフリーLMガイド(直動案内)を出展、転動体に新開発の固定潤滑S膜を使用することでグリースを排除、構成部品をオールステンレス材としたため、半導体製造装置などでの低アウトガス・低発塵を実現する。
提供:南海精工所 南海精工所では、SUS440Cステンレス鋼を使用することで腐食環境、クリーンルームや食品機械などに使える調心機能付きステンレスベアリングを出展した。搬送ローラなどの軸のたわみや取り付け不良などで生じる軸心の誤差を調心し、軸受への異常な負荷を減らす。密閉装置としてシール、シールドを使用しつつ、食品機械用NSF-H1(食品と偶発的に接触する可能性のある箇所で使用が認められている潤滑油)グリースや低発塵グリース、フッ素グリースを封入することで食品機械や半導体製造装置などに使用できるが、さらに油を嫌う環境ではグリースを使わず固体潤滑剤を使用、低摩擦のセラミックボールやフッ素樹脂シールなどの仕様で無潤滑を実現する。
提供:鹿島化学金属 鹿島化学金属では、食品機械の搬送コンベア用ステンレスベアリングに替えて、無潤滑仕様の樹脂で食品にも安全なPEEK材を使用したプラスチックベアリングを出展した。同様に水中や溶液中で使える、PEEKなど無潤滑エンプラを使ったスプロケットも出展、近く販売を開始する予定という。
提供:三和油脂 日清オイリオグループでは先に植物油由来の食品機械用潤滑油を開発しているが、今回、三和油脂と東北大学・堀切川一男教授(開発当時は山形大学)が共同開発した脱脂米ぬかを原料とした硬質多孔性の炭素材料「RB(Rice Bran)セラミックス(RBC)」を販売することを打ち出した。毎年発生する農業系植物資源(米ぬか)を有効利用し、廃棄しても自然環境に害を与えないエコマテリアルであるRBCは、軽量で高強度、高硬質、低摩擦、優れた耐摩耗性を示すため、水のかかる環境や油が嫌われる環境で使われる無潤滑のすべり軸受の摺動材として、実績を持つ。
提供:NSKマイクロプレシジョン また、今回新設された「医療機器 開発・製造技術EXPO」では、NSKマイクロプレシジョンが、従来のステンレス鋼SUS440C以上の高耐食性を示す4化学成分の適性添加と微量元素を調整した新開発材料(TBN-6)に独自熱処理技術を施した高耐食ベアリングを展示した。化学薬品などで侵食されやすい医療器具や精密機器、屋外で使用される機器のほか、塩水にさらされる船舶や釣具など広範な用途で、無潤滑で高い機械的性質を発揮する。住鉱潤滑剤では「機能部品・関連製品フェア」で潤滑性、耐食性、耐薬品性、耐熱性などの複合機能をもつ高機能ドライフィルムを展示していたが、この「医療機器 開発・製造技術EXPO」の出展社・来場者からも注目を集めたという。
半導体やフラットパネルディスプレイ、太陽電池など特殊環境となる製造工程が増えてきているなか、また医療分野での生体適合性など人にやさしい機械技術が求められるなか、昨今話題のダイヤモンドライクカーボン(DLC)コーティングだけでなく、各種ドライ潤滑技術の適用はますます広がってきている。
第96回 JX日鉱日石が誕生、総合エネルギー企業に求められる省エネ・環境対応の新技術
第96回 JX日鉱日石が誕生、総合エネルギー企業に求められる省エネ・環境対応の新技術提供:日鉱日石エネルギー
JXホールディングス傘下の石油事業会社である新日本石油とジャパンエナジーが7月1日に統合、下流の石油精製事業や新エネルギーなどを受け持つJX日鉱日石エネルギー、上流の石油開発を受け持つJX日鉱日石開発が誕生した。民族系石油元売り同士の大型統合は、1999年の日本石油と三菱石油の合併以来で、JX日鉱日石エネルギーの燃料油の国内シェアは35%、潤滑油の国内シェアは4割強となる。同社では成長分野として潤滑油や、パラキシレンなどの石油化学、エネファームなどの新エネルギーなどに注力する意向だ。
このうち機械全般に関わる事業は、機械を円滑に動かす潤滑油。「機械の血液」とも言われる重要な基盤技術であることは論をまたないだろう。
先述のとおり、JX日鉱日石エネルギーは潤滑油の国内シェアが4割強となるため、同27%程度の出光興産を大きく引き離すこととなる。2008年世界潤滑油販売ランキングでは10位が出光興産、12位が新日本石油となっているが、統合によりこのランキングにも変動がありそうだ。しかしこうした中、2位の出光興産でも2012年度の世界販売量を2009年度比3割増の110万kLに拡大する計画を打ち出すなど、明らかに競争が活発化してきている。
さて、第88回で出光興産がトラクションドライブという新しい無段変速機構を機能させるトラクションオイルという高機能潤滑油を手掛けていることを紹介したが、もちろんJX日鉱日石も、様々な先進潤滑油技術の開発に余念がない。
たとえば旧ジャパンエナジーでは、早くから代替フロン冷媒に対応する冷凍機油に強みを持つが、その合成油研究の流れであろうか、ハードディスクドライブ(HDD)でディスクを高速・高精度に回す流体動圧軸受(FDB)用オイルを手掛けている。FDBは、適正な粘度を持つ流体潤滑膜を形成することで軸と非接触で回転する。FDB用オイルには、粘度上昇でモーターの電流値が上がらないことや蒸発しないことなど多様なニーズに対応している。
焼結含油軸受(提供:ポーライト) 最近では、やはりパソコンのファンモーターなどで、主軸の焼結含油軸受に含浸する熱可逆性ゲル状潤滑剤を開発している。通常の含浸油では軸受の運転に伴い高温化して蒸発、流出して軸受寿命に至る。これに対しゲル状潤滑剤では、高温の駅状態で含浸、常温では半固体状のため流出消耗しにくく低摩擦特性も付与するため、モーターの省電力化、長寿命化に貢献するという。
提供:日産自動車 また、旧新日本石油ではかねてからエンジン油や駆動油など輸送機器用潤滑油に強いが、エンジンの省燃費化を目的にカムシャフト/バルブリフター間の摩擦を低減すべく適用が始まった水素フリーのダイヤモンドライクカーボン(DLC)コーティングに最適なエンジン油(図では、「超低フリクション皮膜」と記述)を開発している。省燃費油で一般的なモリブデン系添加剤を含まずエステル系添加剤を用いることで、DLC被覆バルブリフターと組み合わせて約2%の燃費向上が得られている。すでに日産車60万台/年に採用、CO2排出低減に貢献している。
さらに自動車電装機器でも、日本精工と共同でオルタネータや電磁クラッチなど電装補機に使われる軸受向けに、ナノカーボン粒子を配合することで早期はく離(帯電による白色はく離)を防止、白色はく離寿命を10倍以上延長したほか、独自増ちょう剤により軸受温度180℃での焼付き寿命を従来比2倍に高めた長寿命グリースを開発している。いずれも日本トライボロジー学会技術賞を受賞している。
これら両者の保有する独自潤滑技術のシナジー効果で、さらに機械の省エネ稼働を実現しつつ環境に優しい潤滑技術の開発が促進されることに期待したい。
今回までJX日鉱日石エネルギーでは余剰な石油精製設備を削減、現在の精製能力の1/3にあたる日量60万バレルの削減を打ち出す一方で、JX日鉱日石開発では、石油開発日量20万バレル(現在比6万バレル増)を目標に掲げている。石油開発ではこの4月にBPが米メキシコ湾で原油流出事故を引き起こしているが、今回誕生した上流から下流までを手がける「和製メジャー」では、地球の有限な資源を有効活用する務めを担う総合エネルギー企業として、環境負荷が少ない資源開発に努めつつ、潤滑油や燃料電池、ヒートポンプなど省エネに貢献する技術の開発に努めてほしい。
第97回 知財戦略推進で産業競争力の向上を
第97回 知財戦略推進で産業競争力の向上を提供:アップル 米国アップル社の新型マルチメディア端末iPadが先ごろ日本などで発売されたが、中国では早くから店頭やネット上で類似品が出回っている。おしなべて本物の最低価格499ドル(約4万5000円)より2割程度安いようだが、APadなる商品はなんと900元(1万2000円)程度からという激安ぶりだ。かの国では知的財産権(知財権)も何もあったものではないだろうと思いきや、知財戦略が急速に進んできているという。特許出願件数は米国が年に約40万件、日本が同30万件程度なのに対し、中国では約22万件に拡大してきている。欧州を抜き、日本に迫る勢いである。
知財は無体財産権といい、国が新規・進歩性のある発明と認める「特許」、同じく新規・創作性のある工業デザインとして認める「意匠権」、差別化された商品ブランドとして認める「商標権」など、工業所有権に分類される。工業所有権とは国が、一企業が独占することを認める権利で、独占禁止法においても正しい特許法の使い方なら独占して構わない、とのスタンスをとる。独占を認める背景には、特許権が20年で満了という時限効力の権利だという事情がある。つまり企業はこの期間内に研究開発、製品化に要した費用を回収しなくてはならない。売上ランキング上位にあった武田薬品が2009年3月期に純利益26%減の赤字に陥ったのは、主力薬品の特許ぎれで安価なジェネリック薬品に市場をさらわれたことが響いた。
このことが示すのは、知財が競争力を確保し、競合他社の市場参入を抑制し、価格競争に陥らず利益を向上させる役割を果たすということだ。特許が切れれば、たちまち価格競争が始まるのである。そこで知財を有効活用した経営戦略としては、事業戦略、研究開発戦略、知財戦略の三位一体で取り組む必要がある、と弁理士の相川俊彦氏(オリオン国際特許事務所)は言う。機械産業では当たり前のことだが、弛みない研究開発が不可欠であり、この研究開発の方向性を決める上でも知財を利用しようというわけである。
相川氏は、特許調査により自社のビジネスに影響する他社特許を把握することを勧める。「たとえば潤滑関連の特許をみると、油潤滑に関するものが約1万件、グリースは500件強、非油脂が300件弱、装置関連が3000件強、特殊条件下が50件弱、軸受など機械要素の潤滑は約1万5000件にものぼる。ここから、機械要素の潤滑や潤滑油を攻めるよりも、グリースや非油脂、中でも特殊条件下で使えるグリースや非油脂の研究開発のほうが参入が少なく、産業競争力が付けられそう」というわけである。機械要素関連のビジネスでは、小社『Bearing & Motion-Tech(BMT)』の特許情報もぜひ活用していただきたい。いずれにしても、知財戦略は、時機をとらえて、自社の優位性を出せるビジネスを選択、経営資源を集中させて、進めたい。
中国での日本製ボールベアリングの偽造品流通が依然問題になっているが、今や市場が拡大基調にある中国など新興国での事業展開・拡大は避けられない。しかし一方で、海外展開では製品・技術が模倣される危険性を常にはらんでいる。そこで一歩先を行く知財(特許)戦略が求められる。大手企業では早くから取り組んでいようが、知財戦略は中小企業にこそ必要な手段となろう。近年では知財を担保に融資を受け、事業を増強している例もある。技術優位性のある知財を保有していれば、中小企業にもグローバルで勝負できる。
世界市場においてわが国の製品・技術が価格競争に陥ることなく、産業競争力を高められるよう、知財戦略のさらなる推進を期待したい。
第98回 7/29~30開催 DISKCON JAPAN 2010に見るデータストレージのこれから
第98回 7/29~30開催 DISKCON JAPAN 2010に見るデータストレージのこれから提供:Seagate 米国ドライブメーカーのシーゲイト社では先ごろ、世界初3テラバイト(TB)の記録密度を持つ外付けのハードディスクドライブ(HDD)を市場に投入した。3TBがどの程度の容量かというと、120タイトルのHDムービーと1500のビデオゲーム、数千点の写真、音楽をいれられるそうである。この大容量化し続けるHDDの業界唯一の総合イベント「DISKCON JAPAN 2010( http://www.idema.gr.jp/diskcon )」が、IDEMAJAPAN( http://www.idema.gr.jp )主催で開かれる。最新のストレージ関連製品・技術の展示会と、市場動向・技術動向に関する講演会「国際ディスクフォーラム」の同時開催となる。
さて、HDDの大容量化を支えるメカニカルな技術としては主に、記録媒体であるディスク(HD)を回転させるスピンドルモータ、ディスク上で記録再生を行うヘッドスライダー、それを支えるサスペンション、ヘッドの位置決めを行うボイスコイルモータなどがある。
HDDでは、回転するディスク上に記録再生素子(磁気ヘッド)を搭載したスライダーを浮上させて記録再生を行うため、記録密度を向上させるには、ヘッドとディスクの浮上すき間を低減する必要がある。現在この浮上すき間は10nm(1nmは10億分の1m)を切るレベルまできており、ディスクとスライダーが接触する可能性が高まってきている。この接触により磁気記録層にダメージを与えデータが破壊されることのないよう、ヘッドおよびディスクに低摩擦で耐摩耗性の高いDLC(ダイヤモンドライクカーボン)などのカーボン系保護膜がコーティングされ、さらにディスク保護膜の上には1分子層の潤滑油膜が形成されている。現在4~3nmの保護膜についても1nm薄くするだけで記録密度向上に利いてくることから、FCA(真空中でのアーク放電によりプラズマ化したカーボン粒子を表面に堆積させる)成膜技術により2nmの保護膜を形成する研究開発なども進められている(富士通研究所、フェローテック)。
たとえばサーバ向けで15,000回転という高速スピンドルモータでは、高トラック密度化が進む中、かつてのボールベアリングに見られる回転に同期しない振れ(NRRO)がない流体軸受が使われている。流体軸受のスリーブでは、動圧を発生させるヘリングボーン溝の加工技術や作動オイルの技術が今なお開発・改良されている。
また磁気ヘッドを取り付けたアクチュエータの支点部分に使用されるピボット軸受では、攪拌抵抗が少なく、また揺動によるフレッチング摩耗を防ぐグリース技術や、耐久性を高めるボールや保持器の技術が適用されている。
日立グローバル ストレージテクノロジーズや東芝ストレージデバイスなどドライブメーカーはもとより、これらHDD部品における日本メーカーの技術優位性は高く、たとえばスピンドルモータでは日本電産やミネベア、ピボットベアリングではミネベアや日本精工、ディスク(HD)では昭和電工や富士電機デバイステクノロジー、HOYA、ヘッドではTDK、サスペンションではニッパツなどが、世界的にも高シェアを占める。
今回開催されるDISKCON JAPAN 2010の主催者IDEMA JAPANは、こうしたドライブメーカーや部品メーカー、材料メーカー、製造装置メーカー、試験評価機器メーカーなどが参加、ディスクドライブ業界の健全な発展と交流促進を目的に、最近ではHDDの信頼性を脅かすイオン性のマイクロコンタミネーションを測定・評価する改訂案を提起、10年ぶりに新しいグローバルスタンダード(イオンコンタミ測定)を成立させるなど、業界のデファクトスタンダードの確立にも取り組んでいる。
さらにIDEMA JAPANでは、HDDの市場を脅かすといわれてきたSSD(メモリー媒体の記録装置:ソリッド・ステート・ドライブ)メーカーも加え、活動を広げている。IDEMA JAPAN専務理事の安達三郎氏は、「今回のDISKCON JAPAN 2010でもSSDの技術やアプリケーションに関する一大セッションを設けている。HDDは大容量、SSDは安価でコンパクト、大データ転送などが得意と、すみ分けが明確化してきており、SSDの採用拡大と同時に、信頼性、大容量化による低価格化など、HDDの今後の課題も具体化してきている」と語る。
パソコン向けのほか、カーナビゲーションシステム、HDDレコーダー、ゲーム、さらにはクラウドコンピューティング、グリーンITなどアプリケーションが拡大するなか、DISKCON JAPAN 2010を通じて、HDDやSSDなどデータストレージの方向性をじっくりと見てみたい。
第99回 HEV・EVの普及拡大で求められるメカニカル試験評価
第99回 HEV・EVの普及拡大で求められるメカニカル試験評価 富士経済では先ごろ、ハイブリッド車(HEV)、電気自動車(EV)、プラグインハイブリッド車(PHEV)の3種を「エコカー」と定義、2009年のエコカー世界市場が前年比44.2%増の76.3万台となったのに対し、2010年は100万台突破、2015年には500万台超え、2020年には1,800万台超えとなる予測を発表した(「2010版HEV,EV関連市場徹底分析調査」)。
内燃機関からHEV、EVなどに至る自動車技術のパラダイムシフトに対応して、新しいパワートレインのための試験評価技術が近年、注目されてきている。こうしたニーズをとらえ英国UKIP Media & Events社では本年、インド、ドイツ、中国、米国で4回にわたり、自動車の各機性能試験評価機器の総合展「Automotive Testing Expo」を開催する。
さて、従来の内燃機関が600~8,000rpmの領域で回しているのに対し、HEVやEVのモータ・ジェネレータでは始動の0rpm~20,000rpmまでの幅広い回転領域で、正確に、より省エネに回さなくてはならない。また、モータ・ジェネレータでは小型・軽量化しつつ高速回転させて馬力を稼ぐ発想となるため、内燃機関に比べはるかに高い減速比となり、歯車には極めて過酷な条件となる。
それらHEV・EV特有のニーズに対応した試験評価機器の開発も本格化してきている。たとえばスペースクリエイション(http://www.spacecreation.co.jp)では、青木邦章社長がヤマハ発動機で舶用ディーゼルエンジンの開発・設計に長年携わった経験から、自動車分野を主に各種開発試験機を開発しているが、近年ではHEVやEV、メカニカル・ロス低減といった自動車のニーズに対応した試験評価装置の開発を進めている。
先述のHEV・EV用モータの運転ニーズに対応して、モータ・ジェネレータ用高速モータリング装置(MED-10)を開発、販売を始めた。モータ・ジェネレータを0rpm始動から25,000rpmという高速で力行/回生運転するほか、連続定回転運転、パターン運転、急加減速運転などに任意に対応、正確に、より省エネに回すという実機に近い評価試験を可能にしている。提供:スペースクリエイション また、HEV・EV用モータではエンジンに比べはるかに高い減速比となり歯車にとって過酷な条件となると述べたが、実機に近い環境で高減速比の歯車を評価する動力循環型モータリング装置(MRP-20)を開発した。独自開発の油圧サーボアクチュエータによりねじり荷重を発生させ、運転中でも荷重負荷を任意に変更でき、変動荷重負荷を与えることもできる。
これら新しいパワートレインに対応する試験装置はすでに国内自動車メーカーで適用が進んできているが、「中国など新興国を中心に海外自動車メーカーへのアプローチも始めている」(青木社長)という。中国などの現地企業の自動車では、排出ガス規制対応車両と謳ったものでも、生産技術が安定していないためか、規制値をクリアしていない車両も流通しているのが、現状。それでもHEV・EVの開発はすでに盛んで、ギヤの静音化など日本よりも厳しい要求も出てきている。
HEV、EVの信頼性を支え、それらの市場拡大を支える試験評価機器の開発は、グローバルで強く求められてきている。
第100回 MEMSビジネスを支えるメカ技術
第100回 MEMSビジネスを支えるメカ技術 世界最大規模のMEMS(微小電子機械)、超精密・微細加工、ナノテクノロジー、バイオに関する国際見本市「第21回マイクロマシン/MEMS展」が7月28日~30日、東京・有明の東京ビッグサイトで開催された。MEMSの基盤技術でもある表面技術の総合展「SURTECH2010」とMEMSの応用分野である次世代ロボットの製造技術展「ROBOTECH」が併せて開かれた。
提供:NEDO MEMSは、半導体製造技術やレーザ加工技術など、各種微細加工技術を応用し、微小な電気要素と機械要素を1つの基板の上に組み込んだセンサ(振動や動きなどを感知するしくみ)やアクチュエータ(機械を正確に稼働するしくみ)などのデバイス・システムをいう。MEMSは半導体製造技術を使って、機械的な部品を作ることからスタートした技術で、シリコンなどの半導体基板上に、3次元的可動構造体を利用したセンサやアクチュエータを形成する。半導体が「産業のコメ」と呼ばれるのに対し、マメの主成分であるたんぱく質が目や耳などの感覚器官や筋肉とあらゆる情報を認識し、行動を起こす器官を構成することがMEMSの機能そのものであることから、MEMSは「産業のマメ」とも呼ばれる。
機械の小型化・集積化を図れることが最大の特徴で、機械を微小化すると軽量化、省スペースだけでなく、省資源、省エネルギーが図れる、感度を高くできる、といった多くのメリットが得られる。またシリコン単結晶などの機械的特性に優れた材料を使用するため、製品の信頼性が向上する。
Wiiコントローラ(提供:任天堂) こうした特性に優れるMEMSの応用例として、たとえば任天堂のテレビゲーム機「Wii」の手の動きで操作するコントローラ用3軸(X、Y、Z)ジャイロセンサでは、幅広い検出範囲、高い他軸感度、高い耐振動性、耐機械的衝撃性、コントローラの小型化を実現している。また、モバイル機器に搭載されるハードディスクドライブ(HDD)のヘッドに3軸加速度センサを搭載することで、万が一機器が落下したときでも、落下を検知しヘッドをディスクから待避させデータを保護する。
自動車のハブベアリングユニットなどに搭載される加速度センサ、角速度センサなどのMEMSセンサは、車両の統合安全制御に貢献している。
さらに携帯電話等のモバイル機器の高周波部品をMEMS部品に置き換えることで低消費電力、低コストで数十GHzの通信帯域を実現するRF-MEMS、光通信網で用いられる従来の光電変換型のスイッチに比べ、省スペース、省エネルギー、低コスト化の効果が得られる光MEMSなどの適用も広がってきている。
さて、MEMSにはシリコン系基板への成膜、フォトリソグラフィー、基板および薄膜のエッチング、接合(ボンディング)といった基本的なプロセスフローがある。今回の展示会ではそれぞれについて開発、研究成果が示された。
信頼性の高いMEMS製品を作るには機械的に信頼性のある膜が成膜される。メンブレン構造の場合、シリコン基板をベースにシリコン酸化膜層や窒化シリコン層、クロムやタングステンなどの金属薄膜といった積層構造をとる。ここでは厚い金属膜が堆積されることが多く、PVDやCVDより成膜速度が速いメッキや電鋳がよく利用される。同時開催のSURTECHでは、ナノスケールでの制御を実現するメッキプロセスを用いたMEMS作製が多数提案された。通電して金属などを析出させる電解メッキはすでにMEMSで多用されている。
提供:住友精密工業 また、シリコン基板のエッチング技術としてSi深掘り装置が住友精密工業などから展示された。シリコン基板に細い溝を深く形成するもので、溝の深さと幅の寸法比(アスペクト比)を大きくできることがポイント。 一般にシリコンは深く掘るにつれて横方向にも削られるという問題があるため、高アスペクトで深堀りする技術が求められている。同社では100μm/min以上の高エッチレート加工を実現した。
MEMSの構造材料として用いられるシリコン系材料に加えて、金属ガラスなどの適用も検討されているが、脆性のため短時間・低コストで三次元形状の構造材を作製することがこれまで難しかった。これに対しレーザフォーミングという、材料表面にレーザを照射して局部加熱による熱応力で塑性変形させる方法も提案されている(熊本大学 高島・大津研究室)。
MEMSの高機能化の技術としては、立体形状自由加工技術(立体構造上へのパターン形成技術)のほか、ナノ機能材料選択的形成技術(ナノ材料局所形成技術)、機能性表面形成技術(化学的・バイオ的表面修飾技術)などが、低コスト化に資する技術としてはマイクロプレス成形技術(ナノインプリンティング技術)やパッケージ技術(高度実装技術)などが、技術基盤の確立として、各種シミュレーション技術(プロセス解析技術)、多品種・少量・省エネ・フレキシブル加工技術などが挙げられている。いずれも微細加工技術のさらなる進展が中心となろうが、表面改質技術も機能性表面を作る上で重要と言えそうだ。
わが国のMEMS市場は単体・応用製品を含め2005年度で約4,400億円。これが2010年には1兆円規模に、高集積化・複合化が進み2015年には2兆4,000億円規模にまで拡大していくと予測されている。さらに2025年以降には、ガンや肝炎にかかった人たちが常にセンサを身に付けて自分の体をモニターすることを可能にするようなバイオMEMSなども後押しして、市場は10倍近くに拡大するとも見られている。上述のような加工・表面改質、さらには解析、試験・計測・評価技術を含めたメカ技術の課題克服で、MEMSビジネスの拡大を促進してほしい。
第101回~第110回
第101回~第110回第101回 わが国技術の発信で、インフラ関連プロジェクトの獲得を!
第101回 わが国技術の発信で、インフラ関連プロジェクトの獲得を!リニアモーターカー(提供:JR東海) 経済産業省( http://www.meti.go.jp )は、本年6月策定の「産業構造ビジョン2010」で提言されたインフラ・システム輸出に関する総合的な戦略を官民連携で策定する目的で、「インフラ・システム輸出部会」を設置した。鉄道、航空宇宙、原子力、水ビジネスなどの主要団体トップや有識者が集まって、インフラ関連産業の海外展開のための総合戦略やインフラ・システム輸出を進めるにあたっての官民連携のあり方などについて意見交換していく。
産業構造ビジョン2010では、2020年までに海外分を含めて19兆7,000億円の新市場と18万7,000人の新規雇用を創出する目標を掲げている。その中でインフラ・システム輸出は重要な戦略分野の一つに位置づけられており、政府がインフラ関連プロジェクトの受注などに積極的に関わるべく、今回インフラ・システム輸出部会が設置された。
たとえば鉄道分野では、米国(全長1300kmのカリフォルニア高速鉄道網など)やメキシコ、ベトナム、中国、インドネシア、タイなどで高速鉄道の建設が計画されている。鉄道車両はCO2排出量が少ない大量輸送手段として世界的に重要性が見直されているが、自動車などによる輸送を鉄道で代替する「モーダルシフト」はオバマ政権が5年間で130億ドルを投入する方針を打ち出すなど、特に米国で急速に進み、新幹線(N700Iブレット)やリニアモーターカーなど日本の高速車両技術が求められている。
新幹線を見ると最新のN700系で時速300kmと高速化が加速する一方、この環境対策からは、安全性を確保した上でのメンテナンス周期の長期化が図られているが、鉄道の輸出においても、新幹線の開発で培った、安全で環境に優しい高速化の技術を全面に打ち出す必要があろう。
たとえば鉄道車両用軸受のうち車軸用軸受は、軸を直接支持し、また線路からの振動が直接伝わる過酷な環境下で使われ、かつ転がり疲れ寿命の長寿命化が求められている。そのため欠陥につながる介在物の少ない高清浄度鋼が使用されているほか、潤滑寿命の延長からは封入グリースの改良とともに、樹脂製保持器を採用して摩耗粉を抑制している。主電動機(モーター)軸受には60~90kmで中間給脂が行われているが、120万kmへのメンテナンス周期延伸のニーズに対し、長期グリース補給を維持できるグリースポケット形状などの工夫がなされている。センサー組込みによる運行中の軸受のモニタリングシステムなども、メンテナンス周期の長期化や安全性向上では重要な役割を担う。
このほか、列車の走行に必要な電流を流す電気的特性、パンタグラフとの接触力変動が少ない良好な接触を保つための機械的特性、摩耗しにくく破断することのない材料的特性が求められるトロリ線や、機械的特性や摺り板が摩耗しにくく破損せずトロリ線を摩耗させない材料的特性、風を受けることで発生する揚力が適切で、風を切ることによる騒音が小さいなどの空力的特性が求められるパンタフラフなど、高速車両の信頼性を高める技術は枚挙にいとまがない。すなわち、鉄道の輸出とは、これら車両の機械技術や安全で省エネな運行・管理のためのエレクトロニクス技術などを統合して提供する必要があるということだ。
ここにきて新幹線の技術をもとに製造された中国の高速鉄道の輸出が加速してきているようだが、日本が1964年以来の安全で信頼性の高い高速化技術を着実に積み上げてきたのに対して、中国は10年程度の経験しか持たない。コストはいざ知らず、統合力では圧倒的に日本がリードしているはずである。
これは鉄道に限らず原発や航空宇宙、水ビジネスなどでも同様であろう。多岐にわたる機械技術や電気・電子技術が集積されたこれら産業の輸出において、いかにわが国技術の優位性を前面に打ち出してプロジェクトを獲得し、先述の市場および雇用の創出につなげていくか、今回誕生した経産省インフラ・システム輸出部会の今後の取組みに、強く期待したい。
第102回 ラベリング制度の普及で、タイヤの安全性向上と低燃費化技術に拍車
第102回 ラベリング制度の普及で、タイヤの安全性向上と低燃費化技術に拍車提供:日本自動車タイヤ協会 自動車のタイヤ性能に関するラベリング制度の導入が世界的に進んできている。本年1月に運用を始めた日本に続き2011年には韓国で、2012年には欧州で導入が予定されているほか、米国でも導入が検討されている。同制度の性能要件であるタイヤの低燃費化への要求が新興国も含めて強まってきている。
タイヤの燃費への寄与率を10%と仮定した場合、転がり抵抗を20%低減したとすれば自動車の燃費は2%向上する計算となる。このため近年タイヤに対しても低燃費化の要求が高まっていることから、各タイヤメーカーではこれまで独自基準の性能評価による低燃費タイヤを販売してきた。これに対しタイヤラベリング制度は、統一された試験方法により実証されたタイヤ性能を消費者にわかりやすく示し、低燃費タイヤの普及促進を図るねらい。国内では日本自動車タイヤ協会( http://www.jatma.or.jp )が本年1月から業界の自主基準として乗用車用夏用タイヤを対象に「低燃費タイヤ等普及促進に関する表示ガイドライン(ラベリング制度)」の運用を開始している。
同制度では、低燃費を示す転がり抵抗係数(RRC、単位N/kN)を
(1)グレードAAA:RRC≦6.55
(2)グレードAA :6.6≦RRC≦7.7
(3)グレードA :7.8≦RRC≦9.0
(4)グレードB :9.1≦RRC≦10.5
(5)グレードC :10.6≦RRC≦12.0
の5等級で、制動の安全性を確保するウェットグリップ性能(G、単位%)を
(1)グレードa:155≦G、
(2)グレードb:140≦G≦154
(3)グレードc:125≦G≦139
(4)グレードd:110≦G≦124
の4等級で表示。転がり抵抗係数は「JIS D4234(乗用車、トラックおよびバス用タイヤ-転がり抵抗試験方法-単一条件試験および測定結果の相関): 2009(ISO28580)」により、ウェットグリップ性能は「EU 規則 Wet Gripグレーディング試験法(案)(TEST METHOD FOR TYRE WET GRIP GRADING (C1 TYRES))」により評価、ウェットグリップ性能110以上(グレードa~d)、転がり抵抗係数9.0以下の上位3等級(グレード AAA~A)を満たすタイヤを、「低燃費タイヤ」と定義している。
タイヤの転がり抵抗には、(1)走行時のタイヤの変形によるエネルギーロス、(2)トレッドゴムの路面との接地摩擦によるエネルギーロス、(3)タイヤの回転に伴う空気抵抗によるエネルギーロスがあるが、ゴム(粘弾性体)に加えられた力は、変形により熱に変換されエネルギーを消費してしまうことから、これらの要因のうち、タイヤの転がり抵抗にはタイヤ変形の影響が大きい。
これに対し横浜ゴムでは、タイヤの内部に貼り付けて自然と起こる空気漏れを抑制するインナーライナーに、樹脂の低透過性とゴムの柔軟性を高次元でバランスした従来品の5分の1の薄さの新素材を適用、タイヤの空気漏れによる転がり抵抗の悪化抑制と軽量化による燃費向上を図っているほか、接地摩擦によるエネルギーロスの低減からは、コンパウンドをナノレベルで解析、天然ゴム+低発熱ポリマーを適用し転がり摩擦抵抗を低減し低燃費性能を向上している。
提供:ブリヂストン また、ブリヂストンでは、ブロックを路面に水平に接地させトレッドショルダー部の無駄な変形を抑制したほか、従来のトレッドゴムに配合されていたカーボン同士が擦れ合ってエネルギーロスが発生していたのに対し、カーボン粒子をナノレベルで調整し分散、カーボン同士がぶつかり合って起こる発熱を抑制、エネルギーロスを低減し転がり抵抗を抑えている。
提供:日本自動車タイヤ協会 しかし一般的に、タイヤの転がり抵抗を低減すれば、濡れた路面での制動距離(ウェット制動距離)が伸びるというように、転がり抵抗係数とウェットグリップ性能はトレードオフの関係にある。つまり、適正範囲を超えて空気圧を上げたり材料技術などで転がり抵抗をやみくもに低減することは、トレードオフとなるウェットグリップ性能の低下、つまり自動車の安全性を損なうこととなる。そこで、転がり抵抗低減の一方で、タイヤのトレッドパターン(溝の形状)による排水性の改善など、ウェットグリップ性能の向上が図られている。
提供:日本ミシュランタイヤ たとえば日本ミシュランタイヤではセンター部に配置したストレートグルーブや独自のサイプ技術により、雨天時も優れた排水性とグリップ性能を発揮しているほか、横浜ゴムではゴムをしなやかにしてグリップ力を高めるオレンジオイルなどの配合により、ウェットグリップ性能を高めている。
タイヤによる燃料消費量低減の効果が大きいことから、ガソリン高の中国で価格が割高であるにもかかわらず低燃費タイヤが注目されるなど、その市場は確実に成長してきている。電気自動車においても自動車の安全性、操縦快適性などに関わるタイヤの役割は変わらない。むしろ、バッテリーやモータ・ジェネレータの負担軽減などからは、タイヤの転がり抵抗低減への要求は、より高まっていくことだろう。タイヤのラベリング制度が世界的に普及し、低燃費タイヤの需要が拡大していくなか、安全性を確保するウェットグリップ性能を向上した上での、タイヤの転がり抵抗低減のさらなる取組みに期待したい。
第103回 ACTA構想に技術製品の安全信頼性確保を期待
第103回 ACTA構想に技術製品の安全信頼性確保を期待 経済産業省( http://www.meti.go.jp )と外務省は8月16日~8月20日、米ワシントンで開催された模倣品・海賊版拡散防止条約(ACTA)の第10回関係国会合の概要を公表した。参加国は、我が国をはじめ、米国、EU、スイス、カナダ、韓国、メキシコ、シンガポール、豪州、ニュージーランド、モロッコ。今回の会合では、次回会合を本年9月に日本で開催し残された実質的論点を解決すること、署名の前に条約の全条文を公表することなどの合意をみた。
ACTA構想は、2005年に当時首相だった小泉純一郎氏が模倣品・海賊版拡散防止のための法的枠組みの必要性について発言したことを機にスタート、2008年6月には現在の11ヵ国が参加した関係国会合が開催、条文案をベースとした本格的な議論が始まった。そうした経緯からも、今回の会合でも、わが国がACTAの早期実現を目指し、今後も関係国との議論を積極的にリードしていく姿勢を示した。
模倣品・海賊版による被害は世界で年間80兆円に上り(世界税関機工および国際刑事警察機構資料より)、国際貿易に限定しても20兆円以上に達する(OECD資料より)という。ACTAが指摘しているのは、「模倣品は安全性や耐久性に問題を抱えているものが多くあり、こうした模倣品は誤って購入した消費者に危害を加える上に、企業の信頼を損なうおそれがある」ということである。模倣品が引き起こすおそれのある被害と商品分野の例として、加工精度や材料の品質が低劣なことによる装置・部品の故障・破壊の被害をもたらすベアリングや自動車部品を挙げる。
WBA京都設立総会(提供:日本ベアリング工業会) 実際にベアリングの分野では1990年代の終わりから、ブランド名を使用することでメーカー品と誤解を招きかねないようなベアリング製品がアジア、中近東、中南米、アフリカなどに多数流通、問題化してきている。これに対して、日本ベアリング工業会では、「こうした偽造品は、わが国ベアリングメーカーの知的財産権を侵害するばかりでなく、品質面で問題があるケースも多い。これらを使用した自動車や電気製品などは早期破損に繋がる可能性が高く、消費者や工場の作業者などを危険にさらすことになるほか、機械の突然停止による生産効率の低下、メンテナンスコストの増大など経済的な損失を招くことも少なくない」との危惧を表明、不正商品の生産拠点があると思われる中国に2000年11月末に第1次ミッションを派遣、以来2008年までに第8次ミッションを派遣し、中国政府機関に対して、不正なベアリングによる身体、生命への危険性を訴えながら、その製造・販売の撲滅に向け取締りの要請を行うなどの対策に努めている。
こうした努力が結実して海外の偽造品に対する抑止効果を発揮、偽造品の流通量は減少に向かってきていたが、2008年後半からの世界同時不況を契機に大量の在庫が発生したため、再び偽造品の製造が復活し始めたという。
一方、タイでは2005年ごろからタイ政府の強力なバックアップのもと、偽造品対策を始め、中国同様ミッションを派遣し、日本ベアリング工業会が現地で対策委員会を設け、偽造品の識別方法を伝授するなどして水際対策を強化、当時市場の20%を占めていた偽造品の流通を現在ではかなり低いレベルにまで抑えこんでいる。しかし、今なお中国からの偽造品流入ルートは存在し、タイにおいても、再び偽造品の流通が増えることが懸念されている。
日本ベアリング工業会では、「低価格が売りの偽造品は安価で劣悪な原料や部品が使用され、また製造現場から輸送に至るまでの品質管理がまったくなされていない。わが国製品の権利侵害を訴えるよりも、“偽造品は品質がまったく保証されていないため、ベアリングのユーザーにとって危険きわまりない”ということを前面に訴え偽造品対策に取り組んできた。これからも取組みを強化していく」方針だ。
こうしたベアリング産業の共通の利害問題に対して、日米欧のベアリング工業会が協調して関連法規に基づきながら効率的に対処する目的で、世界ベアリング協会(WBA:World Bearing Association)が2006年9月に京都でWBA設立総会を開催、WBA定款が採択されWBAが設立された。WBAでもこの日本ベアリング工業会の取組みが評価され、偽造品対策が強化されてきている。
しかし、効果を上げてきているとはいえ、先述のとおり特に中国においては「いたちごっこ」の様相を呈しており、業界団体だけの取り組みでは限界があるだろう。世界的な法的枠組みがどうしても必要だ。ベアリングなど技術商品の安全性・耐久性を確保するためにも、模倣品・海賊版拡散防止条約、ACTA構想の実現に強く期待したい。
第104回 海外生産シフトで求められる表面改質・加工技術
第104回 海外生産シフトで求められる表面改質・加工技術日本銀行 経済産業省では先ごろ、円高が企業活動、収益などに及ぼす影響について緊急ヒアリングを実施、結果をとりまとめた。対米ドルが1ドル=85.92円~84.55円、対ユーロが1ユーロ=111.16円~106.74円だった8月11日~8月24日の期間に、足下の円高の影響や、円高が継続した場合の影響、中小企業・下請企業への影響などについて、輸出製造企業を中心とした102社の企業を対象としてヒアリングを行ったほか、各経済産業局を通じ下請企業を含む中小企業98社から現場の「生の声」を聴取、概ね以下の産業界の意向が浮き彫りになった。
輸出型企業、たとえばトヨタ自動車では1円円高に振れると350億円の利益が飛ぶと言われる(1)対ドルの円高で製造企業の約6割強が、対ユーロでは約5割強が「減益」。円高が半年継続すれば、対ドルの円高で「深刻な減益」は1割から3割へと増え、収益の悪化はさらに深刻化。ウォン安により、特に新興国市場で日本企業は韓国企業との競争に苦戦する、と円高が企業の収益を悪化させている状況を示した。
(2)1ドル85円水準の円高が継続した場合、中小企業の約7割、下請中小企業の8割強が「減益」と回答。製造企業のうち4割が「生産工場や開発拠点等を海外に移転」、6割が「海外での生産比率を拡大」と回答。下請企業を中心に、取引先のコストダウン要請、海外企業に奪われ受注が取れなくなる恐れ、取引先の海外移転の影響を懸念する声が多くあり、1ドル85円の円高が継続した場合、国内産業の空洞化がさらに加速するおそれがあるとしている。
自動車など製造業ではすでに為替変動に左右されにくい海外生産へのシフトを進めているが、成長市場である新興国での円高による価格競争力の低下から、企業の海外生産拡大への意向が強まってきているようだ。
現地生産でコストメリットを出すには材料・部品の現地調達率の拡大が不可欠だが、特に中国やインドなど新興国で安定した品質の材料を確保するのは難しいと、某自動車メーカーの関係者は言う。
たとえば、多結晶体である鋼の疲労特性は結晶粒の微細化によって向上するが、この材料の微細構造の制御にばらつきがあるらしく、結晶粒の分散状態が悪く浸炭処理後に結晶粒が粗大化、形状精度のほか製品寿命の低下につながることもあるという。日本同様の仕様の材料が得られない状況に対し、機能に影響しない範囲で仕様を変更する現地リファイン材や現地のスタンダード材料を使おうとする現地調達の考え方がある。いずれにしても素材性能が確保できない状況で信頼性の高い部品としての性能を向上させるには、熱処理を含む表面改質技術や加工技術で不足する部分をカバーする必要があるとメーカーは考える。
イメージ図:ガイドブロックの外側の加工に比べ、内側のボール循環部の加工は製品性能を決める難しさがある(提供:THK) 新興国ではしかし、この加工技術でも安定した品質を得るのが難しいという。直動案内製品の関係者によれば、海外生産にあたっては先述の状況から耐久性や摺動性能に関わる材料については依然として日本から材料を供給した上で、ガイドブロックの外形の加工などは現地のメーカーに委託するものの、内側のボール転動面の加工は日本で行うとのことだ。ボールがなめらかに転がるための表面粗さの確保や転動面の耐久性に関わるダメージのない加工が現地ではまだ難しいようだ。
こうした材料や加工などの技術的な問題が多い中で海外生産を拡大しなければならない状況を止めるよう、円高阻止に向けた政府、日銀の方策に期待したいが、長期的にはやはり海外生産シフトは進む傾向にある。近年、グローバル生産の進展を象徴するように日本車のリコール問題が多発しているが、材料の性能を高めるリファイン技術とともに、それを補い信頼性の高い部品を作る表面改質や加工技術、耐久信頼性・安全性を裏付ける試験評価技術を含めた現地調達システムの確立が急がれるところだ。
第105回 インプラント医療機器を支える表面改質技術
第105回 インプラント医療機器を支える表面改質技術提供:瑞穂医科工業 経済産業省では先ごろ、「平成22年度医療機器分野への参入・部材供給の活性化に向けた研究会」を開催、本年度の活動を開始している。
世界的な高齢化が進展し医療機器市場の大幅な拡大が見込まれる中、2007年4月には文部科学省、厚生労働省および経済産業省によって「革新的医薬品・医療機器創出のための5か年戦略」が策定され、また2009年12月には「新成長戦略(基本方針)」が閣議決定され、ライフ・イノベーションによる健康大国戦略として、医療・介護・健康関連産業の成長産業化が謳われるなど、医療機器産業の活性化はわが国の成長において重要な役割を担っている。
わが国は世界に誇る優れた科学技術やものづくりの力を有し、近年そうした高度な工業技術を活かして医療機器産業への参入を目指す中小企業の動きが活発化してきている。一方で医療機器産業は薬事法をはじめ法律・制度の影響を大きく受ける産業で、また、国際的な規制や品質管理の問題など、医療機器分野への参入には高い障壁があるとの指摘もあり、医療機器産業への参入を促す環境整備が求められている。さらに、医療機器のリスクに対する懸念から、部材供給者が医療機器、特に埋込み(インプラント)型治療機器を中心とする医療機器への部材供給を躊躇しているとの指摘は顕著で、こうした部材供給問題も医療機器産業の活性化の阻害要因の一つとなっている。
こうした指摘に対し経済産業省では2007年度にインプラント型の医療機器などに対する材料や部材の提供を活性化するための方策について、関係業界と共同で検討を開始、2008年度には、現状把握とともに対策の基本的方向性について検討するために、「医療機器分野への参入・部材供給の活性化に向けた研究会」を立ち上げた。本年度は同研究会を継続開催するとともに、医療機器分野への参入方策および部材供給の活性化方策を検討する二つのワーキンググループを立ち上げ、具体的課題の抽出および対応方策に関する議論を深めたほか、医療機器産業の活性化および医療機器産業に参入する中小企業の支援を行う全国の医療機器クラスターを支援するための枠組み構築に向けた活動を展開した。
提供:瑞穂医科工業 整形外科で使用されるインプラント製品である人工関節で最も多い股関節でも、そのほとんどを海外メーカーが占めている。人工股関節は、生体適合性が高く耐摩耗性・低摩擦性に優れる超高分子量ポリエチレン(UHMWPE)製のソケットと、コバルトクロム合金や各種セラミックスなどでできたヘッドとの組合わせからなり、市場で多いのは、メタル・オン・ポリエチレン(コバルトクロム合金などメタルのヘッドとUHMWPEのソケットの組合わせ)だが、瑞穂医科工業では国産技術として潤滑性を持たせたメタル・オン・メタルのシステムを手がけている。メタル材料としては耐摩耗性に優れたコバルトクロム合金が主だが、コバルトイオンの溶出を防ぎつつ生体適合性と潤滑性を高めるコーティング技術として、DLC(ダイヤモンドライクカーボン)など様々なコーティングを適用する研究が行われているという。
しかし人工股関節に要求される寿命30年という長期使用を考えた場合、コーティングの密着性低下による耐久安全性の劣化が懸念される。そこで、微粒子を圧縮性の気体に混合して高速衝突させるという表面改質技術WPC処理を併用することでDLCコーティングの密着性を高める研究も産学共同で進められている。
提供:銀座大幸歯科 また、虫歯などで歯根がなくなった場合に使われる人工歯根というインプラント材料には、噛む力に耐える強度と耐食性、生体親和性に優れた素材が求められる。人工歯根としてはチタン合金母材に母材と同様なチタン材料をプラズマ溶射によって高密着力でコーティングされている。溶射によって表面多孔性構造(ポーラス)にすることによって新生骨が人口歯根表面ポーラスに侵入し、結合することが分かっている。
また同じ人工歯根の用途で、数~数十μmの二次粒子からなるハイドロキシアパタイト微粒子をショットピーニング装置により噴射して、人工歯根など生体内で使用されるチタン合金やステンレス鋼などの表面に埋入させて濃化層を形成させ、表面の生体親和性を高める試みがなされている。
こうしたわが国の高度な工業技術をインプラント製品に適用する上で、厚生労働省の承認を得てわが国のインプラント市場を拡大するための明確な評価基準の確立が求められ、現在、インプラント製品の評価法をJIS化する動きが広がっている。わが国の医療機器市場のさらなる拡大のためにも、生体材料のJIS規格化をすすめていくとともに、上述の表面改質技術などにより安全性が高められたインプラント製品の仕様の明確化と安全性の情報発信の強化がますます求められている。
第106回 わが国金型産業の競争力向上のビジネスモデルを
第106回 わが国金型産業の競争力向上のビジネスモデルを提供:富士テクニカ 自動車向け金型国内2位の富士テクニカ( http://www.fujitechnica.co.jp )は9月17日、政府が出資する企業再生支援機構の支援により、同3位の宮津製作所から金型関連事業を譲渡する形で本年12月中に事業統合することを決定した。自動車向け金型でそれぞれ9.0%、5.2%の国内シェアを持つた富士テクニカと宮津製作所が事業統合することで、すでにタイ大手自動車部品大手メーカーのタイサミットの傘下にあるシェアトップ(同13.5%)のオギハラを抜き、自動車向け金型国内最大手メーカーが誕生することとなる。
富士テクニカと宮津製作所はともに自動車向け独立系金型メーカーとして、国内自動車メーカーはもちろん、ゼネラルモーターズなど米国ビッグスリーや欧州の自動車メーカーとも取引が多い。富士テクニカは北南米に、宮津製作所は欧州市場での売上比率が高く、今回の事業統合でも顧客基盤の補完という統合シナジーが期待される。しかし、今回の事業統合に至った金型業界の置かれた状況としては、北米市場や国内市場が低迷する中での国内勢による消耗戦の展開や、新興国の自動車市場が拡大する中での地場企業の金型事業への参入と価格競争にともなう金型製品価格のグローバルでの大幅な下落がある。
このため富士テクニカでは今回、外部からの資本の受入れを含む財務基盤の強化と、日本の金型技術を結集し技術優位性を生かした事業モデルを策定することにより、新興国の金型メーカーとの差別化と国内企業間の過当競争の解消を図ることが必要との判断から、ともに金型業界のトップメーカーである宮津製作所との事業統合を決めたもの。
金属やプラスチックなどの素材に圧力を加え特定の形状の部品に成型するのに使われる金型は、大量生産において製品の品質・性能・生産性を左右する重要な要素でマザー・ツールとも呼ばれ、金型産業は日本の代表的な基盤産業の一つに位置づけられている。わが国の金型産業は、世界最高レベルの技術力を背景に、自動車をはじめ国内外の製造業全体の競争力向上に寄与してきた。日本の金型なしには車が作れないと言われた時代もあったが、1990年代以降の自動車・電機分野での海外生産に伴う産業空洞化の進む中、わが国金型産業は低迷し始めた。従業員20人未満の中小企業が9割を占めるという金型産業では、技術の流出により自らの商権を奪われることを懸念して、海外進出に二の足を踏む企業が多かった。
自動車パネルへの溶射技術の適用(提供:富士テクニカ) 確かに金型の守るべき蓄積された技術は多い。金型の生産では一般的だった放電加工から近年、切削による直彫り加工の適用が進んでいるが、高速・高精度加工を実現するためのビビリ抑制や耐久性向上などの工具技術、微小送り・位置決めの直動案内技術や5軸制御などの工作機械技術などが用いられている。また金型には、生産効率に関わる長寿命化や製品品質に関わる精度の維持といった要求から、耐摩耗性や耐焼付き・凝着性、離型性、耐熱性、耐疲労性など様々な表面特性が求められる。富士テクニカでもたとえば、自動車メーカーの省燃費化を目的とした軽量化のため、薄くて強度が出る高張力鋼板を成型するための高硬度な金型を作るべく、金型の摩耗を防ぐ皮膜を形成する溶射技術を使用条件に合わせて開発、自動車鋼板パネルを生産するメーカーでは摩耗による金型のメンテナンス頻度が減り、生産性を向上しているという。
さて、富士テクニカではこうした高い技術力を持つわが国の金型技術が新興国で価格だけによらない競争力を示すべく、国内工場に高い技術力・高い管理能力を集約させマザー工場としてさらなる強化・発展を図りつつ、中国やインドネシア、マレーシアなど海外製造拠点を早期に育成・強化し、グローバル・サプライチェーンの確立を目指したいとしている。新興国での現地生産により価格競争力を高める一方、国内拠点には研究開発機能を持たせ技術競争力を高める考えだ。
今回の富士テクニカと宮津製作所との事業統合に対して経済産業省では、(1)わが国が優れている品質・納期管理能力に加え、新興国に勝るコスト競争力を構築し、持続性ある雇用基盤の構築と、着実な再生が進展すること、(2)経営統合後の会社が、わが国を代表する競争力を身につけ、飛躍的に発展することや、他の金型企業ひいては他のものづくり企業においてもこうした取組みが進み、わが国ものづくりの競争力の向上、さらには、日本経済の成長につながることを期待していることを、企業再生支援機構に対し意見している。わが国で生まれ築き上げられた高い金型技術が、今後も世界の産業の生産を支え続ける、そんなビジネスモデルを金型業界に示していくことを今回の事業統合の成果として期待したい。
第107回 24時間換気システムの普及で求められるベアリング技術
第107回 24時間換気システムの普及で求められるベアリング技術提供:パナソニック 2003年7月1日に国土交通省によりシックハウス対策に係る建築基準法が改正されたことで、住宅には原則として常時作動する機械換気設備の設置が義務づけられるようになっているが、近年ファンモータおよびベアリングに対して24時間作動に伴う静音化や省電力化などの要求が強まってきている。
改正建築基準法(令第20条の8)では、内装の仕上げなどにホルムアルデヒド発散建築材料を使用しない場合であっても、家具などからもホルムアルデヒドが発散されるため、居室を有する全ての建築物に機械換気設備の設置が原則義務付けられており、この機械換気設備は原則として24時間作動で居室の空気を強制的に新鮮な外気と交換することを目的として設置される。給気と排気の両方をファンで行う「第一種機械換気方式」や排気のみをファンで機械的に行い、その結果生じる内外の気圧差を利用して給気口から給気することで換気を行う「第三種機械換気方式」などがあるが、いずれにしてもファンが常時回転しているため、建築物への換気設備の導入が進む中で、ファンモータ用軸受には居住空間における静音化と省電力化が求められてきていた。
こうした要求に対したとえばパナソニックの24時間換気システムの一つである天井埋め込み型換気扇を見ると、20 dB 未満の低騒音で消費電力を最大で3~5割低減するブラシレスDCモータを採用している(平成20年度省エネ大賞資源エネルギー庁長官賞受賞)。
提供:NTN これらファンモータにおける静音化のニーズに対しNTNでは先ごろ、信頼性、静粛性に優れ、転がり軸受との互換性がある「動圧軸受ユニット」を開発した。現在、家庭用換気設備向けにサンプル提出を進めており、2011年度中の市場投入を目指す計画だ。
NTNではすでに、焼結含油軸受の内径面に動圧溝を形成した動圧ベアファイト(焼結金属製動圧軸受)が2001年以降からHDD向けにスピンドルモータ・ファンモータなどで採用され、実績を残している。動圧軸受は軸と軸受が油膜を介して非接触で回転するため、静粛性に優れているものの、転がり軸受とは寸法や使用条件が異なることから、これまで転がり軸受から動圧軸受への置き換えには制約があった。一方で、改正建築基準法による全建築物への24時間換気システムの設置義務付けで家庭用換気扇の需要も増えているが、リビングルーム、寝室などにも取り付けられることから、特に静粛性に対する要求が高くなってきている。
そこでNTNでは、この動圧軸受の静粛性という特徴を生かしつつ市場ニーズに応えるため、小型換気扇など、軸受荷重が比較的小さく荷重変動が少ない用途向けに、転がり軸受と同寸法で互換性のある動圧軸受ユニットを開発した。動圧ベアファイトを軸受部に採用し、優れた静粛性に加えて転がり軸受同等のトルクを維持したほか、ハウジングとの組み合わせでユニット化したシンプルな設計としている。
一方、静粛性を阻害する要因として、フィルタが捕獲した埃などがファンモータ、さらには軸受内部などにはいることで、異音を発生させるという問題があった。
提供:日本精工 これに対し日本精工(NSK)では、室内換気システム、分煙機用ファン、天井埋込型換気扇向けなど需要が増えている室内換気システムの軸受として、低トルク化による省エネ化や塵埃環境での防塵性能向上による静音化に貢献する「低トルク高防塵シール付き深溝玉軸受」を開発、サンプル出荷を開始した。NSKでは本製品の売上として2013年度に1億円の売上を目指す。
室内換気システムは24時間稼動するため、軸受には低トルク化による省エネ性能が求められる一方、室内換気システムは夜間に寝室で稼動しており、異音の発生原因となる塵埃の軸受内部への侵入を防止するため、軸受には高防塵性能も求められる。
NSKではこれらにニーズに対し、様々な使用環境に合わせ2種類のシール付き軸受を開発した。
①接触タイプ
低トルク化のため、解析技術によりシールリップ剛性を最適化しシール接触圧力を標準品に対し約3割低減。シール接触による高防塵性能を損なわずに従来比で約3割摩擦損失を低減することでモータ消費電力を低減している。
②非接触タイプ
防塵性能向上のため、シールと内輪の非接触シール部を延長、径方向すき間だけでなく、軸方向すき間も極小化するため、ゴムシールを採用。非接触シールによる低トルク性能を損なわずに防塵性を向上、静音性能を約2倍向上している。
提供:ジェイテクト さらにジェイテクトでは先ごろ、24時間運転でのファンモータ用軸受の電食による音響寿命を含めた長寿命化を図るべく、「長寿命電食防止軸受」を開発している。電食とは、軸受の損傷形態の一つで、モータ回転時に軸受の内外輪間に電位差が発生し、内外輪転走面と転動体の間で、グリースの油膜を介して電流が流れることにより、軸受内部が損傷し、音響寿命に至る現象。
開発品では転動体にセラミックスを使用することにより内外輪転走面と転動体の間に電流が流れることを防止、グリースの長寿命化と電食防止を実現したほか、耐熱温度140℃の高温対応のゴム材質を用いたシールのリップ形状を最適化し、ゴムシールと内輪の接触を極軽接触とし、低トルク化を実現した。さらに、エステル油+エーテル油の基油にリチウム石けん増ちょう剤を配合した長寿命グリースを開発した。これにより雰囲気温60℃でのファンモータ寿命100,00時間以上の長寿命化を達成している。
すでにエアコンやHDDなど電機分野で鍛えられてきたわが国の軸受の静音化技術、省エネ技術は世界に誇る技術の一つだ。建築物での24時間換気システムの導入が進む中、静音化や省電力化を追求するファンモータ用軸受の開発はますます進みそうだ。
第108回 クルマの省燃費化を図るエンジンオイルが販売開始
第108回 クルマの省燃費化を図るエンジンオイルが販売開始提供:出光興産 出光興産( http://www.idemitsu.co.jp )は、API(米国石油協会)と日米の自動車メーカーで組織されるILSAC(国際潤滑油規格化認証委員会)の新規格に合格したガソリンエンジンオイルを新規格発効日の10月1日から全国一斉に系列サービスステーション(SS)で販売を開始した。JX日鉱日石エネルギーや昭和シェル石油などの石油元売りメーカーでも、新規格適合のエンジンオイルを11月から発売すると発表している。旧来規格と比べ省燃費性能をはじめ高温酸化安定性能、触媒被毒防止性能の向上が求められるほか、バイオ燃料対応性能が新たに求められている。
「機械の血液」と呼ばれる潤滑油には、油膜を作ることで摩擦・摩耗を抑え焼付きを防止する「潤滑作用」、ピストンリングとシリンダ間で油膜を作り燃焼ガスの漏れを防ぐ「密封作用」、燃焼により発生した熱を外部に逃がす「冷却作用」、燃焼や回転中に受ける応力を分散する「緩衝作用」、摩耗で発生した粒子(摩耗粉)を洗い流す「清浄作用」、金属部品の錆発生を防止する「防錆作用」などの機能がある。エンジン油は高速、高圧、高温などの環境下にさらされるピストンリングとシリンダーライナー、クランクシャフトとコンロッドのベアリング、動弁機構などエンジン部品の動きを円滑にし、エンジンの性能を引き出すとともに保護する。
旧来、このエンジン油の性能・品質を規定する規格としては、石油メーカーで組織されるAPIが制定するAPI規格が用いられてきたが、近年、自動車メーカーにおいてCO2削減、つまり省燃費性能の向上が重要課題とされる中、クルマの省燃費化システムをAPI規格が満足させられない事態が発生、1991年に日米の自動車メーカーからなるILSACが組織され、エンジンの構成部品の一つであるエンジン油に省燃費性能の規格を盛り込んだILSAC規格が作られることとなり、順次クルマの最新技術に適合したエンジン油が市場にリリースされるようになった。以降、ILSAC規格が改訂されるのに合わせてAPI規格も市場投入されている(ILSAC規格=API規格+省燃費性能)。
ILSAC GF-5規格は、省燃費性能のさらなる強化、市場におけるロバスト性向上、排出ガス適合性の強化、の三点を主眼に開発された。省燃費性能の強化では、新試験法により実際の運転状態をより反映させるよう、回転数、負荷、出力、油温、水温などの試験条件を変更して境界・混合潤滑領域となる高温・低回転条件の割合が増えたことで、エンジン油の違いによる燃費のバラツキが排除されている。ロバスト性向上では、主に清浄性を中心とした性能の強化が規定された。排出ガス適合性強化では、排出ガス後処理装置の触媒寿命を低下させるエンジン油添加剤中のリン(P)に関して、前規格のGF-4までその含有量が段階的に低減されてきたが、リンは摩耗防止の機能を持ち、リン含有量の低減は摩耗促進につながることから、リンの含有量はGF-4同等(最大0.08mass%)としつつ、リンの蒸発量(減少量)を規定、その目標値を11%未満(残存量89%以上)としている。
この厳しい規定をクリアすべく、石油メーカー各社では省燃費化につながる0W-20という低粘度化を図る高粘度指数(温度による粘度の変化が少ない)のベースオイルに加えて、粘度指数向上剤や低粘度下で懸念される油膜切れなどに対する摩擦調整剤など各種添加剤の適切な配合が行われている。今回発売された出光興産のエンジン油では、金属間のすべりをよくして省燃費性能を高める摩擦調整剤(FM)モリブテンの効果を最大限に引き出す添加剤処方を開発、同社従来オイル10W-30に対し、モータリングテストで約9%のトルク改善を記録、対10W-30燃費向上率が約8.4%だった同社SM/GF-4適合エンジン油に比べても2%上回っているため、さらなる燃費向上が期待できるとしている。
GF-5規格は、2011年までに製造されるすべての乗用車で省燃費性能を向上し排出ガスを低減するために施行される新しい政府規制を満たさなければならない米国はもちろん、日本、カナダ、韓国でGF-4と同様に新車に採用される見込みだが、中国では依然数世代前の規格が流通していることから、量的に拡大する中国向け車両に対して新規格に適合した0W-20といった低粘度オイルの工場充填が遅れるとの見方も強く、GF-5適合油の市場が予測よりも縮小することを危惧する声もある。
自動車メーカーと石油メーカーとの長年の協議のもと規定されたGF-5規格とそれをクリアすべく多額の費用と開発期間を投じて開発された新規格適合のオイルの普及と、それによるクルマの省燃費化、CO2削減が促進されることに期待したい。
第109回 ノーベル賞発表、基礎研究の深耕と応用展開を望む
第109回 ノーベル賞発表、基礎研究の深耕と応用展開を望む提供:チッソ スウェーデンの王立科学アカデミーは10月5日、2010年のノーベル化学賞を有機合成の革新的手法「クロスカップリング反応」を開発した鈴木章・北海道大名誉教授と根岸英一・米パデュー大特別教授、リチャード・ヘック・米デラウェア大名誉教授に、同じくノーベル物理学賞を炭素の新素材「グラフェン」を開発したアンドレ・ガイム・英マンチェスター大教授とコンスタンチン・ノボセロフ・同大教授に授与すると発表した。
液晶材料で多数活用されているクロスカップリング反応
ノーベル化学賞を受けた業績「有機合成におけるパラジウム触媒によるクロスカップリング」は、炭素を効率的に結合させる反応。複雑な化合物を作るためには、炭素原子同士を結合させなくてはいけないが、炭素原子は安定で容易に反応しない。パラジウム触媒によるクロスカップリング反応はこの問題を解決し、有機化合物炭素結合を組み替えて新たな有機化合物を合成するもの。液晶や有機EL(エレクトロルミネッセンス)などの製造技術に活用されている。
たとえば液晶は10~20種程度の有機化合物を混ぜ合わせた半透明の液体。これら有機化合物がクロスカップリング反応を用いて液晶材料として製造される。クロスカップリング反応が液晶の生産コストを下げ、液晶テレビの市場拡大に貢献したとも言われる。液晶材料の世界シェアで5割を占めるチッソに限らず、世界でクロスカップリング反応の恩恵を受けていない化学メーカーはないという。
摩擦・摩耗特性が期待されているグラフェン
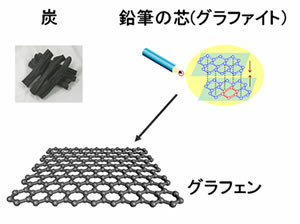
富士通研究所は東北大学らと共同で、一般的な半導体製造プロセスである化学的気相成長法(CVD)でグラフェン絶縁基板上に低温で直接形成する技術を開発、大基板の全面にトランジスタを形成することに世界で初めて成功した。従来のグラフェンの形成温度が800~1,000℃であるのに比べ、形成温度を650℃と大幅に引き下げたことで、さまざまな絶縁基板上に直接グラフェントランジスタを形成することが可能なほか、従来の1/10~1/100という低消費電力LSIや、それを利用したIT機器の実現で省エネルギー化に寄与していくとしている。また、日立製作所は東北大学と共同で、シリコンの10倍以上速い電子移動度が期待されるグラフェンを、CVD法を用いてサファイア基板上に作製する技術を開発した。通信基地局のネットワーク機器などに用いられる高速電子デバイスへの応用が期待されているという。
層状結晶構造のグラファイトの単層を1枚剥ぎ取った超薄膜であるグラフェンは、そうした電気的特性だけでなく、機械的特性、中でも優れた摩擦・摩耗特性が期待されている。潤滑油剤の適用が嫌われる電子機器の摺動部品などでの機械的特性を高める固体潤滑コーティングとしての研究もぜひ進めてほしいところだ。
わが国の二人の研究者がノーベル化学賞を受けた「パラジウム触媒によるクロスカップリング」のように、世界で適用されていく重要な基礎研究の深耕を進めるとともに、その応用展開によって新たなビジネス・産業の創生につながっていくことに期待したい。
第110回 製品品質向上と環境保全を図る産業洗浄技術
第110回 製品品質向上と環境保全を図る産業洗浄技術 日本洗浄技能開発協会と日本産業洗浄協議会、日刊工業新聞社は10月13日~15日、東京・有明の東京ビッグサイトで「2010洗浄総合展」を開催した。機械・電子部品の高品質を保つ部品洗浄など、最新の洗浄剤・洗浄システムなどが多数展示された。
金属部品の油汚れに用いられる洗浄剤
産業洗浄では、様々な部品や材料が品質・機能を確保する目的で洗浄されるが、その半分が金属部品との報告がある(2003年機械振興協会経済研究所)。落とすのは圧倒的に油汚れが多く、グリース・潤滑油剤を筆頭に、加工油、防錆油などが続く。つまり大半は金属部品の油汚れで、強力な洗浄力が求められる。
かつて、この金属部品の油汚れを落とす洗浄剤といえば、塩素系洗浄剤である1,1,1-トリクロロエタンが定番であった。極端な話、油まみれの部品を1,1,1-トリクロロエタンの液中にどぶ漬けしておけば、油汚れは跡形もなく除去されていた。しかし1995年をもって特定フロン・エタンはオゾン層保護を目的に生産が中止、ここから洗浄力の強力なエタンに匹敵しつつ環境負荷の小さい総合的な代替洗浄技術の開発が本格化したと言える。つまり洗浄剤、洗浄システムの合わせ技によって、環境に負荷を与えずに、製品の競争力向上からは機能に影響する洗浄品質を効率的に、かつ低コストに実現しなければならないという取組みである。
環境負荷の小さい洗浄剤の開発が本格化
金属加工部品の加工後の洗浄を例にとると、付着した油汚れと相溶することで脱脂洗浄を行う炭化水素系洗浄剤が多用されている。地下水汚染物質、有害大気汚染物質、オゾン層破壊物質、温室効果ガスのいずれにも該当せず使い勝手がよいことも、採用される理由だろうか。しかし、炭化水素系洗浄剤は従来、引火性があることから装置には防爆仕様が求められ、また相溶しない水溶性加工油の洗浄は不得手としていた。これに対し、たとえば日鉱日石エネルギーの「NSクリーン」では、パラフィン系炭化水素の単一物質で構成し非常に狭い沸点範囲を実現することで、引火しやすい軽質分を含まないため同等の平均沸点を持つ混合物に比べ引火点が高く、より安全性を高めている。また、水溶性加工油に対しても、特殊な界面活性剤を配合することで、被洗浄物に付着した水分を素早く引き離し、分離した水分は水滴となり比重差によってすみやかに沈降させるという。
洗浄の効果に加えて省エネ化が求められる洗浄システム
提供:カイジョー 洗浄工程で洗浄効果を高める手法としては、超音波洗浄が多用される。特に複雑形状の部品や止まり穴があるような部品では、物理的な作用がなければ洗浄液が汚れの部分まで浸透しにくいためである。超音波洗浄は主に(1)キャビテーション、(2)加速度、(3)物理化学的反応促進作用の三つの相互作用によるものとされ、特にキャビテーションをいかにコントロールするかが重要。キャビテーションは周波数が低いほど発生しやすく、また周波数が高くなるに従い加速度は大きくなる。これらの効果の違いから、それぞれの洗浄物や汚れの種類により周波数の使い分けがなされている。機械加工部品に付着した油の洗浄には、キャビテーションを利用した100kHz程度の周波数が選ばれる。
ものづくり基盤技術の一つとして様々な分野で活躍が期待される洗浄技術
こうした合わせ技によって産業洗浄技術は、自動車部品やベアリングなどの精密部品の品質・性能を保持し、はてはハードディスクドライブなど微細機構のマイクロコンタミネーションを抑制し信頼性を高めている。表面特性向上というでは、洗浄工程は機能性コーティングの母材への密着性を高める前処理としても重要な位置づけを占めるなど、ものづくり基盤技術振興基本法によりものづくり基盤技術の一つに指定される、重要基盤技術である。オゾン層保護のための特定フロン・エタン代替としてスタートした環境対応の洗浄技術はその後、地球温暖化防止、揮発性有機化合物(VOC)排出規制などに対応し、さらに化学物質全般の管理について国際的な協力体制のもと推進すべく、「経済的に実行可能な最良利用可能技術(EVABAT)」として検討が進められてきている。MEMS(微小電子機械)など微細機構の商業化とともに、微細なコンタミネーションの除去による表面機能や品質の確保が求められるといったように、産業の拡がりとともに産業洗浄のカバーする領域は常に拡がり続けている。環境保全と最先端分野での表面創成を実現する産業洗浄技術の合わせ技が、今後もますます求められている。
第111回~第120回
第111回~第120回第111回 レアアース調達難航で、希少金属使わない技術開発の推進を
第111回 レアアース調達難航で、希少金属使わない技術開発の推進をi-MiEV(提供:三菱自動車) 中国のレアアース(希土類)の禁輸が拡大してきている。経済産業省が9月28日~30日に実施した「中国における輸出入状況に関する調査」の結果でも、レアアースの貿易に関与している31社全社から、尖閣諸島での中国漁船衝突事件の後の9月21日以降、日本向けの輸出が止まっているとの報告がなされている。
ハイブリッド(HV)車や電気自動車(EV)の二次電池のリチウムやモーターの磁石のネオジムやデジカメのレンズのタンタルなどのレアアース。中国はこのレアアースの世界生産量の97%を占める。来年度の日本のレアアース需要は3万t以上に上る見通しで、そのほぼ全量を依存する中国の禁輸から、約1万tが不足すると見られている。
こうした事態に先立って、資源に乏しいわが国では、レアアースやその他レアメタル(希少金属)に頼らない技術の確立を目指し、研究開発が早くから進められている。
レアアースを使用しないHV・EV用モーターを開発
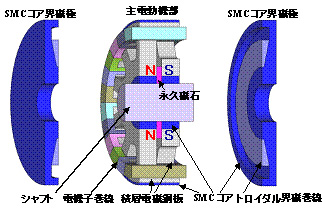
リウムの使用量を低減させる技術と代替材料

プラチナを表面改質してレアアースの使用量を減少
中国のレアアース禁輸に対し、ドイツが日本のレアアース確保の支援を約束し、新たな供給源開拓のために日独が協力して取り組む方針を示唆するなど、国際的な協調体制構築も進んでいる。しかし、資源に乏しいわが国がこれまでレアメタルに頼ってきた先端分野で引き続き先導的役割を果たし続けるべく、今後も、様々な産業分野においてレアメタルを極力使わない技術の確立が求められよう。
第112回 JIMTOF2010に見る工作機械のトレンドに対応する軸受・直動案内技術
第112回 JIMTOF2010に見る工作機械のトレンドに対応する軸受・直動案内技術 10月28日~11月2日、東京・有明の東京ビッグサイトで「第25回日本国際工作機械見本市(JIMTOF2010)」が開催、切削・研削・研磨・プレス加工などの工作機械をはじめ、直動案内機器や軸受などの工作機器、工具、切削・研削油剤などの関連技術が一堂に会した。LEDなどグリーンエネルギーに関わる微細加工の技術が紹介される一方で、ここ数年で大幅な需要拡大が見込まれる航空機や中国など新興国が市場を牽引する建設機械など大型部品の加工技術もデモンストレーションなどをまじえて紹介された。こうした各種ニーズに対応する多軸機や複合機の可動部を支える軸受や直動案内などの機械要素技術も多数出展された。
航空機部品など難削材加工にセンサ付きスピンドル
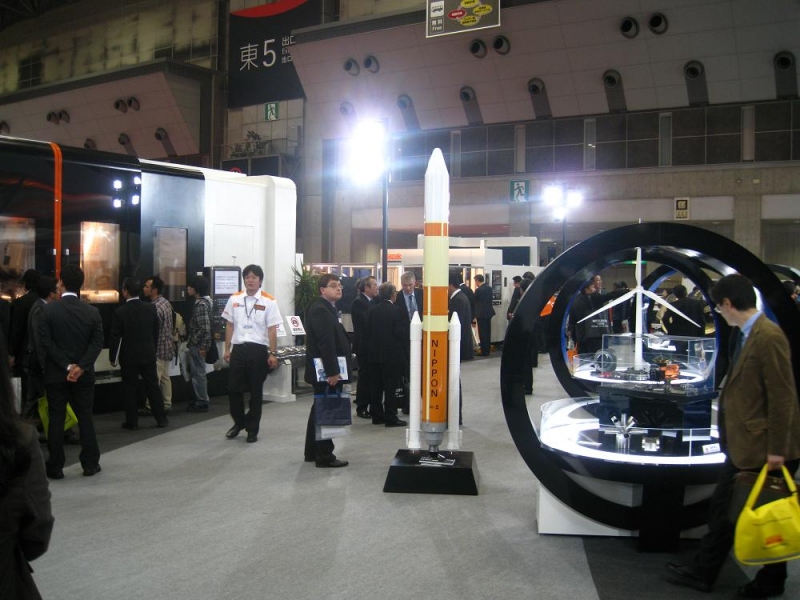
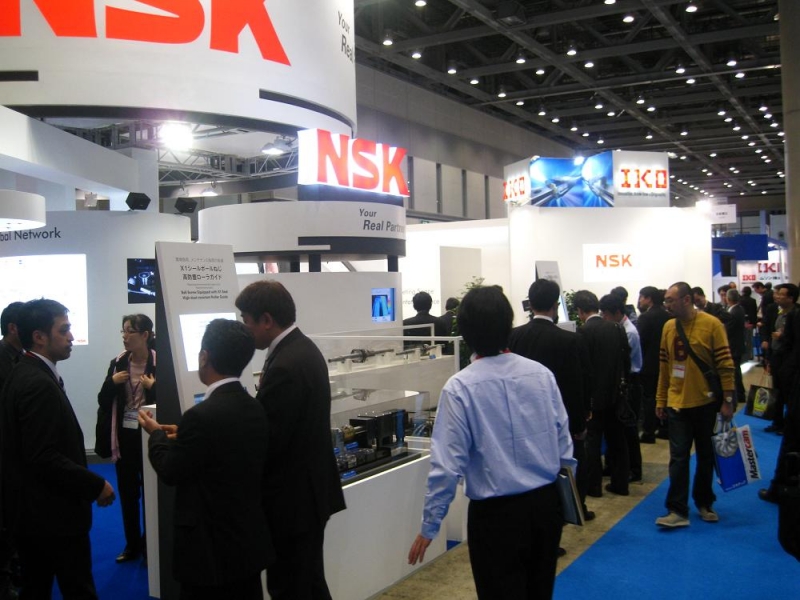
精密・微細加工に対応する各種機械要素技術
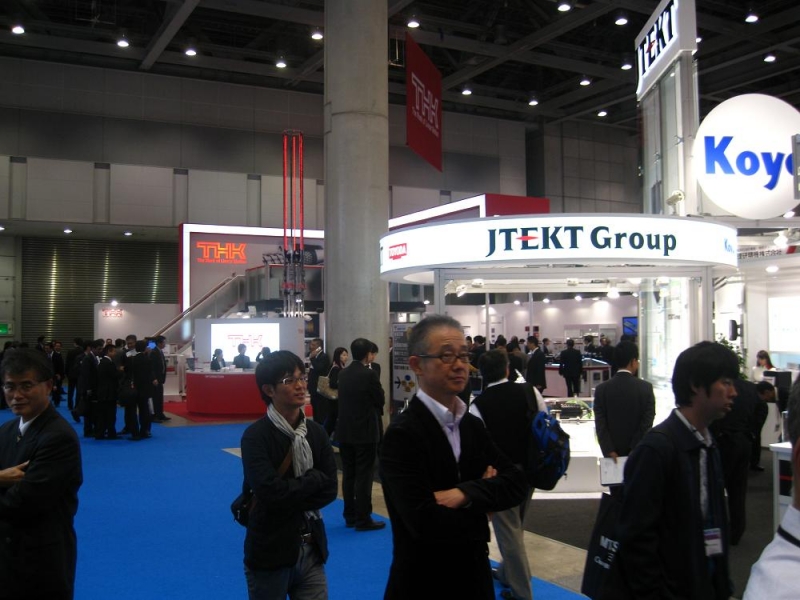
新興国向けの機種には部品にもコストパフォーマンスが求められる
こうした用途での高剛性とは別に、自動車や家電製品など需要が堅調な中国など新興国では、加工の時短要求とともに工作機械の使い方が荒いと言われる。タフでコストパフォーマンスの高い仕様としては、たとえばスライドユニット長さを長くし組み込まれるローラの数を増やすことで精度を向上しつつ、小形サイズながら負荷容量と剛性を上げ、工作機械のトータルコストダウンを実現する日本トムソンの「超高精度・超高剛性ロングユニットMXL」などがあろう。また、異物粉ガ発生しやすい生産現場で稼働する直動案内で異物侵入による軌道面の異常摩耗や展胴体の循環不良による破損を防ぐ日本精工の「高防塵サイドシール付きローラガイド」なども、直動案内の潤滑寿命を延長し工作機械の長時間稼働を実現するタフな技術と言えようか。
JIMTOFの会場で某工作機械メーカーが、「(これまでの自動車分野の偏重から)航空機、医療など成長分野をはじめどんな分野の加工にでもチャレンジしていかなくてはしなくてはいけない。多軸・複合機によってこれまで思いもよらなかった分野まで加工対象が拡がってきている」と語っていた。軸受・直動案内など機械要素技術の活躍によって、微細・精密な加工機から、大型部品の加工機、新興国などでの荒い使用に耐える低コストの加工機に至るまで多様な加工ニーズに対応して進化し続ける工作機械の高性能化と信頼性向上が支えられている。
第113回 秋の叙勲に、わが国ベアリング業界の先進性を思う
第113回 秋の叙勲に、わが国ベアリング業界の先進性を思う提供:NTN 平成22年秋の叙勲では各界で功労のあった計4,173名が受章、ベアリング分野からNTN会長の鈴木泰信氏が旭日重光章を受章した。同氏は、同社社長、会長として産業の発展に寄与したほか、日本ベアリング工業会の会長、ならびに近年設立された世界ベアリング協会の初代会長としてベアリング業界の発展に寄与した功績が評価されたもの。
世界を牽引するベアリング大国日本
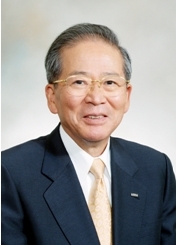
ベアリングは本欄でも度々取り上げているとおり、自動車・新幹線や風力発電用など、あらゆる機械の回転部分を支え、省資源や環境保全に貢献する製品として、その重要性が年々高まってきている。また、日本から世界に向け発信できる優位性の高い商品の一つであり、それゆえ日本製ベアリングの世界での流通とともに、1990年代の終わりから偽造ベアリング製品がアジア、中近東、中南米、アフリカなどに多数流通、問題化してきていると言えよう。これに対し日本ベアリング工業会では、こうした偽造品を使用した自動車や電気製品などは早期破損に繋がる可能性が高く、消費者や工場の作業者などを危険にさらすことになるほか、機械の突然停止による生産効率の低下、メンテナンスコストの増大など経済的な損失を招くことも少なくないとの懸念から、世界に先駆け、不正商品の生産拠点があると思われる中国に2000年11月末に第1次ミッションを派遣、以来2008年までに第8次ミッションを派遣し、中国政府機関に対し不正なベアリングによる身体、生命への危険性を訴えながら、その製造・販売の撲滅に向け取締りの要請を行うなどの対策に努めている。WBAでもこの日本ベアリング工業会の取組みが評価され、偽造品対策が強化されてきている。
省エネ・高信頼性ベアリング製品の開発によりと市場投入によりさらなる活性化を
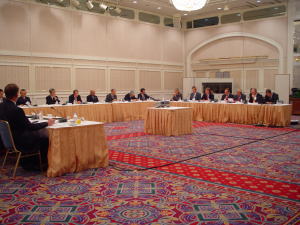
秋の褒章でのベアリング業界からの栄えある受章を機に、あらためて世界に先駆けたわが国ベアリング業界が一丸となっての不正商品撤廃による製品の信頼性向上、地球環境保全への取組みと、世界のベアリング業界への波及の進展を思いつつ、世界に誇る省エネ・高信頼性ベアリング製品のたゆみない開発と市場投入によって、わが国ものづくり産業の活性化につながっていくことを期待したい。
第114回 世界に発信した日本の強み、次世代高速車両リニア新幹線
第114回 世界に発信した日本の強み、次世代高速車両リニア新幹線リニア新幹線 11月13日~14日、横浜で開催された「2010年日本APEC首脳会議」では、地域経済統合、成長戦略、人間の安全保障を中心に、アジア太平洋の将来像について議論を行い、首脳宣言として、APECがさらに緊密に高度化した経済統合で結ばれ(緊密な共同体)、質の高い成長を実現できる強い共同体(「強い共同体」)であり、安全で、安心して経済活動を行える共同体(安全な共同体)に向かっていくという「横浜ビジョン」で合意した。具体的には、ボゴール目標達成評価を行った上で、アジア太平洋地域での地域経済統合を更に推進するために、アジア太平洋自由貿易圏(FTAAP)の構築に向け具体的な行動を取ることとなった。また、世界の成長センターであるこの地域として初めての、長期的かつ包括的な成長戦略をとりまとめた。また人間の安全保障の課題に対処するため、食料安全保障、防災、感染症への対応、腐敗対策、テロ防止などの分野に注力していくこととなった。
最高時速502kmの超電導リニア新幹線
ところで今回の開催にあたり、来日した首脳らに対し、日本政府は、地元自治体である横浜市・神奈川県とともに、心からの歓迎の意を表し、地元自治体等との連携のもとに宇宙から帰還した小惑星探査機「はやぶさ」など最先端技術やものづくり、伝統文化や現在の美術などの「日本の強み」をアピールした。特に米国などでも採用を検討している高速鉄道・リニアモーターカーなどが出席者から注目を集めた。
先にJR東海が計画するリニア中央新幹線計画について、国土交通省の審議会は東京-名古屋間をほぼ直線で結ぶルートが最も経済効果が高いとする試算を公表した。2045年に直線ルートで全線開業し東京-大阪間が67分で結ばれた場合、沿線地域の企業への経済効果を年間8,700億円と見ている。
さて、この超電導リニア新幹線は、車両に搭載した超電導磁石と地上コイルの間の磁力で車両を10cm浮上させ、最高時速502kmの超高速で走行する。
車両は基本的に非接触で浮上、ガイドウェイ(従来の鉄道の軌道)に案内され、推進するが、超電導機構での安全性や高速走行での信頼性を向上するメカニカルな機構も備えている。
電導機構での安全性、高速走行での信頼性を向上するメカニカルな機構
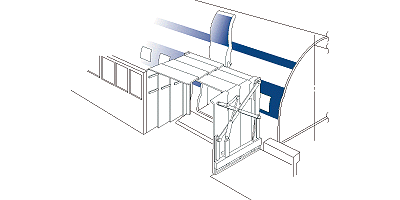
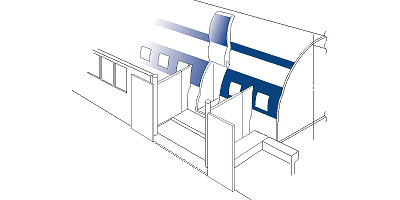
また、分岐装置(ポイント)は列車が進路を振り分けるために必要不可欠な装置。この分岐装置には、使用目的に応じた列車速度の違いから高速用、低速用、車両基地用の3種類がある。車両が基準線側(直線側)を高速浮上走行し、分岐線側(曲線側)を低速車輪走行する区間にトラバーサ方式の分岐装置を採用している。トラバーサ方式は、ガイドウェイをいくつかの横方向に移動可能な桁(可動桁)に分割して、移動させることにより、進路を構成するもの。山梨実験線では、この桁を移動させるための動力として、電動方式と油圧方式の2種類を採用し、試験を行う。始点や終点のターミナル駅等の基準線側、分岐線側を低速車輪走行する区間に側壁移動方式の分岐装置を採用している。側壁移動方式は、桁を移動する代わりに側壁だけを上下、左右に移動させて進路を構成するもの。分岐装置の前端部と後端部は側壁を左右に、中間部は側壁を上下に動かすようになっている。
時速500kmの高速からの制動力を実現するのは通常は電力回生ブレーキだが、バックアップブレーキとして発電抵抗ブレーキ、コイル短絡ブレーキ、空力ブレーキ、車輪ディスクブレーキを備えており、超電導効果が発現しない非常時でも安全に停止することができるようになっている。
今後もグリーンエネルギーとして注目されるリニア新幹線
今回のAPECでは、各国・地域から経済危機から回復しつつあるこの時期にAPECが初めて長期的・包括的な形で成長戦略を策定していくことが時宜にかなっているとして強い支持があった上で、「均衡ある成長」「あまねく広がる成長」「持続可能な成長」「革新的成長」「安全な成長」という柱に沿った形で、それぞれの取組の重要性について議論が深められ、特にグリーン成長や構造改革の分野での具体的行動を求める声が相次いだ。このグリーンエネルギーとして各国が注目するのが中でも環境負荷が少ない高速車両の技術である。中国でも新幹線の技術を導入し高速車両を輸出し始めているが、その実績は少ない。それに対しわが国の新幹線は、高速車両として半世紀の安全神話を誇る。グリーンエネルギーに貢献し都市間を超高速で結ぶ高速車両の最高峰、リニア新幹線に世界中の視線があらためて集まってきている。
第115回 アクティブメンテナンスで現場の生産性・信頼性の向上を
第115回 アクティブメンテナンスで現場の生産性・信頼性の向上を 11月17日~19日、東京・有明の東京ビッグサイトで日本プラントメンテナンス協会らの主催による「メンテナンス・テクノショー」が開催、最新の設備診断・保全技術が多数展示された。
「事後保全」から「予知保全」へ
わが国では、円高対応などでさらなる生産性向上によるコストダウンに取り組んでいる一方で、設備管理方法として、機械設備が故障してから修理する「事後保全」方式をとっている生産設備の休止損失によって利益を圧迫し、また機械の不具合による製品の品質低下を招いている現場も少なくない。そこで、この展示会では予知保全(PM:predictive maintenance)の概念から、設備の劣化状況や性能状況を診断、その診断状況をもとに保全活動を進める設備診断・保全技術が紹介された。特に、劣化状態を観測し、真に保全の必要な時に保全を施す状態基準(監視)保全(CBM:condition-based maintenance)の概念から、設備の状態を定量的に把握する設備診断技術の出展が多かった。
軸受の予知保全
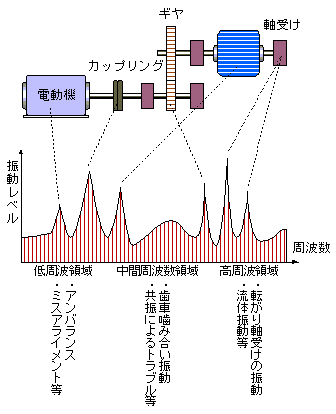
潤滑油の予知保全
また、機械設備では潤滑トラブルが全トラブルの25%以上を占めるといわれ、特に油圧システムの故障では8~9割が油の劣化に起因するといわれるほど、油の汚れ(コンタミ)が機械システムに与える損害は大きい。そこでやはり予知保全の観点から、金属摩耗粉やスラッジ、侵入した粉塵などコンタミによる使用油の劣化の状態を、早期に検知する手法が適用されている。たとえば自動粒子計数器(パーティクルカウンター)によるオンライン測定するシステムでは、稼働する装置の油圧作動油や各種潤滑油の中のパーティクルを、100mL中に分類された粒子サイズごとに、数量により規定された等級で評価するNAS1638やISO4406による清浄度コードなどで清浄度のチェックが行われ、潤滑油の管理がなされている。
生産現場でのロスをなくし経済効果を高めるにはこうした設備診断機器の導入促進が引き続き望まれるが、そうした軸受管理や潤滑管理に携わる技術者の育成も重要である。
メンテナンスには設備だけでなく「人」の育成も必要
技術のグローバル化を推進するため、診断技術の分野でもISO18436-2(機械状態監視診断技術者(振動)の認証に関する規定)が2003年に発行された。機械の共通技術である設備の状態監視、診断、保守の分野ではすでにグローバル化が進み、多くの企業が国際的に事業を展開しているため、グローバル化された企業においては、本資格を有している技術者がいることが必要となる。日本機械学会では2004年10月からこのISO18436-2に準拠した「機械状態監視診断技術者(振動)」として、機械振動の測定・解析を行う技術者の認証を行っている。また2009年10月からは、ISO18436-4に準拠した「機械状態監視診断技術者(トライボロジー)」としての資格認証を開始、この資格認証はトライボロジー(摩擦・摩耗・潤滑の科学技術)の専門学会である日本トライボロジー学会(JAST)との共同認証になる。この認証により、潤滑技術や潤滑管理だけでなく積極的にメンテナンス全般に関わる幅広い知識を有する技術者を訓練・育成することが可能となるという。製造業にとっては、スペシャリストとしての資格保有者がメンテナンスを担当することで技術的な保障と責任体制が確立されるため、資格制度を取り込んだ技術者を擁する海外企業との競争でも、国際的な技術レベルの評価を受けることができる。資格保有者自身にとってもステータス、社会的信頼を得ることにつながり、専門技術者として可能な仕事の範囲が広がることが期待されている。
製品を製造し直接的な価値を創造する生産設備に対して、設備診断機器は生産に直結しない設備として導入が後回しにされ、依然として事後保全に陥っている現場も少なくないという。社会的ステータスの高い機械状態監視診断技術者が生産現場で活躍していくことで、予知保全技術・機器による生産性・信頼性を高めるアクティブメンテナンスの思想・体制が生産現場に根付いていくことに期待したい。
第116回 信頼性の高い衛星開発の推進を
第116回 信頼性の高い衛星開発の推進を小型科学衛星プロジェクト(提供:JAXA) 菅政権の「事業仕分け」第3弾の後半戦(再仕分け)では、文部科学省の宇宙関連事業を取り上げ、宇宙航空研究開発機構(JAXA)の開発した小惑星探査衛星「はやぶさ」が小惑星「イトカワ」の微粒子を持ち帰るなど実績をあげていることから、宇宙開発の重要性が認められ、今年度予算の水準約1,800億円を維持することでまとまった。文科省は次年度の概算要求で、すでに「はやぶさ」の後継機の開発費などを挙げている。
過酷な宇宙環境で求められる衛生材料・部品
「はやぶさ」のミッション成功など、わが国の宇宙開発技術が世界的に注目されている一方で、大学・高専などが製作、H2Aロケットとともに打ち上げられた小型衛星は、次々とトラブルに見舞われている。これは宇宙機器に使われる材料に影響を与える、-150~+200℃という温度サイクル、真空紫外線、10-3~10-5という高真空、原子状酸素、宇宙塵(スペースデブリ)といった過酷な宇宙環境に起因しているという。真空環境一つをとっても、金属同士がくっついてモータや弁の軸が動かなくなる要因となる。
こうした中、JAXA宇宙科学研究所では、特徴のある宇宙科学ミッションを迅速、高頻度、低コストで実現することを目指し、中型・大型科学衛星を補完する位置づけで小型科学衛星(SPRINT)シリーズを立ち上げた。まずは、現在JAXAで開発されている新固体ロケットを用いて2012年に1号機(SPRINT-A)を打ち上げることを目標とし、その後5年間に3機程度のペースでの打ち上げを目指す「小型科学衛星プロジェクト」が動き出している。
このプロジェクトでの「信頼性の考え方」を見ると、“不具合発生時に原因究明に支障がでる箇所や過去に類似品で不具合経験がある箇所については冗長構成をとる”、とある。衛星の信頼性を高めることは重要だが、冗長システムは結果的にコスト増大を招く。根本的な解決策としては、宇宙空間で壊れにくい材料・部品を使って衛星を作るしかない。
宇宙開発事業予算の確保を機に信頼性の高い衛星開発の推進を
そうした観点から宇宙材料の耐環境性についてはこれまで、各種宇宙用材料を実際の宇宙空間で曝露して特性変化を観察する軌道上材料曝露試験が行われている。米国では1980年代から、わが国でも1990年代から材料曝露実験が実施されている。それらのデータが宇宙用材料の開発にフィードバックされてきているとはいえ、最近でも国際宇宙ステーション(ISS)の実用ソーラーパネルに使われるポリイミドの原子状酸素による破断事故などが報告され、さらなる材料の改善が求められている。
しかし近年、その軌道上材料曝露実験での問題点が多数指摘されている。「軌道上材料曝露実験高度化ワーキンググループ」の神戸大学・田川雅人教授は、現在でも材料曝露実験を実施する機会が少ないことや、一つのミッションにかける期間が長すぎるといった問題があるのに加え、スペースシャトルの2011年最終フライト以降は軌道上曝露材料回収のめどが立っていないという問題を指摘する。
サンプル回収が困難になれば、軌道上でのその場解析(in-Situ解析)などを行って材料の評価を行う必要がある。そこでは、宇宙空間で稼動する機構部品の信頼性がますます求められる。そこで宇宙機器で多くの搭載実績を持つ固体潤滑剤が期待されている。「特に実績のある二硫化モリブデンを使うことで機構部品をコンポーネント化、これまでのオーダーメイドからレディーメイドとして、小型衛星ユーザーも使いやすくなるのではないか」と田川氏は言う。
しかし、これまで実施されてきた軌道上材料曝露実験と地上試験との相関は得られておらず、紫外線スペクトルや原子状酸素曝露条件など宇宙環境とまったく同条件での地上試験は不可能なのが現状。スペースシャトルに代わるソユーズで回収可能な小型の材料曝露パレットの開発など解決の方策もいくつか掲げられているが、過去の材料曝露実験のデータが十分には公開されていないという指摘もある。
軌道上その場解析という段階では、材料・機械分野からだけでなく、システム分野からも研究者が参画することが不可欠になる。現在は公開されていないデータが多いが、これまで実験を重ね蓄積されてきたデータを共有しての横断的な研究により、固体潤滑剤など宇宙用先端材料開発の課題を解決していくことで、宇宙機器、さらには衛星のさらなる信頼性向上につながっていく。宇宙開発事業予算の確保を機に、信頼性の高い衛星開発の推進を望む。
第117回 セミコンに見る半導体の微細化・大面積化に対応したメカ技術
第117回 セミコンに見る半導体の微細化・大面積化に対応したメカ技術 半導体製造装置や材料の展示会「セミコン・ジャパン2010」が12月1日~3日、幕張メッセ(千葉市美浜区)で開催された。韓国、台湾の半導体デバイスメーカー、ファウンドリー(受託生産会社)と競争力向上からは、集積度を上げる回路線幅の微細化やの出展各社のブースには回路線幅の微細化に対応した装置に加え、ウェハーサイズの大面積化、チップやセルを縦に積み上げる3次元構造化などに対応する装置や部品・材料が多数展示された。
各所で求められる微細化技術
半導体メモリーで見ると、パソコンでは読み書きが速いDRAMが、携帯電話などではデータ保存でき、消費電力が低いNAND型フラッシュメモリーが主流。DRAMではエルピーダメモリが40nmプロセスを導入、NAND型フラッシュでは韓国サムスン電子、東芝などが32nmプロセスを導入している。こうした回路線幅の微細化では、回路を焼き付ける露光光源の短波長化が進められ、65nmプロセスからは波長193nmのフッ化アルゴン(ArF)エキシマレーザーが用いられている。また投影レンズの明るさNA(開口数)を向上し解像度を高める手法として、45nmプロセスからは投影レンズとウェハーの間に純水を満たし光の屈折率を向上させる液浸技術が採用されている。さらに32nmプロセスではArF液浸で2回露光を実施するダブルパターニングが用いられている。
提供:ニコン 露光装置で、レチクルのパターンを投影するレンズは1/4の縮小倍率では、レチクルステージはウェハーステージの4倍の速度でスキャン動作を行い、ウェハー上に微細なパターンを焼き付けていく。ステッパーでは1時間あたりに処理できるウェハー枚数をいう「スループット」の向上が課題で、レチクルステージには露光を開始する位置に高速に移動し、高精度に位置決めする必要がある。そこでレチクルステージは磁気浮上型リニアアクチュエータなどで案内、そのXY平面の位置をレーザ干渉計で0.25~1nm程度の分解能で常時検出、Z軸方向の位置は多点焦点位置検出系からなるフォーカスセンサによって計測し、それらの計測値に基づき高精度に制御・駆動される。また、 ウェハーを搭載するウェハーステージは、リニアモータ駆動により、エアで浮上させ非接触としたエアベアリングで支持されリニアエンコーダーシステムにより位置が計測され高精度に制御・駆動される。
ArF液浸ダブルパターニング露光装置では高い重ね合わせ精度が必要で、32nmプロセスでは2nm以下の重ね合わせ精度が必要となる。たとえばニコンの液浸露光装置S620Dではステージ位置決めの高精度化のため、高精度エンコーダーとレーザ干渉計のハイブリッドシステムを採用している。これにより2nm以下の重ね合わせ精度と、1時間あたり200枚といった高スループットが実現されている。
大面積化に対応する各技術
提供:安川電機 微細化の一方で1ウェハーあたりのチップ収量を上げるため、すでに300㎜ウェハーのラインが構築され大口径化が進んでいるが、これに対応した搬送系の機構では、大口径化しつつ薄厚化したウェハーのたわみや反りによる負荷を低減することが求められる。これに対したとえば京セラのウェハーハンドリングアームでは、ウェハーへのダメージの緩和や不純物の拡散防止などを目的に、DLC(ダイヤモンドライクカーボン)コーティングなどを基材のセラミック表面に被膜している。またそれぞれ微細化したチップへのコンタミの付着防止が求められ、に用いられる軸受では、CVD成膜装置など高真空環境でのウェハー搬送用ロボットなどでは、ステンレス鋼の内外輪・玉に、銀など固体潤滑剤を被覆した軸受などが適用されている。また、半導体洗浄装置やCMP(化学的機械的プラナリゼーション)装置など水や薬液への体制が求められる環境でのウェハー搬送用ロボットでは、ステンレス鋼、セラミックス、樹脂などの耐食材料を用いた耐食軸受が適用されている。
半導体製造プロセスでは、さらに米Intel、韓国サムスン電子、台湾TSMCなどが現在の1.5倍となる450㎜ウェハーへと大口径化を進めている一方で、TSMCなどが2Xnmプロセスを導入し始めている。これら次世代プロセスに対し、搬送系などのメカにはさらなる高精度でクリーンな稼働が求められている。
第118回 グローバル競争に打ち勝つ工業標準化の推進を
第118回 グローバル競争に打ち勝つ工業標準化の推進を提供:大同メタル工業 経済産業省は先ごろ「平成22年度工業標準化事業表彰」を発表、機械要素分野からは、産業技術環境局長表彰で、滑り軸受の国際標準化活動への貢献が認められ、オイレス工業・特別顧問の笠原又一氏と大同メタル工業・研究開発所 業務推進室 室長の岡本 裕氏がそれぞれ受賞した。工業標準化事業表彰は、ISOなど国際規格やJIS(日本工業規格)の作成や普及に寄与し、その功績が顕著と認められる個人および組織を表彰することで、工業標準化の適切な推進と普及を促進し、わが国経済産業の発展に寄与するために制定されたもので、産業技術環境局長表彰は国際標準化活動を幅広い側面から支える関係者に対し贈られる。
市場占有率高める一方で国際標準化が遅れた日本の滑り軸受
オイレス工業の笠原又一氏は、ISO/TC123(平軸受)の国際標準化活動に参画、ISO/TC123/SC6(用語及び共通事項)の国際幹事や日本滑り軸受標準化協議会の会長を務め、標準化活動に貢献したことが認められた。また、大同メタル工業の岡本 裕氏は、ISO/TC123において国際標準の策定に尽力し製品の品質向上に貢献、またISO/TC123/SC6(用語及び共通事項)の国際幹事を務めるなど、わが国が主導的立場で標準化活動を進めることに貢献したことが認められた。
提供:大同メタル工業 流体潤滑で使用される滑り軸受は、流体膜圧力により衝撃を吸収するため、荷重変動の大きいエンジン用軸受やコンプレッサ軸受から、ポンプ軸受、タービン軸受など幅広く適用されている。油膜圧力に支持された滑り軸受では、転がり軸受よりも作動が静かで摩擦が低く、振れ回りが少ないなどからHDD(ハードディスクドライブ)のスピンドルモータ軸受などにも使われる。特にエンジン用軸受など自動車用では、わが国滑り軸受メーカーのシェアは圧倒的に高い。
しかし、滑り軸受産業においてわが国メーカーの市場占有率が高い一方で、滑り軸受に関わるわが国の国際標準化活動は欧米に後れをとっていた。わが国転がり軸受メーカーがISOされた製品をもってグローバル市場に早期に進出し、世界シェアを高めていったのとは対照的である。たとえば標準化で先行するドイツの滑り軸受企業が、自社規格(インハウス規格)をDIN(ドイツ工業規格)化しISO化するといったように、欧米では国際規格を商取引上で有利に利用するといった戦略を進めていた。
日本の国際標準化主動は経営的理解が必要
滑り軸受のISO国際標準化は、1967年に幹事国ロシアのもとに技術委員会TC123(滑り軸受)が設立、わが国では、日本機械学会の国内組織「ISO/TC 123すべり軸受調査班」(1999年4月に「ISO/TC123平軸受国内委員会」と改称)がそのオブザーバーとして参加してきた。ISO/TC123平軸受国内委員会の主査(委員長)を十数年間務めた染谷常雄氏(東京大学名誉教授)は、WTOのTBT協定が結ばれ、国内規格が非関税障壁とならないようにJISはISO に基づいてつくるべきことなどの国策が示された1995年にJIS原案作成委員会を発足、滑り軸受の損傷に関する規格ISO 7146 を翻訳しJISをつくった。しかしその翻訳作業の際に、お手本とすべきISO規格に市場を押さえているはずのわが国滑り軸受分野での理解と異なる点があることが明らかとなり、ISO規格づくりへの参画が活発化した。2000年3月にオブザーバー的なO メンバーから発言権のあるPメンバーへと資格変更になり、2004年には新たに分科委員会SC6(用語及び共通事項)を設立しその幹事国を引き受け、さらに2008年にはこれまでのTC123の幹事国ロシアに代わり幹事国を引き受けるに至った。今回の表彰は日本の滑り軸受の標準化の遅れを挽回する各位の尽力が評価されたものと言えよう。
しかし、欧州や米国で標準化活動を長期的経営戦略の中心に据える傾向にあるのに対し、わが国では依然、標準化や規格制定に関する活動の重要性に関する企業経営陣の理解が必ずしも十分ではないと言われる。前述の染谷氏は「標準化活動の本命は、有用な規格をタイムリーにつくり保守すること。TC123 の国際規格によって滑り軸受の利用度・応用範囲を高めたいと考えている。一般に国際標準を制するものは市場を制すると言われるように、ルールの範囲内ではあるが、自社・自国に都合の良い規格を積極的に作り、不都合なものはできるだけ阻止することなどの国際標準化のメリットを示すことができれば、経営者の理解も得られよう」と語っている。
中国など新興国に牽引されますますグローバル化が進む中で、技術力のあるわが国の滑り軸受を国際規格に提案する国際標準化活動は、グローバルで高品質・高性能な滑り軸受製品を提供する上で重要な役割を果たしている。滑り軸受の国際標準化事業に尽力している各位の今回の工業標準化事業表彰にあらためて敬意を表するとともに、これによってわが国滑り軸受メーカーの経営戦略として標準化活動が据えられるよう期待しつつ、ビジネス戦略上で重要な、また技術の進歩・普及に寄与する有用な規格作りが促進されることを望む。
第119回 ライフラインのさらなる安全信頼性向上を
第119回 ライフラインのさらなる安全信頼性向上を耐震配水管(提供:東京都水道局) 厚生労働省の発表によると、全国の配水管のうち震度6強相当の揺れに耐える配水管は、3割程度との調査結果が出た。国は2013年までに水道管の耐震化率100%達成を目標としているが、耐震工事実施がまだまだ必要な現状が明らかになった。調査は、川や湖などの水源から浄水施設、配水池、給水地域を結ぶ全国の主要な水道管10万735kmを対象に水道管の材質や地盤の強さごとに調べた結果、震度6強の揺れでも継目が外れない構造とされたのは、全体の30.3%、3万483kmだった。
経年寿命に達するわが国の水道管
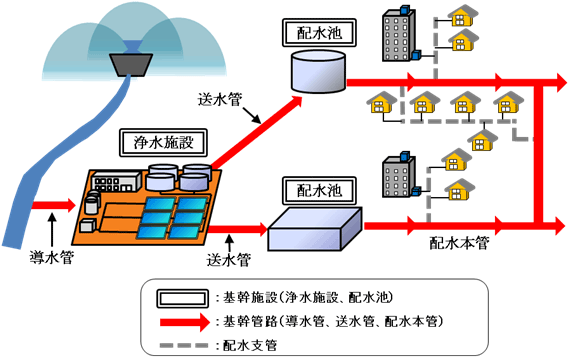
コンクリートカッター(提供:明和製作所) 水道管の耐震工事ではまず、アスファルトやコンクリートの路面をコンクリートカッターという機械で切断する。機械に搭載したOHVエンジンで円盤状のダイヤモンド砥粒ブレードを回し、クーラントとなる水をかけながらカットしていく。その後、地下1mくらいに埋設された水道管が現れるまで、土をミニショベルなどで掘り下げていく。経年菅から新しい耐震配水管にバイパスしながら置き換えていくという流れである。
ライフラインを断ち切られることのない耐震排水管を
それでは耐震配水管とはどういったものか。厚生労働省健康局の平成18年度「管路の耐震化に関する検討会」では、水道用ゴム輪形硬質塩化ビニル管RRロング継手(RRロング管)が、使用実績・期間ともに十分に耐震性能が検証されているとはいえないと注釈をつけながらも、RRロング管が基幹道路で耐震適合性のある管として採用可能と報告している。耐震適合性があるというのは、水道管を継手が抜けにくい構造である。
耐震配水管(RRロング管、提供:東京都水道局) このRRロング管とは、継手部の受口部に±75㎜の伸縮性能を持つもので、差し口突部とロックリングの引っかかりで、震度6程度の地震動による地盤ひずみを吸収できるという。また、液状化地盤などでの側方流動(地盤永久ひずみ)や地割れ・段差沈下のような地盤破壊が生じる場合には、その接合部にさらに耐震金具を適用することで±1.5%の地盤永久ひずみを吸収できるとしている。
わが国の水道は普及率が97%を超え、世界に誇る安全な飲料水を供給する、市民生活、社会活動に不可欠なもの。1995年の阪神・淡路大震災では、68の市町村で水道施設の被害が出た。重要なライフラインが不測の事態で断ち切られることのないよう、国と地方自治体には現状の3割という耐震化率を早急に改善するよう取り組んでほしい。
第120回 鉄道車両のさらなるグリーン化に向けて
第120回 鉄道車両のさらなるグリーン化に向けて次期東北新幹線はやぶさ(提供:JR東日本) この時期、帰省で新幹線を利用される方も多いと思われる。今回は新幹線の安全神話を支え、さらなるグリーン化をめざす技術を紹介したい。
本欄「第118回 グローバル競争に打ち勝つ工業標準化の推進を」で取り上げたすべり軸受、特にエンジンベアリングでは環境規制に対応した鉛フリー化が早くから進められ鉛代替が完了しているが、グリーン輸送機器である鉄道車両においても、鉛フリー化の取組みが進められてきている。
すり板に使用される潤滑剤としての鉛
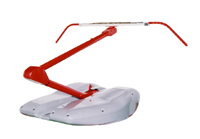
すり板から摩耗粉として排出される鉛は線路に撒かれる程度と判断されていたのかどうかは分からないが、これまで騒がれてこなかったのが、近年の環境保全の高まりから風雨などで沿線周辺の環境汚染を招くとして鉛フリー化が避けられなくなったものと見られる。
鉛に代わる固体潤滑システムとは
しかしながら前述のとおり、鉛は新幹線線の集電系の耐久信頼性を確保する上で、重要な役割を担う潤滑材である。代替となる固体潤滑システムを構築する必要がある。
新幹線用焼結合金すり板の鉛フリー化では以下の点が考慮された。
- すり板の耐摩耗性・耐アーク性を保持するための硬質金属粒子の種類と添加量
- 潤滑性を保持するための潤滑成分の種類と添加量
- トロリー線への影響を考慮した硬さの上限
- 車両集電部品として必要な導電性と機械的強度
繰り返しになるが、このうち優先されるのは2の潤滑性である。
提供:鉄道総合技術研究所 現用材は鉄(Fe)の素地に硬質成分としてチタン(Ti)、モリブデン(Mo)、クロム(Cr)などを、潤滑成分として鉛を用いている。これに対し開発材では、潤滑成分として使われていた鉛を使わない新幹線用焼結合金すり板として、鉄の素地に耐摩耗成分としてCrやクロム・バナジウム(Cr-V)を、潤滑成分として二硫化モリブデン(MoS2)を用いた材料と、耐摩耗成分としてCrを、潤滑成分としてMoS2とボロンナイトライド(BN)、ビスマス(Bi)を用いた材料を開発、定置摩耗試験、現車試験によって鉛含有の現用材と摩耗特性、トロリー線への影響が同程度であることが確認した後、現在では東北・上越・長野・山形・秋田新幹線前線で開発材2種の導入が完了しているという。
高速で大量輸送を実現する新幹線の安定走行を支えているすり板技術は、耐久信頼性の確保とともに、今や環境保全をも実現している。新幹線利用の際に、さらなるグリーン化を目指している鉄道開発者・技術者の活躍を思い出していただければ幸いである。
第121回~第130回
第121回~第130回第121回 「はやぶさプロジェクト」にわが国の誇る技術力を思う
第121回 「はやぶさプロジェクト」にわが国の誇る技術力を思う提供:JAXA 昨年末、内閣府において、約7年、60億kmの宇宙航行を経て、イトカワから約1,500個の微粒子を持ち帰った小惑星探査機「はやぶさ」プロジェクトに関わった宇宙航空研究開発機構(JAXA)のはやぶさプロジェクトチームと、それを支えた118の企業や大学などの功労者に対して、海江田万里・宇宙開発担当相と高木義明・文部科学相から感謝状が贈られた。
ヒンジ部にNTNの球面滑り軸受採用
プロジェクトチームには、探査ロボット「ミネルバ」と回収カプセルを開発したIHIエアロスペース、サンプル採取装置を開発した住友重機械工業、イオンエンジンを開発したNEC、化学推進スラスタ・イオンエンジン推進剤供給系を開発した三菱重工業などのほか、重要な機械要素である軸受のメーカーとしては、NTNが参画した。
「はやぶさ」外観(提供:JAXA)。3枚の太陽電池パネルを開くための関節部分(矢印の箇所、接合部位)にNTN製軸受が採用
「はやぶさ」に採用された球面滑り軸受(提供:NTN)衛星は打ち上げ後、その駆動源である電力を主として、宇宙空間で展開した太陽電池から得ている。太陽電池は一般に平板で効率よく発電するためには、太陽方向に対し直角に向いている必要がある。太陽電池パドル機構部(PDM)はこの動作を行う機構で、この展開駆動部となるヒンジ部(関節部位)に軸受が用いられている。「はやぶさ」では、宇宙空間で太陽電池パネルを開くためのこのヒンジ部にNTN製の球面滑り軸受が採用、宇宙空間という特殊な環境で作動し、太陽電池による電源供給を確実にする役割を果たした。
プロジェクトチームにはそのほか、固有技術を持つ多くの中小企業も参画、その中に海江田宇宙開発担当大臣が自ら視察を行った、固体潤滑被膜を手がける川邑研究所がある。
各種駆動箇所には川邑研の固体潤滑剤

(提供:住鉱潤滑剤) 宇宙空間では10-5Pa以下の真空、微小重力、原子状酸素などの環境にさらされる。この真空環境では、地上で使われているオイルやグリースなどの液体潤滑剤は蒸発による機能の大幅な低下が避けられず、真空中でも蒸発しない固体潤滑剤が用いられる。中でも層状固体潤滑剤であり、摩擦せん断時の劈開により潤滑なじみを実現する二硫化モリブデンの焼成膜などが国際宇宙ステーション(ISS)の日本実験棟「きぼう」などでも実績がある。
宇宙関係での二硫化モリブデンの適用に長年の実績を持つ川邑研究所では、「はやぶさ」でも二硫化モリブデン被膜を提供、打ち上げのロケットブースターの切り離し部や、太陽電池パドル駆動部、探査ロボットの脱着部など、各種の駆動箇所に多用されていると見られる。
「はやぶさ」を支えたこうした技術に触れた海江田宇宙開発担当大臣は、「宇宙開発は総合的な技術力が求められる裾野の広い分野で、多くの機関や企業の力を集めてはじめて成り立つもの。はやぶさの成功も、探査機の製造、打上げ、運用、回収、試料分析など様々な分野で、プロジェクトメンバー一人一人の力の結集があってこその快挙」と語っているとおり、中小企業に至るまでのわが国の世界に誇る技術力の結集によって、はやぶさは数々のトラブルに見舞われながらも奇跡の帰還を果たした。「プロジェクトメンバーの表彰は、はやぶさの成功に貢献した個々の高い技術力を顕彰する目的」(海江田氏のブログより)とのことらしいが、わが国の優れた技術力のアピールを国内にとどめていてはもったいない。はやぶさが世界的に注目される中、衛星ビジネスも少しずつではあるが立ち上がってきている。今年こそ、こうしたわが国のインフラ・システムの世界市場への輸出を本格化させられるよう、官民一体となった取組みに期待したい。
第122回 タブレット端末の操作をなめらかにするコーティング技術
第122回 タブレット端末の操作をなめらかにするコーティング技術提供:アップル ハードディスクドライブ(HDD)大手の日立グローバル ストレージテクノロジーズの堀家正充社長はある席で、「デジタルデータは年率55%で増え続けており、その中心を担うHDDはクラウド・ストレージの増大で今後も市場を拡大していくだろう。そしてそのクラウド・ストレージを押し上げるキードライバーの一つが、iPadなどのタブレット端末だ」と語った。
タブレット端末の操作をスムースに行うためのコーティング技術
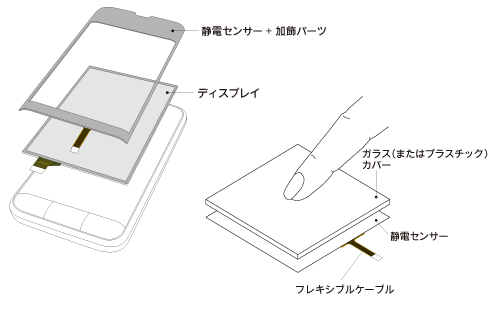
ピンチアウト(提供:アップル) iPadでは、画面上のアイコンなどを指先で軽くつつく「タップ」、画面に指をつけたまま、上下左右にずらす「ドラッグ」、指の腹で画面上をはじくような「フリック」、二本の指で画面を押さえ、その指の間隔を広げる「ピンチアウト」、二本の指で画面を押さえ、その指の間隔を狭めてものを挟むような「ピンチイン」といった動作があるが、これら動作をスムーズに行い、またガラス基材表面の耐久性を高める技術の一つが、コーティング技術である。
その代表的なコーティング技術は、基材にフッ素樹脂塗料などをディッピングまたは蒸着し、滑りの良さや指紋除去性を高めるもの。
たとえばダイキン工業が先ごろタブレット端末の市場拡大に対して増産を決めたフッ素樹脂コーティング剤「オプツールDSX」を見ると、その優れた撥水・撥油性により、タブレット機器のタッチ・スクリーンの基材であるガラスなどの表面にコーティング処理することで指紋汚れが付くのを防ぐ「防汚性」、タッチ操作をなめらかにする「表面滑り性」を付加できるほか、さらに10nm以下の極めて薄い皮膜で視認性や反射率などの光学特性にほとんど影響を与えないため、ディスプレイの見やすさを損なわないという。
OH基がガラス基材のSi基に吸着、効果を持続(提供:ダイキン工業) 同フッ素樹脂コーティング剤は、水酸基(OH基)を介した強固な化学結合によりガラス基材のSiに吸着、コーティング膜がはがれにくいことから、長期間それらの効果が持続する。
タブレット端末は、15年には10年の約10倍となる800万台の予測
こうした防汚性・潤滑性コーティング剤はダイキン工業のほかに、旭硝子や信越化学工業などが手がける。
調査会社のシード・プランニングでは、タブレット端末の2015年までの市場規模予測を実施、タブレット端末の日本市場は2台目のニーズをとらえていたネットブックと個人向けのノートパソコンの需要、業務用端末としての需要を取り込み、2015年には2010年の約10倍となる800万台の市場となると予測している。ここではタブレット端末の再表層の技術だけを取り上げたが、使われる部材は多く、iPadでもすでに、液晶ディスプレイや携帯電話高層波処理、フラッシュメモリー、水晶振動子などで日本メーカーが参入している。タブレット端末では、タッチパネルやバックライト、バッテリー、アルミフレームなどとその材料および加工技術など、わが国の強みである技術は多い。是非とも拡大基調にある市場に、その技術優位性をもってさらに食い込んでいってほしいものである。
第123回 モーターのトップランナー基準で、産業界のさらなる省エネ化の推進を!
第123回 モーターのトップランナー基準で、産業界のさらなる省エネ化の推進を!提供:日立産機システム 経済産業省は1月24日の総合資源エネルギー調査会第16回省エネルギー基準部会を開催、温室効果ガス削減に向け自動車や家電製品、OA機器などのエネルギー消費効率の改善をメーカーに求める「トップランナー基準」について、現行の対象機器は基準の見直しを進めるほか、新たに主要な産業用モーターである三相誘導モーターを対象機器に追加することを決めた。
「トップランナー基準」対象機器に三相誘導モーターを追加
トップランナー基準は1999年に導入された省エネ規制で、商品化された製品で最もエネルギー消費効率の高いもの(トップランナー)を基準として、機器メーカーにその効率を達成する省エネ型製品の製造を求めるもの。現在、自動車や家電製品、OA機器など23品目を対象に、品目ごとにエネルギー消費効率の目標基準値、製品区分、目標年度、基準値達成の判定方法などを規定。目標年度に基準値を達成できなかったメーカーに対しては、経済産業大臣による勧告や社名の公表、命令などの措置に加え、罰金が課せられる(省エネ法による)。トップランナー基準導入により、たとえばルームエアコンでは導入前に比べエネルギー消費効率を68%改善しているという。
三相誘導モーターはブラシや整流子がなく堅牢構造でメンテナンスフリーで使えること、周波数と電圧の制御(VVVFインバータ制御)が可能なことなどから、国内で年間1,000万台弱が出荷、1億台を超える機器が国内で普及しポンプ、圧縮機、送風機から、工作機械、新幹線に至るまで、各種産業用機械に幅広く採用されている。しかし、三相誘導モーターによる電力消費量は、わが国における産業用電力消費量(約4,900億kWh)の約75%と推計されるほか、電力消費量全体(約1兆kWh)の50%超を占める。
米国では1997年に施行されたエネルギー政策法(EPAct)に代わり、2010年12月19日にはエネルギー独立安全保障法(EISA)が施行され、その中で米国内で製造・輸入されるモーターの効率が規制、これまでEPAct(IE2レベル)効率が適用されていた機種にはPremium(IE3レベル)効率の使用を、規制対象外だった機種にはEPAct効率の使用を義務付けており、効率基準を満たさないモーターとモーターが組み込まれた製品が販売された場合にはペナルティーが課せられる。欧州でも同様の高効率化が進んでいるのに対し、わが国は、ロシアやインドとならんで効率規制が取られておらず、トップランナー基準によって三相誘導モーターの標準品から高効率品への移行を促すことで、産業分野での省エネ化の推進をねらうもの。
メカニカル・ロスを抑制し、さらなる省エネ化へ
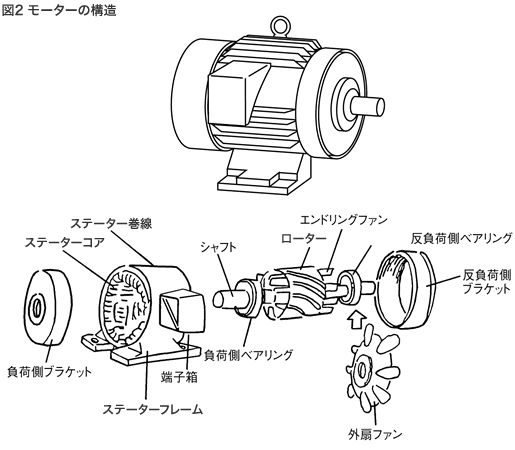
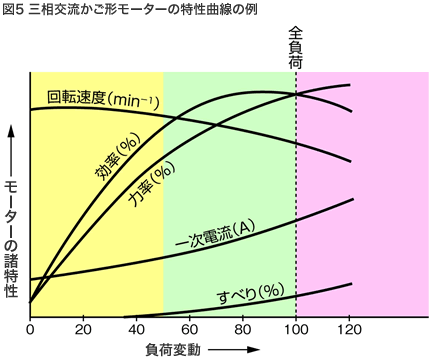
モーターの効率は一般的に次のように表される。
効率(%)=出力/入力×100=(入力―損失)/入力×100
つまり出力=(入力-損失)から、損失は(入力-出力)として定義される。損失は、モーター内で熱、振動、音などのエネルギーに変わってしまうもので、銅損、鉄損などの電気的な損失と、ベアリングの摩擦損失や冷却ファン損失による機械的な損失などからなる。
電気的な損失に対しては、高磁束密度鉄心の開発や電線充填量の高密度化などで高効率化が図られている。メカニカルな損失に対しては、軸受ハウジング部の冷却性能向上により軸受の発熱を抑えたり、軸受に封入するグリースの配合を変えるなどで低トルク化を図っている。
仮にすべてのモーターが高効率モーターに転換された場合、わが国電力消費量全体の約1.5%にあたる年間約155億kWh、温室効果ガス排出量(12億8,200万t)の約0.4%に相当する約500万t-CO2 が削減されるという。トップランナー基準対象機器への三相誘導モーターの追加により、ベアリング技術などメカニカル・ロスをなくす技術開発が促進され、産業界のさらなる省エネ化が図られるよう期待したい。
第124回 建設機械の省エネ化がグローバルで進展
第124回 建設機械の省エネ化がグローバルで進展ハイブリッド油圧ショベル(提供:コマツ) 日本建設機械工業会が先ごろ発表した2010年の建設機械出荷額は、前年比59%増の1兆8,489億円と、2年ぶりのプラスとなった。中国をはじめ新興国向けを中心に輸出が2倍近くに急増、特に油圧ショベルが前年の2.1倍に増え、出荷額を押し上げた。そうした中、新興国向けを含めたグローバルでの建機の省エネ化が進んでいる。
建設機械におけるシール、作動油の省エネ化
建設機械ではディーゼルエンジンを回して油圧ポンプを駆動し、油圧作動油をブームシリンダやアームシリンダ、バケットシリンダといったアクチュエータに送り、車体各部を作動させる。油圧作動油を用途別に見ると建機向けが5割強というから、油圧機器もまたその主要用途は建機と言えるだろう。油圧機器に使われるパッキンの某メーカーでは、業績がリーマンショック前の9割近くまで回復、生産をスリム化していたため受注の急増に対してうれしい悲鳴を上げているという。
油圧シリンダ(提供:KYB) さて、油圧機器の省エネ技術を見ると、350気圧といった高圧シリンダにおいて、油圧作動油の密封性を高めつつ作動時の摩擦を少なくするPTFE製のシールリングと合成ゴム製Oリングを組み合わせたロッドシールなどが用いられている。シールの摺動面にダイヤモンドライクカーボンコーティングを施して、さらに低摩擦化し省エネ化につなげようという取組みも進められている。
また、油圧作動油でも省エネ化が進められている。高粘度指数(高VI)基油と非金属系の添加剤を使うことなどで、低温における始動トルクが小さく動力損失を軽減できるほか、高圧・高温化でも配管詰まりの原因となるスラッジの発生を抑え、エネルギー損失を抑えることができるという。
油圧機器とモーターのハイブリッド化による省エネ化
こうした油圧機器におけるメカニカルな省エネ化の取組みの一方で、油圧機器とモーターとのハイブリッド化による省エネ化も進められている。
コマツでは先ごろ、新型ハイブリッド油圧ショベルを開発、すでに日本で販売を開始し今後は北米、中国、中南米、東南アジア、欧州などへも販売を拡大する予定だ。独自ハイブリッドシステムにより、車体旋回の減速時に発生するエネルギーを旋回電気モーターで電気エネルギーに変換してキャパシター(蓄電器)に蓄え、発電機モーターを通じてエンジン加速時の補助エネルギーに活用することで、大幅な燃料消費量の低減を実現する。また、必要な吐出量を確保しながら、日米欧の排出ガス規制に対応したエンジンの回転を低く抑えるエンジン・ポンプマッチング制御を採用、燃費効率の良いところでエンジン回転とポンプの吐出量をマッチングさせることで燃費低減を図るという。
世界中の建設現場で使われる建設機械では、早くから生分解性の作動油を採用するなど環境対応への取組みがなされてきたが、さらに動力損失や使用電力を抑える技術的取組みが強まってきている。わが国の得意とする油圧ショベルなど建設機械において、わが国の誇る省エネ技術が搭載されることによって、建設機械の市場拡大が促進されるよう期待したい。
第125回 難削材の加工機械・技術が注目
第125回 難削材の加工機械・技術が注目高精度・高効率複合加工機(提供:森精機製作所) 日本工作機械工業会は先ごろ、2010年の工作機械の受注額が前年比2.4倍の9,783億円と大幅に増加したと発表、2011年の受注については3年ぶりの1兆円台となる1兆1,000億円となる見通しを打ち出した。中国などアジアをはじめ、欧州、北米、日本ともに需要が回復しているが、自動車や航空機などの精密部品、特に難削材の加工に適した日本の工作機械・加工技術が注目されているという。
航空機の機体材料はアルミニウムが大半を占めていたが近年は軽量化による燃費向上を目的に、CFRP(炭素繊維強化プラスチック)の比率が構造部材重量の半分を占めるまでに多用され、CFRPと相性が良いチタン合金も様々な部位で使用されるようになった。チタン合金は軽く、強く、錆びないという特性を持つ反面、熱伝導率が低く、靭性が高く、切削速度を上げると急激に工具摩耗が起こるため、難削材と言われる。このほか燃焼室回りに使用される耐熱性の高いインコネルなどのNi基合金の材料も同様に難削材である。
一方、航空機部品では軽量・高剛性化を図るべく、ねじなどによる締結方法をとらないため部品単体の形状が複雑となり、旋削機能も含めた高剛性で高精度な5軸複合加工機が必要となる。5軸複合加工機1台に工程集約できるようになり、工程間の搬送や段取り時間の削減、加工精度のバラツキを抑え、航空機部品の生産性向上に大きく寄与している。
5軸制御マシニングセンタ(提供:牧野フライス製作所) こうした難削材の加工に対して、たとえば牧野フライス製作所の5軸制御マシニングセンタ「T2/T4」では、高トルク(1000/1500N・m)の主軸により、重切削での耐久性と高速性、高精度といった高能率加工を実現、また200L/min(7MPa)のクーラントが切屑を速やかに除去するほか、難削材の重切削加工で発生する振動を高剛性の本体構造により低減することで、チタン合金の加工時間を従来の1/4に減らし、工具寿命を2倍に高めているという。
こうした難削材に対応する高剛性、高精度の工作機械構造が工夫される一方で、工具においても難削材の加工に対応する技術も進んできている。
提供:三菱マテリアルツールズ 三菱マテリアルでは先ごろ、高い比強度を持つ反面、炭素繊維が高強度であるため工具寿命が極端に短く、積層体構造であるために穴加工時にデラミネーション(層間剥離)が発生しやすいCFRPや、CFRPとアルミニウム合金の重ね板の穴加工に特化した「MCS形」を開発した。切刃デザインと新開発の多層微粒CVDダイヤモンドコーティングの採用により優れた穴精度と長寿命を実現したほか、独自の素材成形技術によるユニークなクーラント穴を付加することで、特にCFRPとアルミニウム合金の重ね板加工をする際の切りくず排出性が向上、高い穴精度を実現している。
日立ツールの「エポックDスレッドミル」では結晶粒子がさらに微細化したSi系ナノコンポジットコーティングをPVD(物理気相成長)処理、3800HVの硬度と1200℃の耐酸化温度を実現、1本の工具で高硬度材における下穴+ねじ切り加工を可能にしている。
航空機だけでなく、無害で耐摩耗性、耐食性、人体との親和性が要求される人工関節などのインプラント製品にも、コバルトクロム合金、チタン合金、セラミック系のジルコニアなどの難削材が用いられる。人工骨、人工歯などインプラント製品もまた形状が複雑なことから、工作機械にはCAMによる加工プログラムや、難削材に対応した機械剛性、高速、高精度加工が求められる。森精機製作所では旋削とミーリングを融合した高精度・高効率複合加工機「NT1000」を用いて、これまでエンドミル加工していた人工大腿骨コンポーネントのR 形状を、CBN砥石を使用して加工することで加工時間を大幅に短縮。難削材の加工にもかかわらず、エンドミルに比べて工具寿命が長く、工具費用を大幅に抑えることができるほか、ワークを2個取り付けることで加工効率が向上した、としている。
航空機、医療機器など複雑形状の難加工が必要とされるアプリケーションが増えてきている。中国、韓国などアジア勢の工作機械の生産が拡大してきているが、わが国の得意とする高精度・高速・高剛性で複合加工に対応するマシニングセンタや難削材加工での高能率化を実現するコーティング工具などの高付加価値技術で差別化を図り、工作機械産業のさらなる市場拡大に努めてほしい。
第126回 nano tech 2011/ASTEC 2011に見る、表面改質/計測・評価技術
第126回 nano tech 2011/ASTEC 2011に見る、表面改質/計測・評価技術 「nano tech 2011 国際ナノテクノロジー総合展・技術会議」や「ASTEC 2011 国際先端表面技術展・会議」、「METEC2011 第40回表面処理材料総合展」など9展が2月16日~ 18日、東京ビッグサイトで同時開催された。
グリーンナノテクノロジーでDLCなど薄膜技術を展示
今回の9展示会共通テーマは「グリーン・ナノテクノロジー 10-9がつくる環境力」。10のマイナス9乗メートルはナノメートルで、グリーン・ナノテクノロジーとは、ナノメートル(nm)レベルの薄膜や微粒子を使って、自動車関連の次世代二次電池、LED照明、新エネルギー技術、土壌・水質浄化など環境問題の解決に役立つ製品を創出する技術。
今回は主にASTEC2011 やMETEC2011でナノレベルの表面改質技術が、nano tech 2011でカーボンナノチューブなどのナノ粒子や、微粒子や薄膜の計測・評価技術が展示された。
出展されたグリーン・ナノテクノロジーとしては、たとえば潤滑剤に頼らずフリクションを低減することで省エネに、耐摩耗性を高めることで省資源化につなげるDLC(ダイヤモンドライクカーボン)膜がある。
接触角が大きく水を弾く撥水性ICF(提供:ナノテック) ナノテックでは単に硬質で摩擦係数が低いDLCにとどまらず、DLC薄膜の特性を物性により分類したICF(Intrinsic Carbon Film:真性カーボン膜)を開発、たとえばクロムめっきの代替や各種金属溶出防止膜として、高硬度、低摩擦係数、耐摩耗性で、めっきからの代替を可能にすべく大面積の成膜が可能な環境調和型ICFや、フッ素(F)ドーピングとコーティング条件の工夫で、水を弾く特性を持たせた撥水性ICFなどを提起している。
プラズマイオンアシストでは微細複雑形状に成膜でき流路側面、底面に均一な成膜が可能で、高い耐食性と金と同等の接触抵抗を持ち、燃料電池セパレーターなどへの適用が可能な高導電性DLCなどを出展した。
薄膜の計測・評価技術
DLCなど薄膜の計測・評価技術としては、0.01nmの押し込み分解能を持つためバルク材の影響を受けずに薄膜自体の機械的強度を測定できるナノインデンターなどが、東陽テクニカから展示された。
この機械的特性を非接触で測る手法としてまた、DLC薄膜からの反射光の偏光状態から、硬さや密度と相関性がある膜の屈折率や消衰係数が求められる分光エリプソメータなどの展示も見られた。
また、先の撥水性ICFなどのような膜の撥水性を見る手法として、解析ソフトウェアと組み合わせて、動的接触角(拡張/収縮、滑落・界面張力の測定や表面自由エネルギー解析も可能とする各種接触角計が、協和界面科学から出展された。
三次元顕微レーザーラマン分光装置(提供:東京インスツルメンツ) DLC薄膜に照射した光の散乱光(ラマン散乱光)を分光測定するラマン分光装置も展示、DLC膜の構造解析の中でも、DLC膜の諸特性に大きな影響を及ぼす水素濃度を把握しDLC薄膜を作り分けるのに有効な手法として、提案された。
第127回 ベアリングの大型化で期待されるメカ技術
第127回 ベアリングの大型化で期待されるメカ技術提供:Vestas社 航空機や建設機械など大型機械、さらにはそれらを加工する大型工作機械の需要が増加してきている。また、新興国の経済成長に伴う医療・福祉の向上などから、医療機器、中でもがんの早期発見につながるCTスキャン装置の市場が、グローバルで拡大基調にある。
ガントリの大口径化とともに大型化するCTスキャン用ベアリング
世界市場でのこうした大型構造物の増加に伴い、それら機械装置の回転機構を支えるボールベアリングもまた、大型化してきている。
こうした大型軸受の需要拡大に対して、ベアリングの追加加工を手掛ける日本軸受加工では、大型ベアリング専用の工場設置や設備投資を進めている。
ベアリングが高速回転することで温度上昇が起こり、軸受材料が熱膨張して適正なラジアルすき間が維持できないことがある。こうした事態に備えた軸受ユーザーからの委託により日本軸受加工では、軌道面をミクロン単位で研磨し、すき間の手直しを行っている。
また、高速回転に伴う発熱対策として、工作機械主軸の組み合わせアンギュラ玉軸受の間座の給油孔の加工なども、工作機械の仕様に合わせて行う。
同社の大型ベアリングへの加工は、大型工作機械のテーブル用ベアリングなどで実績がある。たとえば、独シェフラー社で外径4,000㎜強まで対応するアキシアル・ラジアル複合ころ軸受などがラインナップされている、あれである。
同社の伊藤正憲社長は、「CTスキャン装置のベアリングは現在、内径900㎜程度のものが多いが、内径1m超まで大型化した設計がなされてきている」という。
提供:NTN
CTスキャナ用低振動軸受(提供:NTN) CTスキャン装置では、患者が横たわったベッドがガントリ部に進入、その際にガントリ部が患者の周りを回転してX線撮影する。このガントリ部が大口径化することで、欧米人のように体格の大きな患者でも検査できるようになる。また、人体の患部がガントリ部の中央に位置するときに鮮明な画像が得られることなどから、大口径化により心臓を診る時などにはベッドをオフセットさせ患部が中央にくるよう位置決めできるようになる。確かに、ガントリの大口径化とともにベアリングは大型化する傾向にあり、精密画像を得るために振動を抑制したNTNの「CTスキャナ用低振動軸受」では、軸受外径が1,200㎜に及ぶ。
風力発電機では外径1,580㎜のベアリングも
また、風力発電機では、出力1.5MW級で外径1,000㎜程度だったベアリングが、国内最大級の出力2.4MW風車向けのベアリングでは外径1,580㎜に及ぶ(NTN)。
こうした大型ベアリングの加工の需要に対して、日本軸受加工では大型研削盤を導入、伊藤社長の設計により、外径、内径を同時に研削できる機械や、軸受の姿勢を90°変えられ、複合加工ができる機械なども稼働しているという。
風力発電機を開発する某社によれば、「風力発電機の高出力化に伴いそのベアリングもかつてない大型化が進展、経験のない大型化から予期せぬ故障もあった」としているが、この風力発電機ひとつをとっても、実際の使用にあたっては仕様に合わせた各種の加工や、使用条件に合わせた潤滑技術、潤滑剤を異物から守り機能させるオイルシールの技術、長期耐久性を実現する軸受の高清浄度鋼技術など、複合的な取り組みが必要とされる。もちろん1社のみで対応できることではない。先の日本軸受加工でも、熱処理など表面改質や、内・外輪への歯切り加工などは協力企業に外注するという。新しいアプリケーションには、既存の技術ネットワークだけでなく、新たな技術リソースも模索し、活用していかなくてはならない。
かつてないベアリングの大型化に伴う経験のない使用に対しては、中小企業の光る技が活躍する場面が、まだまだ多そうである。
第128回 PV EXPO 2011に見る機械加工技術
第128回 PV EXPO 2011に見る機械加工技術 「PV EXPO2011 第4回国際太陽電池展」が3月2日~4日、東京・有明の東京ビッグサイトで開催された。同展は、太陽光発電業界国内最大の国際商談展示会として、世界各国の太陽光発電システムのほか太陽光発電関連の製造装置、部品・材料、検査・測定・分析装置などが多数展示された。
太陽光発電協会がまとめた2010年の国内太陽電池セル・モジュールの出荷統計によると、2010年の国内総出荷は発電能力ベースで前年比205%の991,920kWとなり、2年連続で対前年2倍増となった。材料別では、結晶シリコン系(Si単結晶+Si多結晶)が2,090,156kW(前年比172.3%)、シリコン薄膜系が269,522kW(前年比186.3%)、その他が77,348kW(前年比262.8%)だった。材料別の構成比はSi多結晶が50.8%、Si単結晶が34.9%、Si薄膜が11.1%だった。
結晶シリコン系太陽電池の製造工程と主な評価機器(提供:堀場製作所) この市場の大半を占める結晶シリコン系の製造工程を見ると、大まかには電着バンドソーなどによりシリコンインゴットをブロックに切断した後、それをウェハにスライス切断(ウェハリング)し、ウェハを洗浄、続いてテクスチャーを形成し、その後pn接合形成(熱拡散)→酸化膜除去→反射防止膜形成→電極形成→硬化/焼成→封止という工程をとる。
太陽電池市場における競争がグローバルで激化する中、コスト競争力向上につながる生産性を高める加工技術が要求されている。
電着ダイヤモンドワイヤソー(提供:旭ダイヤモンド工業) ウェハリングを行う加工技術としては、たとえば旭ダイヤモンド工業が電着ダイヤモンドワイヤ「エコメップ」を出展していた。これは、高張力ワイヤにダイヤモンド砥粒を「電着」と呼ばれるめっき技術で付着させた固定砥粒工具。従来の石油系研削油と研磨材を用いて鋼線で切断する遊離砥粒方式に比べ、このシリコンのほか、LED基板であるサファイヤなど硬脆材料をスライスする切断時間を約1/3に短縮できるほか、切り代や加工歪みが低減され歩留まり向上が期待できるという。また水性切削液を使用するため切り粉の回収や再資源化が行え、トータルコストダウンが図れる。
クラレアクアでは、こうしたワイヤソー(ウェハリング)工程でシリコンの切り粉などが混じった切削液をフィルターで分離し、切削液を回収しリサイクルする機器を展示した。切削液が再利用でき加工にかかる費用が低減できることや産廃費用を圧縮できることなどから、装置を導入しても1年程度で償却でき、その後はそのままコスト削減に直結するとしている。
結晶系太陽電池の構造(提供:産業技術総合研究所) 結晶系太陽電池では、モジュール用ガラスのセル表面の反射率を低減し、受光した太陽光を閉じ込める(受光量を増やす)ため、エッチング装置(テクスチャリング装置)を使って、ウェハ表面に凹凸構造(テクスチャー)を形成する。
さらにこのテクスチャー形成に加えて、光の表面反射をより低減させる目的で、プラズマCVD装置を用いて、セル表面に複数の薄膜層からなる反射防止膜を形成する。
テクスチャーの三次元測定(提供:オリンパス) PV EXPOではこのテクスチャリング装置(ワイエイシイなど)や反射防止膜成膜装置(島津製作所など)などが出展されたほか、テクスチャー構造の観察・評価のための三次元形状測定器(オリンパスなど)や、反射防止膜の評価分析サービス(コベルコ科研など)などもアピールされた。
太陽電池の発電効率を高めるための加工技術は多様で、それぞれに計測評価の技術がある。太陽電池の市場規模は2010年の2兆円強に対して、2025年には4倍以上の8兆円強が見込まれているが、PV EXPO2011の展示を見て、こうした要素技術の急速な開発・実用化により市場規模が押し上げられていくものと実感できた。
第129回 東日本大震災の被害者救済と復旧を願う
第129回 東日本大震災の被害者救済と復旧を願う3月11日14時46分に始まった「東日本大震災」による被害が拡大している。国内観測史上最大のマグニチュード9の大地震と、波の高さが7mにも及んだ津波によって町は防備するまもなくのみこまれ、家屋が流され、火災に見舞われた。はじめに、震災で亡くなられた方々のご冥福を祈りたい。また、一人でも多くの方が救済されることを願っている。
記者は地震発生時、東京にあったため、JRおよび私鉄の全線が運行を止めたことで帰宅難民になった程度に過ぎない。しかし、幾多の震災を経て防災システムが整備されてきたとはいえ、あらゆる地震に対して万全の備えなどないということは実感できた。
その後の数回の余震を考えると、二次被害を抑えるべく電車を止め、線路の異常や車輪の浮き上がり、架線の摩耗など、点検を進め復旧に備えた鉄道関係者の判断を讃えたい。鉄道の安全神話はまずまず守られたといってよいのではないだろうか。
一方、原子力発電所の対応はどうだっただろうか。東京電力福島第一原子力発電所1号機が爆発し、周辺住民の約100名が被爆した。原子力発電機は放射性物質を①核分裂生成物を閉じこめた「ペレット」、②ペレットからじわじわと拡散する核分裂生成物を封じ込めつつペレットから放出された熱を外側の冷却材に逃がす「燃料被覆管」、③冷却材が封じ込められた一次圧力バウンダリ、④捨てる冷却材を封じ込める「原子炉格納容器」、⑤「原子炉建屋」という五つのバリアが機能する、安全なシステムのはずだった。このうち、高温・高圧下にあるペレットと燃料被覆管には特に注意が払われる。
ペレットは酸化ウランの粉末を圧縮して焼結したセラミックスでできており高温に強いが、薄い肉厚の金属のチューブである燃料被覆管はペレットの熱を素早く外側の冷却材に伝えることで自身が加熱されるのを防いでいる。今回は原子炉内の水位が下がり炉心が露出、燃料の温度が上昇し燃料被覆管が溶ける「炉心溶融」が起こり、水素爆発に至ったと見られる。
ここに至る経緯としては、冷却機能を補うはずのディーゼル発電機が作動しなかった、さらに冷却水を補充するためのポンプ車などの手配も遅れたようだ。こちらは原発ルネッサンスと叫ばれる中、強く求められる安全信頼性の回復に応えられなかった。今回の対応を振り返りながら、今後より徹底した安全対策が図られるよう生かしてほしい。
また、地震発生後30分も経たないうちに大津波が発生し、自動車よりも速いスピードで瞬く間に町をのみこんでいった。今回の未曾有の津波に対して対策の立てられようもなかっただろうが、これまでも声高に繰り返されているとおり引き続きの津波対策としては、高い堤防および防波堤の設置などハード面と、地震発生から津波発生に至るまでの早期の津波情報の提供や避難対策の充実などソフト面のさらなる強化が、国と地方自治体の課題と言えよう。
専門家によれば、今後3ヵ月はマグニチュード8の可能性もある大きな余震への注意が必要、としている。引き続き、できうる限りの防災対策を施していかなくてはならない。これ以上の人命を危険にさらすことはあってはならない。家屋や工場、生産施設などの損壊を招いてはならない。
あらためて被害に遭われた方々に追悼の意を表するとともに、今後一人でも多くの人命が救われることを、また被災地の少しでも早い復興がなされることを、ただただ願うばかりである。
第130回 メンテナンス活動から、ものづくり産業の復活・拡大へ
第130回 メンテナンス活動から、ものづくり産業の復活・拡大へ東日本大震災に伴う津波で建物が全壊した宮城県南三陸町志津川のガソリンスタンドで先日、地下タンクから足こぎ式ポンプを使ってガソリンをくみ上げる作業が行われた。地下タンクに吸引ホースを差し込んでペダルをこぐと、3回転で1Lのガソリンをくみ上げられるという。緊急車両や避難所の発電機などへの給油がなされた。
津波被災地のスタンドの多くで給油機が流失しているが、地下にあるタンクは破損していないものも多い。国内石油元売り最大手のJX日鉱日石エネルギーのENEOS系スタンドでも、東北地方にあるスタンドのうち1,000件程度の地下タンクで漏洩がないことが確認できており、系列のメンテナンス企業が復旧工事に取りかかり始めたという。
ガソリンスタンドの構造 ガソリンスタンドには地下5m程度の深さにそれぞれレギュラーガソリン、ハイオクガソリン、軽油、灯油のタンクが埋設され、各々から配管がなされ、燃料をくみ上げ給油する計量機(給油機)に接続されている。
今回の津波被害により地上にある給油機は流されているものの、破損していないタンクであれば配管工事と給油機設置で早い時期にガソリンスタンドを再開できるという。依然、東北地方での燃料供給が逼迫する中、メンテナンス作業が急がれる。
こうしたガソリンスタンドをはじめ、これまで円滑に稼働しているときには陰の立て役者であったメンテナンス事業の活躍が今まさに期待されている。原子力発電所の事故収拾は最たるものであろう。
メンテナンス作業をはじめ、冒頭に紹介した足こぎポンプによる給油活動に見るように、また自動車部品メーカーなどの工場復旧に向け自動車メーカーや工作機械メーカー、計測器メーカーなどが支援に動き、徐々にではあるが操業が再開されてきているように、できることから取りかかり、我々は前進していかなくてはならない。
震災による国民生活、産業界への打撃は確かにはかりきれないが、そうした先行きの不透明性からシュリンクするのではなく、一人一人が希望を持って、アクティブな活動を再始動したい。わが国のものづくり産業の復活、さらには成長に向けて。
第131回~第140回
第131回~第140回第131回 計測・分析技術の適用促進で、風評被害の防止を
第131回 計測・分析技術の適用促進で、風評被害の防止をエネルギー分散型蛍光X線分析装置(提供:パナリティカル) 東京電力福島第一原子力発電所からの放射性物質の流出が広がるなか、被害を受けている福島県と近隣の自治体に対して、堀場製作所が環境放射線モニター100台を寄贈した。同製品は、同社が平成23年度からの中学校・高校の放射線学習導入に先駆け2009年に発売したもので、0.001~9.999マイクロシーベルト/毎時の放射線(ガンマ線)を検知、自然界や生活環境にある微弱な放射線から、その100~200倍程度の放射線までを1分で計測できる。被災者が正確な放射線の情報を把握し安心感を得られるよう、もてる技術の一端を提供した同社の支援活動を讃えたい。
同様に放射性物質の流出に関連して、分析技術も注目され、適用が進んでいる。
たとえば、さまざまな物質の元素組成の同定に使用する蛍光X線分析(XRF)がある。この手法は、各種コーティング層の厚みや組成の測定・分析のほか、潤滑油中の摩耗粉の分析などにも使われる。
左がEDXRF、右がWDXRFの原理(提供:パナリティカル) 蛍光X線装置は検出方法の違いから、エネルギー分散型蛍光X線分析装置(EDXRF)と波長分散型蛍光X線分析装置(WDXRF)の2種類に大別されるが、そのうち試料から直接放出される特性X線の異なるエネルギーを測定できるエネルギー分散型蛍光X線分析装置が、短時間で正確に非破壊分析を行える手法として有望視されている。
たとえば、カドミニウム、鉛、水銀、ヒ素など環境負荷物質である重金属の非破壊分析でサブppmレベルの微量検出能力を持つパナリティカルのエネルギー分散型蛍光X線分析装置「Epsilon5」が、ヨウ素やセシウムなどのスクリーニング分析に使われている。国立環境研究所が頒布する環境標準資料NIES CRM No.9(海藻ホンダワラから調整した天然試料)を用いて、京都大学原子炉実験所が同X線分析装置によるヨウ素の感度測定を実施したところ、ヨウ素の検出下限値が0.64ppm(600秒)で、さらにノンスタンダード(F.P.)定量結果でも標準値との差が相対値で4.1%となり、スクリーニング分析として測定時間、測定精度ともに実用性が実証されている。すでに各種の分析機関に納入され、風評被害が始まっている、被災地における食品などの放射能汚染の分析を目的に納入が進んでいるという。
海外においても、日本からの輸入製品に対して一時は警戒態勢にあったが、各種のスクリーニング分析によって安全性が確認されるとともに、欧州を中心に警戒感が緩みつつあるようだ。市場で実績のあるこうした計測・分析技術が放射能汚染の評価に転用され、風評被害の広まりを阻止し、日本経済を少しでも下支えしてくれるよう期待したい。
第132回 EVの高性能化に向け、部品・材料開発が進展
第132回 EVの高性能化に向け、部品・材料開発が進展SIM-LEI(提供:シムドライブ) 東日本大震災によりガソリンの供給が混乱した中、被災地で救援物資を運ぶ支援車両として、三菱自動車のi-MIEVや日産自動車のリーフなど電気自動車(EV)が現地に相次いで投入され活躍した。ガソリンが出回るよりも電気が早く復旧したことや、電力需要の少ない夜間に充電できることも、EVが重宝された理由で、航続距離が短いという最大の難点も、地域間の連絡手段としては十分に機能したようだ。
さて、EVが予期せぬ場面で注目される中、この航続距離を1充電あたり333kmに延長するというEVが、お披露目された。慶應大学ベンチャーのシムドライブ社が2013年頃の量産化をめざし進めてきた、先行開発車事業第1号の車両「SIM-LEI」だ。性能目標はEV普及の上で最大の課題となる航続距離を300km以上に延長することだったが、完成した車両は何とJCO8モードで同333kmを打ち出した。この航続距離伸長にはタイヤホイールの中にモーターを内蔵させトランスミッションやシャフトをなくしたインホイールモーターの技術などが貢献している。エンジンの代わりにモーターを搭載する方式に比べ、30%以上航続距離を延ばせるという。
インホイールモーター(提供:NTN) 今回採用したインホイールモーターは、減速機を用いずにローターを外側に配置するダイレクトドライブ方式だが、インホイールモーターとしてはこのほか、NTNが開発を進めるギヤリダクション方式がある。NTNでは、モータートルクを増幅してタイヤに伝えることが可能な世界最高速、高効率、高負荷容量、高減速比の「サイクロイド式減速機構」を採用しつつ、同社の高精度•長寿命転がり軸受技術を用いることで、サイクロイド減速機構の速度限界と負荷容量の限界を、電気自動車で利用できるレベルまで向上させることに成功した。
エンジンの代わりにモーターを置いて、車軸やギヤなどを介して動力伝達を行う現行のEVにせよ、インホールモーター式のEVにせよ、駆動源となるモーターの技術の改良がバッテリー消費を減らす上で重要であろう。
先のシムドライブ社では、2014年頃に参加企業による量産化をめざして、先行開発車事業第2号を本年から開始しているが、今回は化学材料の適用を拡大している点に特徴がある。金属材料に替わる耐久性があり軽量化が図れるエンジニアリングプラスチックを手がけるポリプラスチックス社、同じく炭素繊維強化プラスチックス(CFRP)などを手がける東レなどがプロジェクトに参加しているわけだが、軽量化によってモーターの回転負荷を減らしエネルギー消費を減らそうというねらいであろう。無給油ベアリングのオイレス工業や表面改質処理の日本パーカライジングのプロジェクト参画も無関係ではないであろう。
シムドライブ社ではプロジェクト終了後は参加企業がそこで培った技術を自由に利用して良いとしている。そうしてEV専用の技術開発が進むことで、EVの航続距離や耐久性の問題も徐々に改善されていくだろう。
しかし3月に自己破産申請したゼロスポーツのように、EVとして優れた技術開発を進めながらも、改造後の品質保証の問題などで自動車メーカーからの車体調達が難航し、事業が行き詰まった例もある。EV専用部品・材料の開発が進む中、EV市場のさらなる拡大に向けて、そうしたEVコンポーネントの積み替えといった規制緩和や量産での実績が豊富な自動車メーカーとの協調体制などへの期待が高まってきている。
第133回 DLCコーティングの標準化で成長戦略の推進を
第133回 DLCコーティングの標準化で成長戦略の推進をDLCの物性制御のコンセプト(提供:ナノテック) ニューダイヤモンドフォーラムが5月11日、「平成23年定時会員総会」を開催した。同フォーラムは1985年に設立、CVDダイヤモンドを中心とするニューダイヤモンドの技術開発、ならびに新用途分野開発に向けて、産学官の研究者・技術者の情報交換・相互研鑽を通して、ニューダイヤモンドの発展を追求してきた。さらに近年は、ダイヤモンド、ダイヤモンドライクカーボン(DLC)、フラーレン、カーボンナノチューブなどのカーボン系高機能材料技術の実用化推進をめざし、受託調査研究などを実施、わが国産業の発展に寄与することも目的としている。
同フォーラムでは、 以前「mst」で紹介したとおり、平成21年度より受託事業として、「ダイヤモンドライクカーボン膜および評価技術に関する標準化」プロジェクトを推進している。DLCはカーボン系材料の中でも、金型、工具から自動車部品まで、近年特に産業化が進んでいる材料であり、カーボン系材料でわが国産業の発展に寄与する使命を掲げる同フォーラムとしても、その標準化による市場拡大は、注力しているプロジェクトの一つと言えよう。
ところで、総会当日は未踏技術協会理事長の木村茂行氏による「グリーンテクノロジー政策と学術の寄与」と題する特別講演が行われた。総合科学技術会議の策定した第4基基本計画の中で研究開発の中核に位置づけているグリーン・イノベーションとライフ・イノベーションの概要を説明、学術の成果活用でこうした社会要請に応える道と、本来の学術活動に専念する道をともに模索するアプローチを示唆した。
環境大国を目指すグリーン・イノベーション政策と、健康大国を目指すライフ・イノベーション政策。
グリーン・イノベーション政策では、その柱である“太陽光発電の飛躍的な性能向上と低コスト化”に。シリコンと同等の半導体特性および共有結合を主体とした構造を有する炭素材料、中でも耐久性が高く低コスト化が可能なDLCの適用が検討されている。
また、ライフ・イノベーション政策では、医療機器、特に人体に埋め込まれる人工関節やカテーテルのステント材料など、耐久性と生体適合性が必要とされる用途でDLCの適用研究が進んでいる。
DLCが幅広い用途で適用されているのは、ダイヤモンドからグラファイト、ポリマーライクまで広範な物性を発現できるという点が大きいが、反面、その広範な特性を示すコーティングをDLCと一括りにしていることで、ユーザーが適用する場合に混乱を招き、市場の拡大を阻害しているという一面もある。
DLCを早くから手がけるナノテックでは、DLC膜の構造制御や元素のドーピングを行うことでダイヤモンドからグラファイト、水素を含んだポリマーライクカーボンまで、各種用途に合わせた機能性を付与するICF(真性カーボン膜)を提唱、適用を進めているが、同社のようにDLCの分類を進めたり、また評価手法の確立を目指す標準化作業によって、DLCの使い勝手は向上し、適用用途は広がっていくであろう。
東日本大震災の後、総合科学技術会議ではグリーン・イノベーションとライフ・イノベーションの二大戦略に並んで、「復興・再生ならびに災害からの安全性の向上への対応」を成長戦略に加えた。ここにおいてもDLCの活躍の可能性は多々考えられよう。DLCのいち早い標準化作業によって、わが国の成長戦略推進の一助となることに期待したい。
第134回 「人とくるまのテクノロジー展2011」が示した自動車技術の威信
第134回 「人とくるまのテクノロジー展2011」が示した自動車技術の威信シボレー・ボルト 自動車技術会は5月18日~20日、横浜市西区のパシフィコ横浜で「2011年春季大会」を開催、「学術講演会」では90セッション・432件の講演発表が行われ、第20回目を迎えた自動車技術展・EV展「人とくるまのテクノロジー展2011」では、400社・860小間で製品・技術の展示が行われた。
今回は国際会議「EV TeC’11」の併催もあり、特別企画展示としては「車両電動化が拓く新しいくるま社会~くるまが変わる/人・社会が変わる」のテーマを掲げ、車両展示をはじめ要素技術・インフラ・将来像など、車両電動化による未来像が示された。
車両展示としてはGMの「シボレー・ボルト」に注目が集まった。ボルトは基本的には家庭用電源でバッテリーを充電してEVとして走るが、EVの航続距離の短さを補うためにエンジンで発電しながらモータを駆動する「レンジエクステンダー(航続距離延長装置)」を搭載した、「レンジエクステンダー付きEV」と称される。機械損失低減や常用域での効率向上を目的として1.4L直噴ターボ付きを使用、1,000~2,000rpmの効率の良い回転域に留めて発電するという。
要素技術ではたとえばNTNが、EV向け商品群として、(1)乗用車の2 輪だけに適用しても小型乗用車と同等の駆動性能を実現する「インホイールモータシステム」(2)駆動モータ、減速機、薄型ハブベアリング、インバータからなる小型モジュールをコミュータの小径ホイール内に格納、高度な車両制御が可能な「電動コミュータ用インホイールモータシステム」搭載試験車両(3)2 段変速機と駆動モータ、インバータをシステム化したEVパワートレイン「ワンモータEV 駆動システム」、(4)ばね下重量の増加がなく、左右輪の駆動力独立制御により駆動性能が向上する「オンボード駆動システム」、(5)転舵操作用のメインモータ、トー角調整用のサブモータを装備、メインモータ故障時には0.1 秒以内にサブモータに切り替わり、安全を確保するステアバイワイヤ操舵システム、(6)「遊星ローラねじ機構」を採用し、小型化と耐久性向上を達成した「電動ブレーキアクチュエータシステム」を展示した。
日本精工ではEVやハイブリッド(HEV)における駆動モータや発電機構の小型化による出力低下を補うため、現行18,000rpmの回転数を1.5倍となる30,000rpm以上に高めたモータおよび発電機構用玉軸受を展示した。軸受の潤滑油入口に油流を制御するプレートを設置したことで、超高速回転時の大きな遠心力が発生する環境下でも、潤滑が枯渇しやすい内輪側に潤滑油を確実に供給、摩擦による発熱を低減した。また、軸受内部の溝寸法や玉径などを最適化することで超高速回転下でも摩擦と発熱を抑制、焼付きを防止したほか、玉および内輪と保持器間のすき間を調整することで保持器の振動を抑制し、接触部の摩耗を低減している。
また、シムドライブ社の本年からの電気自動車先行開発車事業 第2号プロジェクトに参加している日本パーカライジングでは、EVに貢献する表面改質技術として、軽量化を目指した軽金属の表面硬化処理であるプラズマセラミックコート「PALNIP」や、小型化に寄与する薄膜化、航続距離延長の省エネ化につながる低フリクションの化成処理+固体潤滑「パルホス」、安全・環境への寄与として銅表面の径時安定化を図る電磁波シールド「導電ペースト」などを提案した。
こうしたEV向けの製品技術が多数出品される一方で、内燃機関のさらなる燃費向上に寄与する技術も展示された。
たとえば日本精工では、「冷間成形ハブユニット軸受」を出展した。ハブユニット軸受のハブシャフトを従来の熱間鍛造から冷間成形化する新工法により、軸受製造時の電気エネルギーと鋼材使用量を削減するとともに軸受を従来比5%軽量化、燃費向上を図る。ダイハツ工業2010年度技術開発賞を受賞したという。
パーカーグループブースでは、日本カニゼンが析出時の高硬度と高温環境下での高硬度を両立させ、ピストンなどの高温環境下での摺動特性を強化するNi-Co-W-P合金の無電解めっき皮膜「カニハステ」を、パーカー熱処理工業がリニア・イオン・ソースとUBMスパッタ、FCVAソースの適切な組み合わせで基材との密着性が高い多様なDLC膜を成膜できる「ハイブリッドDLCコーティング」を提示した。
そのほか、先のEV第2号プロジェクトに参加するポリプラスチックスでは内燃機関でもEVでも省エネに貢献する軽量化と剛性を両立するポリアセタール樹脂「ジュラコン」、PPS樹脂「フォートロン」などのエンジニアリングプラスチックス技術を展示した。EVでも重要視されるこのエンジニアリングプラスチックス材料ではデュポンやダイセル・エボニック、DSMエンジニアリングプラスチックス、ビクトレックス・ジャパンなど多数の出展があった。
東日本大震災の影響で開催が危ぶまれた本展だったが、「このような時期にこそ自動車メーカーをはじめ自動車関連企業が結束し、世界でトップレベルにある電動化技術をはじめとする自動車関連の最新技術を国内外に向けて発信し続けることが産業界の復興に向けて重要である」との開催決定理由のとおり、内燃機関の省燃費技術やHEV、EVの省エネ技術、安全技術など、わが国自動車技術の威信を示す展示会となったと思う。自動車産業の本格的な回復には今しばらく時間を要するが、本展で展示された多数の製品技術は次世代につながる研究開発の灯火が煌々と点っていることを示していた。
第135回 表面改質展2011に見る環境対応技術
第135回 表面改質展2011に見る環境対応技術 2020年代の早い時期に電力需要の2割を太陽光発電で賄うとする構想や、東日本大震災被災地の復興に際し太陽電池など新エネルギーを備えた住宅・施設の建設を推進しようとするエコタウン構想など、原子力発電に頼らないエネルギー政策が検討されてきている。こうした中、5月25日~27日に大阪で開催された「表面改質展2011」でも、環境への負荷が少ないドライコーティング(乾式の表面改質)によって省エネ・創エネに貢献する技術が紹介された。
トーカロでは風力発電機向け軸受などでの電食対策として、セラミック溶射技術を提案した。電食とは、軸受周辺から軸受内部に電流が通過し、転動体と軌道面の接触面にスパーク現象が発生、軸受の軌道面と転動面に生じる損傷。電食は、風力発電機向け軸受の故障原因の多くを占める。この損傷に対して、軸受外輪の外径部から側面に特殊セラミックスを溶射した「セラミックス絶縁軸受」では、絶縁性能を著しく向上、電食を防止し、風力発電機向け軸受のメンテナンスフリー化に貢献している。電食対策はまた、新幹線の発電機用軸受でも必要とされており、セラミックス溶射した絶縁軸受によって軸受メンテナンス周期の延長を実現している。
不二機販では、アート金属工業と共同で自動車エンジン用アルミニウム合金製のピストンスカート部にショットピーニング(微粒子衝突による加工)を施し、強度を高めつつフリクションを大幅に低減する技術を紹介した。ピストンスカートとシリンダライナの低フリクション化には、スカートの表面粗さを0.4Ra以下にすることができ耐久性のある表面処理を施すことが必要。表面処理としてはなじみ性の高い樹脂をコーティングするのだが、下地処理としてショットピーニングを施すことで、耐焼付き荷重を高めつつ、スカート面を細かい凹凸面とし樹脂コート後の表面粗さを細かくして、低フリクション化を図るという。
日本アイ・ティ・エフでは、硬度が50Gpa以上で耐熱温度が700℃以上という「水素フリーDLC」を紹介した。日産自動車のエンジン用バルブリフターで採用されたとおり、潤滑油を用いずに低い摩擦係数を示す水素フリーDLCだが、エンジン油中ではさらに摩擦係数を低下、省燃費に貢献するとした。
三菱電機では、IHIと共同で航空機エンジンの低圧タービンブレードの耐摩耗コーティング向けに、微細なパルス放電を利用した被膜形成技術「MSCoating」を紹介した。低圧タービンブレードでは従来、個々の先端が運転中に互いに接触して擦れ合うため、肉盛り溶接によって耐摩耗材料の被覆が行われているが、肉盛り溶接は前処理(予熱)や後処理(余肉の除去加工)が必要で、高い信頼性を得るためには溶接作業の高度な技術が必要と、生産性やコスト面で改善が求められていた。これに対しMSCoatingは、微小なパルス放電の繰り返しにより金属あるいは導電性のセラミックスの皮膜を被処理材の表面に形成する技術で、前処理が不要なほか専用装置による自動的な表面処理により高い生産性と皮膜の高信頼性を実現できる。こうした特徴を活かして三菱電機では、金型、機械部品などに適用することで、硬質被膜による耐久性の向上、ロングメンテナンス化が可能としている。
ダイヤモンドライクカーボン(DLC)の半導体特性を生かした太陽電池の開発が進められるなど、被膜の高機能化は日々進展してきている。表面改質展2011の展示を通して、創エネ・省エネに貢献する被膜の機能性向上への取組みの活発化している様子が感じられた。
第136回 食の安全を守る材料・表面改質・機械要素技術
第136回 食の安全を守る材料・表面改質・機械要素技術 日本食品機械工業会は6月7日~10日、東京・有明の東京ビッグサイトで「FOOMA JAPAN 2011(国際食品工業展)を開催した。
同展は、食品機械・装置および関連機器に関する技術・情報の交流と普及や、食品産業の一層の発展に寄与すべく、「食の安全・安心」に関わる食品機械の最先端テクノロジー、製品、サービスを通して、「食の技術が拓く、ゆたかな未来」を提案する目的で開催されるもの。今回は「つくります! 美味しい未来」をテーマに645社/2783小間の規模で、圧搾機や攪拌機、乾燥機、混合機などの原料処理装置から、製パン・菓子装置や食肉・水産物加工機、飲料製造装置など食品製造・加工装置・ライン、エンジニアリング・生産流通システム、鮮度管理・品質保持装置、包装・充填、保管・搬送、計測・分析・検査、衛生対策・管理、環境対策・リサイクル、設備機器・技術・部品などの最新技術・製品が出展された。
このうち設備機器・技術・部品としては、食品機械の耐久性など機械的特性や省エネ性能などを向上しつつ、衛生安全性を向上する製品技術が展示された。
潤滑剤関連では、偶発的に食品と接触することが許容される「NSF H1規格認証品であり、機械部品の寿命向上や効率改善に役立つ食品工場用潤滑油剤が展示された。エクソンモービルでは、コカコーラ社の採用担当者の談話のVTRなどを流しながら、同社ペットボトル飲料のキャップを閉めるスクリュー圧縮機に採用されているNSF H1登録の食品機械用高性能合成潤滑油「モービル SHC シーバス シリーズ」などを紹介した。耐摩耗性、長期間にわたる酸化安定性、錆止め性、腐食防止性に優れるほか、高性能基油と独自添加剤の配合により内部摩擦抵抗を低減し潤滑時の油温上昇を防ぎ省エネも実現するという。日清オイリオグループでは、植物由来の食用油脂と食品添加物だけという食品に使える素材だけを使うことでNSF H1、3H(焦げ付きを防ぐために使われる植物油など、直接食品に接触する目的で使用される離型油)の認証を取得した安全性の高い食品機械用潤滑油「エステローラF」を紹介した。食用油の持つエステル基により潤滑性を確保した上、酸化安定性を高め作動油としても長時間の稼動を実現しているという。藤本油化では100%合成油とスルフォン酸カルシウムベースの米Lubriplate製グリースを展示、製パン機などに適用できる滴点371℃以上という高温安定性のほか、耐摩耗性や極圧性など高い機械的特性を示した。
また、軸受関連では大同メタル工業が金属母材中に固体潤滑剤を微細で均一に分散させたことで無潤滑で-200の極低温から700℃の高温まで使用できる高性能無給油軸受「サーマロイ」を紹介した。水中のほか、オーブンなどの高温での摺動箇所にも適用できる。また、三旺は中国製の錆に強いステンレス製ベアリングなどを紹介した。
水のかかる環境下で使われることの多い食品機械では、このようにステンレス製の部品が多用される。たとえば攪拌機のシャフトやプロペラにはオーステナイト系ステンレスが使われるが、耐食性に優れ高靱性だが、耐摩耗性が低く、また表面に高い荷重や衝撃が加わった箇所ではソースやマヨネーズなど酸性物質による孔食が進みやすい。これに対しボディコート・ジャパンでは、オーステナイト系ステンレス鋼専用の表面硬化処理「コールスタライジング」によって耐摩耗性、表面硬度、耐食性を向上させるほか、高負荷で衝撃された際の素材の塑性変形に追従するよう弾力性も付与されるという。
食の安全への意識が高まる中、食品機械の機械的特性を高めつつ、衛生安全を確保する材料・表面改質・機械要素技術がますます求められてきている。
第137回 復興構想が決定、自然エネルギーの効率、省エネの推進を!
第137回 復興構想が決定、自然エネルギーの効率、省エネの推進を! 東日本大震災の本格復興の構想を議論する政府の「復興構想会議」は6月25日、首相官邸での会合で「復興への提言~悲惨のなかの希望」を決定、菅直人首相に提出した。復興財源確保のための所得税や法人税などの臨時増税の検討を求めたほか、災害時の被害を最小限に抑える「減災」の理念を重視し避難路整備などを重視するよう提起した。また、被災地を地形や被害状況に応じて5分類し住居や都市機能の高台移転などを勧めた。地域限定で規制緩和や税制優遇を認める「復興特区」を創設し、水産業などで活用するよう求めた。再生可能な自然エネルギーの導入促進も明記した。
再生可能な自然エネルギーの導入促進では、特に原子力発電所の事故被害のあった福島を風力発電や太陽光発電、小水力発電、木質バイオマスなど自然エネルギー導入の先がけの地、「スマートビレッジ」とすることとなった。スマートビレッジ
ここでは、効率の良い再生可能エネルギーや省エネルギー技術に関する革新的技術開発の取組みによる、抜本的な発電効率の向上やコスト低減が急務となり、機械効率を高めコストパフォーマンスを上げるメカ技術が重要となる。
6月22日~24日に開催された「第15回機械要素技術展」でもそうした再生可能エネルギーの効率を高める機械要素技術が多数展示された。精密制御用高剛性減速機の構造
たとえば太陽光発電ではナブテスコが、太陽の位置に合わせて電池の向きを変え、発電量を2~3割増やす太陽光追尾装置の開発を進めているが、たとえばこの装置での適用をイメージしてケーブルを減速機内部に通せて省スペース化が図れる中空機構を採用したうえ、アンギュラ玉軸受を組み込むことで外部荷重を支持し高剛性・モーメント容量大により旋回軸への使用が可能な精密制御用高剛性減速機などを出展した。風力発電のブレードと発電機を結合するゴムカップリング
また、三木プーリは風力発電のブレードと発電機を結合するゴムカップリングを展示した。風力発電機では増速機と発電機との間を連結して軸トルクを伝達するとともに、両軸のミスアライメントを吸収する軸カップリングが用いられているが、ゴムカップリングではゴムの弾性を、樹脂カップリングは樹脂の弾性を利用して、衝撃や振動を減衰・吸収する。高フレキシブル、低騒音、潤滑不要なため、高度80m以上という取り付け位置にあり保守が難しい風力発電機で高効率な動力伝達とロングメンテナンス化を実現している。
その他、同展では摩擦を低減し省エネルギーにつなげる表面改質技術やベアリング技術、潤滑技術などが出展された。
復興構想会議の提唱するスマートビレッジでは、風力発電、太陽光発電、バイオマスなど再生可能エネルギーシステムのほか、それらエネルギーの変動に合わせた需給バランスの調整を行うエネルギー・マネジメントシステムの構築も求められる。わが国の得意とする再生可能エネルギーによる「先駆けの地」が、上述のようなメカ技術に支えられつつ、復興の新しい形、わが国の活力を世界に向け示していくことに期待したい。
第138回 健康大国戦略を支えるの医療機器技術の普及・拡大を!
第138回 健康大国戦略を支えるの医療機器技術の普及・拡大を! 現在のわが国における医療機器の規模は、世界市場の10%程度にあたる約2億円。MRIや内視鏡など診断用機器が輸出され続ける一方で、人工心臓など人体に埋め込まれる治療系インプラント機器は、ほとんどが海外製品に頼っている。6月29日~30日に横浜市のパシフィコ横浜で開催された医療機器設計・製造展「MEDTEC Japan 2011」では、カテーテル治療に関する技術を中心とする治療系インプラント機器が広く紹介された。
カテーテル治療では、ふとももの付け根などに小さな穴をあけ、細い管状のカテーテルチューブを血管に通して、異常のある冠動脈入口まで到達させる。カテーテルの中にはさらに細い針金(ガイドワイヤー)が通っていて、この針金を使って細くなった血管を広げたり、詰まってしまっている血管を治療する。カテーテル手術は、小さな穴をあける程度の傷だけですむので、従来のバイパス手術に比べ回復が早く、患者への負担を軽くできる低侵襲治療として適用が広がってきている。
まず、血管を通すカテーテルチューブ自身に生体適合性があり滑りのよい材料を使う必要がある。シリコーンやポリイミドなどが用いられるが、東レ・ダウコーニングでは、さらにカテーテルチューブの外面に施すことで、冠動脈入口までカテーテルチューブを滑らかに送り込む高潤滑性シリコーン製コーティングをアピールした。このコーティングは、注射針を挿入しやすくしたり、シリンジを押し込みやすくする潤滑性向上にも用いられるという。
また、PTCA(経皮的冠動脈形成術)ガイドワイヤー製造トップシェアの朝日インテックでは、伸線技術で強度や線径をコントロールし、ワイヤーフォーミング技術でミクロンレベルの精度で成形したうえで、ワイヤーを患部に正確に送り込むための良好な回転追従性を付与する「トルク加工」を施す。さらにワイヤーの表面にPTFEコーティング(いわゆるテフロン加工)や親水性コーティングを施し、血管内でワイヤーを滑りやすくし、ワイヤーへの血栓を付きにくくしている。
一方、ステント治療(ステント留置療法)では、ニッケル‐チタン合金やステンレスなどの金属でできた網目状の筒「ステント」をバルーンにかぶせ、それをカテーテルの中に通っているガイドワイヤーで動脈の狭くなってしまった部分に通す。そこでバルーンをふくらませてステントを広げる。バルーンはすぼめて取り除くが、ステントは広がった状態で動脈の狭くなった部分に残すので、動脈を広げることができ、血流を正常に保つことができる。治療した部分がまた狭くなってしまう再狭窄を防止する治療法として注目されている。MEDTEC2011不二製作所ブース この血管内に留置されるステントの生体適合性を高めるため、カーボン材料、特にダイヤモンドライクカーボン(DLC)コーティングが採用されてきている。こうした用途に対し不二製作所では、DLCコーティングの下地処理として密着性を上げるブラスト処理を提案している。ステントの機能を長期にわたり発現させるDLCコーティングの耐久性を高めることで、ステントの機能不全に伴う再手術の危険性を低減し、患者の精神的・肉体的な負担を軽減する技術としても期待できよう。
昨年発表された新成長戦略では「ライフイノベーションによる健康大国戦略」として医療・介護・健康関連産業を成長牽引産業にすること、日本発の革新的な医療機器の研究開発促進を重点的に行うこと、アジアなど海外市場へ積極的な展開などを行うことを戦略分野とする基本方針が決定した。わが国の医療機器産業の活性化が期待される中で、ここで紹介したような材料・コーティング技術に支えられた医療機器が、安全で信頼性の高い低侵襲治療の場で活躍し、もって日本の医療機器の市場を拡大していくことを願う。
第139回 わが国有人宇宙開発のさらなる推進を
第139回 わが国有人宇宙開発のさらなる推進を 米国フロリダ州ケネディ宇宙センターから日本時間の7月9日に打ち上げられたスペースシャトル「アトランティス」が11日、地上400kmにある国際宇宙ステーション(ISS)にドッキングし、搭乗員4人がミッションを開始した。1981年の初飛行以来、有人宇宙開発を支えてきたスペースシャトルは今回が最終飛行となる。
有人宇宙開発では、高真空環境での実験などを通して得られた技術が真空を利用する半導体産業などに転用されてきた。しかし、その技術を多く利用しているわが国においては有人飛行を米国とロシアに委ねてきた。近年では若田光一宇宙飛行士がスペースシャトル「エンデバー」でISSに赴き、船外実験プラットフォームと船外パレットを取り付け日本実験棟「きぼう」を完成させた。現在ISSで医学実験のミッションを薦める古河聡宇宙飛行士はロシアの「ソユーズ」に搭乗した。「きぼう」の全体イメージ
若田さんが操作し船外実験プラットフォームの取付作業を行ったロボットアームは、「親アーム」とその先端に取り付けられる「子アーム」を動かすが、この潤滑には高真空などの宇宙環境から、地上で使われる一般的な潤滑油やグリースが使えない。そこで、たとえばロボットアーム関節に使われる、軽量・省スペースで1/160という大きな減速比を実現する宇宙用ハーモニック・ドライブ減速機では、低蒸発でトルク損失を軽減する宇宙用真空グリース・オイルが適用されている。これは、合成炭化水素油MAC(Multiply Allkylated Cycropentane)をベースにしたもので、特に高真空の半導体用途などに転用されている。
また一方で、宇宙機器に使われる材料は、-150~+200℃という温度サイクル、真空紫外線、10-3~10-5という高真空、原子状酸素、宇宙塵(スペースデブリ)といった過酷な宇宙環境にさらされることから、金属同士がくっついてモータや弁の軸が動かなくなるといったトラブルを引き起こすことがある。こうしたことから宇宙材料の耐環境性について、これまで、各種宇宙用材料を実際の宇宙空間で曝露して特性変化を観察する軌道上材料曝露試験が行われている。米国では1980年代から、わが国でも1990年代から材料曝露実験が実施されている。それらのデータが宇宙用材料の開発にフィードバックされてきているとはいえ、最近になってもISSの実用ソーラーパネルに使われるポリイミドの原子状酸素による破断事故などが報告され、さらなる材料の改善が求められている。しかし、スペースシャトルの今回の最終フライト以降は軌道上曝露材料回収のめどが立っていないという問題も指摘されている。スペースシャトルに代わるソユーズで回収可能な「小型の材料曝露パレット」の開発なども求められる。軌道上材料曝露試験を通じて、たとえば小型衛星「はやぶさ」の動力供給源である太陽電池パネルのヒンジ部軸受では、二硫化モリブデン(MoS2)焼成膜が適用されるなど、宇宙機器での固体潤滑の信頼性を実証し適用を拡大している。
近年、中国やロシアが独自で有人宇宙開発を進める中、「はやぶさ」で世界中から注目されるような独自の衛星技術を誇るわが国においても、米国やロシアに依存しない有人宇宙開発が必要となってきている。といっても、宇宙開発を一国のみで完遂することは難しい。ISSという参加国共有の研究開発ベースを最大限に活用できるように、わが国独自の有人飛行の推進を強く望むものである。
第140回 SURTECH 2011にみる環境対応表面改質技術
第140回 SURTECH 2011にみる環境対応表面改質技術 「SURTECH 2011表面技術総合展」が7月13日~15日、東京・有明の東京ビッグサイトで開催、電気めっきや無電解めっき、PVD(物理気相成長)やCVD(化学気相成長)などドライコーティングといった、各種表面改質の最新技術が広く紹介された。
環境保全・省エネと機能の両立を目指すめっき技術
環境負荷物質として6価クロムの使用が規制される中、6価クロムめっきに替わる表面改質技術が模索されている。その優れた耐食性と高硬度から6価クロムが多用されてきた航空機分野では、すでに高速フレーム溶射などの適用が始まっているが、めっき業界もただ手をこまねいているわけではない。
上村工業では、後処理なしで6価クロムを上回る耐食性と硬度を持つ、6価クロム類似の光沢白色系クロムめっき「ユープロ クロム CLH‐1」を出展した。航空機での適用をにらんでであろう、融雪塩への耐性も6価クロムめっきより高いという。また、6価クロムめっきに比べ耐食性は劣るものの、3価クロムめっきは、安全性、ミストの少量性、排水処理の容易さ、均一の電着性、不純物除去の容易さなどから、6価クロムめっきの代替技術としての最有力候補とも言われる。同社では、めっき浴管理法を改善し、均一電着性に優れる3価クロムめっき「ユープロ クロム CTA‐3」も紹介した。
また、電力不足を反映してか、めっき析出のエネルギーを低減させる提案もあった。
日本表面化学では、浴温度20~40℃でのめっきを可能にしたため、冷却設備を省きエネルギーコストを削減するほか、一定時間あたりのめっき析出量が従来品の約1.8倍にするなど生産性を向上させた亜鉛‐ニッケル合金めっき「JASCOストロンNiジンクZN-208」を出展した。
日本カニゼンでは、ELV、WEEE、RoHS規制に対応した、無電解Niめっき用の後処理剤を紹介した。めっき全面への吸着被膜を形成し、水切り性・シミ対策に特に有効なタイプⅠ、めっきピンホール部を中心にした不動態皮膜を形成し、錆防止効果に特に優れるタイプⅡ、めっき全面への不動態皮膜を形成し耐変色性や防錆性に優れるタイプⅢの三つのラインナップを示した。
機能性向上で適用が広がるドライコーティング技術
金型や工具、機械部品などに硬質被膜を成膜し耐久性を付与し長寿命化を図るPVD、CVD、プラズマCVD(PCVD)などドライコーティング技術も出展された。
ユケン工業ではPVDの一種であるイオンプレーティング法を用いたセラミック被膜コーティングを紹介した。樹脂成形金型に被覆することで、一般的な樹脂成型金型用処理である同社の無電解ニッケル-フッ素樹脂複合めっきに比べて、離型性が同等に良好で、硬度が5~6倍程度と高い耐摩耗性を実現するという。
また耐摩耗性つまり耐久性を高めつつ、低摩擦つまり省エネルギー・省燃費を両立する被膜として、パーカー熱処理工業では自動車エンジン部品や舶用エンジン部品などへのダイヤモンドライクカーボン(DLC)コーティングの適用を提案した。リニア・イオン・ソースとUBMスパッタ、FCVAソースの適切な組み合わせで適切な膜を成膜できる「Hybrid PVD System」では、摩擦摩耗特性に優れた多機能DLCコーティングの密着性を高め、コストパフォーマンスもよいという。
「使える表面改質新技術」を育てる
今回、展示会に合わせて講演会が開催、中でもドライコーティングをテーマとした講演が多数行われた。
その中で、「DLC膜の標準化」をテーマとした講演会は、自動車をはじめ適用が進むDLCへの関心の高まりからか、多くの関係者が参加し、ディスカッションを行った。標準化はDLC膜の分類基準を確立し、正しい被膜を選択しやすくすることで、DLCの適用を促す取組みである。
「表面改質、浸炭・窒化、高周波熱処理技術のロードマップ」と題する講演会で「表面改質とドライコーティング」をテーマに講演した東京都立産業技術研究センターの内田 聡氏は、「DLCは高機能性を付与するドライコーティング技術として早くから認識されながら、自動車分野で採用されてようやく注目されるといった具合で、適用がかなり遅れた。(DLCに限らず)使える技術は現場で積極的に使って、いかに使える技術を育てるかに心を砕くべきだ」と語った。氏は、小さい失敗を積み重ねることで、致命的な失敗を防ぐとも語った。そうした試行が繰り返される中で、技術の信頼性が向上していくということだろう。小ロット品からでも、新しい表面技術の適用を進めていこう。SURTECH 2011で展示された新技術が、早い時期に何らかの産業でトライされ、改善・育成されて、ゆくゆくは環境保全や機械の効率向上、ロングメンテナンス化など高機能化に役立っていくことに期待したい。
第141回~第150回
第141回~第150回第141回 モーション・エンジニアリング展が開催:新産業を支えるベアリング技術
第141回 モーション・エンジニアリング展が開催:新産業を支えるベアリング技術 「第20回モーション・エンジニアリング展」が7月20日~22日、東京・有明の東京ビッグサイトで開催、モーション・メカニズム、機械要素技術、アクチュエータシステムなど駆動・伝達・制御に関する製品技術が多数展示された。
NTNがメインテーマに掲げた「次の産業を支える技術」のとおり、同社をはじめベアリング各社で、新しい産業を支えるベアリング技術を紹介した。
NTN「回転センサー付き樹脂製すべり軸受」 「次の産業」としてNTNでは、インホイールモーターシステムをはじめ、電気自動車(EV)システム関連商品を前面に押し出した。そのうちEVモーター用ベアリングでは、バッテリー寿命延長のための「低トルク密封深溝玉軸受」を紹介した。グリースを掻き取り転走面への流入を防いで攪拌抵抗を低減する低トルク保持器や、低粘度で耐熱性に優れる基油と増ちょう剤の量を低減した低トルクグリースの採用で、回転トルクを従来比で50%低減した。またEVをはじめ高い制御性を必要とする軸受・システムでは、センサー付きとして稼働状況を確認しフィードバックをかけるほか、数十点という多数のベアリングが稼働する複写機など事務機器では不具合箇所を早期に特定できることを強調する。転がりからすべりに変えて軸受コストを抑えつつセンサー付き(写真は回転センサー付き樹脂製すべり軸受)とすることも推奨していた。
ジェイテクト「セラミック玉絶縁軸受」 ジェイテクトでは「グリーンテクノロジー」をテーマに、たとえば風力発電機用ベアリングを展示した。ジェネレータ(発電機)用「絶縁セラミック軸受」は、転動体にセラミックス(窒化ケイ素)を使用することで電食(回転中の軸受内部に電流が通過して転がり接触部の表面が局部的に溶融する現象)を防止するとともに、軸受内部の発熱を抑制し、軸受に封入されたグリースの長寿命化を実現する。同社では「発電機や増速機が収納されるナセルが高度80m以上という高所にあり、メンテナンスの難しい状況でロングメンテナンス化を図るときに、セラミック溶射被膜を施した軸受では被膜が減摩することで絶縁機能が失われる。絶縁機能が失われることのないセラミックボールの信頼性をアピールして、採用拡大につなげたい」としている。
日本精工「E-DFO処理」
日本精工では省スペース、低騒音、低発塵、洗える!防水など過酷な環境下で活躍するベアリングと精機製品を展示した。そのうち、半導体やフラットパネルディスプレイ(FPD)などますます微細化の進む分野での要求が厳しい低発塵化に対応するベアリングとして、宇宙機器で使われているMAC(シクロペンタン)油をベースにした、超低蒸気圧の炭化水素系オイルとフレーク状PTFEパウダーである吸着物質からなる薄膜潤滑技術「E-DFO」を施したベアリングを展示した。潤滑皮膜の保持性を向上することによりV-DFO潤滑皮膜(従来の固体潤滑皮膜に比べ10倍以上の長寿命化、フッ素系グリースと比較して1/10の低発塵・低アウトガスを実現した、フッ素油焼付け膜)と比較しても、さらに数倍以上の耐久性を有するとともに、真空環境の汚染も半分以下に抑えることができる。たとえば半導体・FPD製造プロセスや太陽電池製造プロセスで活躍する各種真空成膜装置のベアリングとして、高い潤滑性を実現しつつ、超クリーン環境を保つという。
23日に明らかになった東日本大震災からの「復興基本方針」の原案では、太陽光発電や風力発電などの導入促進などのエネルギー政策が打ち出されている。「産業の米」といわれるベアリングは、グリーンエネルギーなどそうした新しい産業においても、センサー付きとして知能化を図るなど進化を遂げながら、今後も重要な機械要素として位置づけられていくだろう。
第142回 中国高速鉄道に求められる二重三重の安全設計
第142回 中国高速鉄道に求められる二重三重の安全設計 中国東部の浙江省温州市付近で7月23日、高速鉄道「和諧号D3115」が後続の高速鉄道車両「和諧号D301」に追突され脱線事故を起こし、車両4両が地上20~30mの高架橋から転落した。D3115はカナダ・ボンバルディア製Regina C2008型をベースにしたCRH1型、D301は日本・川崎重工製E2系1000番台(東北新幹線はやて)をベースにしたCRH2型とされる。
技術供与した両社とも「車体と事故は関係ない」との声明を出しているように、中国が自主開発した列車運行センターのデータ収集装置のプログラムソフト設計に欠陥があったと中国鉄道省の責任者が発表した。温州南駅の信号設備が落雷で故障した影響で、D3115は搭載している列車制御装置が不安定になったためいったん停車、その後規定に従い徐行運転をしていたところ、後続のD301には走行可能の信号が伝わっていたため通常速度の時速百数十km~200km前後と減速することなく走行し、D3115に追突したという。
当初、落雷による信号機故障のみが報じられたが、関係者が口を揃えて言うとおり、最高時速250kmという高速車両は、(誤っていたという)信号を目視してから減速・停止できるものではなく、わが国の新幹線が1964年の東海道新幹線開業以来採用している「ATC(自動列車制御装置)」により、先行列車との間隔や進路の条件を見て自動的にブレーキがかけられることで車両同士の接触事故が防止されている。台湾新幹線にも採用されている最新のATCシステムでは、地上から各列車に前方列車の位置や速度制限などの情報を伝送、各列車では車上に記憶されているブレーキ性能など車両性能データや路線データから、最適なブレーキパターンを作成し、そのブレーキパターンと自分の列車の走行速度を照査し、最適なブレーキをかける。
また車両や線路・電機設備などに異常を発見したときなどに列車を緊急に停止させて安全を確保する「列車防護システム(ATP)」もある。世界の高速車両の常識であり、中国でも構築されているはずと信じられてきた。原因は明らかにされていないが、今回の事故ではこのシステムが働かなかったのは明白だ。
地震の多いわが国では、「地震警報システム」も包括した列車防護システムを構築している。地震警報システムは、地震の初期波であるP波を新幹線沿線の地震計または周辺検知点で計測、P波を基にして地震の震源と規模を推定。その規模が一定以上の値を示した場合、新幹線への送電を止め、主要動であるS波が来る前に非常ブレーキがかかる仕組みとなっている。これにより先の東日本大震災のときにも本震の数秒前に地震警報システムがP波を検知してATCが作動、脱線することももちろん死傷者を出すこともなく東北新幹線は一斉に停車した。
わが国の新幹線が約半世紀にわたって高速走行での安全神話を確立している背景には、防護する列車の運行管理システムだけでなく、ATCを確実に履行する車両や線路などの二重三重の機械的な技術開発とその保守管理も貢献している。
たとえば、車両。電気指令式空気ブレーキ(今回の事故車両でも採用)では、電気ブレーキを優先的にかけて負担しきれない分を空気ブレーキで賄い機械ブレーキの摩耗を減らす制御や、高速域で車輪・レール間の粘着力(車輪からレールに伝達される力)が低下することから、速度に対するブレーキ力のパターンを定め、速度に応じてブレーキ力を変化させる制御などがある。
こうした制御を全うするには、車輪とレールの接触状態を安定させる軌道状態の管理も重要になる。電気軌道総合試験車(ドクターイエロー)などによりレールの傷や摩耗量を走行しながら超音波探傷し、保守計画を策定し保守作業を実施することで、軌道状態がどの区間においても良好な状態で均一になるよう、管理がなされている。
中国の高速鉄道は2007年の「第6次鉄道高速化」により営業運転を開始したばかりだが、昨年末には総延長約8,000kmに達し、さらに2015年までに1万6,000kmに拡大する計画で、急ピッチの建設・路線拡大に安全管理が追い付くのか疑問視されていた。今回はソフト面の不備による事故と見られるものの、こうした急拡大にあってハード面での保守管理がおろそかにされていることも懸念され、車両や線路などに起因する事故が引き起こされる可能性も否定できないだろう。
「中国独自のシステム」と謳い高速車両の輸出を進めるのは結構だが、鉄道という大量輸送機関で優先させるべきは、何より安全である。行きすぎた高速志向を今一度見直し、高速走行での安全確保でソフト・ハード面ともに多くの実績・経験を持つ欧州やわが国などに再度学び安全確保に努める、真摯な姿勢が求められている。
第143回 2011国際洗浄産業展がまもなく開催、製品表面の機能性を高める洗浄技術
第143回 2011国際洗浄産業展がまもなく開催、製品表面の機能性を高める洗浄技術 日本産業洗浄協議会( http://www.jicc.org/ )などは8月31日~9月2日、東京・有明の東京ビッグサイトで「2011地球環境保護 国際洗浄産業展」を開催する。
産業洗浄は、各種機械部品の品質を保つのに不可欠なプロセス技術で、製品や部品の機能性や性能の向上、製品の外観の向上、品質や信頼性の向上、製品の次工程への橋渡しなどを目的に行われる。ハードディスクドライブや半導体などの微細機構においてはナノ・マイクロコンタミネーションを除去しクリーン環境を保持することで、長期間にわたり高性能化を実現する。
産業洗浄の対象として大きな部分を占める金属部品の洗浄では、加工油剤など油脂類の除去を目的とする洗浄が最も多く実施されている。これは多くの工業製品が切削加工や塑性加工によって生産され、そこで使われた加工油剤や固体潤滑剤・化成膜に加えて、切削くずなどが製品表面に付着しているためだ。工業製品の多くはそうした加工後に熱処理やコーティングなどの各種表面改質が施されるが、いかに高精度な表面改質でも汚れの付着した表面に施したのでは、不具合が生じる。表面改質による機能性の良否は、前処理としての洗浄技術にかかってくるわけだ。
ここで、汚れを加工油剤に絞っても水溶性加工液に適した水系洗浄剤(アルカリ・中性・酸性)、鉱油系加工油に適した炭化水素系洗浄剤や塩素系洗浄剤などがあり、水系洗浄剤では排水処理が必要、炭化水素系洗浄剤では引火点があるため防爆対応が必要、塩素系洗浄剤では環境への配慮や人体への影響などから洗浄装置の密閉化構造が必要など、汚れの種類や持ち込み量、それに伴い選定した洗浄剤などによって適切な洗浄装置・システムを選ばなくてはならない。たとえば複雑形状の部品を大量にバッチ処理で洗浄するには、強力なキャビテーションや振動を発生させ超音波洗浄が適しているといえよう。
2011国際洗浄産業展では、最新の洗浄剤や洗浄機・システムから、溶剤や廃液などの回収装置、水処理や油水分離などの周辺機器などが多数出展されるほか、環境にやさしい適切な化学物質を選定し揮発性有機化合物(VOC)の排出抑制を支援するため、日本産業洗浄協議会で長年構築してきた「経済的に実行可能な最良利用可能技術(EVABAT)」なども紹介される予定だ。ぜひ会場に足を運んで、最新の洗浄関連製品・技術に触れるとともに、各種洗浄技術のエキスパートと意見交換していただき、適切な洗浄処理という適切な前処理によって、表面改質の機能を最適化し、表面の機能性を向上させ、ひいては各種工業製品の付加価値向上につなげていただきたい。
第144回 分析展・科学機器展が開催、材料・表面改質技術の発展を支える計測・評価技術
第144回 分析展・科学機器展が開催、材料・表面改質技術の発展を支える計測・評価技術日本分析機器工業会と日本科学機器団体連合会は9月7日~9日、千葉・幕張の幕張メッセで、「来て・見て・わかる 確かな技術」をテーマに、「分析展2011 / 科学機器展2011」の合同展示会を開催した。分析、科学機器分野でアジア最大の展示会として、出展規模500社1,500小間での開催となった。同合同展は、“研究、開発、分析の入口から出口まで”の最新機器の情報を発信する展示会として2010年に第1回を開催、本年が2回目となる。
試験・計測・分析機器は、先端の材料や表面改質技術の開発を支える基盤技術であるが、今回は特に、震災からの復興で期待される自然エネルギーなど、グリーン・イノベーションに貢献する評価機器・技術が多数出展された。
近年、材料自身にない耐久性や潤滑性などの機械的特性を表層に付与する表面改質技術が長寿命化やオイルフリーなど、環境保全の観点からも注目されてきている。今回はこうした表面改質薄膜を評価する機器が多数展示されたので、その一端を紹介したい。日本電子「SEMの検出器」
たとえば、細く絞った電子ビームを材料表面に入射して表層の数nm深さから出る二次電子を検出器でとらえて薄膜を画像化する走査型電子顕微鏡(SEM)がある。高分解能、高倍率で観察できることから、表面観察手法として多用されている。日本電子では、スーパーハイブリッド対物レンズにより、0.8nm (15kV)、1.2nm (1kV) の高い分解能が得られるサーマル電界放出形走査電子顕微鏡「JSM-7800F」を出展した。大電流を使うことで、分析精度や元素マップの品質を落とさずに、短時間で分析ができるほか、Gentle Beam 搭載の高性能電子光学系が、試料表面の微細構造を映し出す。非導電性試料でも金属のコーティングを施すことなしに像観察・分析できる。
また試料に電子ビームを照射し、透過してきた電子を結像し、薄膜の界面組織などを高分解能で観察できる装置として透過型電子顕微鏡(TEM)がある。日本エフイー・アイでは、走査型TEM(STEM)「Titan G2 60-300」を出展した。TEMでは電子線が透過するように試料を薄膜に加工する必要があるが、加速電圧を60~300kVの広範囲で設定できるため、SEM- FIB(集束イオンビーム)などで作成された薄膜試料に最適な加速電圧条件で二次元や三次元での材料組織の評価や組成分析、状態分析が行える。STEMモードでは70pmの超高分解能を達成、これによりカーボンナノチューブの内部構造の観察が可能となっている。リガク「SmartLab」
このTEMのような微細加工が不要な装置として、X線の照射エリアが10~20㎜角と広く、TEMやSEMのように微小領域に限らず、広い領域での解析が可能なX線回折装置(XRD)がある。リガクでは、全自動水平型多目的X線回折装置「SmatrLab」を出展した。独自の光学系の使用により微小角入射することで、nm~μmレベルの薄膜の相組成や結晶構造のほか、多層膜の中間層や下地薄膜なども解析できるほか、表面均一性なども測定できる。オプションの搭載で、薄膜中のナノ粒子の形状や粒径分布なども分析できる。
これら表面観察機器の一方で試験評価機器も展示された。たとえば、押込み荷重をμNオーダーで制御し圧子の押込み深さをnmの精度で測定、従来の硬さ試験機では不可能だった薄膜や極表面層の硬度測定を行う試験機として、極小押込み試験機(ナノインデンター)がある。東陽テクニカでは、独自のCSM法により深さ方向に硬度、ヤング率を連続で取り込むことのできるアジレント・テクノロジーズ社製ナノインデンター「G200システム」を展示した。超低荷重硬度・ヤング率が計測できる摩耗試験のほか、硬度・ヤング率深さプロファイルが得られる破壊靭性試験、ナノスクラッチによる疲労試験が1台で行えるという。東陽テクニカ「G200システム」
もちろん上述のような表面改質技術に限らず、材料技術自体でも、たとえば自動車の燃費向上、つまりCO2排出削減につながる軽量化が進められ、金属製部品から軽量化に有利な樹脂製部品へと置き換えが進んできている。すでに金属代替の自動車部品としてはポリアセタール樹脂やPPS樹脂、液晶ポリマーなどのエンジニアリングプラスチックが採用されているが、自動車部品としての長期的な耐摩耗性や剛性など機械的特性を評価し安全性を保障するため、硬さ試験や引っ張り試験、摩擦摩耗試験などが不可欠となっている。ハイブリッド車に続いて、電気自動車など新しいシステムが登場する中、高温への耐性など材料に求められる特性も変化している。グリーンエネルギーに関わるシステムなど、未知の使用領域での材料や表面改質層の性能を試験・評価し、信頼性を高め、適用を促進するうえで、試験・計測・分析機器の活躍の場はますます広がってきている。
第145回 フランクフルト自動車ショー 欧州燃費規制で進むEV化、軽量化
第145回 フランクフルト自動車ショー 欧州燃費規制で進むEV化、軽量化 ドイツ・フランクフルト国際自動車ショーが9月13日~25日に開催されている。32の国・地域から1,012社が出展した。自動車メーカーの世界初披露(ワールドプレミア)89件のうち、45件が独メーカーによるもの。特に欧州ではCO2排出規制が2012年から強まることから、電気自動車(EV)やHEVの出展が目立った。欧州では従来、長距離をレスポンスよく低燃費に走るディーゼルエンジンの割合が高いが、燃費規制に対応して長距離ドライブにはHEV、短距離走行用の街乗り(シティ・コミューター)としてはEVが有効と見られている。しかし、EVの市場を拡大する上では走行距離の延長が不可欠だ。ここではEVの展示について、走行距離延長の試みを交えて、トピックス的に紹介する。
独フォルクスワーゲン社では全長3.54mの車体に、排気量1Lのアイドリングストップ機構付き直列3気筒エンジン(出力は44kW/55kWのガソリンエンジンまたは出力50kWの天然ガスエンジン)を搭載した小型車「up!」を発表したが、2013年に発売する予定の電気自動車仕様「e-up!」も展示した。upの欧州混合モード燃費は、44kW仕様が23.8km/L、55kW仕様が23.3km/L、天然ガス仕様車の燃費が31.3km/kg。これに対しe-up!は、フロントアクスルに置かれたトランスミッションとデファレンシャルを一体設計した最高出力60kW(連続出力40kW)のモーターを回して、0~100km/hで加速11.3秒、最高速135km/h、最大走行距離130kmという走行性能を発揮する。高張力鋼板(ハイテン)を使って車体重量を1t程度と軽量化し走行距離延長を図るほか、ルーフにはソーラーパネルを装備し、床下にレイアウトされた蓄電容量18KWhのリチウムイオンバッテリーの充電を補完する。
独ダイムラー社は、独BASF社と共同開発したEVコンセプト・モデル「smart forvision」を出品した。ルーフにBASF社製有機太陽電池を搭載、発電で得られた電力は、車内換気用ファンの駆動に利用される。また、室内側には車内を面で明るくできる有機ELを使った照明を採用、消費電力の低減を図った。これらの手法によってリチウムイオンバッテリーに蓄えた電力の使用を低減し、走行距離の延長につなげている。
EVの課題である航続距離の延長では、何といってもモーターの負荷を軽減する軽量化が有効だ。独BMW社は車体の約3割に炭素繊維強化プラスチック(CFRP)を採用し約100kgの軽量化を実現した2013年発売予定の「i3」を披露した。i3はモーター、バッテリー、サスペンションなどを収めたアルミ製の「ドライブ・モジュール」の上に、CFRP製の乗員室「ライフ・モジュール」を載せた構造。CFRPは米ボーイング社「787」や仏エアバス社「A380」で採用され航空機の航続距離延長と燃費低減に貢献しているが、ここでは軽量・高剛性なCFRPの採用により、全長3.85mながら車重1,250kg、走行距離130~160km、バッテリー充電時間6時間を実現しつつ、ドライバビリティ向上と衝突安全性を確保している。BMWグループとSGLの合弁会社SGLオートモーティブ・カーボン・ファイバーでCFRPの生産工場を開設しているが、部品製作にあたっては加工の難しいCFRPの易加工性と低コスト化が求められている。
EVでは、モーターの高出力化のためモーター本体の電気設計やモーターの制御・電気システムの改良や、出力向上に伴う発熱量増加に対応するための冷却性能の向上だけでなく、部品の耐熱性が重要となる。特に軽量化から採用が進む樹脂部品では耐熱性を補うコンパウンド技術などが適用されているが、上述のCFRPの加工性の悪さをも解決する手法として、CFRPに熱可塑性樹脂をあらかじめ含浸させ射出成型による量産性を持たせた熱可塑性カーボンプリプレグが登場している。ポリエーテルエーテルケトン(PEEK)樹脂など耐熱性が極めて高く機械的特性に優れる熱可塑性樹脂をマトリックスとしたカーボンプリプレグを使うことで、軽量化だけでなく耐熱性や摩擦摩耗特性を高めるなど部品の付加価値を高めることになる。
EVの搭載バッテリーあたりの走行距離延長では、軽量化のためのユニットのコンパクト化などから、ますますモーター周辺の高温化が進むと見られる。EVの市場拡大においては、上述のような軽量化につながり高温への体制に優れる材料技術や表面改質技術などの開発促進が待たれている。
第146回 太陽光発電の効率向上・コスト改善に貢献する薄膜技術
第146回 太陽光発電の効率向上・コスト改善に貢献する薄膜技術 先ごろ、「電気事業者による再生可能エネルギー電気の調達に関する特別措置法」が成立し、全量固定価格買い取り制度が来年7月に導入される見通しとなった。再生可能エネルギーで発電した電力を、電力会社に一定期間買い取らせる全量固定価格買い取り制度が対象とするのは、太陽光、風力、水力、地熱、バイオマス(生物資源)の5つ。このうち原子力など既存エネルギーを代替できる再生可能エネルギーとして、太陽光発電の市場が拡大してきている。太陽光発電協会(JPEA)がまとめた、国内企業29社が2010年度(2010年4月~2011年3月)に出荷した太陽電池セルと同モジュールについての統計では、2011年度の総出荷量は対前年度比で152.2%の253万8814kWに成長した。10年度に出荷した太陽電池セルと同モジュールについての統計(太陽光発電協会)
しかし、太陽光発電の発電コストは2011年現在で42円/kWh以下を想定しているが、最も変換効率が高い単結晶シリコン(Si)の太陽電池で最高変換効率は25%程度。太陽光発電が現在の原子力発電を代替するには3倍、火力発電を代替するには6倍の変換効率が必要とされ、再生可能エネルギーとして太陽光発電の普及・利用が進むには、太陽電池の変換効率のさらなる向上が課題とされている。
市場に流通している太陽電池としては、単結晶Si太陽電池および多結晶Si太陽電池の「結晶シリコン太陽電池」、Si系薄膜太陽電池およびCu(InGa)Se2系薄膜太陽電池(CIGS薄膜太陽電池)、さらにはCdTe太陽電池の「薄膜太陽電池」などがある。
結晶シリコン太陽電池の薄型化とパッシベーション膜技術
1GWのSi太陽電池を製造するには約1万tのSi原料が必要とされ、Si基板の厚さは従来300~400μmだったが、世界的な材料供給不安や製造コストの削減などから薄肉化が進み、現在200μm、さらには100μmの厚の製品も登場してきている。しかし、結晶シリコン太陽電池では基板の薄型化とともに裏面再結合速度が大きくなり、熱変換効率が著しく低下する。このため基板の薄型化と高効率化の両立には、太陽電池裏面をパッシベーションし裏面再結合を抑制することが重要になる。高品質なパッシベーション膜としては熱酸化膜(SiO2)が知られているが、低コスト基板の使用、プロセスコストの低減、スループットの向上などのために、低温プロセスによるパッシベーション膜の開発が望まれている。プラズマCVD はパッシベーション膜の低温堆積技術として有望であり、プラズマCVD によるシリコンナイトライド(a-Si1-xNx:H)膜、アモルファスシリコン(a-Si:H)膜、アモルファスアルミニウムオキサイド(a-Al1-xOx:H)膜などが次世代パッシベーション膜として期待されている。
薄膜太陽電池とロール・トゥ・ロール成膜技術
シリコンの膜をガラス基板などに蒸着させて製造される太陽電池で、シリコン使用量は結晶型に比べ1/100程度となるため、低コストで生産できる。変換効率はアモルファスSiで17.3%を、CIGSで20.3%を記録している。
太陽電池は、モジュール表面の温度が上がると出力が下がるという性質があるが、薄膜シリコン型は高温環境下でも出力が落ちにくく、温暖な地域を中心にメガソーラー用途としても注目される。特にアモルファスSiでは高分子などのフィルム基板とすることができるため、ロール状に巻き取ることができ、たとえばTDKなどの工場では大面積の連続生産を可能とするロール・トゥ・ロールでの量産が実現されている。
さて、アモルファスSi太陽電池では、スパッタリング法と呼ばれる真空蒸着法によって、基板に電極となる金属(アルミニウム)の薄膜を形成し、これをプラズマCVD法のチャンバー(反応室)に送り込む。CVD法とはヒータで加熱した基板表面で原料ガスを熱分解し、化学反応によって薄膜を形成させる化学蒸着法である。高周波のグロー放電中で熱分解させると、比較的低温(約200℃)でも優れた膜質が実現する。このプラズマCVD法によりn型・i型・p型という3層のアモルファスSi半導体の薄膜を形成したのち、再びスパッタリング法によって透明電極の薄膜を形成する。
この透明電極の形成に対し、神戸製鋼では、各種カソード(DC、UBM、DMS、ロータリーマグネトロン)を用い、高分子フィルム基板ウェブにロール・トゥ・ロール方式でITO, ZnOなどの透明導電膜(TCO)などを形成するスパッタロールコータを提供している。
太陽電池では屋外で20年以上使用されるため、水蒸気透過率を10-3 g/m2/day以下に保持しなくてはならない。しかし、高分子フィルム基板はガラス基板に比べガス透過性が大きい。これに対し神戸製鋼ではまた、 2本のローラー間で発生する放電によるプラズマCVD法によって、高分子フィルム基板ウェブにロール・トウ・ロール方式でバリア膜(シリカ膜)を形成するPE-CVDロールコータを提供している。バリア膜の成膜により、高分子フィルム基板のアモルファスSiで水蒸気透過率WVTR 10-2~10-5g/m2/dayというガスバリア性を実現している。
このほか導電性ポリマーやフラーレンなど、有機半導体を用いる太陽電池で、軽量・柔軟性に富み印刷技術を利用でき安価といった特徴から有機薄膜型太陽電池が注目、変換効率10%を実現した三菱化学が実用化に目途をつけている。有機薄膜太陽電池では、p型有機半導体に、「テトラベンゾポルフィリン」と呼ばれる有機物を、n型有機半導体に、炭素原子60個からなるフラーレンに有機分子を取り付けた「フラーレン誘導体」を用いている。ここでも素材自体の低コスト化だけでなく、ロール・トゥ・ロール生産による生産コストの低減が期待されているが、ロール・トゥ・ロールで数百nm(1nmは10億分の1m)の均一な膜を塗布する技術の確立が求められている。
従来の工法でアモルファスSi太陽電池を生産する場合、工程ごとに搬送の手間がかかり装置規模が大きくなる、工程ごとにスタッフを要するなどの課題があったが、ロール・トゥ・ロールではロールからロールへの受け渡しによる連続工程で手間がいらず、製造コストが大幅に削減できる。再生可能エネルギーとして太陽光発が確固たる地位を占めるには、こうした量産手法と同時に機能性を高める薄膜技術の確立による、太陽電池の変換効率の向上、コストの改善がますます求められている。
第147回 EVEXが開催、EVに見るクルマの新しいカタチ
第147回 EVEXが開催、EVに見るクルマの新しいカタチ 電気自動車(EV)や関連製品の総合展示会「電気自動車開発技術展(EVEX)」が10月12日~14日、横浜市のパシフィコ横浜で開催された。展示会実行委員長の大聖泰弘・早稲田大学教授が基調講演で「1970年代、1990年代に続いて3度目のEVブームが到来している」と述べたとおり、自動車メーカー、二輪車メーカー、自動車部品メーカー、充電器メーカー、コンバートEV(内燃機関自動車のエンジンをモータにし、バッテリーを搭載して改造したEV)メーカー、大学の研究室などが、EVの市場拡大に向けて様々な提案を行った。
慶応大学・清水浩教授が社長を務めるEVベンチャーのシムドライブは、先行開発事業第1号車の「SIM-LEI」を出展した。EV普及の上で最も大きな課題とされている航続距離を、JC08モード(日本における標準的な市街地走行モード)で333kmと延長した。この性能の実現にはインホイールモータ、コンポーネントビルトイン式フレームに加え、オール鋼鉄製モノコックボディーによる車体の軽量化、高パワー密度電池の利用による回生エネルギーの高効率回収、超低転がり抵抗タイヤの採用、超低空気抵抗ボディーによる空気抵抗低減の効果が大きな役割を果たしたとしている。先行開発事業第2号では日本パーカライジングなどが参加し、各種表面処理技術による低フリクション化などが進められる予定だ。
NTN「電動コミュータ用インホイールモータシステム」 最終日の14日には佐賀市が公用車として電気自動車「日産リーフ」4台を導入したが、環境都市をアピールする自治体によるEVの導入が進んでいる。静岡県磐田市もコンバートEVを公用車として採用し、公道走行における性能、安全技術、品質などのデータを収集・分析することで、次世代EVとしての実証実験を行う予定だが、このコンバートEVにはNTNの「インホイールモータシステム」が搭載される。インホイールモータ方式は、モータや減速機を直接ホイールに取り付ける方式で、次世代EVの駆動方式として注目されている。内燃機関自動車と比べると、エンジンやトランスミッション、駆動軸などが不要になり、自動車の組立や保守工数が削減されるほか、空いたスペースが有効活用できるため、車体デザインの自由度が大幅に高まる。今回、NTNでは「電動コミュータ用インホイールモータシステム」を出品した。これは、薄型のハブベアリングを採用したホイール内に収納できる小型インホイールモータモジュールで、駆動モータ、減速機、ハブベアリング、制御システム(インバータを含む)といった電動コミュータの駆動系を一体的にシステム化し、左右輪の駆動力を独立制御する。
今回は「クリーン発電&スマートグリッドフェア」が同時開催されたが、情報通信技術で地域の電力需給を調整するスマートグリッド(次世代送電網)に将来、EVが組み込まれることを見据え、蓄電池としてのEVの適用も多数提案された。折しも国土交通省が、大容量の蓄電池が搭載されたEVを駐車中に活用し、住宅やオフィスビルなどとEVとで電力を融通し合うシステムの開発を支援することを決めた。電力需要が大きな昼間帯などはEVの蓄電池の電力を住宅やオフィスで利用する一方、電力会社の供給に余力があり料金が安い深夜の電力はEVに充電し、日中でも建物の屋根にある太陽光パネルで発電した電力の余剰分は充電に回す。東日本大震災後の電力不足で注目されたEVのリチウムイオン電池は最大24kWhで、一般家庭であれば約2日分の使用電力を貯蔵することが可能という。
こうしたなか日産自動車では、JX日鉱日石エネルギーと共同で、日産リーフと燃料電池「エネファーム」を使ってクルマと家のトータルでのエネルギーの低炭素化を目指す実証実験を2012年に開始することを発表した。JXエネルギーが住宅向けエネルギー機器等の実証試験を行っている「ENEOS創エネハウス」(横浜市)で、家庭の消費電力が少ない時間帯にはエネファームで発電した電力で日産リーフの充電を行い、家庭での消費電力をエネファームでは賄えない時間帯には、日産リーフから家庭へ電力供給を行うことでエネファームの稼働率向上を検証するという。
EVの航続距離延長や走行の信頼性向上、蓄電池の住宅などへの電力供給源としての利用には、耐久性などの課題も残っており、国交省では2012年度予算の概算要求に1億2000万円を盛り込み、自動車や住宅メーカーなど異業種で構成する企業連合に研究開発費を補助する方針を打ち出している。スマートグリッドを構築する主要コンポーネントなど新しいクルマの形を示すEVには、蓄電池自体の技術の改善が引き続き求められるとともに、エネルギー消費を抑えるモータ軸受や表面改質などの低フリクション化技術や、軽量化技術、モータ周辺の熱対策など機構部品の性能向上も求められている。
第148回 石炭火力発電の省エネ・高効率化を図る材料・表面改質技術
第148回 石炭火力発電の省エネ・高効率化を図る材料・表面改質技術磯子火力発電所 東日本大震災を機に、わが国で稼働する発電システムの内訳が変わってきている。以前は33%を占めていた原子力発電が14%に減少する一方で、62%を占めていた火力発電が77%に増えている。中でも、石油などに比べ埋蔵量が豊富で産出国に偏りがない石炭による火力発電が、あらためて注目されている。実は世界の発電電力量の4割以上が石炭火力によるもので、燃料別では最大。特に電力需要の増加が著しい中国では約8割、インドでは約7割、米国でも約半分は石炭火力だという。
石炭火力発電の仕組み 世界トップの熱効率43%を誇るJパワー・磯子発電所の超臨界圧微粉炭火力でみると、石炭が貯炭設備から微粉炭機(粉砕機ミル)に送られ、燃焼効率を上げるよう数十μmのパウダー状の石炭(微粉炭)にされる。この微粉炭をボイラ内に送って燃やし蒸気を発生させ、その膨張力で蒸気タービンを回し発電するわけである。
石炭を乾燥させながら微粉砕する竪型ローラミルでは、ローラタイヤでテーブルセグメント(鉢形の皿)を一定圧力で押さえながら、テーブルを回転させることにより、ローラタイヤとテーブルの間に入った石炭を微粉炭に粉砕する。このためローラタイヤおよびテーブルライナの摩耗対策として、硬化肉盛溶接が行われている。石炭粉砕機の構造
このとき、テーブルは1000rpmから20rpmに減速されて回転しているが、減速機は粉砕時の振動を受けながら減速することで摩耗が進みやすいため、減速機油にはポリアルファオレフィン(PAO)といった合成潤滑油が使われている。また、減速機の大きなスラスト荷重を支えるスラスト軸受には、球面ころ・円筒ころのほか、他モーメント荷重も受けるためのティルテングパッドタイプすべり軸受などが採用されている。
さて、超臨界圧微粉炭火力発電では、ボイラーから蒸気タービンへと送られる水蒸気を、水の臨界圧を超える600℃、25MPaという高温・高圧条件下に置くことで、水を気化させるための熱エネルギーを削減、より少ない熱消費量で効率的に発電を行うことが可能になる。液体に一定水準以上の熱および圧力を掛けると、気体から液体への転移が起こる。ボイラー内を常に気体から液体へと転移する以上の圧力をかけておくことで、通常環境下での沸点よりも低い熱量で気化させることができる。この超臨界圧ボイラーを利用することで発電効率が向上、ひいては排出されるCO2の量も7%程度削減することが可能になっている。しかしここで、水を高温・高圧の水蒸気に変換する伝熱管は高温・高圧下で長時間使用されることで部品強度の低下をひきおこす。このため、18-8ステンレス鋼に、モリブデンなどに比べ安価な銅やニオブ、窒素などを最適量添加し、クリープ強度、靱性などを大幅に高めた低コストの高効率火力発電伝熱管用高強度ステンレス鋼管(住友金属工業)などが開発され、超臨界圧微粉炭火力発電設備の長寿命化に貢献している。
先述のとおり、蒸気タービンでは蒸気を高温・高圧化することで高効率化を図ることができる。しかしそうした過酷な環境下での蒸気タービンロータの耐久性を高めるには、ロータ材料に耐熱性に優れるNi基超合金を使うだけでなく、合金温度を低減させる遮熱コーティングがキーテクノロジーとなる。遮熱コーティングは、熱伝導率の小さいセラミックス製の遮熱溶射層(イットリア安定化ジルコニア:YSZ)のトップコートと、遮熱層と基材の間の熱膨張差を緩和して密着性を向上するためのMCrAlYと呼ばれる結合層(ボンドコート)を基材上に成膜した2層構造からなる。しかしこのような遮熱コーティングは、長期使用により結合層が酸化し、割れやはく離が発生する問題があり、定期的なリコーティング補修が必要とされているほか、遮熱層には、球状や層状の気孔が多く含まれ、この気孔の効果によって熱伝導率の低下を図っているが、セラミックスの焼結により気孔が少なくなると、熱伝導率が上昇してしまい、高温部品の信頼性を低下させるという問題もあった。
こうした背景から経済産業省では、省エネ・高効率な発電用蒸気タービン・ガスタービンおよびジェットタービンの実現に向けて、遮熱コーティングの耐久性と信頼性を評価するための試験・測定方法の標準化を進めている。2010年11月にJIS H8453:遮熱コーティングの熱伝導率測定方法、JIS H8454:遮熱コーティングの縦弾性係数試験方法、JIS H8455:遮熱コーティングの線膨張係数試験方法の3件が制定されている( http://www.jisc.go.jp/newstopics/2010/201011tbc.htm )。
超々臨界圧石炭火力発電プラントを手がける日立製作所などでは、蒸気温度700℃クラスといったさらなる高温・高圧化による高効率発電を目指しており、上述のような試験をクリアした優れた遮熱コーティングの普及なども含めた材料・表面改質技術の進展がますます期待されている。
第149回 海洋汚染を防ぐ密封技術で、北極圏油田の開発促進を!
第149回 海洋汚染を防ぐ密封技術で、北極圏油田の開発促進を!北極圏における未発見石油資源量図 デンマーク領グリーンランド沖の海底油田の開発に向けて、石油天然ガス・金属鉱物資源機構(旧・石油開発公団)や国際石油開発帝石、出光興産、住友商事などが出資・設立した「グリーンランド石油開発」が入札に参加する。グリーンランド沖合に埋蔵されている石油は100億バレル以上と推定されるほか、北極圏に埋蔵されている石油は900億バレルに及ぶという(米国地質調査所推定)。地球温暖化に伴う海水の減少で新航路が生まれていることもあって、北極圏油田を巡る石油獲得競争が活発化してきている。
さて、海底油田の開発にあたっては、2010年に起こったBP社の掘削機爆発によるメキシコ湾原油流出事故などはもってのほかで、開発のために航路を行き来する船舶による汚染さえ、非常に厳しく取り締まられている。特に問題視されているのが、プロペラ軸が船内から船外に貫通する船尾管という部位での油漏れである。船尾管の軸系装置の構造
船尾管は、プロペラ軸を支える船尾管軸受と、軸受を潤滑する流体を密封する船尾管シールから構成される。タンカーやコンテナ船などの外航の中大型商船にはホワイトメタル軸受が使われ、油で潤滑されている。この油を密封船外への油漏れ防止の機能を受け持つ。しかし船では嵐や振動などの外乱が大きいため、完全に油を密封するのが難しく、船尾管からの油漏れが大きな環境問題となってきているのである。
大型タンカーの座礁などによる大規模な油流出事故をきっかけに、1983年にIMO(国際海事機構)の海洋汚染防止条約が発効、この条約を受けて各国で油漏れに対する規制が設けられている。米国では2009年に環境保護庁のVGP法が発効、船尾管などすべての推進装置について、シールの保守の義務付け、生分解性の潤滑油の使用を推奨している。
問題の北極海域では、資源開発の本格化を受けて、DNV(ノルウェー船級協会)が極地船規則で、船尾管と可変ピッチプロペラについて生分解性潤滑油の使用を義務付けている。
生分解性潤滑油としてはベースオイルにエステル系、ポリグリコール系を使ったものの大別して2種類がある。いずれの生分解性潤滑油もシール材質のフッ素ゴム(FKM)を劣化させ密封機能を低下させるおそれがある。
ポリグリコール系潤滑油はFKMを膨潤させるため、FKMよりも耐薬品性の優れた四フッ化エチレン-プロピレン系フッ素ゴム(FEPM)などがポリグリコール系油対応の船尾管シール材として開発されている。
また、エステル系油はFKMの主材は膨潤させないが、一部の配合剤との相性が良くないため、配合剤の工夫がなされている。
上述の通り船尾管シールでは油の漏えいを防止するだけでなく、海水が潤滑油に侵入することによる焼付きなど軸受損傷を防ぐことが要求される。これに対し、KEMEL社では、無公害タイプのエアシールを開発、中・大型商船に採用されている。エアシールでは、船内からシールリング側に空気を供給して2本の海水側シールを背面から押し広げ、空気を海水側に吹き出させる。これにより船の喫水の変化を探知し、それに応じた適切な圧力を各部に付加することで、船尾管に海水が浸入するのを防ぐとともに、各シールリングにかかる負荷も小さくしている。また、空気室から供給された空気のうち少量をドレンタンクに戻すことにより、万が一空気室に潤滑油が漏れ出た場合でも、潤滑油をドレンタンクに回収できるようにしている。船尾管シール(無公害エアシール)の構造
海洋汚染防止では生分解性潤滑油を使用し、対応する船尾管シールを組み入れたシステムのほか、水潤滑での取組みも進められているという。そこでは、水という潤滑油よりも低粘度の流体を密封するシーリングや水潤滑下で焼付きなどの損傷を引き起こさない軸受の技術開発も求められている。省エネで生態系・環境にやさしい海底油田開発を推進する上では、航路を行く船舶から石油掘削機までの密封技術の改善・向上がますます求められている。
第150回 B787が世界初就航 省燃費・ロングメンテナンスに向かう航空機
第150回 B787が世界初就航 省燃費・ロングメンテナンスに向かう航空機 全日本空輸(ANA)が世界に先駆けて導入した米国ボーイング社の中型旅客機「B787ドリームライナー」が11月1日、羽田-岡山線、羽田-広島線で定期便として初就航した。ANAでは新型エンジンを搭載し、軽量・高剛性の炭素繊維強化プラスチック(CFRP)を採用したB787を、燃費効率が良く民間航空機市場を活性化させる戦略機材と位置づけ、来年1月には羽田-独フランクフルト線に投入するなど、2017年度までに計55機を導入する計画だ。
こうした中、10月26日~10月28日に東京・有明の東京ビッグサイトで開催された「東京国際航空宇宙産業展(ASET)2011」では、260社・団体が出展、B787に代表されるような高速航行・燃費改善につながる軽量化、安全性を向上させる高耐久性の材料・部品技術、生産性を向上させる加工技術などが多数出展された。
B787の世界初就航記念特別展示として、その1/25スケール模型が展示された傍で、代表的な技術として機体重量の50%に採用されたCFRPの技術が紹介されていた。CFRPはアルミより軽く、鉄より高い比強度、チタンより高い弾性率を持つほか、継続的な負荷に対する優れた強度を持つとともに、歪みにくく摩耗しにくい複合材料。このため軽量化による省燃費化を目的に、B787のほか仏エアバス社のA380など新世代旅客機で採用が相次いでいる。穴あけ加工でのデラミネーションの発生
工具形状や工具コーティングの改善で、穴あけ加工でのデラミネーションの発生なし
しかしCFRPは難削材で、航空機部品で部材接合のために行う穴あけ(ドリリング)などCFRPの切削加工では、積層されたファイバーが穴の出入口などで剥離することで表層剥離や層間剥離、盛り上がりなどが生じる「デラミネーション」などの不具合が発生しやすい。切削加工時の切削抵抗が生じたのに対して、その反力によってデラミネーションが発生するため、この切削抵抗を下げ分散させる工具形状や、ファイバーをせん断するための鋭利な切れ刃と耐摩耗性が必要とされる。これに対しオーエスジーの複合材加工用ドリルでは、Wアングルドリルやトリプルアングルドリルとすることでドリル切れ刃が繊維の軸に対し大きな角度でせん断することになり、切削抵抗の反力を穴の軸方向でなく半径方向に分散させたほか、超微結晶ダイヤモンドコーティングにより切れ刃をシャープに保ち工具寿命を伸ばしている。
CFRPの適用が進んでいるとはいえ、ジェットエンジン1基に使用される素材のうち3~4割は1100℃という耐熱性を有する高いチタン合金が占め、ファンブレードやファンディスク、低圧・高圧圧縮機ブレード、静翼などの主要なチタン合金製部品の加工でも、難削材ゆえの加工性を改善する工具や加工剤の技術が求められている。難削材の加工では工具刃先が高温化しやすく、摩耗が進み工具寿命が低下する。これに対し出光興産( http://www.idemitsu.co.jp )では、この冷却性を高めつつ、相反する高温での潤滑性、刃先での潤滑性・冷却性を発揮させる浸透性を高いレベルでバランスさせたソルブルタイプの水溶性切削油「ダフニーマスタークールWT」を紹介した。チタン合金のミーリング加工では、同切削油が潤滑・冷却の有効成分が刃先まで到達することで刃先の熱的負荷を低減させるため、難削材用従来エマルション切削油に比べて工具寿命が約5倍に向上するという。CVAコーティング装置
ところで、ジェットエンジンでは大量の空気を取り込み圧縮した上で燃料を噴射、点火し爆発させて大きな推進力を得るため、タービン入り口温度を高温、高圧にするほど効率が上がることから、過去10年間にジェットエンジンのガス入り口温度は1,100℃ から 1,230℃に上昇、ガス自体の温度も1,550℃と高温化している。この高温と厳しい運転条件のため、タービンブレードなどの高温になる部品では摩耗や疲労破壊、腐食、酸化が進みやすい。これに対してDKSHジャパン( http://www.dksh.jp )では、タービンブレードやステーターなどのジェットエンジン部品にアルミニウムのディフュージョン膜を作る、イオンボンド社のBernex CVA (Chemical Vapor Aluminizing) コーティング装置を紹介した。CVAコーティング装置は特に、タービンブレードの内部冷却チャンネルのコーティングプロセスとして適用できるとしている。
このほか、航空機部品のトータル加工のニーズに対応すべく、東京都が都内の中小企業10社で構成する共同受注組織AMATERAS( http://www.amateras-tyo.biz )では板金・プレス加工から放電加工、レーザ加工・電子ビーム溶接、切削・機械加工、絞り加工、表面処理、熱処理、組立・整備までをカバー、先ごろ米航空機部品メーカーから圧力調整用のプレッシャーレギュレーターバルブなどの部品を初受注している。
鉄道などと旅客シェアを競う民間航空機では、低コスト化を実現する燃料消費の抑制やメンテナンスコストの削減が不可欠となっている。こうしたニーズの高まりの中で、上述のような中小企業の活躍する場面も増えてくるものと見られる。省燃費化やロングメンテナンス化を実現するべく、軽量化や高い耐久性を図る材料や表面改質技術、加工技術、潤滑技術などがますます求められている。
第151回~第160回
第151回~第160回第151回 東京スカイツリーがギネスに認定、高さ世界一と安全性を誇る機械要素技術
第151回 東京スカイツリーがギネスに認定、高さ世界一と安全性を誇る機械要素技術 2012年5月にグランドオープンを目指す高さ634mの「東京スカイツリー」がこのほど、世界一高いタワーとしてギネス世界記録に認定された。11月17日にギネス世界記録認定式が開かれ、ギネス・ワールド・レコース社社長のアリステア・リチャーズ氏から東京タワースカイツリー社長の鈴木道明氏に認定書が渡された。これまでの世界一高いタワーは高さ600mの中国・広州塔だったが、スカイツリーでは今年3月に634mの最高到達点を達成した。
さて、この世界一高いタワーの長期信頼性を高めるため、様々な材料や機械要素が適用されている。
東京スカイツリー頂上部に使用された円形鋼管と同型の鋼管 まず材料だが、スカイツリー最上部の放送用アンテナを取り付けるゲイン塔には、神戸製鋼所の円形鋼管が採用されている。これは肉厚が最大80㎜で1m2あたり780N級の引っ張り強度(従来の引っ張り強度は590N級)を持つ。降伏比(引っ張り強度に対する降伏強度の比)が通常の95%に対して90%と低いため、外力が加わっても破断するまでの耐性が強く、倒壊に対する安全性が高いという。
また、三菱重工鉄構エンジニアリングは、その放送用アンテナを支えるゲイン塔を600m超の高層部で風から生じる共振現象である渦励振から守る制震装置を納入した。これは倒立振り子型で、ウェイトとウェイトフレームからなる振動体の基部をユニバーサルジョイントが支える構造で、ほかに押し引きバネ、オイルダンパーなどで構成され、制震振幅縦横±70cm(最大振幅±125cm)を実現する。東京スカイツリー向け制震装置
世界一高い東京スカイツリーでは、日本最長の昇降距離となる464mを昇降する東芝エレベータ製トラクション式業務エレベータが採用されている。巻上機を機械室に設けた機械室付きトラクション式エレベータでは、一方にかご、他端につり合おもりをつるしたロープを巻上機の綱車にかけ、ロープと綱車の間の摩擦を利用して駆動する。東京スカイツリーでは、テザックワイヤロープが製造する摩擦特性と潤滑剤の保持力に優れた高強度・高寿命ロープが採用されている。また、その昇降距離464mのエレベータと、地上高350mの第1展望台まで国内最高速となる分速600mで昇降する最大40名を収容する大容量タイプエレベータの巻き上げ機では、日本精工製の専用の静音・低振動自動調心ころ軸受が採用され、巻上機の静音・低振動化を図るとともに、高速化での安全性を確保している。摩擦特性と潤滑剤の保持力に優れた高強度・高寿命ロープ
エレベータ用静音・低振動自動調心ころ軸受
最上部ゲイン塔などの部材の締結に使用されたボルト 材料に戻るが、東京スカイツリーは634mという高さに組み上げられた鉄骨を100年間、錆から守り、強度確保だけでなく美観維持を実現する防食性能の高い塗膜が求められる。634mの高さを組み上げるために必要な鋼材が膨大な量になることや鋼材のサイズが直径2m超、長さ10m超など巨大になること、また高張力鋼でめっき時の熱割れの懸念があることなどから、溶融亜鉛めっきは適用できない。また、金属溶射は溶射業者が限られ処理能力不足で工期に支障が出ることなどから見送られ、重防食塗装が採用されている。上塗りでは旭硝子製のVOC(揮発性有機化合物)を低減した高耐候性水溶性フッ素樹脂塗料が使われ、1回の塗装で25年以上のライフサイクルを実現する見込みという。長大な建築物では、締結部での防食ももちろん重要になる。外周部の鉄骨造塔体本体や最上部ゲイン塔での部材の締結には、神鋼ボルト製の防錆処理高力ボルトが採用されている。
東京スカイツリーはその600m級の電波塔を持つことで、デジタル放送において良好な電波を効率よく配信するという第一の役割に加えて、高さ450mの展望台からは関東一円を見渡す広大なビューが楽しめるなど、国内外から多くの観光客が見込まれている。観光スポットともなる東京スカイツリーでは、制震装置による安定した電波配信や、高耐久性フッ素樹脂塗料による建築物の耐久性と空にとけ込む白を基調とした美観、高耐久性ワイヤロープや静音・低振動ベアリングによるエレベータの安定した高速昇降など、世界一高い自立式電波塔であり続けるとともに、超高層建築物での多数の観光客の安全性・快適性を実現するであろう。
第152回 豊富な資源・地熱の有効活用を!
第152回 豊富な資源・地熱の有効活用を!大容量地熱発電用二車室タービン(提供:三菱重工業)
経済産業省は先ごろ、資源・燃料政策に関する学識経験者らとの意見交換会で国内資源として地熱開発の重要性を強調、企業が地質調査する際の補助制度や、発電のための井戸を掘る資金の債務保証制度を設けることを検討する方針を打ち出した。また、超党派「地熱発電普及推進議員連盟」も地熱発電の適地の約8割を占めるという自然公園内での開発規制の緩和を求める決議をまとめた。わが国では1970年代の石油ショック後に、地熱発電所の開発が相次いだが、開発コストが巨額に及ぶことから普及が進んでいなかった。原発政策が見直される中、グリーンエネルギーとして国内資源が豊富な地熱が注目、早期開発の必要性が高まった格好だ。地熱発電所の構成機器例(提供:三菱重工業)
火山国の日本では、温泉に見られるように、地下深くの熱水など地熱資源に恵まれている。地熱発電はこの地下のマグマ溜まりのエネルギーで熱された熱水と水蒸気を地中から取り出し、そのエネルギーでタービンを回し発電する。具体的には地下約300mから約3000mのところに井戸(生産井)を掘り、その井戸から噴出する高温・高圧の熱水・蒸気を高圧汽水分離器(セパレータ)と低圧汽水分離器(フラッシャ)に導いて蒸気と熱水に分離する。ここで作られた清浄な蒸気がタービンに導入され、地熱エネルギーが機械エネルギーに変換され、さらにタービンに結合された発電機で電気エネルギーに変換される。
地熱発電の効率向上につながる地熱タービンの性能・信頼性を向上させるには、地中から取り出された地熱流体から汽水分離された不凝縮ガス(硫化水素やCO2など)や塩分などを含む蒸気によるエロージョン(機械的作用による浸食)やコロージョン(化学的作用による腐食)に耐える高い耐食性を持たせなくてはならない。ブレード材には13%Cr鋼、ロータ材には1%Cr鋼などが使用されるが、さらにCr量を増加させたり適正な熱処理を施すなど、応力腐食割れを抑える材料技術が適用されている。
さらに厳しい腐食環境や高い応力に耐える技術としては、ブレード材やロータ材にショットピーニングを施すことで、圧縮の残留応力を発生、従来の2倍以上の応力腐食割れへの耐性を実現している。また、特にブレード材では耐食性とともに高い耐エロージョン性が求められるが、耐エロージョンを高めるために材料硬度を高くすると応力腐食割れが劣化する。このため両特性を両立させるタングステンカーバイド系の溶射被膜が適用される。
地熱は、原発20基分にあたる2000万kW分以上の資源量が国内にあるといわれている。その長期にわたるエネルギーをまかなえる資源量と、風力発電や太陽光発電に比べエネルギーの安定供給が期待される地熱発電の普及がより一層進むよう、上述のような地熱タービンなど機械技術のさらなる性能・信頼性向上に期待したい。
第153回 「熱処理・表面処理技術研究会」発足で表面設計指針の作成目指す
第153回 「熱処理・表面処理技術研究会」発足で表面設計指針の作成目指す※当記事は 機械的特性を高める表面改質の情報サイト「mst」より転載したものです。
神奈川県産業技術センターはこのほど、地域ものづくりの競争力を維持するための新たな試みとして、素材表面の熱処理からコーティングまでを含めた総合的な表面設計指針を示すことを目的に「熱処理・表面処理技術研究会」を発足した。
同センターは、平成21年1月に「熱処理技術フォーラム」を開始、年に数回窒化処理鋼材の分析解析結果報告や招待講演を行っていた。しかし、企業支援という観点から見た場合、講演会形式の一方通行の情報提供では限界があると判断。また背景として、アジア新興国の急速な技術力向上、国内人材不足と海外への人材・技術流出、生産拠点の海外シフト、技術体系化不全などの状況を鑑み、個々の企業相談のほかに中小企業と協働で具体的な課題に取り組むことが急務と考え、同研究会の発足に至った。
研究会メンバーは、同センターと熱処理や表面処理を行う表面改質事業者のほかに、神奈川科学技術アカデミー高度計測センター、横浜国立大学、神奈川県金属熱処理協同組合、自動車メーカーなどの大手ユーザー企業などを加え、多方面からの意見やニーズを集約する予定(図1)。図1 熱処理・表面処理研究会の模式図
研究領域としては、新たな技術開発を行わずに、熱処理と表面処理の複合化技術など表面(耐凝着性)、界面(密着力)、基材(強度と靭性)における総合的な表面設計指針を明らかにすることを大きな目標としている(図2)。その上で、具体的産業分野として①金型、工具などを対象とするセラミック硬質皮膜分野②機械構造用部品を対象とする表面硬化処理分野―の二分野に取り組むことを決定。まずは表面改質が採用されることの多い分野に絞って取り組みを始める。図2 具体的研究領域
①は現状、多くの場合が素材(工具鋼メーカー)、機械加工(金型製造業)、熱処理(熱処理業)、セラミック被膜(成膜業)と各工程の専門企業が分担して行っており、トータルでのマネジメントが不充分な状況にあったという。たとえば、金型の破損などの不具合が起こった時にユーザーからクレームがあるが、どこの工程に原因があったのか充分に分析・解析されることがないため、フィードバック機能が不全になることが多い。また現在使用されることの多い膜厚試験や応力測定、硬さ試験などの基礎的な膜質評価と、破損の原因の関連付けが困難な状況にある。これに対し、研究会では実際に金型を製作し、実機評価試験を導入する。金型はブランキング金型と鍛造金型の二種類の金型を製作し、前者は主に凝着摩耗による金型破損、後者は主に繰り返し行われる加工による疲労破壊についての破損機構をフィードバックするとともに、基礎的膜質評価の結果と併せて素材から被膜までの表面設計指針構築につなげていく。さらに、二つの金型において様々な素材や熱処理、被膜の組み合わせを試し、それぞれの破損のメカニズムや耐久性についての考察を行う予定(図3)。図3 セラミック硬質皮膜分野への取り組み
②は、熱処理歪みの少ない表面硬化処理として窒化に着目、窒化ポテンシャル制御を用いた処理で、化合物層の厚さと形態および拡散層深さ制御の可能性評価、化合物層の生成機構と微細構造の解明、疲労強度に及ぼす化合物層および拡散層制御の影響評価などを明らかにするとともに、浸炭焼入れ、高周波焼入れを含めた各部品の負荷応力に応じた表面構造設計指針の高度化を目指す。
同センターでは、今回の研究会発足にあたり「地域の産学公連携による協働体制の下に熱処理・表面改質処理分野の“情報センター”となる研究会に育てたい」と話している。
第154回 東京モーターショーが開催、エコと走りを両立する自動車部品技術
第154回 東京モーターショーが開催、エコと走りを両立する自動車部品技術第42回東京モーターショー2011のもよう
日本自動車工業会( http://www.jama.or.jp )は12月2日~11日、東京・有明の東京ビッグサイトで「第42回東京モーターショー2011」を開催、会期中は84万2,600人が来場した。24年ぶりに会場を東京に移し開催した今回の東京モーターショーでは、国内全メーカー14社・15ブランド、海外からは21社・25ブランド(乗用・商用・二輪・カロッツェリア)が参加し、ワールドプレミア(世界初の発表)53台を含む最先端の製品や技術が多数登場した。今回のショーテーマは、「世界はクルマで変えられる。」"Mobility can change the world."とし、クルマが移動手段だけでなく、環境、安全、エネルギーなど世界の様々な問題の「解決手段」となりつつあるというクルマ社会の未来を、世界に向けて発信した。
トヨタ自動車「プリウスPHV」 トヨタ自動車では2012年1月に発売するプラグインハイブリッド車「プリウスPHV」を出展した。高容量・高出力な新型リチウムイオン電池の採用などで、フル充電でEV(電気自動車)として走行するEV走行換算距離26.4km、EV走行とHV(ハイブリッド車)として走行する燃費を複合して算定したプラグインハイブリッド燃料消費率(PHV燃費)は61.0km/Lを実現、JC08モード走行の場合の電力消費率は8.74km/kWhを達成している。そうした省燃費につながる100km/hまでの走行、坂道走行でEV走行などを可能にするため、モーターのさらなる高出力化が図られている。
ハイブリッド車の出力向上、燃費向上では、小型・軽量化を実現する駆動用モーターとそのトルクを高めるリダクションギヤ、駆動用モーターに大電力を供給する発電機用モーターの高速回転化が進められて、それらを支える軸受の高速化が求められている。これに対し日本精工では、次世代ハイブリッド車のモーター用・発電機用玉軸受として、潤滑が枯渇しやすい内輪側に潤滑油を確実に供給する油流制御プレートの設置や軸受内部の溝寸法や玉径の最適化や保持器の高強度化などで回転数を30000rpm以上に高めた軸受を展示した。ジェイテクトではハイブリッド車の変速機(リダクションギヤ)向け軸受に、高速回転時の遠心力による保持器の変形を抑え、50000rpmという高速回転対応を可能にした軸受を展示した。
ハイブリッド車やアイドリングストップシステムでは、エンジンが頻繁に起動・停止されることから、エンジンベアリングやピストンリングなどの摺動部ではエンジン油の膜が形成されにくい。これに対し大豊工業では、固体潤滑剤である二硫化モリブデンとポリアミドイミド樹脂からなる樹脂コートエンジン軸受を展示し、油膜が形成されずに固体接触した場合の摩擦低減の効果を示した。
富士重工業では、量産AWD乗用車用として世界初の縦置きチェーン式無段変速機(CVT)「リニアトロニック」(5代目レガシーで初採用)を搭載した「ADVANCED TOURER CONCEPT (アドバンスド ツアラー コンセプト)」を出展した。BOXERエンジンの性能をフルに発揮し、常に最適な回転数を維持することで、快適な走りと優れた燃費性能を両立するとしている。チェーン式CVTは、プーリーへのチェーンの巻きかけ径を変化させることで変速、巻きかけ径の最小~最大の幅(レシオカバレージ)が広いほど、トランスミッションとしての変速範囲も広くなる。チェーンは一般的なCVTのスティールベルトに比べ、より小さく曲げることができるため、同じサイズのプーリーの場合、スティールベルトよりも巻きかけ径が小さく、レシオカバレージを広くとることができる。つまりリニアトロニックでは、トランスミッション全体をコンパクトにまとめつつ、全速度域でエネルギー効率が高く、燃費も速度域に関わらず良くなる。また、アクセル操作に対するリニアなレスポンスが良好で、思い通りの加減速ができるため、クルマを操る愉しさがより深まるという。ジヤトコ「CVT8 Hybrid」
リニアトロニックでは独シェフラー社が提供するCVTチェーン(LukハイバリューCVT)を採用しているが、アウディ、スバルに続いて、ジヤトコでも今回、このCVTチェーンを採用したハイブリッド車用CVT「CVT8 Hybrid」を発表した。軸径を小さくしたプーリーと同チェーンを採用することで、軸間距離を大きく変えることなくプーリー比を拡大し、変速比幅をCVTとして世界トップレベルの7.0に拡大したほか、オイルリーク量を低減させることでオイルポンプを小型化し、新開発の低粘度オイルを採用することなどで、フリクションを約40%低減させた。
EV車への対応としては、NTNや日本精工などで車軸軸受(ハブベアリング)にモーター、荷重センサー、電動ブレーキなどを組み合わせてホイールを制御する「インホイールモーター」などが出展された。特にNTNでは、独自インホイールモータシステムと新開発の独立操舵システムにより、その場回転移動や4輪すべてを真横90°方向まで転舵することによる真横方向移動を実現した小型二人乗り4輪電動コミュータのコンセプトモデルを試作、デモ走行を行い、シティーユースとしてのEVの未来像を示した。
環境、安全、エネルギー問題を解決する技術対応が必至の自動車分野ではあるが、自動車メーカーの走りへのこだわりは強い。中国や韓国の自動車需要が拡大する中で、国内のクルマ離れは進む一方だが、クルマの消費喚起を促そうという自動車関連税制の減税も議論されている。上述のような部品技術を搭載したエコと走りを両立する「ワクワクするクルマ」の開発・上市で、わが国の自動車産業の活性化に期待したい。
第155回 原発の40年廃炉に、保全のさらなる重要性を思う
第155回 原発の40年廃炉に、保全のさらなる重要性を思う東京電力では先ごろ、大口など自由化部門の顧客を対象に、4月から電気料金の値上げを行うと発表した。福島第一・第二原子力発電所の被災や、電力を購入している他社原子力発電所の被災、柏崎刈羽原子力発電所の停止の長期化などに対応する中で、安定供給を維持するために、火力発電の焚き増しや長期計画停止中の火力発電設備の運転再開など、供給力の維持・確保に努めた結果、燃料費負担が大幅に増加、今後の燃料調達に支障を及ぼし、電気の安定供給にも重大な支障をきたす恐れがあることから決定に踏み切った。
こうした動きをにらんで、電力使用量の4割以上を占める製造業では、これまで電力需要の3割を賄っていた原子力発電について、安全稼働を確認し国民の理解を得たうえでの再稼働を望む声も高まってきている。この一方で細野豪志・原発相は1月6日、原発の運転期間を原則として40年に制限することを柱とする原子炉等規制法などの改正の方針を発表した。柱となる新しいエネルギー開発が進まない中で電力の安定供給が不安視される中、今回新たに原発の運転期間が法制化されたことで、産業界では批判の声が高まっている。
この批判は、原発の縮減によってさらなる電力供給の不安定さや電気料金の値上げを生むのではという懸念からきているのだろう。しかし、この政策は老朽化した原発を廃炉とする一方で、安全が確認された原発の再稼働は容認するとも受け取れ、それにより電力の安定供給につなげるという見方もできよう。つまりそこでは、当然のことだが、安全な稼働を可能にする保全技術がますます求められることになろう。
さて、原子力発電所の保全指針では、安全で信頼性の高い稼働を実現するため、一般的な産業機械で実施される定期的な修理や事後保全に優先して、運転中に機器の異常な兆候を察知するための状態監視保全の実施が強調されている。
振動診断:振動診断とは、モータなどの回転機器に異常が生じるときに変化する振動を数値化する技術。運転中の振動診断により、機器の異常兆候を早期に検知し、故障内容の診断が可能。 最も一般的に実施されるのが「振動診断」。原子力発電所では、タービン本体とタービン駆動原子炉給水ポンプの軸の振動変位の測定、原子炉再循環ポンプのモータ頂部とポンプ軸受の振動変位の測定でオンライン振動系を用いて常時、状態監視を実施している。このほか、分解点検実施後の機能確認としての回転機器と往復動機器の振動変位の測定や、3ヵ月に1回といった周期でのポンプ・モータなど回転機器の振動速度の測定と劣化徴候の評価などが行われている。機械の故障の約6割が軸受・回転機器の故障によるものとされることから、この診断がしかし、先の保全指針では、「振動診断だけによらず総合的な設備診断により稼働の安全性、信頼性を高めることが必要」と強調している。
赤外線サーモグラフィ:物体の温度を熱画像(写真や映像)として表し、監視する技術。熱画像から得られた情報から、異常な局部加熱や過去データと有意な温度差がないことをなどを確認し、異常兆候を早期に検知。
潤滑油診断:回転機器の軸受や歯車などに使われている潤滑油を採取して、分析する技術。潤滑油の汚れ具合を診断することにより、機器の異常兆候(摩耗など)の早期検知につなげる。 そこで電力会社では設備診断技術として振動診断のほかに、物体の温度を熱画像として表し異常な局部加熱などを早期に検知する「赤外線サーモグラフィ診断」や、回転機器の軸受や歯車などに使われる潤滑油を採取して汚染度などにより摩耗など機器の異常兆候を早期検知する「潤滑油診断」も並行して実施されている。これは軸受の故障の8割が潤滑不全によるものとされるためだ。
ところがこれだけの設備診断技術を謳っていても、すべての原子力発電所の現場でこれらの保全業務が徹底されているわけではなく、常時監視の振動診断結果だけがルーチンで報告され安全と審査され稼働されているという話も聞こえてくる。内閣府原子力安全委員会の安全委員・審査委員に原子力業界から多額の寄付金が渡ったというニュースを聞くと、保全のずさんな状況も、真実味を帯びてくる。
そうは言っても、今回の原発40年廃炉政策が示す“安全が確認された原発の再稼働は容認”されているのが、我が国のエネルギー供給の現状と言えよう。政府の「グリーンイノベーション構想」では、“燃焼によるエネルギー転換は、熱として多大な損失を伴う。この転換効率を高めるのみならず、太陽エネルギーや原子力エネルギーなどあらゆるエネルギー源の転換効率の向上を図る”と謳い、二酸化炭素を削減する手法として原発を掲げていた。原発以外にも低コストで安定的なエネルギー源の開発は引き続き進めなくてはならないが、持続的な経済成長を図る上ではエネルギーの確保が必要で、当面は、安全に管理された原発を安全に利用しなくてはならないことも否定できないだろう。そのためにも、原発の稼働の安全性、信頼性を高めるべく、保全指針が謳うような総合的な設備診断技術が現場で報告だけでなく実際に徹底して実施されることを望むものである。
第156回 ネプコンジャパン2012/オートモーティブワールド2012に見る省エネ・創エネ表面改質技術
第156回 ネプコンジャパン2012/オートモーティブワールド2012に見る省エネ・創エネ表面改質技術 1月18日~20日、東京・有明の東京ビッグサイトで、アジア最大のエレクトロニクス製造・実装技術展「ネプコンジャパン2012」 (インターネプコン ジャパン、エレクトロテスト ジャパン、半導体パッケージング技術展、国際 電子部品 商談展、プリント配線板 EXPO、先端電子材料EXPO、精密 微細 加工技術 EXPOから構成)と、「オートモーティブ ワールド2012」(国際 カーエレクトロニクス技術展、EV・HEV 駆動システム技術展、クルマの軽量化 技術展から構成)、「次世代照明 技術展」が同時開催された。
ネプコンジャパンでは、年々進むエレクトロニクス機器の高機能化・高性能化を支える、最新の製造技術・実装技術が出展され、オートモーティブワールドでは、電気自動車(EV)やハイブリッド車(HEV)などの最新の自動車技術やエンジン車の燃費改善につなげる軽量化手法などが示された。いずれの展示会でも、レアアースなどの高価な材料技術によらず表面を改質することで、機械的特性や電気特性を改善する表面処理技術が展示された。
インターネプコンでの出展をみると、たとえば低摩擦・耐摩耗性に優れるダイヤモンドライクカーボン(DLC)コーティングでは、ナノテックヴァルト( http://www.nanotec-jp.com/wald/ )が、DLCコーティングをベースに第三元素を膜中にドーピングし、低摩擦、高硬度を維持しながら、高耐久性・撥水性・耐熱性などの付加価値を加味したICF膜による生産性の向上を提案した。
都ローラー工業「環境対応型常温DLCコーティング 」 DLC膜ではまた、都ローラー工業( http://www.miyako-roller.co.jp/ )がプラスチックフィルム表面上に常温で成膜できるDLCコーティングを展示、セパレータ基材への成膜で絶縁性や表面硬度を向上しリチウム電池の信頼性を高めることを示した。また、太陽光発電パネル向け塗布装置ドクターロールへのDLCコーティングの適用では、ガラス表面の異物付着低減など帯電防止機能の付加などにより発電効率向上につなげる提案を行った。
新東工業「DASPの歯車への処理例」 一方、オートモーティブワールドでは、新東工業( http://www.sinto.co.jp/ )が、材料・真空浸炭、ショットピーニング技術を融合し、歯車など自動車部品の曲げ疲労強度を約80%向上するプロセス技術「DASP」を展示した。最大約45%の小型・軽量化、駆動ユニットのダウンサイジングが可能となることで燃費性能向上につながることを示した。また、ロボットを使って、ばねの内径にショットピーニングを施し疲労強度を高めるデモンストレーションなども実施した。
また、フロロコート( http://www.fluorocoat.co.jp/ )では、自動車のダウンサイジングに役立つターボチャージャー部品で耐熱性や耐久性を付与、燃費改善、高効率化を図り環境規制(EU6)対応するフッ素樹脂コートを提案した。
エレクトロニクス機器のサプライチェーンの寸断で自動車生産が停止した例にみるとおり、自動車の燃費や安全のための制御にはエレクトロニクス技術が欠かせない。一方で、今なお主流のエンジン車からHEV・EVの省エネ化には軽量化が不可欠である。こうした中で、エレクトロニクス機器の効率向上を図り、自動車部品の耐久性向上により軽量化を図る表面改質技術が注目されてきている。依然、電力の安定供給が懸念される中、ここで示したような省エネ・創エネにつながる表面改質技術の動向が注目されてきている。
第157回 工業用内視鏡の状態可視化で機械の信頼性向上を!
第157回 工業用内視鏡の状態可視化で機械の信頼性向上を! 東京電力は先ごろ、工業用内視鏡による福島第一原発2号機の原子炉格納容器内の調査を行った。廃炉に向けた作業の一環で、炉心溶融(メルトダウン)した核燃料が溶け落ちていると見られる格納容器内の様子や汚染水の水位、内部の温度などを調べるのが目的。工業用内視鏡で観察・撮影された映像からは、内部の配管に大きな損傷はないが、内壁の塗装が溶けており、高温状態にさらされたことや、水面の位置を確認できなかったことから水位が予想以上に低下していることが分かった。
今回観察・撮影に使われたのはオリンパス製の工業用内視鏡で、格納容器につながる貫通口から入れられ、内部を約30分間撮影した。工業用ファイバースコープの構成図
工業用内視鏡の一つ、工業用ファイバースコープは、数千から数万本の光ファイバーを束ねたイメージガイドを通して直接、目視観察できる軟性内視鏡。挿入部、操作部、接眼部から構成され、画像伝送用イメージガイドファイバー、照明用ライドガイドファイバー、湾曲ワイヤーは内部に組み込まれている。手元操作部のアングルレバーで先端部を上下左右4方向に湾曲させることが可能で、これにより先端部を検査箇所に近づけやすくする。先端部を湾曲させる機構では、指の動きと先端の動きがシンクロする「メカニカル湾曲(医療用内視鏡方式)」と、より感覚的な方向の制御を可能にした「ジョイスティック湾曲」との利点を両立させた「トゥルーフィール機構」がある。基本的な構造はメカニカル湾曲であるが、ジョイスティック操作時の負荷をモーターの動力によって軽減させるパワステのような構造になっている。スコープの挿入部
原発内部のように過酷な環境にさらされるスコープの挿入部は、精密な内部構造を守るため、外装はらせん管、編管、樹脂チューブの上に特殊樹脂含浸タングステンブレードを被服した独自の四重構造になっており、極めて強度が高く、ねじれがなく、柔軟性を保っている。こうした材料技術に加え、さらにこのメカニカルな湾曲動作をなめらかに動かすのには、二硫化モリブデンなどの固体潤滑剤が使われている。
非破壊検査は、大掛かりな解体作業や無駄な操業停止を伴わず、短時間で内部状況を確認できる手法として、航空機や自動車、各種プラントの品質管理や状態監視に幅広く使われている。
非破壊検査を行う装置には超音波や渦流、X線などを活用したものがあるが、中でも工業用内視鏡は、わずかな隙間から内部の対象物に接近し、肉眼で見るのと同様に観察でき、リアルタイムで状況を判断できることから多用されている。
今回の工業用内視鏡による撮影で、福島第一原発2号機の状況がすべて明らかになったわけではないが、機械を解体することなく損傷状況を可視化できたことは、決して無駄な試みではなかっただろう。工業行内視鏡によるそうした観察結果をフィードバックすることで、今後の各種プラント機械の信頼性向上設計につなげて欲しい。
第158回 海底シールド工事の信頼性向上に向け岡山・海底トンネル事故の真相究明を!
第158回 海底シールド工事の信頼性向上に向け岡山・海底トンネル事故の真相究明を!岡山県倉敷市の海底トンネル事故現場 2月7日、岡山県倉敷市の鹿島建設施工の海底シールド工事で、海底トンネルの工事現場を襲った出水事故によって、作業員5人が行方不明となり、内1人が死体で発見された。同シールド工事は、水島港の海底約800mを結ぶ第二パイプライン防護設備で、JX日鉱日石エネルギーの2つの工場をつなぐ配管を格納する目的で施工していた。2010年10月からB工場側から縦坑(深さ約34m)の掘削を開始、2011年11月からは横坑(トンネル)の掘削をシールド工法で開始し約160mまで掘進したところで、トンネル内に水が流入、水は一気に縦抗の入り口付近まで上昇した。
パイプライン防護設備図
シールド工法とは、トンネルの先端にシールドと呼ばれる茶筒状の鋼鉄製の外筒を設けて、崩壊しようとする土を押さえながら掘削を行い、内部でセグメントと呼ばれるブロックをリング状に組み立てていく。河川や海底下、大深度など、特に水圧の高い土砂層を安全に施工する工法として多用されている。シールド掘削機
シールドマシン断面図
シールド掘進機(シールドマシン)では、土質に応じて調合した泥水をカッタヘッドチャンバ内にスラリポンプで加圧・送水し、切羽水圧および土圧に対抗させて切羽の安定を図る。掘削土砂は排泥パイプラインにより後方に流体輸送される。
マシン先端で土砂を削るカッタビットには耐摩耗性に優れる超硬合金E2材やE-3材が用いられるが、これらの材料は衝撃には弱い。そこで掘削時の耐衝撃性を高め掘進距離を延長させるため、機械的特性を高める浸炭焼入れなどが施される。また、数mの大径旋回座ベアリングが高荷重を負荷しながらカッタヘッドの高速回転を実現、スムーズな掘進作業を実現している。シールドマシンの後方に高炉セメントB種など耐久性の高い補強材セグメントを送り、トンネルの内張りにしてトンネルを構築するわけだが、そのセグメントの搬送・位置決めには、剛性が高く動きが軽やかなローラタイプの直動転がり案内が使われ、滑らかにセグメントを供給する。一方、カッタビットで掘削した土砂はクロスローラベアリングなどに支持されたスクリューコンベアで、シールドマシンの外に運ばれる。シールドマシンのテール部では、ワイヤーブラシに発泡ウレタンを充填することなどで、高水圧下などでの止水性・耐久性を高め、シールドマシンへの水や土砂の侵入を防ぎ、稼働を円滑にしている。
シールドマシン自体は、こうした技術の積み上げによって信頼性の高い掘削、トンネル構築作業を行うことの可能な多くの実績を持つ機械だ。しかしながら、現時点の調査では、工事元請けの鹿島建設がトンネルの掘削箇所の事前の地質調査を実施していなかったことが判明している。N値50以上の硬い礫で構成されていたという現場の土質は、10年前の地質調査を参考にしたものだという。これが本当で土質の把握ができていなかったのであれば、土質に応じて調合した泥水を加圧・送水し、切羽水圧・土圧に対抗させて切羽の安定を図るシールドマシンの仕事は、成り立たない。
石油業界の高効率化・安定供給のための企業間での石油製品類のやりとりや、またシェールガスなど新たなエネルギーの受け渡しでも、海底パイプライン防護設備の需要は今後ますます高まるであろう。高性能のマシンがあっても、その使用方法や管理によって重大な事故を招いてしまうことは、先の原発事故を語るまでもなく明らかだ。海底シールド工事の信頼性を高め、エネルギー需給の安定性を高めるためにも、事故の真相究明を急いでほしい。
第159回 nano tech 2012/ASTEC 2012開催、ライフ&グリーン・テクノロジーとしての表面改質/計測・評価技術
第159回 nano tech 2012/ASTEC 2012開催、ライフ&グリーン・テクノロジーとしての表面改質/計測・評価技術 「nano tech 2012 国際ナノテクノロジー総合展・技術会議」や「ASTEC 2012 国際先端表面技術展・会議」、「SURTECH 2012 表面処理材料総合展」など8展が、2月15日~17日、東京・有明の東京ビッグサイトで同時開催された。
今回の8展共通テーマは、「Life & Green Nanotechnology 10-9 Innovation」。10のマイナス9乗メートルはナノメートルで、ライフ・ナノテクノロジーとグリーン・ナノテクノロジーは、ナノメートル(nm)レベルの薄膜や微粒子を使い、医療機器や医薬品、食品、化粧品など健康・安全に貢献し豊かな生活に役立つ製品や、自動車関連の次世代二次電池、LED照明、新エネルギー技術、土壌・水質浄化など環境問題の解決に役立つ製品を創出する技術。
今回は主にASTEC 2012 やSURTECH 2012ではグリーン・テクノロジーとしての表面改質技術が、nano tech 2012ではカーボンナノチューブやフラーレンなどのナノ粒子や、微粒子、微粉末、薄膜とその計測・評価技術が展示された。
ライフ&グリーン・テクノロジーとしての表面改質技術
ライフ・テクノロジーの表面改質技術として、たとえば大阪真空化学では、成形品に湿式・乾式で銅・ニッケルめっき、または塗装することでシールド効果を発現するEMIシールドを紹介、医療用機器の外装ケースなどへの適用を示した。
また、ナノテックではDLC(ダイヤモンドライクカーボン)薄膜の特性を物性により分類したICF(真性カーボン膜)を展示、優れた生体適合性から人工関節やステントなど医療機器などへの適用の可能性も紹介した。人工関節では経年による可動部分からの摩耗粉によって痛みや細胞の壊死などにつながり、置換手術後数年で、再手術を余儀なくされることがある。自身の耐摩耗性と相手材に対する攻撃性が少ないDLC膜を人工関節に施すことで、患者は長年にわたり自律的な生活を送ることができる。
グリーン・テクノロジーに貢献する表面改質として、プラズマイオンアシストでは燃料電池など各種新エネルギーの電極材料として、貴金属の代替や安価な材料の使用を可能にする導電DLCなどを出展した。
また、金型や工具の耐久性を高め省資源化につなげる表面改質として、オンワード技研では、PVDとP-CVDによる平滑・高硬度DLCコーティングや、セラミックス、チタン、フッ素コーティングなどを紹介した。
三菱電機ブースでは、環境リスクから使用が規制されてきている六価クロムを含まず、柿渋を使った化成皮膜処理技術を紹介した(アートビーム社開発)。耐食性・コストがクロメート処理と同等で、酸化クロム処理よりもコストメリットが出せるという。
神戸製鋼所では、プラズマCVDを搭載したロールツーロール方式により、ロール間で発生する放電を利用してSiOx(シリカ膜)を成膜しバリア性を生産性よく実現、太陽電池などグリーンエネルギーの高効率化を支援している。
表面改質層の試験・評価技術
DLC膜の国際標準化作業に携わるナノテックでは、DLC膜からの反射光の偏光状態から、硬さや密度と相関性がある膜の屈折率や消衰係数が求められDLC膜の膜質評価が可能で標準化に有用なツールとして分光エリプソメータを提案した。
またDLC薄膜の硬さ試験として、0.04nmの押し込み分解能、0.001μNの荷重分解能を持つため、バルク材の影響を受けずに薄膜自体の機械的強度を測定できるナノインデンターが、CSM Instruments社から展示された。同社ではまた、ステントに生体適合性を付与するDLC膜など各種コーティングの密着性をみるスクラッチテスターなどを紹介した。
東陽テクニカでは、1kVの低加速電圧で10nm以下の分解能を実現するコンパクトFE-SEM(電界放射型電子顕微鏡)を出展した。従来のデスクトップタイプSEMと比べ、電子ビームによる試料表面の帯電が非常に尐ないため、ナノ構造を被覆して埋めてしまう可能性のある導電性コートや、面分解能を落とす原因となる高電圧測定に頼る必要がなく、ガラスなど帯電しやすい試料から、高分子や薄膜、バイオマテリアルなどの電子線ダメージを受けやすい試料まで、幅広い試料の表面構造を高分解能で観察できるという。
表面改質技術は、潤滑剤に頼らずに、材料にない低摩擦特性を付与することで省エネルギー化に、優れた機械特性を付与することで材料やそれを使った部品、さらには機械を長寿命化させ、省資源化に寄与できるグリーン・テクノロジーである。また、生体適合性や耐久性などを付与することでインプラント製品などの耐久性を上げ健康で自律的な生活を支えるライフ・テクノロジーと言える。そうした表面改質技術とその開発を支援する各種試験・評価技術の発展によって、人と環境にやさしいライフ&グリーン・テクノロジーの進展を願うものである。
第160回 スペースデブリ除去衛星で求められる材料・表面改質技術
第160回 スペースデブリ除去衛星で求められる材料・表面改質技術提供:EPFL スイス連邦工科大学ローザンヌ校(EPFL)のチームが、2015~2016年をめどに、ロケットや人工衛星の破片など地球の周りを漂う宇宙塵(スペースデブリ)の回収実験に乗り出す。
地球を周回する人工衛星は、運用を終え、燃料が枯渇し速度が低下するとともに、地上に落ちてくる。地球の周りには現在、10cm以上のスペースデブリが約1万5000個も漂っているとされ、地上に落下する部品は年に400個に及ぶ。その多くは大気圏への再突入で焼失するが、宇宙空間に漂うデブリ同士が衝突し、さらに小さなデブリを増やす自己増殖が始まっている。高度600㎞前後にあるスペースデブリは、時速2万8000㎞で周回しているため、国際宇宙ステーション(ISS)などへのニアミスも起きている。これは東京-大阪間を1分間で移動するのに等しい速さで、一方、破局的衝突に必要なエネルギーを示す平均衝突強度は、アメリカ航空宇宙局(NASA)の一連の衝突実験から、1gあたり40Jという値が得られている。太陽電池パネルを破壊させるのに十分なインパクトを持つ。
これに対し、EPFLでは2015~2016年をめどに、UFOキャチャーのように4指のロボットアクチュエータでスペースデブリをつかむ回収装置を備えた人工衛星を打ち上げ、高度630~750㎞にある直径10㎝四方のデブリを捕獲、回収する計画を進めている。アクチュエータ駆動用には、真空用の超小型モータを開発した。アクチュエータで把持したデブリを大気圏まで運び落として焼却するが、デブリだけ切り離して衛星は再利用するか、衛星ごと燃やすかは今後、検討していくとしている。
一方、日本でもすでに、宇宙航空研究開発機構(JAXA)で「お掃除ロボット衛星」を用いて、スペースデブリを大気圏まで運ぶ研究を進めている。
大型デブリについては、除去衛星を打ち上げて、ロボットアームや伸展式のブームなどでデブリを捕獲して、導電性テザーなどで減速させ、大気圏に再突入させて燃やす方法を検討しているほか、除去衛星よりも大きいデブリについては、除去衛星から投網のような物を投げて捕獲するというアイデアもある。おそうじロボット衛星のイメージ。ターゲットとなるデブリにアームを延ばしてしがみついて、デザーをのばし、大気圏に一緒に突入する。(提供:JAXA)
このうち、現在活発に開発が進んでいるのが、導電性テザーという長い紐を使った除去衛星(お掃除ロボ衛星)。目標のデブリに近づき、お掃除ロボ衛星から捕獲用のアームを伸ばしてしがみついた後、導電性テザーという長いひもを数km伸ばしてデブリに取り付ける。電気的な力で自動的にデブリにブレーキをかけデブリの速度を落とすことで、衛星とお掃除ロボ衛星が徐々に高度を下げ、大気圏に落としていく。導電性テザーの構成
導電性(ベア)テザーは、重量、強度、電気抵抗、熱光学特性、電子収集特性、柔軟性、テザー繰り出し時の摩擦特性などを考慮して構成が決定、軽量化のため導体はアルミニウムとし、高強度のステンレス繊維と編むことにより強度・剛性とも向上させている。またテザー形状については、ミリサイズのデブリが衝突してもテザーが切断されないように、ブレーディング、網などの長寿命テザー構成を検討し、合金の種類や太さ、強度繊維などを変更して数種類の試作を行われている。
この導電性テザーは、結び目なしに編み上げる丈夫な 無結節網の製造機を世界で初めて発明した漁網メーカーの日東製網が開発を進めている。髪の毛くらいの細さの繊維を撚り合わせた直径約1㎜の紐3本が網状に編まれている。小さなスペースデブリと衝突して1本が切れても、残り2本で耐え、網の機能が保てるものができているが、さらに強度や宇宙空間での摩擦特性を向上させるため、導電性テザーへの固体潤滑材のショットピーニングなど各種の表面改質技術が検討されている。
JAXAでは、2020年度までに、まず運用を終了した衛星の除去を目的とした小型衛星で技術実証を行い、次いで大型衛星による実用化を目指している。使用済み衛星やロケットを年間5基ずつ除去できれば現状の環境をほぼ維持でき、それ以上のペースで除去できれば危険回避に向け改善されていく可能性があると考えている。
現在新たに打ち上げられる衛星では、運用を終えた後に軌道を意図的に下げて大気圏に安全に落下させるシステムが取られているが、スペースデブリ化した場合の責任の所在は明らかになっておらず、我が国も参加して、衛星などがスペースデブリ化しないようにするための国際指針の策定が、国連で進められている。引き続き、運用を終えた衛星が確実に大気圏で焼却されるシステムを徹底化させるとともに、スペースデブリ化した衛星の掃除が確実に行われるよう、各国でのお掃除ロボット衛星の技術開発の進展に期待したい。
第195回 2014日本ダイカスト会議・展示会を開催、熱処理やブラストなどの表面改質技術を多数紹介
第195回 2014日本ダイカスト会議・展示会を開催、熱処理やブラストなどの表面改質技術を多数紹介日本ダイカスト会議・展示会のもよう 日本ダイカスト協会( http://www.diecasting.or.jp/ )主催の「2014日本ダイカスト会議・展示会」が11月13日~15日の三日間、横浜市西区のパシフィコ横浜で開催、展示会では136企業・団体が出展した。
ダイカストとは、溶融金属を精密な金型に圧入することにより、高精度で鋳肌の優れた鋳物をハイサイクルで大量に生産する鋳造方式の一種。ダイカストの金型は熱間工具鋼などで作られ、ダイカストマシンに取り付けて、溶融したアルミニウム合金、亜鉛合金、マグネシウム合金、銅合金などを圧入して鋳造する。その工程はほぼ自動化されており、生産性の高い大量生産に適している。ダイカストは、他の鋳物に比べて寸法精度が高く、強度に優れ、鋳肌が滑らかで美しく、機械加工も少なくて済む。このような特徴から、金型などに多く使用されており、それに伴い様々な表面改質が適用される分野の一つ。今回の展示会でもコーティング、熱処理、ブラストなどの受託加工を行う企業や装置メーカーが数多く出展した。
「スーパーボロンコーティング」を成膜したサンプル オリエンタルエンヂニアリングは、プラズマCVD(PCVD)により各種セラミック膜、DLC膜を成膜した金型サンプルなどを出展した。PCVDは、一度の工程で真空を破らずに窒化などの拡散硬化処理とコーティングの複合処理が可能なことで比較的簡単に処理が可能だとした。また、新開発の膜として硬さHV4000以上で優れたトライボロジー特性、耐酸化性、耐溶損性、離形性、耐ヒートチェック性を有する「スーパーボロンコーティング」を紹介。この被膜は、PCVDによりTiNとTiAlN、TiAlBNを積層した多層膜で、アルミダイカスト金型・押出金型などの熱間加工用金型から、高張力鋼板加工用金型などの冷間加工用金型まで幅広く適用できるという。
大同DMソリューションのブース 大同DMソリューションは、素材から熱処理、コーティングを一貫して提案できる事業内容の詳細と、コアピンメーカーであるスグロ鉄工と共同で提供する短納期・高品質の鋳抜きピンの供給体制を紹介した。表面改質のラインアップでは、塩浴窒化やガス浸硫窒化、ガス軟窒化、イオン窒化などの熱処理、特殊窒化処理と微粒子ピーニングとPVDコーティングの複合処理「アミコートシリーズ」、耐ヒートチェック性と耐溶損性に優れ、ダイカスト金型に適した表面処理として「アミナイトSS」をPRした。
展示されたダイカスト製品(日本ダイカスト協会) メックインターナショナルは、アルミ溶湯の保温性、湯流れ性を向上させ、金型への耐溶損性も向上させるアルミダイカスト用の「カーボンコーティング」を提案。炭素膜によって溶湯と鋳造型の基材が直接接触することが防止され、鋳造型への溶湯の焼付きや離型抵抗の増大を抑制できるなどのメリットから、アルミダイカスの入子、ピン、スリーブ、チップなど、アルミ溶湯が接触する部品への適用を促した。RTMは、金型の初期微小クラックの補修とともに耐久性を向上する技術を紹介した。この技術は、レーザー溶接を用いて耐熱性に優れた金属複合化層を被覆し耐久性を向上させ、独自の窒化処理技術「タイマ処理」と複合することにより耐ヒートチェック性や耐溶損性を兼ね備えた表面組織を形成する。
「HBF-156」の実機を展示したニッチューのブース 熱処理やコーティングで受託加工の提案が中心に行われる中、ブラスト関連では装置メーカーの出展が多く見られた。ブラストの総合メーカーであるニッチューでは、ダイカスト製品用のハンガータイプショットブラスト装置「HBF-156」の実機を展示。同装置は、投射スピード用インバータや高性能セパレータロータリースクリーンを標準装備。ブラスト室が2室装備してあり、1室で作業者がワークの着脱をしている間、区切られた別の1室でブラスト処理を行うことができるため、効率的な作業が可能。バリ取り、肌調整用ショットブラスト、打痕のない処理もハンガー型により可能であるとした。また、ステンレスカットワイヤーや合金アルミカットワイヤー、亜鉛ショットなど、様々な研削材の紹介も行った。
新東工業のブース 野村ユニソンは、モジュール型エアーブラスト装置「NU-BLAST11」の実機を展示。同装置は、製品を1個ずつ自動でブラスト加工することをコンセプトに開発されており、研削材をノズルから狙った箇所にピンポイントで投射することが可能なため、製品ごとにバラつきがなく均一に仕上がる加工を実現している。また新東工業は、ダイカスト生産現場で期待される・安全・品質・環境、さらにコストダウンを実現するショットブラスト装置の改良提案やダイカスト金型の寿命向上、ダイカスト製品の不良低減などの技術を紹介した。
第196回 ネプコンジャパン2015/オートモーティブワールド2015に見る表面改質技術
第196回 ネプコンジャパン2015/オートモーティブワールド2015に見る表面改質技術オートモーティブワールド2015入口 1月14日~16日、東京・有明の東京ビッグサイトで、エレクトロニクス製造・実装技術展「ネプコン ジャパン2015」 (インターネプコン ジャパン、エレクトロテスト ジャパン、半導体パッケージング技術展、電子部品・材料 EXPO、プリント配線板 EXPO、微細加工 EXPOから構成)と、「オートモーティブ ワールド2015」(国際 カーエレクトロニクス技術展、EV・HEV駆動システム技術展、クルマの軽量化技術展、コネクティッド・カーEXPO、自動車部品 加工 EXPOから構成)などが同時開催された。
ネプコンジャパンでは、年々進むエレクトロニクス機器の高機能化・高性能化を支える、最新の製造技術・実装技術が出展され、オートモーティブワールドでは、電気自動車(EV)やハイブリッド車(HEV)などの最新の自動車技術やエンジン車の燃費改善につなげる軽量化手法などが示された。いずれの展示会でも、表面を改質することで、機械的特性や電気特性を改善する表面改質技術が展示された。
ネプコンジャパンのもよう ネプコン ジャパンの出展を見ると、カナックがSUS製リフローチェーンのメンテナンス回数を減少させる表面処理としてガス窒化処理「Kanuc(カナック)」を提案。500度前後の加熱雰囲気中に数時間保持し、鋼表面から窒素を拡散浸透させ金属元素と反応させることで硬化層を生成。これによりSUSが1300HV以上の硬さになり、無給油での操業が可能になるとした。摩耗軽減されるため、コンタミ防止効果も高く、スプロケットやレール等に処理しても効果的だという。
野村鍍金は、めっきのほかにDLCコーティングを紹介。「タフ カーボン」は、成膜温度が100度以下の低温成膜で硬さ5000HV、耐熱温度500度以上を実現した。離型性も良好であるため、超微細金型に適用してもはんだ、アルミ等が付着しない点などを紹介した。また、半導体・電子部品向けプローブなどへの適用を提案した「タフ コンダクター」は、DLC膜に導電性を付加。硬さ4000HVを維持した上で体積抵抗5×10-3Ω・cmの低抵抗を実現した。さらに同社では、抵抗値を1.0×10-3Ω・cmと体積抵抗を1/5に抑えた「新タフコンダクター」も紹介した。
右がZERO-Ⅰコーティングの処理品 一方、オートモーティブでは清水電設工業がプレス金型や抜き金型など、過酷な状況下で使用される金型に対して優れた耐摩耗性を実現する「ZERO-Ⅰコーティング」を提案。被膜の硬度は3500HVで、耐熱性においては1100℃を実現。焼付きの原因となる冷間鍛造での摩擦熱による酸化や温間鍛造にも対応している。さらに、応力緩和の技術により高密着性と厚膜化を両立。これにより、耐摩耗性を向上させるとともに弾性変形の抑制効果を上げることが可能となった。高硬度皮膜のため、母材はハイス鋼以上を推奨。用途によっては窒化やショットピーニングとの複合処理を推奨している。
日本高周波鋼業グループのカムスは、ハイテン材冷間プレス加工等の高負荷のかかる成形金型において金型の耐久性を向上させるPVDコーティングとして「MACHAON(マカオン)コート KS-G」を提案。この技術は基材上に密着・基材保護層としてCr系被膜を5μm、耐摩耗・耐熱層としてTi系被膜5μmの二層で構成することにより、高い耐面圧性と耐熱性を有しており、金型の耐久性を向上する。東洋ドライルーブは、フッ素等の潤滑性物質と速乾性の溶媒を使用し、金属・樹脂・ゴム等の対象物に塗布することで、ドライもしくはウェット状のふっ素被膜を薄膜で形成する速乾性潤滑剤「LUBICK」や、一昨年から受託加工を開始したDLCコーティングを紹介した。
ハードAに対して耐摩耗試験を実施 また、フッ素樹脂コーティングの受託加工専業のフロロコートは、フッ素樹脂コーティングの特性である耐熱性、難付着性、すべり性を損なうことなく、耐摩耗性、密着性、硬度などを向上させた「ハードA(エース)」を紹介。この被膜は、基材に対して溶射により硬質層を形成し、表面にフッ素樹脂コーティングを被覆した複合プロセス。被膜サンプルに対して耐摩耗性試験を行う様子を展示するとともに、自動車分野の用途としてテールランプ熱溶着用金型やタイヤ用金型に使用された事例などを示した。
高砂工業「TVC 真空浸炭炉」 熱処理関連では、高砂工業が従来の真空浸炭炉と比較して安全性や操作性を重視した真空浸炭炉「TVC 真空浸炭炉」を紹介。省エネに配慮した新しい真空浸炭炉操業支援ソフトを拡充し、最適条件を容易に選択することが可能にした。また、浸炭処理時間は昇温から油焼入れ完了までのサイクルタイムが従来の炉と比べて30~45分の削減が可能になったことなどをPRした。さらに、新製品として従来、洗浄において10分を擁していた乾燥時間を特殊真空ポンプの開発により1〜2分に短縮する「TVD 真空洗浄機」も紹介。同洗浄機の導入により効率の高い熱処理工程を実現するとした。
第197回 ASTEC2015/SURTECH2015開催、表面改質技術や表面試験・評価機器が一堂に会する
第197回 ASTEC2015/SURTECH2015開催、表面改質技術や表面試験・評価機器が一堂に会する展示会のもよう 「ASTEC2015 第10回 先端表面技術展・会議」や「SURTECH2015 表面技術要素展」、「nano tech2015 第14回 国際ナノテクノロジー総合展・技術会議」など15の展示会が、1月28日~30日に東京・有明の東京ビッグサイトで開催、47649名が来場した。
今回は、表面改質関連のASTECやSURTECHのほか、機能性材料と有機エレクトロニクスデバイス関連の「新機能材料展2015」、塗る・貼る・切るという三大要素の加工技術の「Convertech JAPAN2015」、フィルム製品と加工技術の「フィルム産業展2015」など、ナノテクノロジーから材料、加工、エネルギーに至るまで幅広い展示会が一堂に会した。展示会では、DLCコーティングやセラミックコーティングのドライコーティング、熱処理、めっきなどの表面改質処理から、その処理による材料の機械的特性などを評価する硬さや密着性、摩擦・摩耗特性などの試験・評価技術などが紹介された。
ナノテックが展示したRoll to Roll成膜装置 ナノテックは、グループ会社で安定化電源・安全試験の平和電機、ファインセラミックスコーティング受託加工のTSジャパン、医療・バイオ向けDLCコーティングのトッケンと出展。DLC薄膜を機能別、用途別に分類した「ICFコーティング」(真性カーボン膜)を紹介するとともに、大電力パルススパッタリング(HiPIMS法)によって高機能水素フリーICFを660nm/minの超高速で成膜できるRoll to Roll成膜装置を紹介した。日本コーティングセンターは、同社の新しいDLCとしてPCVD法とイオン化蒸着法、UBMS法のハイブリット方式で成膜を行う「Neo-スリック」を紹介。被膜硬度がHV1000~3000で負荷を受けても優れた密着性を発揮し、さらに耐久性と耐摩耗性、低摩擦を実現する被膜としてPRを行った。特徴としては150℃以下の低温成膜のため真鍮やアルミ合金、亜鉛ダイカストなどの非鉄金属への成膜が可能なことや、ポリカーボネートやウレタンゴムなど絶縁物専用の処理として100℃以下の成膜が可能な条件を確立した点などを挙げた。
「ドライプロセスによる自動車向け表面処理ゾーン」として日本コーティングセンター、プラズマイオンアシスト、日本マクダーミッド、オリエンタルエンヂニアリングが出展 また、プラズマイオンアシストは独自技術より、燃料電池用金属セパレータのコスト削減を可能にする導電性DLC「LR-DLC」を紹介。同セパレータに要求される耐食性、導電性を同社開発のDLCを成膜することで、母材をアルミニウムに置き換えても充分な特性を得ることができる。現在、大量生産用の高速インライン装置の開発も進めているという。日本マクダーミッドでは、自動車の内装部品やカーオーディオ、電気製品などのプラスチックパーツを加工・装飾する「FIM(Film Insert Moulding)」を紹介。逆さに印刷されたシートを適宜成形、裁断し最後に射出成型を行うことで、レンズとボディなど複数のパーツをハードコートフィルムで一体化させることが可能な技術だという。耐擦傷性、耐溶剤性、耐薬品性に優れるとともに対象パーツの表面に新たな触感や光沢を与えることができ、インクを変えることで任意の色にすることが可能。欧米の自動車メーカーを中心に採用が進んでいるという。
Openair-Plasmaのデモのもよう 日本プラズマトリートでは、大気圧下で被処理材に密度の高いプラズマを衝突させることで表面を活性化、これにより洗浄効果や材料表面の粗面化、コーティングに適した表面を形成する「Openair-Plasma」のデモを行った。この技術は、プラスチック、金属、ガラス、紙、布地、複合材などに適用が可能で、最速生産が900m/minと高速なためインラインプロセスに無理なく組み込むことができる。また、ノズルを多軸ロボットに搭載することで、複雑な形状や深い溝の中の処理が可能になるという。グループ本社であるドイツを中心に自動車、電子機器、医療、新エネルギー分野など多くの産業で採用されている。
トリニティーラボのブース こうした技術によって形成された表面を測定する試験・評価機器も多数出展された。摩擦摩耗試験機や触覚評価測定機、物性測定機などの試験機を扱うトリニティーラボは、1台で薄膜や厚膜、塗膜などの界面特性(付着・破壊強度)と表面特性(摩擦・引っ掻き強度)が測定できる被膜性能評価機「フィルメータ ATPro301」、材料やコーティング膜など物質表面の静・動摩擦係数と触覚評価が1台で行え、テーブル型、測定部摺動型、測定部上下摺動型と測定に応じて三つのパターンで試験機を構成することができる摩擦摩耗試験機「TL201Ts」の実機を展示した。
東陽テクニカのブース 東陽テクニカでは、ISO 14577 Part 1~3に完全準拠しており、データの再現性を完全に維持しながら、材料の機械特性データを高速に高い信頼性で収録できるナノインデンターシステム「Nano Indenter G200」を紹介。ナノスクラッチ試験、密着強度や破壊靱性の評価などに対応、粘弾性測定や疲労試験といった動的試験への応用も可能なことなどをPRした。このほか低加速電圧・高コンストラストの機能に加え、高分解能化を実現したFE-SEM(走査型電子顕微鏡)や試料表面の正しい評価を行える新しいコンセプトの走査型プローブ顕微鏡(SPM/AFM)の紹介などを行った。
オミクロン ナノテクノロジー ジャパンのブース オミクロン ナノテクノロジー ジャパンは、HYSITRON社製のナノインデンテーション装置「TI950 Tribo Indenter」を紹介。走査型プローブ顕微鏡(SPM)機能による表面形状像、ナノインデンテーション、ナノスクラッチ、ナノウェアなどの標準装備のほか、ナノインデンテーション装置技術を応用して微小構造物や薄膜をそのままの状態で粘弾性評価を行える「ナノ領域粘弾性測定」や、異なる荷重領域の二つのヘッドを並列させることでソフトウェア上の切替えのみでマイクロスケールからナノスケールまで測定できる「高荷重インデント」のオプションについての解説を行った。
現在、自動車産業が好調なこともあり、新企画として「ドライプロセスによる自動車向け表面処理ゾーン」が設置されるなど時流に合わせた出展が多数見られたほか、「バイオ・医療に貢献する先端表面技術」、「MRJの挑戦 ~国産旅客機を世界の空へ~」といった未来を見据えた新産業に関する講演なども行われた。表面改質は、様々な処理方法によって新たな機能を付与することが可能な技術であり、その特徴からあらゆる分野で適用の可能性がある。こうした展示会で、今まで適用のなかった分野の需要を掘り起こし、全体の処理数量を拡大させ続けることが日本製造業の競争力向上につながるものと思われる。
第198回 人とくるまのテクノロジー展2015開催、環境保全と信頼性向上に貢献する表面改質技術
第198回 人とくるまのテクノロジー展2015開催、環境保全と信頼性向上に貢献する表面改質技術自動車技術会は5月20~22日、横浜市西区みなとみらいのパシフィコ横浜で「自動車技術展:人とくるまのテクノロジー展2015」を開催、環境や安全関連などのテーマを中心に各種の次世代技術の出展がなされた。ここでは同展での出展技術のうち、環境、特に燃費改善など環境保全に関わる技術を紹介したい。
トヨタ自動車のブース 自動車メーカーでは、トヨタ自動車が昨年12月に市場に投入した燃料電池車(FCV)「MIRAI」を出展、高圧水素タンクや小型化と世界トップレベルの出力密度を実現する燃料電池FCスタックのカットモデルを置いて、究極のエコカーの姿を提示した。また、マツダが4代目となる新型ロードスターを展示、世界一の高圧縮比(14.0)を達成し、燃費と低中速トルクを従来比で15%改善した新世代高効率直噴ガソリンエンジン「SKYACTIV-G 1.5」の搭載と、軽快なシフトフィールと大幅な軽量・コンパクト化を実現したFR用6速トランスミッション「SKYACTIV-MT」の採用などで、走りの愉しさと省燃費性能を両立する先進の内燃機関技術を示した。
エコカーのエンジンの耐久性を支える表面改質技術
大豊工業のブース ハイブリッド車などエコカーでは、エンジンのオン・オフが頻繁に行われるためエンジン油の油膜の形成が難しく、従来なじみ性を受け持っていた鉛成分が環境面から使えない。この状況下で、クランクシャフトの回転を支えるエンジンベアリングの耐摩耗性を確保する狙いから、固体潤滑剤を分散させた樹脂層を施した鉛フリーの固体潤滑オーバレイエンジンベアリングが大豊工業や大同メタル工業などで出展された。
各種ピストンリングを展示(日本ピストンリグ) また、 燃焼ガスのシール機能やエンジン油のコントロール機能、ピストンで受けた熱をシリンダへ逃がす伝熱機能、ピストン姿勢のサポート機能を持つピストンリングでは、希薄エンジン油下での耐摩耗性や耐久性を高めつつ低フリクション化を図る対策の一つとして、潤滑性を高めるDLCコーティングがピストンリング各社(リケン、日本ピストンリング、TPR)で適用され始めている。中でも、水素含有DLCで問題にされるエンジンオイル中の添加剤によるDLC膜の摩耗促進の心配がなく、硬質で摩耗に強い水素フリーDLCコーティングが採用されている。
カシマコートをコーティングした部品など さらに、ミヤキは硬質アルマイトに潤滑機能を付加した「カシマコート」を紹介。この技術は、1次電解で生成させたアルマイト(陽極酸化)皮膜の微細孔に二硫化モリブデンを電気誘導させて析出させる。この二硫化モリブデンが微細孔の中に溜まっていくことで潤滑性を高め、耐摩耗性の高い皮膜が形成される。ロッカーアームにおいては、鉄からカシマコート処理されたアルミへと変更された際に、その自己潤滑性によってベアリングが不要となり、大幅な軽量化とコストダウンに成功したという。
トランスミッション・金型の信頼性を高める固体潤滑コーティング
二硫化モリブデン系の固体潤滑コーティングを施した「外径コーティング軸受」 近年、自動車に対する低燃費・高出力の要求は益々強くなってきており、トランスミッション用軸受では、軽量化による自動車の低燃費化からアルミニウム製トランスミッションケースが採用され、熱を含むケースの変形などから、トランスミッション内の軸受嵌め合い面で摩耗損傷が発生する場合がある。運転時に軸受外輪が僅かずつ回る外輪クリープと呼ばれる現象によるもので、この外輪クリープによりトランスミッションケースと軸受外輪との間に摩耗が生じ、ギヤの噛み合いずれによる異音発生、回転不良などトランスミッションの不具合の原因となる。このため、外輪クリープの発生メカニズムの解明とそれに基づいた安価で抜本的な防止対策が求められていた。これに対し不二越では、軸受の外輪外径に二硫化モリブデン系の固体潤滑コーティングを施した「外径コーティング軸受」を開発、ハウジング摩耗を抑制することでクリープ防止の溝を不要にしつつ、トランスミッションの不具合を防ぎ信頼性を高めている。
ナノコート・ティーエスとH.E.F Durferrit Japanのブース DLCコーティング関連では、H.E.F Durferrit Japanとナノコート・ティーエスが共同出展。DLCコーティングの処理品などを展示したほか、A5052アルミ合金ボールと多層膜のDLCコーティング「セルテスDC2500」を施したディスク試料の摩擦摩耗試験を行った結果をパネルで発表した。その上で、セルテスDC2500はアルミ合金に対して優れた耐凝着性と耐摩耗性を示しており、アルミ飲料缶製造における各種塑性加工金型や自動車部品の塑性加工金型に多く実用されていることなどを解説した。
グローバル戦略や研究・開発・人材戦略など日本の自動車産業が発展する上での課題は多いが、今回の来場者数(86939名)が示すとおり、自動車産業が日本経済の屋台骨を支えていることは間違いない。今回紹介したようなフリクション低減による燃費改善技術をはじめ、日本がリーダーシップをとる自動車分野を牽引し続ける、革新的な技術が絶えず求められている。
第199回 機械要素技術展開催、ピーニングやコーティングなど機械要素の機能を高める製品・技術が展示
第199回 機械要素技術展開催、ピーニングやコーティングなど機械要素の機能を高める製品・技術が展示第19回機械要素技術展のもよう 表面処理・改質技術、バリ取り・表面仕上げ、試験・計測機器/センサ、軸受や直動案内機器、歯車などの機械要素、金属や樹脂などの材料とその加工技術などに関する専門技術展「第19回機械要素技術展」が6月24日から26日、東京・有明の東京ビッグサイトで開催した。主催のリード エグジビション ジャパンが同時開催した「第27回設計・製造ソリューション展」、「第7回医療機器 開発・製造展」、「第24回3D&バーチャルリアリティ展」を合せて約82000名が来場した。ここでは、表面改質関連の展示について紹介する。
不二WPCのブース 不二WPCは、金属の疲労強度向上と微細なディンプルを付与するショットピーニング「WPC処理」や、金属加工の最終仕上げとして用いられている砥粒研磨技術「3Dラッピング」、安定した密着力でナノレベルの薄膜を成膜するDLCコーティング、各処理の複合処理による機能向上についてPRした。ブースでは各処理を施した製品を展示したほか、来場者が持ち込んだ品物の静摩擦係数を図るデモンストレーションを実施、同社が行った各処理サンプルとの摩擦係数をその場で比較できるようにした。
新東工業のブース 新東工業では、ショットブラストやエアーブラスト、バレル研磨機などの表面処理装置、各種ブラスト用投射材、受託加工サービスを紹介。ブースでは、回転フックに製品を吊り下げ回転させながらブラスト処理を行うハンガー式ショットブラスト「SHBX-Ⅱ」の実機を展示した。加えて、ブラストおよびショットピーニング処理後の表面に対する評価を行う技術「Sightia(サイティア)」により、約10秒で応力測定を行うインライン型のX線測定装置、ピーニング処理において正常処理と未処理・不完全処理を評価するピーニング非破壊検査装置の展示を行い、他社との差別化を行った。
オキツモのブース コーティング関連では、オキツモが超精密潤滑コーティングシステム「UPLコーティング」を紹介。同システムは従来の潤滑塗料と同社独自の塗装技術を組み合わせたもので、微小部品や複雑な形状でも薄膜でかつ均一な塗膜(膜厚精度±1μm以下)で塗装することが可能。低荷重に適したフッ素タイプと高荷重に適した二硫化モリブデンタイプをラインアップすることで、高潤滑・低摩耗を実現。これにより品質の安定と不良率の大幅な低減につながるという。用途としては、ベアリングやシートベルト金具などの自動車部品、精密機器部品など油の使用が敬遠される分野で採用が広っがているという。
東北特殊鋼のブース 東北特殊鋼は、窒化処理において化合物層を生成させずに従来窒化法と変わらない硬度分布を示し、処理前後の表面粗さの変化がないことから研磨仕上げが不要な特殊窒化処理「キリンコートS」、この窒化層を下地としてDLCやTiN、TiCN、CrNなどのPVDコーティングを施す「キリンコートC」を紹介。複合処理によりコーティングの密着性が向上することからコア、ピンなどの射出成形金型やダイ、パンチなどの冷間鍛造金型、摺動部品を中心とした自動化設備用精密部品などに適用が進んでいるという。
新明和工業のブース また新明和工業は、DLCコーティングのサンプルやイオンエッチングによる除膜サンプルを展示したほか、大面積電子ビーム加工装置の実機を展示。この装置は、電子ビーム照射により金属表面を自動で平滑化。金型の最終仕上げや金属表面欠陥層の除去、金型、部品等の耐食性、光沢性向上、微小な部品のバリ取りなどに適用できるという。
日本マクダーミッドのセミナーのもよう 出展者による製品・技術PR公開セミナーでは、日本マクダーミッドの田岡道子氏が「マクダーミッドのカラースタイリストが提案する最新のトレンドカラー」と題して登壇。世界の有名ブランドで取り入れられている色や最近の流行の色などについて解説した。売れる商品の色としては、火や血を連想させる赤、暗闇や夜を連想させる黒、空や水を連想させる青、雲や雪を連想させる白を挙げた。また、日本の地域においても好みの色が分かれるとして各地域で好まれる色の紹介、欧米で好まれるマット調の色を自動車メーカーの実例を挙げて紹介した。最後に、「最近では弊社が販売しているめっき材料においても様々な色が表現できるようになっている」ため、使用する国・地域や用途によって同社独自の提案を行う意図を示した。
第200回 JASIS2015開催、表面試験・評価機器が一堂に集結
第200回 JASIS2015開催、表面試験・評価機器が一堂に集結 日本分析機器工業会と日本科学機器協会は9月2日~4日、千葉市の幕張メッセ国際展示場で、分析機器・科学機器の総合展示会「JASIS2015」を開催した。「未来発見」(Discover the Future.)をテーマにアジア最大級規模の497社・団体、1472小間が出展した。ここでは、表面試験・評価に関連する製品・技術展示について紹介する。
新東科学「HHS2000/3000」 新東科学は、各種摩擦摩耗試験機を出展。実機を展示した「HHS2000/3000」は、1回の測定で、摩耗回数、垂直荷重、摩擦力、摩耗体積の関係を示す三次元摩耗形態グラフ作成、摩耗の遷移に対応する臨界荷重の決定ができる荷重変動型摩擦摩耗試験システム。無駄な試験片を必要とせず、試験時間を大幅に短縮することに加え、煩雑なデータ解析を解消して測定データを得ることができる。測定要素は荷重変換器による抵抗力測定、変位計による摩耗量、摩耗痕、引掻き深さ測定がある。また、オプションの「トライボCCDシステム」を併用することにより、摩耗粉の挙動解析・潤滑剤の移動状態など、さらに進んだ試験を行うことができる。展示では、製品のPRを行うとともに受託試験の案内も行った。
協和界面科学は主力の接触角計とともに自動摩擦摩耗解析装置「TSf-502」の実機を展示した。同品は、独自の機構であるクランク形状二軸天秤の採用により不要な力を検出せず、正確な摩擦の波形取得を実現した自動摩擦摩耗解析装置。同装置の標準繰返測定は最大12回まで繰返し往復運動をして静・動摩擦係数測定を行う。往復測定か往路のみの測定かを選択可能で、往路のみの場合は天秤を自動でピックアップし原点位置まで復帰する。連続静摩擦測定では、設定した移動速度、距離、回数で連続測定を実施する。試料変更測定においては、ステージのハンドル操作で試料もしくは測定位置を変更して静・動摩擦係数測定を行う。また、回数依存、荷重依存、速度依存、停止時間依存の4種の依存性が評価行える。
アントンパール・ジャパンの機械的特性評価機器 アントンパール・ジャパンは、振動式密度・濃度・比重計、粘弾性測定装置、自動マイクロ粘度計、スタビンガー粘度計、ゼータ電位測定装置等とともに機械的特性を計測するスクラッチ試験機や摩擦摩耗試験機、ナノインデンテーションテスタの実機を展示した。インデンテーション測定では、「ウルトラナノインデンテーションテスタ」で、700℃までの高温環境でノイズや熱ドリフトなくナノ領域の変位の正確な計測を可能にする装置の開発や、温度制御機能や湿度制御機能などを備え生体組織のインデンテーション試験を可能にする装置の開発を行っているという。また、卓上式のインデンテーション・テスタにAFM(原子間力顕微鏡)を搭載することが可能になり、コンパクトなスペースで測定およびビジュアルデータを取得することが可能になったことなどを紹介した。
東陽テクニカのブース 東陽テクニカは、表面や内部の構造解析・物性評価を行う分析機器を紹介。同社が販売を行うカールツァイス社のFE-SEMは、独自のカラムデザインを採用し、試料に減速用のバイアス電圧を印加せず、極低加速での観察を可能とし、その時の二次電子と反射電子を分離収集できる。これにより、得られたコントラストが何に起因するかを多角的に判断できるデータを提供する。さらに、FE-SEMにSPM/AFM、ナノインデンター、X線CTの機能を追加することで、ナノスケールの形態観察と組成分析だけでなく、物理・電気・機械特性の解析、内部構造の観察など、材料解析に必要な多くの情報を得られるようになることなどを紹介した。
パルメソは、材料表面の摩耗量の変化を摩耗率という指標で表すことで、様々な材料の深さ方向の表面強度を比較することができる「MSE試験装置」と、この技術を応用して開発された分析前処理用エッチング装置「PERET(ピーレット)」の実機を展示した。ピーレットは、セラミックスや樹脂、ゴム、金属など様々な材料表面において変質なくサブミクロン分解能のエッチングを可能にしたことにより、XRD、ラマン分光、SEM、X線残留応力などの深さ方向分析が行える。短時間処理を行えることや、簡易な操作、最小エッチング深さ10nmと高分解能が可能な点などを利点として拡販を図る予定。現在、販売予約を受け付けるとともに顧客からのサンプルテストにも対応している。
リガク「SmartSite RS」 リガクは、ショットピーニングされた鉄鋼材料表面の残留応力評価に使用できる可搬型X線応力測定装置「SmartSite RS」の実機を展示。同品は小型(幅114×奥行き248×高さ111mm)、軽量(3kg)を実現したヘッドユニットにより、内径200mmの配管内部を測定可能。対象物が屋外の構造体であれば、標準装備のキャリーケースに入れて持ち運び、その場で応力測定することができる。電源確保が困難な場所でもオプションのバッテリーによって駆動することもできる。短時間で測定できることも大きな特長で、高感度なピクセル型半導体2次元検出器を採用したことで、一般的な試料をわずか60秒で測定できる。
大塚電子「FE-300」 大塚電子は分光干渉法と自社製高精度分光光度計を利用した膜厚測定機「FE-300」の実機を展示。反射スペクトル測定により、非接触・非破壊でサンプルを傷つけることなく膜厚を測定できる。また、同機のハイエンドモデルとして「FE-3000」を紹介。最小3μmの微小エリアの測定を行うため、サンプルが例えばドリルやシャフトのような3次元形状がある場合でも、その頂点や底面といった測定光学系の軸に対して垂直なポイントは、平板と同じように水平とみなして測定することができるという。測定範囲は1nm~1mmまでと幅広い膜厚に対応しており、多層膜の測定も可能なことから、DLC膜や有機EL、半導体レーザ内光学膜、樹脂膜の膜厚・膜質解析に実績がある。
第201回 東京モーターショー2015が開催、環境保全と走りの快適性に貢献する部品・材料・表面改質技術
第201回 東京モーターショー2015が開催、環境保全と走りの快適性に貢献する部品・材料・表面改質技術日本自動車工業会( http://www.jama.or.jp )は10月29日~11月8日、東京・有明の東京ビッグサイトで「第44回東京モーターショー2015」を開催した。乗用車、商用車、二輪車、カロッツェリア、車体、部品・機械器具関連製品、自動車関連サービス、SMART MOBILITY CITY 2015を含む総合ショーとして開催。世界11ヵ国から合計160社が参加し、国内全ての乗用車・商用車・二輪車メーカー14社15ブランド、海外メーカー16社26ブランド(乗用車・商用車・二輪車)が出展した。FCA(フィアット クライスラー オートモービルズ)グループの4ブランド(アルファ ロメオ/フィアット/ジープ/アバルト(初出展))が8年振りに復帰したほか、フランスのDSが初出展し、メルセデス・マイバッハが復帰するなど、多くの海外ブランドが東京ビッグサイトに集結した。
ワールドプレミアは76台(乗用車42台、商用車6台、二輪車18台、カロッツェリア5台、車体5台)、ジャパンプレミア(日本初の発表)は68台(乗用車49台、商用車1台、二輪車15台、車体3台)が出展された。
FCV元年、水素化社会を支える部品技術
トヨタ自動車「FCV PLUS」 トヨタ自動車では今回、水素エネルギーが普及した近未来を想定した燃料電池車コンセプト「TOYOTA FCV PLUS」を出展した。車外の水素でも発電が可能で、自宅や移動先でも電力の供給減となる。
左:高圧水素供給バルブ、右:減圧弁 同社では昨年末に燃料電池自動車(FCV)「MIRAI」を市場に投入しているが、同FCVでは70MPaの高圧水素タンクを搭載。ジェイテクトでは、同FCVの動力源となる高圧水素が貯蔵されているタンクに装着され、高圧水素を封止・供給する役割を担う「高圧水素供給バルブ」と、バルブから供給された高圧水素を下流のスタックで使用可能な圧力まで減圧する「減圧弁」を開発し、提供している。
「HONDA WANDER STAND CONCEPT」 ホンダでは、「WANDER=自由に動き回る」をコンセプトにした電気自動車(EV)「HONDA WANDER STAND CONCEPT」を参考出品した。全方位駆動車輪機構の「ホンダ オムニ トラクション ドライブ システム」により、身体を傾け体重移動するだけで速度や方向が変えられ、前後左右・斜めまでどの方向にも自由自在に移動できるため、細い路地にも自由自在に入れる。
日本精工「ニューEVドライブシステム」 同システムについては明らかにされていないが、今回トラクションドライブでは日本精工が「ニューEVドライブシステム」を参考出品。アドバンスド アシスト ステアリング 2 エンジンに代わる自動車の動力源となるもので、高速モータを内蔵し、圧縮された瞬間だけ硬くなる性質を持つ特殊なオイルを介して、ローラで動力を伝達することで、歯車を使わずに動力を伝えるトラクション減速機を採用。トラクション減速機は“転がり"で動力を伝達するため、摩擦損失が少なく、静粛性に優れているという。
エンジンの省燃費化を支える表面改質技術
FCVやEVの進化を謳う出展が多い中で、低フリクション技術を積み上げて省燃費化を図る内燃機関車の最新技術も多数披露された。その中でマツダの「飽くなき挑戦」を象徴するロータリーエンジン(RE)搭載のスポーツカーコンセプトモデル「Mazda RX-VISION」では、三角形のロータが回転することによって動力を生む、独特の構造をもつREエンジンの出力、燃費、耐久性などの性能向上を推し進めた。
REエンジンの耐久性向上ではこれまでに、耐摩耗性や低摩擦性を実現するダイヤモンドライクカーボン(DLC)コーティング技術なども貢献したが、リケン、日本ピストンリング、TPRのピストンリング3社では水素フリー化DLCコーティングによってエンジン油中のモリブデン系耐摩耗添加剤による劣化がなく、また厚膜化によって長期間DLC膜の特性を保持するアプローチが示された。
日本ピストンリング「ディンプルライナ」 また、日本ピストンリングではピストンリングと摺動するシリンダライナとして、シリンダ内周面のピストンストローク中央部に微細なディンプルを形成し、流体潤滑下で摺動面積を減らすことでピストンリングとの摩擦力を低減しエンジンの燃費改善効果をもたらす「ディンプルライナ」を展示した。
自動車メーカーでは環境、安全、エネルギー問題への対応が喫緊の課題だが、今回のモーターショーでは、クルマ本来のあるべき姿である走りの快適性などの新しい形が多方面から示された。こうした中で、ここで一端を示した部品・や材料・表面改質技術の進化によって、走りを楽しみつつ環境保全に貢献する車が次々と登場してきている。
第202回 MEDTEC2016開催、医療機器に求められる安心・安全の技術
第202回 MEDTEC2016開催、医療機器に求められる安心・安全の技術世界の医療機器の市場は2013年で約40兆円、日本の同市場は2014年で2.9兆円と過去最大を記録するなど、拡大基調にある。
欧米に比べ医療機器の承認審査期間が長かった日本国内においても、ここ数年で期間短縮や規制緩和などの施策がなされ、また昨年には米国立衛生研究所(NIH)を参考に日本の医療分野における研究開発の司令塔となる「日本版NIH」の中核機関「日本医療研究開発機構(AMED)」が設立されるなど、日本の医療機器産業の育成に向けた開発支援の気運が高まってきている。
こうした中で4月20日~22日に東京ビッグサイトで開催された医療機器の製造・設計に関するアジア最大の展示会「MEDTEC Japan 2016」では、504社・団体が出展した。展示の一端を紹介することで、医療機器に求められる安全・安心のための各種のアプローチを検証したい。
材料技術ダイセル・エボニックの「VESTAKEEP®デンタル」 ステント、カテーテルや人工関節など生体内で用いられるインプラント機器では特に、材料の生体適合性が求められる。これに対してダイセル・エボニックでは、従来の真鍮の人口歯根と、フルベニアまたはパーシャルベニアなどの複合材料を用いて作られた人工義歯(写真左下)に代えて、長期耐久性に優れ生体適合性の高いポリエーテルエーテルケトン(PEEK)樹脂「VESTAKEEP®デンタル」による一体成型品の人工義歯を提案した。
陽和は、C-F結合から耐熱、耐薬品、非粘着質などの特徴を持つフッ素樹脂の加工技術による医療・分析機器の課題解決ソリューションを提起した。たとえば接着剤を使わず熱と圧力による接合方法で不純物が溶出する懸念のない「PFAビードレス溶着」を、人工透析システム配管部品に適用することを提案。溶着部が完全に一体化しているため液漏れの心配がないことや、内面の平滑化により接合部への滞留を防ぎバイオフィルムの形成を抑制する、などのメリットを示した。
表面改質技術 また、トーヨーエイテックは膜中組成制御によって弾性率を変化させることで、金属だけでなく樹脂などの基材の変形にも耐えうる密着性を実現。医療機器の性能向上に貢献するダイヤモンドライクカーボン(DLC)コーティングを紹介した。ステントにすでに応用済みで、高い生体適合性を実現するという。
トッケンは、抗菌性や抗血栓性、低溶血性、耐腐食性、耐薬品性、耐体液性など医療器具や理化学器具、医療用材料などに最適な特性をDLCコーティングに付加した、ナノテック製の「医療・バイオ向けICFコーティング」を提案した。同コーティングによって、血液付着防止や乱反射防止などの機能を付与することでメスや鉗子などに、細胞増殖性を付与することで培養プレートなどに、高耐久性・離型性を付与することで打錠機、錠剤機などに適用できるとした。
東レ・ダウコーニングは、注射針の表面処理や各種医療機器部材の表面潤滑処理、表面撥水処理、離型剤、プレフィルドシリンジ用潤滑剤として適用できる、医療機器用シリコーン処理剤「Dow Corning Medical Grade」を展示した。適用に合わせフルイドやエマルジョン、ディスパージョンの選択が可能で、医療機器に使われる各種部材に処理することによって、部材表面に潤滑性を付与する。
モーション技術 スガツネ工業は、動きを創造するテクノロジー「モーション デザイン テック」をベースとした、確実で安全で円滑な開閉動作を可能にする機構部品を提案した。たとえば検査センターの大型分析装置や医療機器などで、大型の重い上カバーを女性でも片手で楽に持ち上げられるパワーアシストモーションを紹介した。この「パワーアシストヒンジ」(写真)は圧縮ばねが元に戻るときの反力を利用して持ち上げる操作をアシストするもので、同時にダンパーにより、上カバーを閉める際に、手を離してもゆっくりと閉まっていくため、安全性・静音性を実現している。
竹内精工の「リニアガイド」 竹内精工は、ミニチュアを中心とする直動案内「リニアガイド」や「球面フランジ型リニアベアリング」などの各種ボールブッシング、超精密の「研削ボールネジ」などを幅広く展示。医療機器では特に、臨床検査機器などでミニチュアリニアガイドが採用されてきている、とした。
ハイウィンの「下肢筋力トレーニングマシン」 ハイウィンは、自社の各種モーション機器を組み合わせることで、模擬歩行訓練で患者の自律を促す「下肢筋力トレーニングマシン」(写真)や、内視鏡を固定して支持し精密で確実な位置決めを可能にする「低侵襲手術ロボット」を紹介した。
生産管理システムカールツァイスの「O-SELECT」 カールツァイスは、新製品の卓上型ワンボタン式デジタル画像測定器「O-SELECT」を展示。測定台にワークを置いてボタンを押すだけで、測定精度4.5+L/100μm、繰り返し再現性0.9μmと精度の高い測定を、自動(フォーカス自動設定、照明自動設定、要素自動認識)で行う。加工した医療機器部材の品質管理に利用できる。
HOYAサービスの「Microsoft Dynamics AX」 HOYAサービスは、医療機器生産管理で実績のある医療機器業界向け生産管理プレート「Microsoft Dynamics AX」を紹介した。ロット管理・シリアル管理・製番管理や品質トレーサビリティなどを実現できる同テンプレートを活用することで、失敗しないERP(総合基幹業務システム)導入が可能なことや、ERP導入の効率化も実現し導入期間を低減できることなどをアピールした。
規制緩和などによって医療機器分野への新規参入企業が増えつつある中、従来の材料技術にとらわれない各種のテクノロジーが提起されてきている。医工連携の取り組みも交えて、わが国の医療機器市場の拡大がますます期待されている。
第203回 人とくるまのテクノロジー展2016開催、環境・安全に対応する機械要素技術
第203回 人とくるまのテクノロジー展2016開催、環境・安全に対応する機械要素技術自動車技術展「人とくるまのテクノロジー展2016横浜」(主催:自動車技術会)が5月25日~27日、横浜市のパシフィコ横浜で開催された。過去最大規模となる538社が、ハイブリッド車(HEV)や電気自動車(EV)などの電動化、水素社会実現に向けた燃料電池車(FCV)、先進運転支援システム(ADAS)、さらには自動運転などを見据えて、最新の製品・技術を披露した。
電動化車両の進展:HEV~FCVへ
トヨタ自動車「4代目 新型プリウスのカットモデル」 地球環境保全を背景に、燃費改善によるCO2排出量削減を目的に、HEV、プラグインハイブリッド車(PHEV)を中心とした電動化が進んできている。2050年に走行時CO2排出量の10年比90%削減を目指すトヨタ自動車では今回、JC08モードで40.8Km/Lを達成する「4代目 新型プリウス」のカットモデルを展示。ガソリンエンジントップレベルの熱効率40%を実現したほか、新型リチウムイオン&ニッケル水素バッテリーの採用で軽量化と小型化を実現。トランスアクスルは、リダクションギヤの平行軸歯車化などで約20%の損失低減を図っている。また、モータ複軸構造化などにより小型・軽量化を達成した。
ホンダ「CLARITY FUEL CELLのカットモデル」 ホンダは、燃料電池スタックや水素/空気供給システムといった発電機能と、FC昇圧コンバータや駆動モータなどの配電/駆動機能をコンパクトに集約し、前後幅、左右幅、高さのすべてでV6エンジンと同等のサイズを実現した燃料電池パワートレインを搭載した燃料電池車(FCV)「CLARITY FUEL CELL」のカットモデルを出展した。70MPaの充填圧力に対し水素透過ゼロを達成したアルミライナ製水素タンクを採用。70MPaに対応し、サイズの異なる2本構成とすることで、パッケージング効率を高めながら水素貯蔵量を25%増加している。
自動運転に向け、ADASを先進化
富士重工業「アイサイトver.3を搭載したWRX S4」 富士重工業は、運転支援システム「アイサイトver.3」を搭載した「WRX S4」を出展した。アクティブレーンキープがオンになることで、走行車線を認識しハンドル操作をアシスト、車線中央付近の走行を維持し車線逸脱を抑制する。Ver.3では、「走る」「止まる」に加え、「曲がる」領域での運転支援を実現した。
自動車部品による電動化や安全性向上への対応
こうした自動車の電動化や先進運転支援システムなどの安全性向上への高まりを受けて、自動車部品各社では以下のような製品・技術を披露した。
NTNでは、小型・軽量化を実現したEV向けの「新インホイールモータ」を展示した。平行軸歯車式減速機とハブベアリングの組み合わせで軽量・薄型化を達成したほか、ベース車の懸架・転舵構造を変更することなく車両搭載を可能にしている。左右輪の独立駆動による車両安定制御システムを提供できる。
NTN「電動モータ・アクチュエータの電動シフトセレクタへの適用事例」 同社ではまた、自動車の駆動・制御で普及が見込まれるバイワイヤ制御に不可欠な、汎用性の高い「電動モータ・アクチュエータ」2種(同軸タイプと平行軸タイプ)を展示した。軸受やボールねじの製品技術とモータの設計技術、車両制御のための電子制御技術とを組み合わせたもので、ブースでは平行軸タイプの電動シフトセレクタへの適用を提案した。
ジェイテクト「ラックパラレルタイプ電動パワーステアリング」 ジェイテクトは、最適な駆動力伝達によって優れたトラクション性能と低燃費を実現し、駆動系の小型・軽量化を実現する「ITCC電子制御4WDシステム」を紹介した。また、減速機を弾性支持することでスムーズな中立でのステアリングフィールと路面情報の伝達性向上を実現するとともに、ボールねじの新デフレクタ構造などによる摩擦、トルク変動、振動を抑制した「ラックパラレルタイプ電動パワーステアリング(RP-EPS)などを展示した。
日本精工は、「アクティブオンセンタリング制御」を搭載したEPSを展示した。ドライバーがハンドルにかける力加減と車速や舵角といった走行情報を組み合わせて演算することで、ハンドル操作時にEPSが常に最適な舵角とアシスト力と導き出す技術で、安定した軌跡で直進状態に戻ることで、高速走行での車線変更の際のふらつきや、低速走行時にハンドルを戻すわずらわしさを低減し、ストレス、無駄、無理のない操作に寄与する。
日本精工「次世代クリープフリー軸受」 同社ではまた、設計・材質を最適化することで軌道輪(外輪)の剛性確保と独自開発した高温耐油性Oリングにより、機械的な固定をすることなく、高温の潤滑油にさらされる環境下でも“クリープ"と呼ばれる軸受のすべり現象を大幅に抑制した「次世代クリープフリー軸受」を展示した。クリープに起因する振動とノイズの増大が抑制されることで、HEV・EVの一層の快適性向上に貢献する。
不二越「ELT軸受」 軸受においてトルク低減は燃費改善につながる。不二越では、特殊ボール軸受デザインによって、つば滑りがなく点接触となるため低トルク円すいころ軸受に対し30~50%のトルク低減が可能な「ELT軸受」を展示した。
昨年、トヨタ自動車が2050年に向けた「脱エンジン」宣言を行った。この意味するところはもちろん、エンジン技術だけで先述のCO2排出量削減目標を達成することは難しいとの判断から、エンジンのみの車をなくして、ハイブリッド車(HEV)、プラグインHEV(PHEV)、燃料電池車(FCV)、電気自動車(EV)といった電動化車両を中心に据えていこうという計画だ。
こうした中で自動車部品の開発においては、電動化に対応した小型・軽量の電動ユニットや、ステアバイワイヤ技術の進化などに加えて、HEVにおいてEV走行寿命の延長につながる軽量化や低フリクション化なども、引き続き重要になると思われる。
そうした一方で、2014年に自動車9社が中心になって自動車用内燃機関技術研究組合(AICE:アイス)を発足、ガソリン・ディーゼルエンジンの燃費向上に向けた共同研究を加速させているように、欧州勢に対抗しグローバルで勝ち残っていくうえで、今後も市場の中心となるHEVで重要なエンジン技術の進化は欠かせない。
大豊工業「樹脂コーティング付きエンジン用軸受」 エンジンは数百点の部品によって構成され、多数の摺動する部品の間で生じるフリクションにより、全体の1割以上にのぼるエネルギーロスが発生している。フリクション低減対策としてはすでに、バルブリフタやピストンリング、ピストンピンなどで適用が進んでいるダイヤモンドライクカーボン(DLC)や、HEVでのエンジン起動時の摩擦トルクや耐摩耗性を改善した大豊工業の樹脂コーティング付きエンジン用軸受など、様々な技術が登場している。
自動化に向けた次世代自動車技術を支える自動車部品において、電動化対応と並行して、従来からの小型・軽量化・低フリクション化の技術の追求が、ますます求められてきている。
第204回 人とくるまのテクノロジー展2017開催、環境・安全に対応する材料、表面改質、機械要素の新技術
第204回 人とくるまのテクノロジー展2017開催、環境・安全に対応する材料、表面改質、機械要素の新技術 自動車技術展「人とくるまのテクノロジー展2017横浜」(主催:自動車技術会)が5月24日~26日、横浜市のパシフィコ横浜で開催された。過去最大規模となる550社が、内燃機関の燃費改善に加え、ハイブリッド車(HEV)や電気自動車(EV)などの電動化、先進運転支援システム(ADAS)などを見据えて、最新の製品・技術を披露した。新型プリウス試乗会のようす
電動化車両の進展
これまで一充電走行距離の一層の延長が課題とされてきた電気自動車(EV)に関して、日産自動車は「NOTE e-POWER」を展示。充電を気にすることなくどこまでも走れるEVの新しい形を示した。e-POWERは、エンジンを発電専用に用いる。燃費に悪影響を与える作動領域を使用しない分、エンジンの作動時間を短縮。さらに、ごくわずかな減速でも回生エネルギーがとれるよう設定した。発進時から一気に最大トルクを発生するモータ特有の優れた瞬発力や、アクセルの踏み増しに対する高レスポンスの反応などにより、市街地から高速道路まで、あらゆる走りのシーンで優れた燃費性能を発揮する。日産自動車NOTE
e-POWER
こうした自動車のエンジン-モータの新たなハイブリッド技術による燃費改善や、さらに先進運転支援システムなどの安全性向上への高まりを受けて、以下のような製品・技術が披露された。
運転支援技術に対応する機械要素技術
アドヴィックスは、自動車技術会 技術開発賞を受賞した「環境対応車向け電子制御ブレーキシステム」を展示した。同ブレーキシステムは、ドライバーのペダル操作に応じて、より多くの回生制動力と最適な油圧制動力を発生できるバイワイヤ構成としつつ、電気系失陥時であってもペダル踏み込み力を倍力する機構を織り込み、高いフェールセーフ性と燃費向上を両立。一方、運転支援技術や衝突回避技術の実現には短時間での大きな制動力発生が求められるが、リニアソレノイドバルブにより緻密にコントロールされた圧力で、大流量レギュレータを駆動する世界初の方式により、高い調圧精度による違和感のない回生協調制御と、世界トップレベルの昇圧性能による高い衝突回避性能を両立したブレーキシステムを実現している。アドヴィックス「環境対応車向け電子制御ブレーキシステム」
日本精工は、自動車向けアクチュエータや工作機械で培った技術・ノウハウを活かしたボールねじをラックタイプEPS用に最適化した「ボールねじ式ラックタイプEPS(舵角重畳機構付き)」を展示した。小型、軽量、低コスト化とともに、良好な操舵フィーリングと低作動音を実現するほか、EPSの構成部品であるモータ、ECU、トルクセンサそれぞれを冗長設計とすることで、1重故障ではアシストを止めないシステムを実現した。さらに、舵角比を任意に変更可能な舵角重畳機構により、通常走行時の操舵性能、および緊急時の安全性を大幅に向上できる。日本精工「ボールねじ式ラックタイプEPS(舵角重畳機構付き)」
ピストンリング、シリンダーライナを主力とする日本ピストンリングは、高トルクインホイルモータによるダイレクト駆動が可能な「3D形状圧粉コアを用いたアキシャルギャップ型モータ」を参考出品した。アキシャル構造、3D形状圧粉コアによる高トルク化が実現でき、ギヤレス化による機械損失の低減・ギヤ音削減が図れ、また、Air GAP可変によるモータ特性のチューニングが可能、といった特性から、マイクロモビリティ•カート•車いすなどの低速・高トルク駆動用途への適用を提案した。日本ピストンリング「3D形状圧粉コアを用いたアキシャルギャップ型モータ」
エンジン部品の低フリクション化
ハイブリッド車(HEV)、プラグインHEV(PHEV)、電気自動車(EV)といった電動化車両の各国での導入支援が活発化する一方で、国際エネルギー機関(IEA)では、2050年の時点でも乗用車用動力の約8割を内燃機関が占めるとの予測を打ち出しており、2014年に自動車9社が中心になって自動車用内燃機関技術研究組合(AICE:アイス)を発足、ガソリン・ディーゼルエンジンの燃費向上に向けた共同研究を加速させている。
大豊工業は「エンジントライボロジー現象解析を通じ、エンジン部品の低摩擦化技術の開発」で浅原賞技術功労賞を受賞したトヨタ自動車との共同開発となるエンジンベアリング「細溝付き主軸受」を展示した。エンジン油のサイドへの漏れ(漏れ油量)を減らし軸受の潤滑油量を低減できることで、エンジン油を供給するオイルポンプの容量を低減(オイルポンプのダウンサイズ化)が図れ、駆動損失の低減にもつながるという。大豊工業「細溝付き主軸受」
燃費改善にかかわる表面改質技術
シェフラージャパンでは、マツダの「SKYACTIV-D」の可変動弁機構として採用されている「スイッチャブルフィンガーフォロワー」を展示した。カムと摺動するスイッチャブルフィンガーフォロワーのスライディングパッドでは、カムと相性が良く、高荷重でのフリクションを低減し耐摩耗性を向上するコーティングが検討され第2世代の2014年からはエンジン油中のモリブデン系添加剤に影響されない水素含有DLC(ダイヤモンドライクカーボン)膜が被覆されている。シェフラージャパン「スイッチャブルフィンガーフォロワー」
シーケービーでは、燃費向上から適用の進むアルミ製シリンダーブロックで一般的な鋳鉄製シリンダーライナを撤廃しつつ、ピストンリングとの摺動に耐えると同時に摩擦を低減できる溶射膜を形成する、独Sturm社のシリンダーボア溶射装置の技術を紹介。6気筒エンジンで数㎏という軽量化を実現できるほか、約2mmの厚みがあるシリンダーライナに対して、同溶射技術では被膜は0.15mmと非常に薄く、軽量化に加え、熱伝導性が良くなりエンジンの冷却性能が上がるためノッキングが起こりにくくなり、エンジン効率が全体的に向上する。シーケービー「シリンダーボア溶射技術」
軽量化による省燃費化を図る材料技術
ダイセル・エボニックは主に金属部品の使われるしゅう動材料として軽量化・自己潤滑化が図れるポリエーテルエーテルケトン(PEEK)を提示したほか、独自開発のプルプレス(PulPress)方式により、構造発泡体のロハセル(ROHACELL®)を用いて自動車向け複雑形状の複合成形部品を大量生産するための技術を初披露した。この新製造プロセスにより、従来の鋼鉄構造に比べ約75%軽量化した複合部品は優れた耐衝撃強度を保持。さらに従来のレジンインジェクションなどの方式で製造される複合部品と比べて、最大60%のコスト削減を実現する。ダイセル・エボニック「構造発泡体ロハセルのプルプレス方式で作られた複合部品」(写真右に立てかけてあるのが複合部品サンプル)
自動運転に向けた次世代自動車技術を支える自動車部品においては、電動化に対応した技術と並行して、内燃機関の燃費改善で培われてきた小型・軽量化・低フリクション化の技術の追求が、ますます求められてきている。
第205回 FOOMA JAPAN 2017にみる食品機械の生産性・安全性向上
第205回 FOOMA JAPAN 2017にみる食品機械の生産性・安全性向上
FOOMA JAPAN 2017(国際食品工業展)が6月13日~16日、東京ビッグサイトで開催された。ここでは、同展にみる、食品機械における生産性向上と、安全衛生面の向上の取組みを紹介したい。
潤滑技術が、どう使い分けられているか?
近年、異物混入事件などに伴い「食の安全」が声高に叫ばれる中で、食品機械には異物混入を防ぐことや、菌の繁殖を抑えることが強く求められている。一方で食品機械は、食品加工業者にとって生産性、つまりはコストにかかわる生産機械のため、突発故障に伴う稼働休止(ダウンタイム)のロスを最小限に抑える目的で、保守管理、特に軸受・潤滑管理が重要になる。
食品機械において、コンベアなどに運ばれて食品が通過する製品ゾーン(プロダクトゾーン)の真上などに駆動機器がある場合には、使われるベアリングなど部品は腐食に強いステンレス製とするとともに、近年は、ベアリングに封入されたグリースが漏れ出て食品に混入したとしても人体に害を及ぼさない組成の「NSF H1規格」登録のグリースが推奨されている。
食品機械用潤滑剤を使用する必要性は、食品工場向けロボットを含めて、食品機械の種別を問わず浸透してきているようだ。しかし、すべての可動部に食品機械用潤滑剤を適用するわけではなく、細かく使い分けられている。安川電機 可動部にNSF H1グリースを使用した「トッピングロボットシステム」
たとえばフライヤーは調理油に浸漬された状態でエビなどを載せた下側コンベアが稼働し、その下方に配置されたランプヒータなどの熱源により油温が上げられて揚げ作業が行われる。この時に食材の上方に設置された押えコンベアが同期して稼働している。この押さえコンベアは食品の上方にあって食品と接するため、コンベアの軸受グリースには食品機械用グリースが用いられている。しかし、調理油の中で稼働する下側コンベアの軸受には高温に耐えるグリースがないとの認識からか、ベース金属中に固体潤滑剤を均一に分散させた金属系無給油すべり軸受(大同メタル工業の「サーマロイ」など)が使われているという。プロダクトゾーンから分離されたカス取り装置の軸受などには、一般的な鉱油系グリースを使っている。
また、前川製作所では冷やした空気を吹き込むことで、冷凍庫内の温度を下げ冷凍を行う「エアーブラスト方式」(空気凍結)と庫内に設置されたスリットからの噴流を効率よく食品にあて、表面に膜を作り水分の蒸散を防ぎながら急速に凍結する「衝突噴流方式」を加えることで、凍結(冷却時間)を1/2~2/3に短縮したストレート型連続式急速凍結装置「Thermo-Jack Freezer」などを展示していた。食材を搬送するコンベアには食品機械用グリースが封入された軸受が用いられるか、仕様によっては半割の無潤滑樹脂軸受などが使用される。冷却空気を循環させるファンは、食品が搬送されるコンベアの上に配置されるものの、極低温下での高速回転が求められることから、無給油の軸受が検討、磁気軸受を採用するケースもあるという。前川製作所「Thermo-Jack Freezer」
サタケの、多彩なセンサで機械の稼働状態をモニターできる製粉機「HS Rollermill」では、粉砕ロールの両端の軸受に集中給油装置によって適量の食品機械用グリースが給脂される。しかし、同社の主力製品である精米機では、米が洗われて食される性質から、かつては食品機械用潤滑剤を使用するという認識は少なく、比較的近年になってから採用され始めたそうだ。サタケ「HS Rollermill」
食品加工では離型油も使われる
食品機械用潤滑油剤の規格としては、食品が付着するのを防止するために、接触する硬い表面に使用できる離型油の規格「NSF 3H」というものもある。食品加工には、製パン機のように捏ねて成形する際に生地がくっつかないようにしたり、どら焼きのように銅板の上で押圧して焼く際に焦げ付かないようにする工程がいくつもあるためだ。
たとえばマスダックの「全自動どら焼き機」は、コンベアで送られる焼成部の銅板の上に皮の生地を落として下から焼き、さらに上からも赤外線ヒーターで効率的に焼くことができる機械だが、どら焼きと接する焼成部の銅板にはNSF 3H規格登録品の離型油がリューベ製などの給油装置で供給。毛細管現象で銅板表面に離型のための油膜を形成している。マスダック「全自動どら焼き機」の銅板にはNSF 3H離型油が給油
駆動部を分離する
駆動部がプロダクトゾーンから分離される機構も採り入れられている。ソディックの「麺帯連続圧延切出機DDMシリーズ」では、ダイレクトドライブ(DDM) 方式により、ロール・切刃回転軸に中空軸モータが直結。雄、雌ロールのかみ合いギヤは、装置下部に設けたオイルバス密封パッケージで潤滑されるため、グリースレスで、歯の減りや摩耗粉の発生、混入の心配もないという。オイルバスは下部に隔離してあるため一般のギヤ油が使用されている。
水環境下での潤滑をいかに確保するか?
食品機械は製パン機など水を噴霧する機構が多く、また作業後の洗浄工程が不可欠のため、水環境下での潤滑をいかに確保するかは大きな課題だ。
これに対し、BPジャパン カストロールインダストリアル事業本部では、水に流されにくいPAOを基油としたNSF H1登録の合成系チェーンオイル「オプチレブCH」を紹介したが、潤滑剤を用いずに材料の自己潤滑性や耐摩耗性を利用したアプローチもある。
イグスでは、自己潤滑性があり耐摩耗性がある材質のすべり軸受「イグリデュール」や球面ベアリング(イグボール)、リニアガイド(ドライリン)といった高性能ベアリングや、ケーブル保護管「エナジーチェーン」などを組み合わせて、水中において無潤滑にメンテナンスフリーで稼働できるデモ機を展示。腐食対策や潤滑管理が要らず安全に使用できることをアピールした。イグス 水中で無潤滑・メンテナンスフリーで稼働できるポリマー製品で構成したデモ機
今回の展示会をのぞいて感じたことは、食品機械における潤滑技術の適用はまだまだ模索の途上にあるということだ。潤滑油剤メーカーや材料メーカー、機械要素メーカー、食品機械メーカー、食品加工業者などが一体となって生産性が高く、安全衛生が徹底的に確保された、食品機械に最適な潤滑手法が確立されることを期待したい。
第161回~第170回
第161回~第170回第161回 メガソーラーの効率を向上する材料・表面改質技術
第161回 メガソーラーの効率を向上する材料・表面改質技術 日立製作所などは来年夏の稼働をめどに、宮城県石巻市の男鹿半島に、国内最大級となる出力10MW級の大規模太陽光発電所(メガソーラー)を建設する計画を発表した。トヨタ自動車でもまた、子会社の工場がある宮城県大衡村で10~20MW級のメガソーラーの建設を予定している。本年7月から、太陽光などの自然エネルギーを電力会社が固定価格で買い取る「全量買取制度」が始まるが、メガソーラーで発電した電力は同制度を利用して東北電力に売られる予定だ。
メガソーラーで使用されている機械要素技術
一般家庭の屋根や屋上などに取り付けられる太陽光発電は通常、2kW~4kW程度の発電能力を持つが、これに対してメガソーラーは電気事業者が進める大規模な太陽光発電で、1ヵ所で1MW以上の発電能力を持つ発電所を言う。国内でも、東日本大震災に伴う電力危機を受けて、また、今後の全量買取制度をにらんで、ソフトバンクなども原子力発電代替のエネルギー確保を目的にメガソーラーの設置を提案している。
追尾型集光太陽電池モジュール メガソーラーでは大規模な太陽電池モジュールを数十基並べて集光するが、太陽の移動に合わせてパネルの角度を自動調整する追尾システムを備えている。1 軸追尾システムは、太陽電池モジュールを傾斜角30°で追尾架台に設置し、あらかじめインストールされたプログラムに従って日の出から日没まで太陽を追尾するシステムで、集光2軸追尾システムは、モジュール受光面が太陽に対して常に垂直になるように、方位角と傾斜角を変化させる追尾システム。ベアリングの技術を応用して大同メタル工業が、ロボットの変減速機やモーターなどの技術を応用してナブテスコなどが手掛けている。
野ざらしの状態でこの追尾システムを長期にわたり稼働させるには、追尾するための可動部分は低温から高温までの潤滑に対応する固体潤滑剤などで常に動ける状態にしている。あるいはベアリング部分などに摺動性の高い樹脂材料などを使って無潤滑での稼働を可能にしている。パネルを太陽に対して常に最適な向きに保つことで、20~40%の発電量の向上が期待できるという。
発電効率を高める材料・表面改質技術
また、メガソーラーはできるだけ日照時間が稼げる場所に設置されることから、太陽光パネルは常時、砂や埃にさらされる。太陽光パネルに付着した汚れにより、こちらは20%もの発電効率低下を招くことがあるという。これに対し、機能性コーティング剤の開発ベンチャーであるジャパンナノコートでは、帯電防止による汚れ防止と低屈折入射により発電効率を高める太陽光パネル用コーティング剤を開発している。
太陽光パネルは、光が当たると発電する太陽電池と、太陽電池を覆うカバーガラスで構成されているが、カバーガラスには汚れ付着対策とカバーガラス自体の入射効率の向上という二つの課題がある。カバーガラスの上に汚れが付着し積層すると太陽光が遮られ、発電効率が大きく低下する。日照時間が多いことから中東などの砂漠地帯でマスダール計画などメガソーラープロジェクトが進められているが、風で飛ばされて帯電した細かな砂がパネルに付着、毎日の清掃を欠かすと20%も発電効率が低下するとの報告がなされており、ガラス表面の帯電防止機能をいかに高めるかが課題となっている。また、フローガラスなど一見透明に見えるガラスだが、反射率が12%ほどあることからエネルギーロスが発生しており、反射を抑えていかに入射率を高めるかも課題となっている。
開発された太陽光パネル用コーティング剤は、10nm以下の複数のシリカ粒子と2nmの酸化スズと溶媒としてのエタノール、水などからなり、無機100%のシリカバインダーが持つ高透明、常温硬化乾燥性、強密着性、高耐候性、超親水性といった特性に、帯電防止による汚れ防止機能と低屈折機能を加えたものとなっている。同品を3㎜のフロートガラスに塗布すると低屈折効果によって可視光の透過率が5%以上アップする。これにより、中国や台湾のパネルメーカーの実験では、発電量が2.2~3.4%アップしたとの結果が得られた。
帯電防止に関しては108オームの表面抵抗値(ガラスの場合1011~1012オーム)を示し、砂や埃の付着を大幅に減少させる。また密着性は0.4μmのアルミナ微粒子による2000回転ポリッシャーによる10分研磨やクルマのゴム洗車機を10回通しても剥離しない耐久性を持つ。
DLCコーティングを施したドクター(ゴム)ロール こうした太陽光パネル用コーティング剤を均一な薄膜に塗布するために、都ローラー工業は平滑な常温ダイヤモンドライクカーボン(DLC)コーティングを施したドクターロール(ゴムロール)を持つナノコーターを開発している。このドクターロールによって太陽光パネルのガラスに塗布されたコーティング剤は、最も発電効率の良好な膜厚80~90nmに成膜され、光透過度は8%アップの94%程度に向上している。
電力供給がいまだ安定せず、また今夏から全量買取制度が始まる日本は、海外勢が注目する太陽光発電市場でもある。パネル生産世界シェア6位のカナダのカナディアン・ソーラーでは、2013年に東北地方で15万kW規模の太陽光パネル工場を稼働させる計画を進めている。海外勢も含めた国内メガソーラー市場で低コスト化を売りに参入する海外勢に対抗するには、上述のような材料・表面改質技術など我が国の誇る技術を適用し、発電効率を最大限に高めつつ、長期メンテナンスフリーなど信頼性向上を図ることが、ますます必要となってきている。
第162回 自動車部品のボリュームゾーン攻略で求められる材料・設計技術
第162回 自動車部品のボリュームゾーン攻略で求められる材料・設計技術 高密封性ハブユニット軸受(日本精工)日本自動車部品工業会では先ごろ、2010年現在での会員企業を対象に海外生産に関する調査を実施、2010年の海外の生産法人数は2009年に比べ47社増(2.9%増)の1645社となり、2年連続で前年を上回った。1645社のうち中国を筆頭にアジアが65%(1068社)を、北米が16%(268社)を、欧州が11%(182社)を占めた。部品メーカーの中国を中心とした海外シフトが加速している状況が浮き彫りになった。部品メーカーの中国シフトはもちろん、一昔前のようにローコスト生産を目的としたものではなく、自動車メーカーと同様、現地での需要獲得を狙ったものだ。
新興国での使用を想定した製品・要素技術の開発を
景気が減速したとはいえ、中国の2011年の自動車販売台数は1850 万台にのぼり、3年連続で世界一を記録している。日本の産業界ではこれまで、先進国向けを中心として高機能・高品質で高収益が得られるハイエンド商品を供給してきたが、中国を中心とするボリュームゾーンを攻略するには、コモディティ化したミドルレンジおよびローエンド商品で世界と戦わなくてはならない。ローエンド商品は価格を重視したもので、ミドルレンジ商品は価格と性能のバランスが求められる。ハイエンド商品を手掛けてきた我が国がローエンド商品で戦っても勝ち目はない。価格と性能をバランスさせたミドルレンジで一定の利益を確保しながら、量を追求すべきであろう。そこではもちろん、既存のハイエンド商品の単純な型落ちや機能省略による低価格化では現地ニーズに対応できず、需要を獲得できない。そこで新興国での使用環境を考慮した製品開発が進んできている。
高密封性ハブユニット軸受の構造(日本精工) 日本精工では、新興国に多く見られる未舗装路や冠水路、あるいは寒冷地域での積雪路など、泥、砂利、水という過酷な環境に曝されるハブユニット軸受において、高い信頼性と摩擦損失の低減を両立した「高密封性ハブユニット軸受」を開発した。ハブユニット軸受は車輪の中心にあって車体を支える重要な基幹部品のため、非常に高い信頼性が求められる。また、CO2排出量削減要求やガソリン価格高騰からクルマでは燃費改善が急務で、対応策の一つとしてエンジンからタイヤまでの全ての回転部分の摩擦(フリクション)を低減し、走行抵抗を低減することが求められている。外部からの異物混入を防止する手段としては、軸受の車体内側と車体外側にシールを装着することが広く用いられているが、シールの摩擦によるフリクションが課題となっていた。軸受の車体内側に金属性のキャップを嵌合する形式も用いられているが、十分な密封性を確保することが困難で、また車輪速センサと磁気エンコーダの間に金属性のキャップが介在することで、正確な車輪速の測定が困難になっていた。これに対し日本精工では、ゴムを加硫接着した非磁性体の金属キャップを新開発し、高い密封性による信頼性確保と低摩擦損失を両立させた「高密封性ハブユニット軸受」を開発した。
また、NTNが開発した「過酷環境対応ハブベアリング」は、荷重・衝撃、泥水、低温フレッティングという3つの課題に着目した。荷重・衝撃には、ハブベアリングの内部設計を最適化したことで、軌道面の圧痕深さを従来の1/4に低減、耐荷重性能を向上させた。また、耐泥水にはシールのハブベアリング接触部形状を最適化し、泥水浸入を低減、耐泥水寿命を2倍以上に伸ばした。さらに、車を販売店へ届ける手段として、貨車による長距離輸送が増加、特に寒冷地では貨車走行時のレール間継ぎ目から発生する振動がハブベアリングの軌道面にフレッティング摩耗を発生させることがあったが、特殊グリースの採用により金属接触を防止し、特に低温時の耐フレッティング摩耗を従来の1/10以下に向上させた。密封設計に加えて、潤滑性能の向上で過酷環境でのベアリングの耐久性を高めている。
課題は現地での材料・設計技術
繰り返すが、ミドルレンジ商品は価格と性能のバランスが求められる。つまり、上述のような現地の使用条件を考慮した製品を、コストを抑え開発し供給しなくてはならない。
「現地・現物・現人」を掲げるNTNでは、早くから現地の軸受鋼を調査、「中国製の材料も日本製と同等の寿命を実現し始めている」(『日経Automotive Technology』2010年11月号、p.58)としつつも、すべての軸受鋼で安定した品質・清浄度を得られるわけではないことを踏まえ、“汎用材料を使いながらいかに要求する軸受機能を発揮できるものにするかが、今後の軸受メーカーの材料技術者の使命で、材料、熱処理・加工・粉体技術・コーティングなどの表面改質、潤滑技術などの要素技術の高度化や、個々の技術の複合化・コラボレーションが従来以上に重要” (NTN TECHNICAL REVIEW No.76(2008))と述べている。
特に中国市場を見ると、将来的にはボリュームゾーンが富裕層市場へと移行する兆候がうかがえる。その局面では、日本企業が培ってきたハイエンド商品分野での強みが生かされる場面も増えてくるであろう。しかし、そのときになってもまだ、現地において日本と同等のハイエンド向けの材料が安定的に入手できるとは限らない。新興国でのミドルレンジからハイエンドへの市場移行を見据えて、材料技術をカバーする表面改質技術、ハブベアリングに見たような密封技術など設計技術を含むトータルなアプローチが、ますます求められている。
第163回 300系のぞみ引退 高速化で安全な輸送を支える軸受技術
第163回 300系のぞみ引退 高速化で安全な輸送を支える軸受技術 初代「のぞみ」として知られる東海道・山陽新幹線「300系」と、初の2階建て車両である山陽新幹線「100系」が3月16日に最終運行を迎えた。約600人の鉄道ファンが博多駅、岡山駅にそれぞれ集まり、引退を惜しんだ。300系は1992年に東海道区間で走り始め、翌年から山陽区間に乗り入れた。最高時速はそれまでより50㎞速い270㎞で、東京―新大阪間を0系「ひかり」より19分短い2時間半で結んだ。
高速化を支える新幹線の車軸軸受
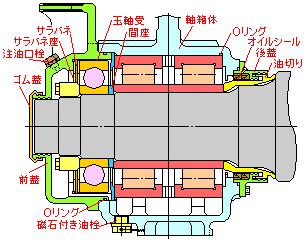
新幹線の高速化を支える車軸軸受には、車両重量による静的および動的なラジアル荷重がかかるほか、軸方向に間欠的にアキシアル荷重、つまりスラスト力がかかる。1964年に営業開始した0系新幹線「ひかり」では、ラジアル荷重を円筒ころ軸受で受け、スラスト力を深溝玉軸受で受け、さらにスラスト力を緩衝させるため、緩衝ゴムや皿ばねが用いられた。また、当時の在来線の車軸軸受で一般的だった封入グリースによる潤滑に代えて、タービン油による油浴潤滑方式を採用することなどで、当時の世界最高時速220kmを達成した。
つば付き複列円筒ころ軸受 その後1979年代になると、車軸方向のアキシアル荷重(スラスト力)を内外輪のつばで受ける「つば付き円筒ころ軸受」が在来線車両で採用された。しかし、つばでスラスト力を受けるこの軸受は、負荷容量の点から高速域で問題があると思われていたのだが、つばの角度やころ端面の曲率、それらを高精度に実現する加工技術などにより、1992年に営業運転を開始した300系のぞみに採用になった。つば付き円筒ころ軸受の採用により、玉軸受に比べて長さを短縮し、省スペース化、アルミ合金軸箱と合わせての軽量化に貢献、時速270㎞を達成したのである。
密封複列円すいころ軸受 この300系での省スペース化、軽量化を図る軸受設計はその後、1997年の500系での複列円すいころ軸受採用によるコンパクト設計に受け継がれた。円すいころ軸受はラジアル荷重と同時にアキシアル荷重に対する負荷容量が大きい。アキシアルすき間を小さくできるため、走行安定性にも優れる。この複列円すいころ軸受をグリース密封型とすることでメンテナンスフリーにし、また、それまでの油浴潤滑方式に比べ軸箱を小さくし、より軽量化を図った。これにより時速285㎞での営業運転を実現した。
さらなる高速化と安全性向上のため、軸受など要素技術の開発を
2007年にデビューした最新のN700系では、時速300㎞とより高速で乗り心地が向上したほか、従来の車両に比べ19%も少ない電力で走るが、この実現につなげる軸受設計としては複列円すいころ軸受でグリースを密封するオイルシールのリップ部(摺動部)の高速下での発熱を抑えるため、軽接触タイプとした。また、樹脂製保持器を採用して従来の金属摩耗粉による潤滑剤劣化を抑制している。さらなる安全設計としては、軸受の状態監視を目的としたセンサー付軸受も開発、従来の温度計測に加え振動を計測でき、早期の異常検知につなげている。
このように、コンパクト・軽量化による大幅な高速化と安全設計を確立した300系を機に、新幹線は世界に誇る高速車両としての地位と安全神話を築いた。その高信頼性の高速走行を支える基盤技術としては、上述した車軸用軸受だけでなく、動力を発生させるモータ用の主電動機用軸受、モータの出力を車軸に伝える駆動装置用の軸受などが使われ、さらにそれら軸受技術でもシール技術や潤滑技術、表面改質技術などの要素技術が支えている。
主電動機用軸受では、電動機内を流れる電流により転動体と軌道面接触部が溶融する電食を防ぐため、外輪にPPS(ポリフェニレンサルファイド)樹脂やセラミックなど絶縁物の被膜を施す絶縁対策がとられている。また、駆動装置には小歯車と大歯車があり、特に小歯車軸受では車両走行時の振動の影響を受け、保持器各部に繰り返し速度が速い様々な応力が発生するため、保持器表面に軟窒化処理を施し耐摩耗性と疲労強度を向上させる手法などがとられている。
300系のぞみの20年にわたる安全で高速な輸送をねぎらいつつ、さらなる高速化に向けても、大量輸送の信頼性を確保する、軸受など要素技術開発のより一層の進展と蓄積に期待したい。
第164回 中小企業の技術が支えるわが国のものづくり
第164回 中小企業の技術が支えるわが国のものづくり りそな中小企業振興財団と日刊工業新聞は先ごろ、「第24回中小企業優秀新技術・新製品賞」を決定、4月11日に東京都千代田区のホテルグランドパレスで、世界に誇る中小企業の製品・技術39件が表彰された。
同賞は、中小企業が開発する優れた技術や新製品を表彰することにより、わが国中小企業の技術振興を図り、産業の発展に貢献することを目的として実施しているもの。表面改質およびその評価技術関連では以下のとおりの受賞となった。
・熊防メタル「超硬質アルマイト イーマイトUH処理」…アルミ材料の表面硬度を高めるアルマイト処理において、従来処理がビッカースHV300~400HVだったのに対して、独自開発の処理液では、1.5倍以上の600HVを実現、鋼相当の耐摩耗性に加え耐食性を実現している。基材を鋼からアルミに置き換えて同処理を施すことで、機械的強度を保持しつつ重量を1/3抑えられるため、軽量化による燃費向上を目指す自動車部品に最適という。
・魁半導体「大面積大気圧プラズマ装置「SKlp-CBL300」」…同プラズマ装置は大気圧プラズマでは世界最大級となる30㎝核でのプラズマ発生を可能にした。自動車ガラスに使われるポリカーボネートの前処理では1秒間で10㎝のスピードで送ることができる。フロントガラスサイズに合わせて、発生面積が1.1×1.4mサイズの本格量産機の開発も進めているという。
・パルメソ「新しい材料表面強度評価のMSE試験装置」…同装置は、水と1μmのセラミックス微粒子をスラリー状に混合、圧縮空気を使って毎秒100mの速度で試料表面に噴射して同微粒子の摩耗度合いを計測し、摩耗率という尺度で評価する。マイクロスラリージェットというある種のブラスト処理を応用して試験評価技術を構築したもの。硬質薄膜材料の表面強さを評価する。たとえばダイヤモンドライクカーボン(DLC)などの硬質膜やセラミックス材料、金属・樹脂材料の表面強度評価を20nm単位で行えるため、基材の影響を受けずに薄膜そのものの評価が可能という。
第24回「中小企業優秀新技術賞・新製品賞」贈賞式で来賓の挨拶を行った経済産業省 中小企業庁・鈴木正徳長官は、「今回受賞した技術は独創性や新規性の面で類を見ない技術。昨年の東日本大震災で実用化されていればと惜しみつつ、わが国発の世界に冠たる技術として誇りに思う」と述べた。
折しも中小企業庁では、「“日本の未来”応援会議~小さな企業が日本を変える~(略称:“ちいさな企業”未来会議)」を設置、30数ヵ所に及ぶ地方会議の開催を進めている。わが国企業の9割を占め、製造業、商業などわが国経済を支える中小企業が、内需減少、新興国との競争、震災・円高など厳しい環境の中で、いかにその潜在力・底力を発揮し、もう一度元気になることができるかは国民的課題であるとし、次代を担う青年層や女性層の中小企業経営者を中心に、中小企業団体、税理士などの士業、商店街関係者、生業、地域金融機関など、幅広い主体の参加の下、中小企業の経営力・活力の向上に向けた議論を行う。
我が国からのインフラ輸出などで前線に立つ大企業の名が報じられることは多いが、実際には航空宇宙や新エネルギー、医療福祉などのビジネス化において、中小企業の技術が土台を支えているところは大きい。わが国企業の9割を占める中小企業の技術が今回のような表彰を機に日の目を見て、当面の課題である東日本大震災の復興や放射線の除染、さらには技術立国を支える国際競争力の高い技術として実用化され、社会に貢献していくことを願う。
第165回 インターモールド2012開催、国際競争力を高める金型技術
第165回 インターモールド2012開催、国際競争力を高める金型技術 「インターモールド2012(第23回金型加工技術展)」が4月18日~21日、大阪市住之江区のインテックス大阪で開催された。「金型展2012」と「金属プレス加工技術2012」が同時開催され、45,075人が来場、306社・団体が、ものづくりの高品質化や高精度化に不可欠な金型関連の最新技術を披露した。
高速・高精度な切削加工による金型製作が行われるようになって久しいが、さらなる高精度化による加工面品位の向上と生産性向上によるコスト競争力向上を図る加工機と切削工具の技術開発が進んでいる。
工作機械の出展として、オークマは高精度金型加工用の立型マシニングセンタ(mp-46V)を展示した。機械の立ち上げ時や加工再開時などのテーブルの熱膨張による寸法変化を制御、テーブル全域で5μmに抑えることで、熱変位を安定させるための暖機運転を短縮するとともに、ワークをテーブルのどこに設置しても安定した寸法精度を実現している。20000回転、30000回転の高速主軸で主軸・工具の温度上昇を回転軸冷却システムで低く抑え、熱変位を低減している。
切削加工では、タンガロイが、金型の彫りこみ加工で高い加工能率を持つ超高送りカッタ(DoFeedドゥーフィード)を出展した。インサート材種には表面の摩擦係数を低下させるとともに、ミクロな応力集中を軽減し、工具材料の性能を大幅に向上させる表面平滑化技術を採用した。この表面改質技術により長寿命化を図った3材種の組み合わせによって多種多様な金型材で超高送りを実現、曲線切れ刃と大きなすくい角により低抵抗化した両面4コーナ仕様インサートと多刃仕様ボディの組み合わせによって、従来よりも30%以上高い加工能率を実現し生産性向上につなげている。
こうした金型の切削加工と併せて、各種金型の耐久性を高める表面改質技術も紹介された。
清水電設工業( http://www.seavac.co.jp )では、高硬度、高耐熱性、高潤滑性のPVDコーティング「ZERO-Iゼロワンコーティング」を紹介、優れた耐摩耗性による金型の長寿命化を提唱した。自動車業界では、高張力鋼板(ハイテン材)や厚板化など、過酷な状況下での金型の使用が進み皮膜の剥離を誘発させる局所的弾性変形の抑制が課題だが、その課題をクリアするとともにTiCN、TiAlNを凌ぐHv3500という高硬度化を実現した。また耐熱温度では、TiAlNを超える1100℃を実現。焼付きの原因となる冷間鍛造での摩擦熱による酸化や温間鍛造にも対応した。
ナノコート・ティーエス( http://www.nanocoat-ts.com/ )は、耐摩耗性や耐食性、離型性などの機能に優れた「プラスチック・ゴム成形金型用セルテスコーティング」を紹介した。クロム系、DLC系、チタン系の膜種を用意、プラスチック・ゴム成形金型の生産性向上に対応する。耐摩耗性に優れた膜種では、射出成形においてガラス繊維などによるアブレシブ摩耗を低減し寿命を向上させるとともに500℃までの高温酸化防止性能によりガス焼けによる母材の損傷を防ぐ。また金型の離型性・型汚れに適した膜種では、金型洗浄や除去の保守頻度を低減するほか、型離れが良好なことから自動運転を可能にしている。
電気、材料、輸送費、法人税率など、アジア諸外国に比べコスト高なわが国の金型産業では、ユーザーの海外進出が止まらず、海外調達に歯止めがかからない状況にある。しかし、こうした金型の高精度加工技術や表面改質技術による長寿命化などによって、基板技術である金型の国際競争力を高めることで収益の増大を図り、ひいてはわが国のものづくり産業の発展につなげてほしい。
第166回 熱海のトラック事故に、ブレーキ技術の活かし方を考える
第166回 熱海のトラック事故に、ブレーキ技術の活かし方を考える 静岡県熱海市で5月14日に4tトラックが暴走して路線バスの乗客らが重軽傷を負った事故で、熱海署は自動車運転過失傷害の疑いで、トラックを運転していた会社員を逮捕した。熱海市上宿町の下り坂が4㎞も続く県道で、2.9tの積載荷重のトラックをコンクリートブロックや小型重機など約6tの貨物を積んで運転、運転手は補助ブレーキを使わずにフットブレーキをかけ続けたため、トラックが制御不能となった。これにより路線バスや軽乗用車など計4台を巻き込んだ衝突事故を起こし、運転者はバスの乗客ら計7人に重軽傷を負わせた容疑で逮捕された。
ドラムブレーキイメージ図:いすゞ自動車提供 さて、取り扱いを誤ったブレーキは、国内の中型・大型トラックに多く採用されるドラム式ブレーキ。この大型・中型トラックの作動方式としては、空気圧式や空気油圧複合式が多く採用される。トラックの場合はトラック車重以上の積載荷重で走行する場合もあり、ドライバーの脚力で油圧をかけるだけ制動できないため、ブレーキペダルによって圧縮エアーを操作、エアー圧で油圧をかけて制動を行う。
ドラムブレーキは低速域では優れた制動力を発揮、ディスクブレーキのパッドに比べ、摩擦材のライニング寿命が長いという長所があるものの、今回のように頻繁にブレーキ操作を行うとフェード(ブレーキの使用頻度が増えるとライニングの温度が上昇し、ブレーキペダルの踏み込みに対して制動力が低下する現象)が発生し、制動力が低下するという課題がある。
排気ブレーキイメージ図:いすゞ自動車提供 つまり、今回の事故で熟練のトラック運転手が取材に答えているように、補助ブレーキである排気ブレーキを利用して、フットブレーキの多用を避けるべきだった。排気ブレーキは、排気管内に設けたシャッターバルブを閉じてエンジン内の排気圧力を高めることで、約1.8倍という強力なエンジンブレーキ力を発生させる。制動力はそれほど強くないが、緩い勾配の下り坂なら十分に効果が得られるという。ところが「積載荷重が大きいほど下り坂では制動しにくいため、ブレーキを踏みがちになった」(日本自動車連盟)ために、排気ブレーキのシャッターバルブを作動させる圧縮タンクの空気圧が通常8kgfに対して5kgf程度しかなく、排気ブレーキの制動力も低下していたと見られる。本来補助ブレーキには、ドラムブレーキのライニング摩耗を低減し、フェードを防止する効果もあるのだが、この補助ブレーキも制動力を失っていたわけである。
ドラムブレーキのブレーキシューは半円弧状で、表面にライニング(摩擦材)が貼られている。このライニングには、適度な摩擦係数、耐摩耗性、耐フェード性、ドラムを摩耗させない低い相手攻撃性などが必要で、これら特性がブレーキ性能に大きく影響を及ぼす。これら特性をバランスよく担う材料として長年アスベスト(石綿)が使われてきたが、近年は石綿規制から、日本ではアラミドパルプ・ベースのノンアスベストライニング(NAO)が主流となっている。
NAOはアラミドパルプや鋼繊維、セラミック繊維などの摩擦材に添加物とともにフェノール系樹脂を結合剤として加えて加熱成型したもので、世界市場でも採用が進んでいるノンアスベスト材だ。しかしながら、熱分解温度がアスベストで600℃以上なのに対して、アラミドパルプでは400℃強で、結合剤のフェノール樹脂では350℃程度と比較的低い。つまり昔に比べると、フットペダルを多用することでの摩擦材の耐久性が低下しているのは否定できない。NAOの課題はまさに、ブレーキ高温時の性能や摩耗、高温時の圧縮変形と言われている。
しかしプロのドライバーとしては、いずれも知っていなくてはならない事柄だった。ノンアスベスト摩擦材が積載荷重超過でのフットブレーキの異常な多用による温度上昇に耐えないかもしれないことは別にしても、下り坂の通行で積載荷重の超過が危険であること、下り坂では補助ブレーキを利用すべきであること、フットブレーキの極度の多用は補助ブレーキの機能をも損なうことは知っておくべきだった。長々と説明してきた摩擦材とドラムブレーキ、さらに補助ブレーキとしての排気ブレーキなどの技術は、どれもわが国が世界に誇る技術である。今回の事故は機械技術や制御技術に起因するものではない。明らかに人為的なものである。関越自動車道で47人の死傷者を出した高速ツアーバスでもそうだが、適正な人材の登用も含め無理のない運行計画を立てて事故を減らすこと、この当たり前のことが守られていなかった。
ブレーキは輸送機器の安全性を支える重要保安部品であり、その使命のもとに技術者たちは、高速・高出力化などの過酷な使用条件に耐えつつ環境規制などもクリアすべく、苦心して技術開発に努めてきた。それは、実際の使用条件の数倍の耐久性をもたせるという安全値を備えた設計で、誤った適用さえしなければ快適で安全な走行を可能にするはずの技術なのである。蓄積した技術を今回のようにだめにするのでなく、技術を活かして円滑な業務の遂行と何より安全性の確保につなげる人材の教育・育成について、今一度考える必要がありそうだ。
第167回 くるまの環境・安全・快適性を支える表面改質技術
第167回 くるまの環境・安全・快適性を支える表面改質技術 自動車技術会は5月23日~25日、横浜市西区のパシフィコ横浜で「2012年春季大会」を開催、「学術講演会」では81セッション・370件の講演発表が行われ、第21回目を迎えた自動車技術展・EV展「人とくるまのテクノロジー展2012」では、400社・914小間で製品・技術の展示が行われた。学術講演会、展示会ともに、表面改質関連のテーマが多数発表された。
春季大会論文賞に4WD車へのWCとDLCのナノ多層膜技術
春季大会では「第62回自動車技術会賞」の発表があり、表面改質関連では今回、ジェイテクト・安藤淳二氏らによる「遊星歯車式トルク感応型 LSD(リミテッド・スリップ・ディファレンシャル=差動制限装置)の摩擦挙動に及ぼす粗さとコーティングの影響」が論文賞を受賞した。高い静粛性と安全性を要求される4WD車で、歯車式トルク感応型LSDの適用拡大に必要不可欠な自励振動の抑制に関する独創的な技術。車両の走行状態によって、歯車式トルク感応型LSD内部では、摩擦しながら歯車を差動回転させる必要があり、摺動部のスティックスリップを抑制しつつ、スムーズに摩擦させねばならない。このため本技術では、混合潤滑下での摩擦挙動(μ-v特性)の理論計算により最適化された摺動面の微細粗さと、WC(タングステンカーバイド)とDLC(ダイヤモンドライクカーボン)のナノ多層膜を採用することで、制振性と耐焼付き性、耐摩耗性を両立した。これにより車両の自励振動の抑制を実現し、パワーを確実に4輪に伝達できることが、今回評価された。
「学術講演会」では、日産自動車・片山拓也氏らによる「DLC対応GF-5 0W-20省燃費エンジン油の開発」や、トーカロ・砂原亮介氏らによる「プレス金型用コーティング皮膜の摺動損傷と動摩擦特性」などの発表があった。
自動車に必要とされる表面改質技術が多数展示
「人とくるまのテクノロジー展」では、環境技術や安心・安全技術、快適・利便(通信)技術の三つの分野で人・くるま・社会をつなぐスマート技術を中心に、完成車、部品、材料、試験計測機器などの製品・技術が出展され、表面改質関連では以下のような展示があった。
不二WPCのブース 不二WPCでは、低燃費車に必要な部品のダウンサイジングとフリクション低減について、ダウンサイジング化した部品に対して微粒子の高速衝突により耐久性を向上させるWPC処理と、さらなるフリクション低減と耐摩耗性向上を図るDLCコーティングの複合処理を提示した。
丸紅情報システムズのブース DLCコーティングではまた、先ごろ受託加工サービスを開始した丸紅情報システムズが、プリント配線基板(PCB)用超硬ドリルで量産実績のある、ビッカース硬さ6,500の高硬度水素フリーDLCを出展し、100℃以下の低温でコーティング処理できるため母材の変形や変質を抑えることができる上、価格も2~3割程度安価に提供可能という点を押し出して、自動車摺動部品などでのメリットをアピールした。
スルザーメテコジャパンのブース スルザーメテコジャパンでは、自動車軽量化のための部品の耐久性向上を図る環境にやさしいドライ処理として、各種の溶射皮膜技術を提示した。セラミック溶射皮膜では、電気自動車(EV)などで多用されるモーターの軸受などで絶縁皮膜を形成し電気腐食(電食)を防止するという。展示では、スイスのスルザーメテコ社で受託加工を行っている「SUME Bore」溶射技術を紹介。同技術は欧州で乗用車、トラックなどのガソリンおよびディーゼルエンジンなどでフリクションの低減や放熱性、耐摩耗性などに優れた溶射技術として普及しているという。今回はサンプルとしてヤマハ発動機の船舶用エンジンの展示を行った。さらに欧州で実績のあるメタプラスのPVD/DLCコーティング装置の提案を行った。
NOFメタルコーティングスのブース NOFメタルコーティングスでは、自動車のボルトやナット、ホースクリップ、シャーシ周りなどで実績のある防錆処理技術「ジオメット」を紹介。完全クロムフリーでありながら高い耐食性を有しており、加えてアルミニウムとの電食防止効果があることなどをPRした。フランスパビリオンでは、H.E.Fグループがガス軟窒化よりも環境にやさしいという液体軟窒化処理による自動車部品の耐摩耗性、耐焼付性、耐食性、疲労強度向上などについて提案した。
今回もEVやハイブリッド車(HEV)とその関連部品・材料の出展が目立ったが、エネルギー需給の厳しい中、依然として主流の内燃機関車での燃費向上は喫緊の課題となっており、たとえばスズキでは、JC08モードで30.2km/Lという低燃費を実現した軽乗用車「アルト エコ」を展示した。ピストンスカート波状のパターンに加工された樹脂コーティングでは、樹脂皮膜のない部分が10μm低いためシリンダに接触しない分、摩擦抵抗を低減しているほか、3本のピストンリングのうちトップリングとオイルリングにDLCコーティングを処理し油膜が形成されにくいアイドリングストップからの再始動時などで摩擦抵抗を減らした。
EVでも、モーターの軸受などで予想される電食対策でも、上述のセラミックス溶射皮膜など、要求される機能を付与する表面改質技術の活躍する場面は多いだろう。ますます進展するグローバル化の中で、コスト競争力の向上には廉価な材料を使いながら表面の特性を向上する必要性も増してくると思われる。今回の主要テーマである自動車の環境・安全・快適性を高める上で、表面改質技術の重要性はますます高まってきている。
第168回 機械要素技術展に見る、求められるモーションテクノロジーと材料・表面改質技術
第168回 機械要素技術展に見る、求められるモーションテクノロジーと材料・表面改質技術 ベアリングや直動案内、ねじ、ばねなどの機械要素や、金属や樹脂などの材料・加工技術や表面処理・改質技術に関する専門技術展「機械要素技術展(M-Tech)2012」が6月20日~22日、東京・有明の東京ビッグサイトで開催された。最新の製品技術を通して、直動案内などのモーションテクノロジーや材料・表面改質技術に対するニーズの傾向がうかがえた。
ベアリング・直動案内で新興国勢が示す過剰品質の見直し
エネルギー不足の中、省エネにつながる各種機械のベアリングの摩擦ロスの低減が求められている。これに対して、イグスは内外輪に自己潤滑性ポリマーを用いたポリマーボールベアリングを、オイレス工業では、水関連ビジネスでも使える水中・海水中での低摩擦を実現する固体潤滑剤埋込型軸受を展示した。
工作機械や半導体・FPD製造装置などの直線運動を支える直動案内では、THKや日本トムソン、日本ベアリングなどがボールリテーナや潤滑部品などの装着により、高精度で低フリクション、長期メンテナンスフリーを実現する製品などを出展した。
こうした中、中国や台湾など新興国からのベアリング製品・直動案内製品の出展も多く見られた。
ゴトー・エンタープライズは一般的な鋼製ベアリングからセラミックベアリングまで、低コスト、短納期を実現する中国製ベアリングを紹介した。また、台湾に本社を置くハイウィンは、日本の機械装置で要求の多い精度や音の静かさなどをクリアしながらも、コストメリットや短納期を図る直動案内をアピールした。
少し前、中国の工作機械需要の急増などから日本製の直動案内のデリバリーの遅れが問題になったことがある。その際に取りざたされたのが、直動案内の用途に対して過剰品質の製品が使われている例が多いのでは、ということだった。たとえばアルミの筐体に取り付けるのに、剛性の高い鋼製の、しかも高精度な直動案内が必要かといったことだった。アルミはたわむ上、アルミの筐体が使われる用途で求められる精度はそう高くないというわけだ。中国製や台湾製の直動案内では、そうした過剰品質の見直し気運の中、コストパフォーマンスや安定した供給体制の可能性を提起した。
医療向けなど新分野を目指す材料・表面改質技術
ものづくりの復権を目指し国をあげて医療やエネルギーなど新規産業の創出が進められる中、材料や表面改質技術でもそうした新分野での適用に向けた提案がなされた。
ダイセル・エボニックは最も機械的特性の高いエンジニアリングプラスチックであるポリエーテルエーテルケトン(PEEK)樹脂を展示、その高い機械的強度と生体適合性を生かした人工関節への適用や生体材料の接合部材としての適用を示した。
カソードアークPVD法による水素フリーダイヤモンドライクカーボン(DLC)を展示したビヨンズは、骨腫瘍診断のために生体から骨標本を切り出すガイドピン式経皮骨針にDLC膜をコーティングすることで患者への負担を軽減した器具(静岡県県立がんセンターらと共同研究)を展示した。
キスコは、化学蒸着法(CVD)による人体に安全で信頼性の高い透明なパラキシリレン樹脂コーティングを出展、ステントやカテーテル、内視鏡、手術器具、注射器ガスケットなど医療機器への適用を提案した。
機械要素技術展は、「日本のものづくりワールド2012」のもとで開催された展示会の一つだが、今回の展示からは、新興国とのコスト競争や円高、エネルギー不足など厳しさを増す経済環境下で、生き残りをかけた我が国のものづくりの在り方をあらためて考えさせられたように思う。
第169回 表面改質展2012が開催 日本のものづくりを支える表面改質技術
第169回 表面改質展2012が開催 日本のものづくりを支える表面改質技術表面改質展のもよう 日刊工業新聞社の主催する表面改質展2012が、7月4日~6日の三日間、名古屋市のポートメッセなごやで開催された。同時開催の難加工技術展とからめて、加工工具や金型などの耐久性を向上させる表面改質から、自動車の燃費改善を支える表面改質まで幅広い製品・技術が紹介された。
斎藤氏の講演のもよう また7月5日には、斎藤秀俊氏(長岡技術科学大学 副学長 物質・材料系教授)が「DLC企画化の意義とISO提案の今」と題した特別講演を実施。日本主導でDLCの標準化・規格化を行うことにより誰もが簡単適切にDLCを使えるようになり、我が国のお家芸である品質を世界に売り込むことができる、と標準化・規格化の意義について解説した。今後の行方として、「軟質膜の定義をどうするか」や「我が国の特許が生きる製造方法の標準化に重点を置く」、「DLCを分類する評価法として、24年度中にエリプソメトリー法・色素法の提案をISO/TC107に提案する予定(摩擦摩耗試験の方法は提案済み)」などを示すとともに、会場に集まった200名以上の聴講者に協力の要請を行った。
オーエスジーコーティングサービスのブース 一方、展示会の加工工具向けでは、オーエスジーコーティングサービスが航空機の軽量化を図る材料として採用が進むCFRP(炭素繊維強化プラスチック)など難加工材の高効率な加工を実現する高硬度・長寿命のダイヤモンドコーティングを中心に紹介した。また、ユニオンツールは自社のPCBドリルなどで累計約1000万本の量産実績を持つビッカース硬さ6500HVの高硬度な水素フリーのダイヤモンドライクカーボン(DLC)ULF(ウルフ)コートの受託加工などを提案した。
清水電設工業のブース 金型向けでは、オリエンタルエンヂニアリングが、パルスDCプラズマCVD(PCVD) 法により4000HV以上の硬さを実現、高張力鋼板プレス加工やアルミダイカストの離型剤フリーの可能性があるスーパーボロンコーティング (TiAlSiBCNO系膜)を被覆した金型などを展示した。清水電設工業は、高張力鋼板(ハイテン材)や厚板化など過酷な状況下での使用が進む金型での被膜剥離につながる局所的弾性変形を抑制する高硬度(Hv3500)・高密着のZERO-Iコーティングなどを提案した。松山技研は、金型の耐久性を冷間パンチで30万程度と高めつつDLCコーティングに近い摺動特性(摩擦係数0.1程度)を実現、鍛造金型・プレス金型の絞り、曲げ、抜きに高い効果を発揮するTi系コーティングXシリーズなどを出展した。
東研サーモテックのブース 不二機販は、精密ショットピーニングであるWPC処理により、従来の金属表面の硬度アップだけでなく摺動性の向上、 金属表面への高硬度被膜の形成、高温域での潤滑性が高い被膜形成といった手法を加えて、 熱間鍛造金型や各種切削工具の寿命向上などをアピールした。東研サーモテックでは、ガス浸硫窒化や無酸化焼入れなどの熱処理加工から、タングステンを含有しTiやAl合金などの金属材料との摺動性に適したMe-DLCコーティングや各種PVDコーティングなど、複合的な表面改質処理が行えることを強みとしてPRを行った。
ユケン工業のブース 自動車の燃費向上につながるコーティングとして、ユケン工業は、軽量化から採用の進む樹脂を成形する金型で、離型性や耐食性、耐摩耗性(耐久性)を実現する低温処理イオンプレーティング法によるセラミックス皮膜Yコートを紹介、膜の密着性を高める独自洗浄技術による前処理なども併せて提案した。また、ハウザーテクノコーティングは、 ピストンリングなど自動車部品に対し過酷な使用条件での耐久性や潤滑性を付与し、自動車の燃費改善に貢献するDLCコーティングなどを、密着性良く成膜するPACVD(プラズマアシスト化学真空蒸着)成膜装置FLEXICOATなどを紹介した。
日本スピードショア/ヤマシタワークスのブース こうした表面改質処理の密着性を向上させる下地処理として、たとえば日本スピードショア/ヤマシタワークスは、金型の手磨きが難しい用途でラップ時間を短縮するとともに、コーティングの密着性を向上する鏡面仕上げ装置エアロラップを紹介した。
金型・工具は様々な製品の製造を支える基盤技術であり、表面改質技術は上述のとおり金型や工具の耐久性や生産性を高めている。今回の展示会では、吉川工業が色つきのセラミックス溶射を施すことで耐久性に加え美観向上をアピールしていたが、各種特性を付与して、我が国の製品競争力を高める重要な手法である。だが、その表面改質技術をさらに効果的に使うためには、洗浄技術やWPC処理、研磨を含む下地処理などによる改質膜の強化やその試験・評価技術が必要不可欠だ。グローバル競争の加速する中、それら周辺技術を含む表面改質技術を有効に利用することで、わが国製品のさらなる競争力向上を実現し、工業立国再興の一助となることを願う。
第170回 スマホ市場拡大を支える加工、表面改質、材料技術
第170回 スマホ市場拡大を支える加工、表面改質、材料技術アップル「iPhone4S」 モバイル・コンテンツ・フォーラム(MCF)は先ごろ、2011年1月~12月のモバイル関連市場の調査結果を公表した。スマートフォンのプラットフォーム別データでは、2010年12月時点でiPhoneが378万ユーザー、Androidが217万ユーザーだったのに対して、2011年12月にはそれぞれ、674万ユーザー、1146万ユーザーと急増した。
こうしたスマホ市場の拡大に対応してモバイル・コンテンツ関連市場は2011年、対前年比115%の1兆9061億円となった。このうち、着信音やゲームなどのデジタルコンテンツの有料配信市場「モバイル・コンテンツ市場」は対前年比114%の7345億円、物販(通販)やサービス系(各種興行、交通系チケット販売)、トランザクション系(証券取引、オークションなどの手数料)の「モバイルコマース市場」は対前年比116%の1兆1716億円だった。
こうしたモバイル関連市場の拡大を支えるスマホに製造関連でも、小さく薄いボディに内蔵される各種部品のコンパクト化を実現する工作機械が必要である。現在、電子部品ICチップの世界最小クラスは大きさ0.4mm×0.2mmの「0402サイズ」と呼ばれるもので、このICチップをはじめスマホ部品では微細加工求められる。
たとえば、カバーガラスやタッチパネルに使用されるITO(透明導電膜)ガラス基板などの端面を高速・高精度に研削する装置では、ガラスを加工ステージへ自動供給でき、装置を停止することなく連続的な研削加工が行え、研削時に発生するチッピングを最小に抑えることができるものなどが、中国向けをはじめ堅調な需要を支えている。
また、スマホで直感的に操作出来るタッチパネルでは、デザイン性、透明性、質感、薄型化の要望から、表示部分に強化ガラス製パネルが使用されているが、万一落下した場合でも、ガラスの破損、飛散を防止し安全性を付与するフッ素系などの特殊高硬度ハードコート材をポリエステルフィルム表面に精密コーティングすることで、表面鉛筆硬度2H以上(粘着層付き)を達成、ハードコート表面に付着した指紋を簡単、きれいに拭き取ることができるという。
ところで2010年度ノーベル物理学賞には炭素原子1個分の厚さ(0.1~0.3nm)のシートで、ハチの巣状の六角形の格子構造を持ち、高強度で導電性があり熱放散性が良く透明性の高いカーボン素材「グラフェン」の研究で物理学者2名が受賞した。この夢の半導体素材グラフェンが、透明電極材料として一般的なITO(酸化インジウム・スズ)を代替する材料として、適用が検討されている。サムスンではRT-CVD(急速加熱型化学気相成長)を用いてロールツーロールプロセスで透明電極用グラフェンをポリエステルフィルムに成膜させるパイロット生産ラインを完成させている。ITO膜が希少金属を使用していることや成膜の効率などから高価なのに対して、グラフェン透明電極では、約1/100にコストを低減できる可能性があるとしている。
成長が鈍化してきているといわれる中国でもスマホ需要は今なお旺盛で、その性能向上や生産性向上に関わる技術は世界的に求められている。加工や表面改質、材料など多角的なアプローチで、スマホ技術の高度化が進められている。
第171回~第180回
第171回~第180回第171回 HTV3のISSへのドッキング成功 宇宙ビジネスの商機をもたらす「こうのとり」
第171回 HTV3のISSへのドッキング成功 宇宙ビジネスの商機をもたらす「こうのとり」「ハーモニー」に取り付けられる「こうのとり」3号機 H2Bロケット3号機によって7月21日に打ち上げられた無人補給船「こうのとり(HTV)3号機」が高度約300㎞で分離、所定の軌道に投入され、7月28日に、高度約400kmで国際宇宙ステーション(ISS)に滞在中の星出彰彦氏が操作するロボットアームで把持され、ドッキングした。今後、HTV3で運搬した宇宙飛行士の食料や日用品などがISS内に移送されるほか、同じく積載してきた和歌山大学/東北大学合同プロジェクト、福岡工業大学、明星電気、海外2大学の小型衛星5機がロボットアームで宇宙空間に放出される。
HTVの飛行イメージ
HTV3では、HTV2まで海外製だったメインエンジン(HBT-5エンジン)とRCSスラスタ(HBT-1スラスタ)がともに国産化(IHIエアロスペース(IA)社が開発を担当)された。HTV3はロケットから分離後、自動的にNASAのデータ中継衛星(TDRS)との通信を確立、ISS「きぼう」に設置された反射板(リフレクタ)を目標に、スラスタでISSに向けて徐々に近づき、ISSの後方約5kmの地点でISSに対して相対的に停止されたことが確認されるとスラスタが停止され、ロボットアーム(SSRMS)でHTV3のグラプルフィクスチャ(FRGF)を把持、ISSの「ハーモニー」(第2結合部)の地球側の共通結合機構(CBM)に結合され、ISSに係留された。ISSに結合されハッチが開かれると、ISSのクルーが補給キャリア与圧部から船内物資(実験ラック、飲料水、衣料など)をISS内に移送し、逆にISSの不要品を補給キャリア与圧部に積み込む。また、曝露パレットを補給キャリア非与圧部から取り出し、船外物資を移送する。
衛星搭載ケースに収納後にソフトバッグに梱包されHTV3で運ばれた10㎝四方の小型衛星(CubeSat)5機の放出機構は次のとおり。ISSの中では「きぼう」だけがエアロックとロボットアームを装備しているが、これらを使うことでクルーが船外活動をせずに小型衛星を放出できる。ISS到着後、ソフトバッグは「きぼう」内に搬入され、「きぼう」のエアロックの内側ハッチを開け、エアロック・スライドテーブルを船内側に伸展させる。衛星を搭載した小型衛星放出機構(J-SSOD)と、親アーム先端取付型実験プラットフォームをエアロック・スライドテーブルのアダプタに取り付ける。スライドテーブルをエアロック内に収納し、エアロックの内側ハッチを閉鎖し、内部を減圧する。エアロックの外側ハッチを開けて、エアロック・スライドテーブルを船外側に伸展させる。「きぼう」のロボットアームで親アーム先端取付型実験プラットフォームを把持し、スライドテーブルから外す。ロボットアームで放出位置まで移動し、位置決めを行う。軌道上もしくは地上からのコマンドで、放出機構(片側)から衛星を放出する。終了するともう片方の放出機構からも衛星を放出する。放出は、分離機構のカムを回転させると正面の蓋が開き、バネの力で押し出される仕組み(図)。ロボットアームで親アーム先端取付型実験プラットフォームをエアロック・スライドテーブルに戻し、ハッチを閉じて内部を再加圧し、船内に放出機構を戻す。衛星は放出から30分が経過するまではアンテナなどの展開はせず、電波の放射も行ないよう設定される。小型衛星は、高度400kmで放出した場合、250日程度で大気圏突入し、ミッションを終了する。図:ばねの力で押し出される仕組み
ISSからの不要品の積み込みなどが完了すると、HTV3はISSから分離され、大気圏に再突入し燃焼廃棄され。HTV3は、次の手順でISSから分離される。まず、ISSのロボットアームで把持した状態で、共通結合機構(CBM)を解除する。これは、2枚のハッチ間の空気を真空引きして減圧したのち、CBM制御装置に16本のボルトを緩めるコマンドを送信(通常はクルーがラップトップPCから送信)し、CBMの固定を解除するもの。ISSのロボットアームで放出ポジションに移動すると、誘導・航法・制御装置(GNC)が起動され、推進スラスタの噴射が準備(スラスタの噴射停止から、噴射が可能な状態に切り替え)され、ISSのロボットアームの把持を解放し、ISS軌道からの離脱噴射を行う。
その後、減速させるための軌道離脱マヌーバを実施し、大気圏に再突入するわけだが、HTV3では、日米の2種類の再突入データ収集装置を搭載し、再突入・分解時の環境データの取得を行う予定となっている。再突入する宇宙機の破壊現象を特定することにより、落下の予測精度を高めて着水警戒区域の縮小につなげると共に、大気・加熱率等の再突入機の設計(回収機であれば耐熱性の検証、廃棄する機体であれば耐熱性や強度の余裕を減らして燃え尽きやすい設計)に役立てるためのデータ取得を行う予定。
再突入データ収集装置「i-Ball」 日本(IHIエアロスペース)が開発した再突入データ収集装置「i-Ball」には2台のカメラを搭載、ハッチが高温で破壊される様子の撮影と、降下しながらHTVが破壊される様子の撮影に挑む(世界でも初めての試み)。i-Ballを起動するためのスイッチ操作は星出宇宙飛行士が行う予定。i-Ballは球形をしており、アブレータで高熱に耐えたのち、パラシュートを使って降下し、着水してからイリジウム衛星経由でデータを送信する方式。データ送信を行うためにしばらくは浮いているが、いずれ沈む設計となっており回収はしない。i-Ballは、HTV3の与圧部から放出される機構を持っているわけではなく、HTV3の破壊と共に外へ放出され、HTV3の破壊の様子(破片の温度や加速度、位置など)を測定する。上空6㎞でパラシュートを開いて落下、着水し、取得したデータを送信する。
さて、小型衛星はこれまでも大学などが低コストな衛星技術として打ち上げ、運用を志向しているが、耐久性不足あるいは打ち上げ時の損傷などがもとで宇宙のごみ(スペースデブリ)と化してしまう例が多かった。これに対してHTV3では先述のとおり、緩衝材となるバッグで運搬されるため、打ち上げ時の衝撃による不具合が出にくいうえ、不具合があってもISS内で修理できる。小型衛星のビジネス化に向けた検証が進めやすくなると見られる。
また、HTV3のISSとの脱着部やロボットアームの駆動部などでは、二硫化モリブデンなどの固体潤滑コーティングが真空中での潤滑を実現しているが、以前本欄で報告した通り、こうした固体潤滑コーティング材を含めた各種材料の宇宙空間での暴露試験では、スペースシャトルの運用終了後、暴露パレットの運搬をどうするかが不安視されていた。こうした点でも、大型の実験ラックや大型の船外物資などISSへの輸送能力の高いHTV3の役割は大きい。
さらに大気圏再突入時のデータどりなど、有人宇宙船の開発につなげるステップとしても期待されている。
宇宙開発の宇宙航空研究開発機構(JAXA)法と内閣府設置法が6月に改正、7月12日には宇宙戦略室が内閣府に設置され、宇宙産業の国際競争力向上に向けた動きが活発化してきている。ここでは他国に依存している有人飛行を自国で賄うことも目標に置いている。HTV3のプロジェクトがその良い試金石となることを願う。
第172回 大田区・町工場がボブスレーでソチ冬季五輪を目指す
第172回 大田区・町工場がボブスレーでソチ冬季五輪を目指す開発中のボブスレーソリ 日本のものづくりを支えてきた町工場。その集積地の一つ、東京・大田区の町工場が中心となって「氷上のF1」と言われるボブスレーの開発プロジェクトが進められている。その「下町ボブスレー」ネットワークプロジェクトでは、2014年にロシアで開かれるソチ冬季五輪に向けて、日本チームが使う2人乗りボブスレーのソリを開発していく。
ボブスレーは独特な形状と機構を持つ専用のそりに乗って、氷が張ったコースを滑走、タイムを競う冬季五輪の人気種目。最高速度は時速130km~140kmに達することから、「氷上のF1」と呼ばれている。ボブスレー用のソリは、鉄製のシャーシに流線型のFRP製カバーをつけたもので、前方にハンドル、後方に停止用のブレーキを備えている。近年では、競技向けボブスレー用そりは空気力学の観点からの研究開発が進んでおり、イタリアチームではフェラーリが、ドイツチームではBMWが、米国では米国航空宇宙局(NASA)がソリを開発するなど、自国を代表する自動車メーカーや航空宇宙関連企業・機関が中心となって、国の威信をかけた開発競争が繰り広げられている。
日本でのボブスレーの知名度は欧米に比べ低く、競技人口も少ないといった背景から、ソリの開発を手がけるメーカーは少なく、日本チームはイタリア製やドイツ製の市販品を購入し改造していた。しかし改造にも限界があり、タイムが上がらない状況だった。
ボブスレーのタイム短縮では、氷面と接触するソリの刃(ランナー)との摩擦抵抗の低減と、ボディーの空気抵抗低減の効果が大きい。
このボディーの空気抵抗低減という点が、レーシングマシンを手がけてきた自動車メーカーが担当している所以である。今回、ボディー開発では、レーシングマシンを手がける「童夢」グループの童夢カーボンマジックが、軽量で剛性の高い炭素繊維強化プラスチック(CFRP)を使用して挑む。また、空気抵抗を減らすための流体解析はソフトウェアクレイドルが担当する。
一方で、ランナーの摩擦抵抗低減は自動車メーカーやNASAの牙城ではない。これには東京大学教授で摩擦工学(トライボロジー)を専門とする加藤孝久教授の指導のもと、金属の精密加工を手がけるマテリアルや、熱処理や各種表面改質処理を手がける上島熱処理工業所など、匠の技を持つ「大田ブランド登録企業」が挑む。精密加工技術でランナーの接触面積を少なくすれば摩擦抵抗は減るが、ランナーの刃先が鋭利すぎると、氷に食い込んで摩擦抵抗が増えてしまう。その精密加工のバランスによるランナー表面の制御で摩擦抵抗を減らす。一方、上島熱処理工業所の表面改質技術がランナーに潤滑性や耐久性を付与する。1/100秒のタイム短縮が競われる中で、ランナーの摩擦抵抗が10%減少すると、ゴールタイムは0.6秒短縮されると言われる。ここでの材料・表面改質技術の優劣がタイムに及ぼす影響は大きい。
上島熱処理工業所はアマテラスという企業集団の一つとして次世代産業である航空宇宙産業向けの新事業を進めるなど、大田区の町工場は先端技術を支えている一方で、この30年間で9000社から4000社に半減するなど、国内製造業の空洞化による影響を受け廃業が続いている。
上島熱処理工業所「難易度の高い大型製品の熱処理作業のようす」 下町ボブスレープロジェクトは、この国内空洞化の傾向に対して、町工場が積極的に新産業に参入していくためのネットワークを作る狙いがある。技術ベースで見ると、ランナーという金属の低摩擦化技術は、風力発電など次世代エネルギー開発には必須の要素技術となる。またボブスレーのソリの土台となる金属と炭素系素材の技術は航空機などに採用されており、環境・航空機産業に進出する足がかりとなる。
大田区の町工場が半減する中で生き残り、なお業況が好調な企業は、航空宇宙産業や医療機器など新分野に打って出ている。フェラーリやBMW、NASAといった大組織との闘いでソチ冬季五輪でのメダル獲得を掲げる下町ボブスレープロジェクトの主旨である「新たな価値の提供」や「夢のあるモノづくり」に賛同し新ビジネスを目指す町工場が1社でも増え、我が国のものづくりの活性化を支え続けることを願う。
第173回 JASIS2012開催、新産業を拓く分析・科学機器
第173回 JASIS2012開催、新産業を拓く分析・科学機器JASIS2012のもよう 日本分析機器工業会と日本科学機器協会は9月5日~7日、千葉市の幕張メッセ国際展示場で、「JASIS2012」を開催した。今回が「分析展/科学機器展」から名称を変えての第1回開催となり、「未来発見。-Discover the Future-」をテーマに、グリーンエネルギーや医療など新しい産業を確立するための、材料・表面改質層の開発を支える表面観察装置・分析装置や表面特性試験装置などが多数展示された。
東陽テクニカ「8500型 FE-SEM」 表面改質層の観察装置としては、細く絞った電子ビームを表面に入射し、表層の数ナノメータ(nm)深さから出る二次電子を二次電子検出器でとらえる走査電子顕微鏡(SEM)が多用されている。東陽テクニカでは、1kVの低加速電圧で10nm以下の分解能を実現するAgilent社製「8500型 FE-SEM(電界放射型電子顕微鏡)」を出展した。従来のデスクトップタイプSEMと比べ、電子ビームによる試料表面の帯電が圧倒的に尐ないシステムのため、ナノ構造を被覆して埋めてしまう可能性のある導電性コートや、面分解能を落とす原因となる高電圧測定に頼る必要なく、ガラスなどの帯電しやすい試料から、高分子や薄膜、バイオマテリアルなどの電子線ダメージを受けやすい試料に至るまで、幅広い試料の表面構造を高分解能で観察できる。
日本エフイー・アイ「Titan」 また、高分解能観察と微小領域の元素分析に用いられる透過型電子顕微鏡(TEM)では、日本エフイー・アイが走査/透過型電子顕微鏡(S/TEM)「Titan」を展示、オングストローム(Å)以下、原子レベルの観察と解析を可能にしている。たとえばカーボンナノチューブ(CNT)を機能性フィラーとして分散させることで樹脂の強化や導電性付与を施した複合材料が実用化されているが、この複合化した樹脂中に分散したCNTの分布の確認などにも利用できる。
試料表面を微小なプローブ(探針)で走査し、試料の三次元形状や局所的物性を高倍率で観察する走査型プローブ顕微鏡(SPM)では、エスアイアイ・ナノテクノロジーがSPMと白色干渉計(非接触表面形状・粗さ測定機)を複合化させた装置を参考出品した。SPMは微小領域での観察が得意だが、広域観察やできず、観察のスループットも課題とされていた。この欠点を白色干渉計で補うことで、たとえば各種タッチパネルに使われる透明電極膜ITO膜などの表面粗さ・形状評価として、Åレベルの狭域からミリレベルの広域までの高精度の計測や、計測結果のクロスチェックなどを実現するという。
一方、薄膜表面の機械的特性評価としては、薄膜の密着性や硬さ、摩擦摩耗特性の評価などがあるが、微小押し込み硬さ試験(ナノインデンテーション試験)では、押し込み荷重をμNオーダーで制御し圧子の押し込み深さをnmの精度で測定することで、母材の硬さに影響されずに薄膜のみの硬度測定を行う。オミクロンナノテクノロジージャパンでは、硬質薄膜からエレクトロニクス分野で採用が広がる柔らかい樹脂材料までの微小領域の機械的特性を評価する各種のナノインデンターを紹介した。
協和界面科学「全自動接触角計 DM-701」 基板に着滴した液体の画像をCCDカメラで取り入れ、液体の接触角(濡れ性)を測定するのに接触角計があるが、協和界面科学では、ウェットコーティングプロセスで川上から川下まで発生する様々な問題に対して、界面科学の視点から解決・最適化する手法を紹介、この接触角計を用いた二次電池の電極スラリー塗布プロセスの最適化について提案した。接触角計を用いて、集電体の表面改質状態がスラリー塗布に適しているか評価する。
今回は、喫緊の取り組むべきテーマとして東日本大震災後の「放射線」の分析、計測、除染に関わる機器の展示も目立ったが、次のステップとして、上述のようにグリーンエネルギーの確立に向けた開発を支援する計測機器も多数展示された。そのほか、医療・バイオ産業や水ビジネス、航空・宇宙ビジネスなどの次世代分野が日本の産業の柱となるよう、材料・表面改質層の計測・評価技術は、強く求められてきている。
第174回 注目されるエコカーとしてのクリーンディーゼル
第174回 注目されるエコカーとしてのクリーンディーゼル エコカーというとハイブリッド車(HEV)や電気自動車(EV)ばかりが取り沙汰されるが、より現実的なエコカーとして注目されてきているのが、クリーンディーゼル車だ。欧米では販売シェアが5割を超えるのに対し、日本では1%未満のシェアだが徐々に拡大してきている。
クリーンディーゼルエンジンの普及を阻んでいるのは、従来のディーゼルエンジンが持つ、排出ガスが汚い、音がうるさい、走行性能に劣るといったイメージによるところが大きかった。これに対して今年2月に発売されたマツダのクリーンディーゼル車「CX-5」では、14.0という低圧縮比を実現した新開発クリーンディーゼルエンジン「SKYACTIV-D」が従来のディーゼル車のイメージを払拭するとともに、従来比2割の燃費改善を達成している。
燃焼タイミングの最適化
ディーゼルエンジンは圧縮比が高い(通常16程度)ため燃料が十分に混ざる前に着火してしまう。その結果、局所所的な燃焼が起こり、NOxやススが多く排出されるため、近年の厳しい排出ガス規制をクリアするには、最適な効率が得られるピストン上死点付近での燃焼が難しくなり、燃費を犠牲にしても、ピストンが下降し圧力と温度が下がるのを待ってから燃焼させるしかなかった。
これに対し、低圧縮比にすると圧縮温度・圧力が下がるので、着火するまでに燃料と空気が均一に混ざる時間を十分に稼ぐことができ、結果として、NOxやススの排出が少ないクリーンな燃焼が実現できる。また、上死点付近での噴射と燃焼が可能なため、実質の膨張比が高圧縮比ディーゼルエンジンよりも大きくとれ、高効率になる。こうしたメリットにもかかわらずディーゼルエンジンの低圧縮比化が進まなかったわけは、低温時の圧縮温度が下がりすぎて始動性に問題が生じることと、暖機運転中の圧縮温度・圧力不足から、きちんと燃焼しない「半失火」の状態になるためだ。
排気バルブ二度開きによる吸気工程EGRシステム そこで「SKYACTIV-D」では、ピエゾインジェクターによる燃料多段噴射などで低温時始動性を確保した一方、冷間始動時の半失火の抑制に対しては、排気バルブの二度開きによる吸気行程EGRシステムという可変動弁機構を採用している。吸気行程中にわずかに排気バルブを開き、排気ポート内の高温の残留ガスをシリンダー内に逆流させることで、空気温度を高めて圧縮時の温度上昇を促進、着火の安定性を向上させるものだ。この可変動弁機構として、シェフラー社の「スイッチャブルフィンガーフォロワー」(マツダ名称:IDEVA)を採用している。
Switchable roller finger follower – ダブルリフトコンセプト
Switchable roller finger follower
スイッチャブルフィンガーフォロワーは、バルブリフト高さを二段階に切り替える可変動弁システム。ローラーフォロワーを備えたインナーレバーと、すべり接触部「スライディングパッド」を持つアウターレバーの二つのレバーで構成される。アウターレバーは油圧式ピボットエレメントとエンジンバルブの二点で支えられ、インナーレバーは回転軸によってバルブ側のアウターレバー上で支持、インナーハウジングはロストモーションスプリングでアウターハウジング端に押し付けられている。二つのレバーがアンロックの状態では、カムはアウターレバーのスライディングパッドフォロワーとの摺動になり、バルブは高リフトで1回開く。これに対して、油圧作動によるロッキングピンでアウターレバーとインナーレバーがロックされた状態では、最初にスライディングパッドとの摺動による高リフト作動、続いてインナーレバーのローラーフォロワーとの接触による低リフト作動の二度開きとなる。IDEVAの切替カムシャフト3連カム機構
排気バルブ二度開きによる吸気行程EGRシステムでは、排気側のカムの回転を一般的なローラーフォロワーとこのスイッチャブルフィンガーフォロワーの二つで受ける構造とした。スイッチャブルフィンガーフォロワーは冷間始動時用で、これを作動させるカムにも冷間時用のプロファイルが設定されている。冷間時に吸入工程で排気バルブが低リフトで開き、高温の排気ガスを逆流させる。
この可変動弁機構は低圧縮比エンジンの信頼性を確保するのに欠かせない技術で、カムとスライディングパッドが焼き付いて作動不良になることのないよう、接触面曲率半径の拡大、片当り防止、部品精度の向上、カムフォーム見直しによる実運転時の面圧低減、カムとスイッチャブルフィンガーフォロワーそれぞれの表面粗さ改善などの動弁系レイアウトの見直しが行われた。
カムは高周波焼き入れしたダグタイル鋳鉄製とし、このカムと摺動するスライディングパッドでは、カムと相性が良く、高荷重でのフリクションを低減し耐摩耗性を向上するコーティングが検討された。シェフラー社ではドイツのコーティングセンターを中心に開発された表面改質技術の中から、硬質クロムベースのCN膜やDLC(ダイヤモンドライクカーボン)膜などを試験した。DLCは、エンジン油の燃費向上に効いているモリブデン添加剤との相性が悪いため見送りとなり、硬質クロムベースのCN膜は、優れた耐摩耗性や低摩擦などの特性から採用になった。PVD法で2~3μm厚に成膜、面粗さはRa00035μm以下に抑えられている。従来比約20%という低フリクション化を図るこの耐摩耗のコーティング技術に加えて、油膜を確保するためカムの面粗さも改善、金属接触をなくし、滑らかな可変動弁を実現している。
エンジンの機械抵抗損失のうちバルブトレインの損失は8%で、その内の35%、つまりエンジン全体の3%の機械抵抗損失をすべり接触が占めるが、今回このスイッチャブルフィンガーフォロワーを適用したことで、ディーゼルエンジンの低圧縮比が実現し、シリンダブロックのアルミ化や部品のサイズダウンを実現、全体では10%の軽量化と、20%の燃費低減を図っている。
米国コンサルティング会社の調査では、世界全体に2010年で7割強だった新車販売でのガソリン車比率が2020年には4割強に低下する一方で、ディーゼル車は約2割のシェアを維持すると予測している。シェフラー社ではすでにエンジン油中のモリブデン添加剤と相性が良いDLC膜の開発も進行中とのことだが、こうした材料・表面改質技術や機械要素技術などの進展とともに、クリーンディーゼル車の一層の燃費向上と市場の拡大が期待されている。
第175回 第15回M-Tech関西が開催、機械要素を支える表面改質技術が一堂に
第175回 第15回M-Tech関西が開催、機械要素を支える表面改質技術が一堂にM-Tech関西のもよう 「第15回 関西 機械要素技術展(関西 機械要素技術展(M-Tech関西)が10月3日~5日、大阪市のインテックス大阪で開催された。同展は、軸受や直動案内、歯車などの機械要素や、機械要素を構成する材料・表面改質・加工技術を一堂に集めた西日本最大の専門技術展。
ベアリングなどの機械要素では、低摩擦にすることで自動車であれば燃費向上に、産業機械であれば省エネルギー・省電力につながる。また耐摩耗性を高めることで機械の長寿命化が図れるほか、同等の耐久性であれば機器のコンパクト化が可能になる。
今回の出展ではそうしたベアリングや直動案内、歯車、シール部品などの最新技術・製品が出展されたのに加えて、それら機械要素の低摩擦化や耐摩耗性向上を実現する各種の表面改質技術も紹介された。
金属部品の低摩擦化・耐摩耗性向上を図る
日本アイ・ティ・エフは、バルブリフターなど自動車部品で実績のある水素フリーDLC(ダイヤモンドライクカーボン)コーティング「HADLC」のほか、高硬度で、耐熱、耐摩耗性に優れるクロム系コーティング「IAX」などを展示した。
丸紅情報システムズは、独自のパルスアークPVD方式により、高硬度・低摩擦で相手攻撃性の低い水素フリーDLCコーティング「ULFコート」の受託成膜サービスを提案、切削工具で累計1000万本のコーティング実績を持つ量産品対応であることを強調した。さらに熱CVD方式による、高硬度で高い密着性と耐摩耗性を持つダイヤモンドコーティング「ダイヤモンドコート」の受託成膜サービスについて紹介した。
また、ナノコート・ティーエスは、軽量化による燃費向上を目的に採用が進むアルミ合金向けに、摺動特性を向上するメタル(タングステン)含有DLCコーティング「セルテスDT」を提案した。
このアルミ・アルミ合金向けとしてアルバックテクノは、硬質アルマイトとフッ素樹脂のシナジー効果で耐摩耗性向上・摺動性向上・かじり防止・スティックスリップの減少等の機械特性を持たせる高機能複合皮膜「タフラム」を、鉄、ステンレス、銅、アルミ合金に対しては、無電解ニッケルにフッ素樹脂を複合させることで、高硬度で耐摩耗性・すべり性・かじり防止・非粘着性・耐候性・耐油性等に優れる「ニダックス」などを紹介した。
高分子材料の機械的特性を改善する
空気圧シリンダーなどに使われる往復運動用シールではゴムや樹脂材料が用いられるが、新興国向けなどで使用頻度が高くなるにつれて、こうしたシール部品の摺動特性や耐久性を改善するニーズが高まってきている。
こうしたニーズに対して、ナノコート・ティーエスは、ゴム部品の摺動特性を向上できるDLCコーティング「セルテスDC-R」を紹介、Oリング等のシール製品の凝着防止・耐摩耗性向上を提案した。
また、住鉱潤滑剤は、密着性に優れる樹脂(バインダー)に低摩擦性に優れるPTFE等の固体潤滑剤を配合した潤滑塗料で、部品へ塗布して硬化させることでドライ被膜を形成する「Moltiacoat(モルティアコート)」を紹介した。素材に対する被膜の密着性が良好なため、柔軟性のあるゴム/プラスチック部品においても被膜が追従するため、はく離が少なく、優れた潤滑効果を持続的に発揮するという。
金型の耐久性・離型性を高める
金型向けでも、部品の精度や品質を高める離型性や生産性を高める耐久性などを改善する表面改質技術が、多数紹介された。
清水電設工業と浅井産業は、PVDを核に各種コーティング技術を提示、S-PVD、TiAlN、TCの利点を活かし、さらなる高硬度、高耐熱性、潤滑性を付与する「ZERO-I(ゼロワン)コーティング)では、優れた耐摩耗性・耐熱性の付与で金型の長寿命化、生産性向上を謳った。また、日本コーティングセンターは、耐熱性と潤滑性、CrNよりも高い耐摩耗性を兼ね備えた新しい金型用被膜「ダイモスコート」などの処理サンプルを展示した。
我が国の機械要素メーカーも例に漏れず、新興国のメーカーとの過酷な競争にさらされているが、今回紹介された表面改質技術は機械要素の表面に高付加価値な特性を付与し、商品の差別化を図る技術だ。今回のような展示会を通じて、機械要素メーカーと表面改質技術の提供者が共同で各種ニーズに取り組み、世界的に競争力の高い商品技術が生み出されていくことを期待したい。
第176回 新エネルギー資源として期待されるシェールオイル
第176回 新エネルギー資源として期待されるシェールオイル提供:石油資源開発 石油資源開発は先ごろ、秋田県由利本荘市にある「鮎川油ガス田」でシェールオイルの採掘に成功した。シェールオイルは、地下1,800mにある頁岩(けつがん)層(シェール)と呼ばれる硬い粘土質の岩盤層を塩酸などを混ぜた酸性の液体で溶かして取り出した。シェールオイルは米国などでは商業生産が本格化しているが日本で掘り出されるのは今回が初めてで、自前のエネルギー資源として注目が集まっている。
シェールオイルは一般の石油や天然ガスのように地層の間に貯留しているわけではなく、硬い岩石の中に閉じ込められた形で存在するため、パイプで掘削しても自噴しない。そのため技術面、採算面で採掘が難しいとされてきたが、近年、水平坑井掘削・水圧破砕といった採掘技術が開発され、1バレル100ドル前後という原油価格上昇でコスト面でも採算が合う状況になってきた(シェールオイルの生産コスト40~60ドル)ことで、国内年間消費量の約100年分とも言われる埋蔵量の豊富な米国では生産が本格化してきている。
日本は比較的地層が新しいため、シェールオイルやシェールガスの埋蔵量が少なく採算的に採掘対象となる油ガス田に乏しいと見られていたが、石油資源開発は2012年3月から石油天然ガス・金属鉱物資源機構(JOGMEC)の支援を受けて調査研究に着手、鮎川油ガス田などの既存坑井を対象とした坑井刺激(酸処理テスト)の結果解析と総合評価、さらに秋田県全域における女川層のポテンシャル評価を主目的に実証試験を実施し、酸処理テストの実施により、今回シェールオイル採取に成功した。シェールオイルの採掘例
硬いシェールには自然の割れ目が発達していることがあるが、その割れ目を石灰岩などで塞いでいることがある。そこで石灰岩を溶かすと同時に割れ目を拡大するために、鮎川油ガス田の地下1,800mの女川層に垂直にパイプを下ろし、塩酸で処理した流体(水)をポンプ注入した(ハイドロ・フラッキング)。注入した液体総量141.6kLに対して、高圧ガスを坑井内に放出し坑内液体の比重を小さくするとともにガスの膨張上昇エネルギーによって液体を地上に汲み上げる「ガス・リフト手法」により回収した液体量52.1kLのうち、31.1kLの原油が得られた。
マンドレルミル この深い掘削深度でのパイプには、高圧や腐食に耐えるシームレスパイプが用いられる。シームレスパイプの製造工程の一つであるマンドレルミルでは、管を圧延して長く薄く伸ばし、管の厚みを製品近くにまで仕上げていくが、パイプ材料には耐食性、耐圧性の高いクロムやモリブデンなどを含有したステンレス鋼が多用される。
球面すべり軸受 マンドレルミルで加工され熱処理されたこのシームレスパイプは、長いもので20m強になるが、掘進距離は今回の場合で1,800mに及ぶため、継手により採掘可能な距離まで延長することになる。長距離のため継手部分は、ねじれなどによって破損することのないよう、ある程度の自動調心機能をもった軸受で支持されている。軸受材料として腐食に強いステンレス鋼(外輪)とベリリウム銅合金(内輪)を組み合わせたような自動調心軸受などが用いられる。
今後、第2ステップの実証試験として、鮎川油ガス田内で新たに井戸を掘り、シェールオイルを効率的に採取する水平坑井掘削技術、水圧破砕技術を試す予定だが、垂直掘進、さらに水平掘進と距離が伸びるため、シームレスパイプおよび自動調心軸受の使用点数が増える。鮎川油ガス田のシェールオイルの埋蔵量は、2011年度に日本国内で生産された石油の総量とほぼ同じ約500万バレル程度で国内の石油消費量の1日強分に留まるが、秋田県全体のシェールオイルの埋蔵量は同約20日分に相当する約1億バレルに上るほか、新潟など他県でも埋蔵の可能性を秘めている。ハイドロ・フラッキング法は、小規模地震の誘発や塩酸含有流体の使用などによる環境負荷も懸念されているが、そうした不安要素への万全な対処や掘削コストの改善も含めシェールオイルの採掘技術を確立することで、現在0.4%に留まる石油自給率を改善する我が国の新しいエネルギー資源確保の取り組みに期待したい。
第177回 JIMTOF2012に見る加工の高効率・高精度化を支える表面改質技術
第177回 JIMTOF2012に見る加工の高効率・高精度化を支える表面改質技術 11月1日~11月6日、東京・有明の東京ビッグサイトで「第26回日本国際工作機械見本市(JIMTOF2012)」が開催、切削・研削・研磨・プレス加工などの工作機械をはじめ、直動案内機器や軸受などの工作機器、工具、工具・金型のコーティング、加工油剤などの関連技術が一堂に会した。我が国ものづくりの競争力を高める加工の高精度や高効率加工、省エネルギー、低コスト化を実現する多軸機や複合機、その可動部を支える軸受や直動案内などの機械要素技術、切削工具や金型の耐久性を高め加工品位を高める各種コーティング技術も多数出展された。
加工の高効率化は、工作機械において工具主軸の高速回転と送りの高速化で実現される。これに対しNTNは、内輪の間座をエアで冷却する「エアオイル潤滑 空冷間座付軸受」を出展、従来比1.3倍以上の高速化と組み込み後予圧量が3倍以上の高剛性化の両立を提案した。送りの高速化では、たとえば日本精工が、ボールねじ「ハイスピードSSシリーズ」と高速・重荷重用サポートユニットを紹介した。独自の高速・静音技術を駆使し、滑らかなボール循環を実現、従来のチューブ循環方式の標準品に比べ2倍以上の許容d・n値(軸径d(mm)×回転数n (min-1))116万の高速回転と6dB(A)低減の静音化、振動レベルの半減が可能になり、最高送り速度は、80m/min(軸径40mm、リード20mmの場合)に達するほか、高速化による支持軸受の発熱低減のため、サポートユニットには予圧を最適化した軸受を採用し、発熱を1/2に低減した。
工作機械側でこうした主軸や送りの高速・高精度・高剛性化が図られているわけだが、同様に各種材料に対して加工を施す加工工具にもビビリの抑制や、長寿命・高能率加工に最適な耐摩耗性向上が要求される。たとえば三菱マテリアルでは、エンドミル工具の耐摩耗性を大幅に向上する(Al,Cr)N系コーティング膜の平滑化により、切削抵抗の低減や切りくず排出性を向上した「スマートミラクルコーティング」を施した切削工具を紹介した。
こうした耐摩耗性や潤滑性を付与した表面改質を施した製品が各工具メーカーから展示される一方、各種コーティングの受託加工メーカーや成膜装置メーカーも出展した。
ハウザーテクノコーティングは、新開発の円形アーク蒸着技術「CARC+」と同技術を用いた成膜装置「Flexicoat850」を紹介した。同成膜装置により、工具に最適な平滑でドロップレットのないTiNやTiAlN、AlTiN、多層TiN/AlN膜を成膜、加工試験においてAIP(アークイオンプレーティング)による処理に比べて高い耐摩耗性能を示すとした。
オンワード技研は超硬工具に最適な、1μmの膜厚と55~65GPaの硬度をバランシングさせた耐摩耗性の高いダイヤモンドライクカーボン(DLC)膜を紹介した。
ユニオンツールは、超硬合金加工用ダイヤモンドコートエンドミル「UDCB」を出展した。超硬合金の切削工具として単結晶・多結晶ダイヤ、CBN工具における切込み量は数μm単位での加工しかできないほか、電着工具では摩耗により高精度な加工が不可能だが、熱CVD法により成膜、9000HVの高硬度で高い密着性と耐摩耗性を持つダイヤモンドコート「UDC」を被覆することで、切込み量百μm単位の高効率加工を超硬材で実現している。丸紅情報システムズでは同社ブースで、そのダイヤモンドコート「UDC」とDLCコート「ウルフコート」の受託加工サービスをPRした。
今回もヤマザキマザックやオークマ、森精機製作所、ジェイテクトなど多くのブースで、航空機部品の加工デモが行われていたが、航空機では機体重量を軽減し燃費を向上させるため、CFRP(炭素繊維強化プラスチック)などの難削材を用いた複雑形状の部品が多い。そこで旋削機能も含めた高剛性・高精度な5軸複合加工機が必要となる。5軸複合加工機1台に工程集約することで、工程間の搬送や段取り時間の削減、加工精度のバラツキを抑え、航空機部品の生産性向上が図られている。
オーエスジーは、このCFRP加工に適したダイヤモンドコーティング工具を紹介、また、オーエスジーコーティングサービスは、超微細結晶の多層構造により表面が平滑で切れ味がよくCFRP加工でのデラミネーション(層間剥離)の発生を防止するダイヤモンドコーティングを紹介した。
企画展示として公開された東京・大田区の町工場有志により作製された下町ボブスレーの初号機マシン(詳細は当コーナー第172回参照)。
今回のJIMTOF2013では、新興国とのモノづくり競争力向上がますます求められる中、航空機、医療、エネルギーなど成長分野のアプリケーションに対応する工作機械や工具・金型などが多数紹介された。こうした中で、加工工具や金型では、スマートフォン向けなど高い生産性の求められる加工や、人工関節など難削材での高精度化が要求される加工などで、耐久性を高める各種の表面改質技術が活躍している。展示会を通じて、MQL(極微量切削油供給)加工などに見られるように加工現場の作業環境改善から加工油の使用が抑制される中、加工工具や軸受、送り機構などでの潤滑性能を補足し高める表面改質技術がますます求められている様子が、うかがえた。
第178回 三菱自リコール問題に包括的な研究開発の復活を求める
第178回 三菱自リコール問題に包括的な研究開発の復活を求める 三菱自動車はミニカなど複数の軽自動車のエンジンについて、クランクシャフト部オイルシールからのエンジンオイル漏れによるリコール(回収・無償修理)に消極的だったとして、国土交通省から異例の厳重注意を受けた。国交省は今後、道路運送車両法に基づく立ち入り検査を行い法令違反がなかったかを確認する。
同社は2005年にエンジンオイル漏れの不具合を把握しながら、2010年までリコールに踏み切らなかった。同じ不具合を理由に届け出たリコールは今月までに計4回に及び、対象車種は10車種約176万3000台と国内で過去最多にのぼる。幸い事故は起きていないものの、走行を続けた場合、オイルが流失することでエンジン部品が焼付いて走行できなくなる恐れがあるという。これに対し国交省は、リコールを検討する三菱側の姿勢が消極的で、原因究明も不適切などとして厳重注意した。
三菱自動車では、エンジンフロントケースに装着しているクランクシャフトオイルシールにおいて、 車両生産時と異なる材質の補修用オイルシールに交換された場合に、エンジンフロントケースの加工ばらつきや、オイルシールの圧入量ばらつきなどの複合要因により、当該オイルシールの保持力が低下しているものがあるため、該当するオイルシールが抜け出し、エンジンオイルが漏れ、油圧警告灯が点灯し、そのままの状態で使用を続けると、 エンジン内部部品が焼付き、走行不能となるおそれがあるとしている。これに対する改善措置の内容は全車両、当該オイルシールの取付部を点検し、車両生産時と異なる材質の補修用オイルシールに交換されたものについて、 オイル漏れが無い場合は、フロントケースにオイルシール抜け止め用プレートを追加装着し、オイル漏れがある場合は、オイルシールを新品に交換するとともに、フロントケースに抜け止め用プレートを追加装着するもの。なお、改善措置用部品の供給に時間を要することから、当面の暫定措置として、すべての使用者に不具合の内容を通知し、 交換部品の準備が整うまでの間、エンジンオイル量の点検を啓発し、運転時の注意事項を周知するとしている。
改善箇所説明図
オイルシールは金属環にシールリップを構成する合成ゴムを焼付け接着し、組み込んだバネによりリップ部を軸に適度に押し付けホールドすることで、運動している部分のシールを可能とする。今回問題となったオイルシールは、エンジンのフロントケースの溝に挿入し、回転するクランクシャフトに密着させてエンジンオイルが外に漏れるのを防ぐ機能をもたせるもの。
正常な取付状態にあるオイルシールは大気側からわずかな空気を吸い込んでいて、この吸い込み現象によって油が外に漏れない仕組みになっている。日本製のオイルシールは高品質でグローバルに流通している。特にクランクシャフトは高速回転するために封入する油温は高くなり、高温に耐えるフッ素系のオイルシールが用いられる。また、リップ部に低いネジ山を設け、漏れようとするオイルを軸の回転によって内部に送り戻す作用を実現する「ネジ付きオイルシール」が使用される。このようにオイルシールは、適確な適用がなされれば、大量の不具合が出るはずのない信頼性の高い技術である。
今回のオイルシールの不具合により一部でエンストに至ったというが、最終的に焼付いたと思われるエンジンベアリングは、本来エンジンオイルの油膜が介在する流体潤滑状態で機能するものだが、近年の省燃費エンジンオイルの低粘度化やアイドリングストップ機構による油膜のできにくい状況に対応して、二硫化モリブデンなど固体潤滑被膜を採用して摩擦抵抗を低く抑え、希薄潤滑下でも、そう簡単には損傷しない技術を確立している。それが焼付いたとすれば、クランクシャフト部で長期にわたり完全に油膜が切れたということなのだろう。
オイルシールメーカーによれば、オイルシールが確実に機能を発揮するには、油との適合性や、軸の表面粗さや外周公差、ハウジングのはめ合い面の表面粗さやはめ合い公差などが厳密に管理されなくてはならないとしている。修理で交換した際のオイルシールと軸やハウジング溝の粗さや寸法は適切だったのか、そのオイルシールは油で膨潤し硬度の低下や耐摩耗性の低下を引き起こすような材料ではなかったか、ぜひとも深く細やかな検証を進めてほしい。
上述したオイルシールやベアリングは世界中で適用されている、日本の誇る優秀な技術だ。しかしこれを適切に用いなければ今回のような事故につながり、社会的には、それらの製品技術に非があるように思われてしまいかねない。グローバル市場での我が国製品の優位性は、その技術と品質にある。技術と品質の保持は製品単体でなく、アプリケーションにあった適用手法の確立も含めて可能になるが、ここにきてエレベータ事故など、過去に指摘された問題が改善されずに起こった事故が各分野で多数報告されているのは、産業界で研究開発予算が縮小傾向にあることのマイナス面が露見してきているのだろうか。こうした中、安倍晋三次期政権が経済成長を税制面から後押しする方針として検討している、企業の研究開発投資を促進する「研究開発減税」の拡充などの施策にも期待したいところだ。その研究開発を拡大する中では、製品単体でなく、その適用法の確立も含めた包括的な取り組みにぜひとも努めていただきたい。
第179回 ASTEC,SURTECH表面改質関連セミナーみどころ紹介
第179回 ASTEC,SURTECH表面改質関連セミナーみどころ紹介昨年のセミナーのもよう 「ASTEC 2013 第8回 先端表面技術展・会議」、「SURTECH2013 表面技術要素展」、「nano tech 2013 第12回 国際ナノテクノロジー総合展・技術会議」など12の展示会が1月30(水)~2月1日(金)の三日間、東京・有明の東京ビッグサイトで開催される。ASTECとSURTECHでは、DLCコーティングやセラミックコーティング、めっき、撥水・親水性表面処理、ブラスト加工などの「表面処理・コーティング・接合技術」、表面張力・形状・硬さ・粗さ測定機やPVD・CVD装置などの「表面処理・加工・計測装置」、機能性ナノ薄膜や樹脂・コーティング材など「材料・素材」などの展示スペースを設け、各分野における最先端の表面処理技術などの展示を行う。
また展示の他には、表面改質関連のセミナーが多数開催される。本稿では、ASTECの第8回先端表面技術会議、SURTECH特別講演、表面技術協会部会講演会の中から編集部注目のセミナーについて紹介する。
表面改質関連セミナー1日目(30日)は、SURTECH特別講演として「多孔質めっき」と「電子部品におけるめっき技術の可能性と展望」と題しためっきの話題が2件、「溶射による表面改質の最新動向」と題した溶射の話題について1件の講演が行われる。表面技術協会(以下、協会)の部会講演会では、新たな環境規制の情報提供と対策法の提示、リサイクル技術、低環境負荷表面処理技術、無害化技術、環境評価技術、危機管理などに取り組んでいる表面技術環境部会が3講演、ドライプロセスによる材料機能の創製(物理蒸着法、化学蒸着法、溶融成膜法、表面硬化法、表面加工法、エッチング法)について年4回の研究例会を開催している材料機能ドライプロセス部会が4件の講演を行う。
2日目(31日)は、協会ナノテク部会、電鋳・金型の表面処理研究部会/表面改質・硬化部会が話題提供を行う。ナノテク部会では、東京都立産業技術研究センターの川口雅弘氏が「DLC(diamond-like carbon) 膜とその評価法 -現状と展望-」と題して講演。昨今、脚光を浴びているDLC膜について、その成膜法や評価法について解説するほか、これまでの日本の市場動向や今後の展望などについて紹介する。電鋳・金型の表面処理研究部会/表面改質・硬化部会では、パーカー熱処理工業の渡邊陽一氏が「自動車材料と表面改質」の演題で自動車に使用される歯車など、高面圧化ニーズが高く低フリクション性能を要求される部材の材料と表面改質技術について設計の考え方から従来の技術および最新の技術について紹介する。もう1件は航空機の話題。JALエアロ・コンサルティングの笹原修氏は「航空機材料と表面改質」と題して、航空機に使用される材料の概要を説明し、表面改質技術が多用されているエンジンと脚について詳細を説明する。エンジンについては、構造や整備の概要を紹介するとともに、タービン翼の進歩に材料や表面改質技術が果たしてきた役割について、脚については構造、材料、および使用されている表面改質技術(めっき)について概要を説明する。
同日にASTECの第8回表面技術会議として、テーマ1「エネルギーの未来を拓く表面処理技術」、テーマ2「自動車産業の発展を支える表面処理技術」で合計9件の講演が行われる。テーマ2では、神奈川県産業技術センターの加納眞氏が「DLCコーティングの自動車部品への適用技術と展望」と題して、アルミニウム合金基材へのDLCコーティング技術と、DLCと環境調和型潤滑剤の組合せによる大幅なフリクション低減技術の二つについて紹介し、自動車摺動部品へのDLCコーティング適用技術の発展の可能性について概説する。また、このテーマではDLCの国際標準化について2件の講演が実施される。1件は東京工業大学教授の大竹尚登氏による「ここまで来たDLC技術(国際標準化を目指して)」。DLCの定義と分類をsp3結合比と水素含有量により整理することを試みた結果を紹介。まずDLCの範囲について検討し、sp3結合比として現在報告されている約90%を上限に設定した点を述べる。そしてspsp3比の定量化方法について詳細に検討・補正を行い、精度を高めてノンドープDLCの分類図を定め、応用例を当てはめた結果について述べる。もう1件は、ナノテック・平塚傑工氏による「ここまで来たDLC評価技術(国際標準化を目指して)」。自動車部品をはじめ様々な製造工程で利用が広がっているDLCの各種評価技術に関して解説。ニューダイヤモンドフォーラムが取り組んでいるDLC評価技術の国際規格化の最新情報として、特に分光エリプソメトリ法を用いた光学評価について基礎から事例を含めて解説する。今後のDLCの発展を見据えながら、自動車部品への表面処理を含めた各種応用に役立つ品質管理方法を紹介する。
3日目(1日)は、SURTECH特別講演が2件、協会でAl,Ti,Zr,Nb,Mgなどバルブメタルおよびそれに準ずる金属の陽極酸化皮膜の生成理論、構造解析および応用に関する研究を行っている金属のアノード酸化皮膜の機能化部会と、アルミニウム、マグネシウムなど軽金属の表面処理技術の研究調査などを行うライトメタル表面技術部会がそれぞれ3件の発表を行う。
第180回 ASTEC2013/SURTECH2013開催、医療・エネルギーのキーテクノロジー、表面改質技術
第180回 ASTEC2013/SURTECH2013開催、医療・エネルギーのキーテクノロジー、表面改質技術 「nano tech 2013 第12回 国際ナノテクノロジー総合展・技術会議」や「ASTEC 2013 第8回 先端表面技術展・会議」、「SURTECH2013 表面技術要素展」など12の展示会が、1月30~2月1日に東京・有明の東京ビッグサイトで開催された。ナノテクノロジーは、情報通信、エレクトロニクスから医療・健康、バイオ、環境・エネルギーまで、様々な重要課題解決のキーとして注目され、特に21世紀に入りクローズアップされている地球温暖化や生物多様性保持など環境・エネルギー問題、また、高齢化社会の中で必要とされる医療分野のほか、食品分野や化粧品分野へ向けた技術革新に貢献する大きなポテンシャルを持っている。nano techを中心とする12の展示会では、日本の新市場としても重要視される医療や新エネルギーの技術革新を支える新技術や新製品が披露された。
特にASTECとSURTECHでは、ダイヤモンドライクカーボン(DLC)コーティングやセラミックコーティングなどのドライコーティングから、めっき、撥水・親水性表面処理、ブラスト加工などの環境にやさしい表面改質技術や、その処理による材料の機械的特性などを評価する硬さや密着性、摩擦・摩耗特性などの試験評価技術などが紹介された。
パーカーグループのブース パーカーグループブースでは、日本パーカライジングがアルミピストンなど軽金属の摺動部品への応用を可能にした複合ニッケル合金めっき「NCC-SPコート」を出展した。潤滑性に優れた分散材を用いた複合めっきで、低い摩擦係数を可能とし、摺動部品の寿命を飛躍的に向上させるとともに、摩擦によるエネルギー損失を低減させる。またパーカー熱処理工業は、優れた導電性と耐食性を持つ導電性ナノカーボンコーティング「σ-コーティング」を紹介した。燃料電池では耐食性と電気伝導性に優れたステンレス分離板が多用されるが、同コーティングはステンレスよりも高い導電性・耐食性を持つため、ステンレスよりも軽い基材が使えて省エネが図れるほか、速い成膜速度と低コスト化で、生産性と経済性を改善するという。
ナノテックではDLC薄膜を機能別、用途別に分類した「ICFコーティング」(真性カーボン膜)を展示、優れた導電性から太陽電池などへ、生体適合性から人工関節やステントなど医療機器などへ適用できる可能性を示した。同社ではまた、構造や水素含有量に違いのあるDLCを使い分けるため、平成21年度からNDF、長岡技術科学大学と共同で経済産業省からの委託を受け、DLCの国際標準化を推進する活動を行っていることを紹介した。
丸紅情報システムズは、ユニオンツールが開発したDLCコート/ダイヤモンドコートの受託サービスを提案した。ダイヤモンドコートは主に切削工具や金型部品の耐久性工場による省資源化に、DLCコート「ULFコート」は自動車部品や機械部品の低フリクション化による自動車の燃費向上や機械の省エネや省メンテナンスにつながるとした。
ユケン工業のブース 今回もまた有害な重金属としてRoHS指令やELV規制などで規制の進む六価クロムの代替技術が多く紹介される中、ユケン工業は、完全クロムフリーで高耐食性のコーティング剤「メタスYC」を出展した。メタスYC-B(2コートベーク処理)+メタスYC-T(反応型の仕上げ処理)の組み合わせにより、キズ部でも安定した高耐食性を得られるほか、従来の処理に比べ焼付け温度が低い(約260℃)ため、素材の物性(展延性、靭性)に対する影響が少なく、処理コストの面でも有利という。
日本スピードショアのブース こうしたコーティングなどの特性を向上させる下地処理なども紹介された。たとえば日本スピードショアでは、ヤマシタワークスが開発した鏡面仕上げ技術「エアロラップ」を出展した。水分を含有した軟質研磨材をブラスト工法で投射することで、ワーク表面にダメージを与えることなく鏡面に仕上げていくため、たとえば続く熱処理工程での加工ダメージに起因する不良などの発生を防ぐほか、コーティング前に処理することで膜の密着性を向上させる。
また、表面改質膜の評価装置も多数出展された。
CSM Instrumentsのブース 薄膜の機械的特性評価装置を専門に扱うCSM Instrumentsは、DLCなど硬質薄膜からポリマーなど軟質薄膜までの硬さ試験として、0.0015nmの押し込み分解能、0.005μNの荷重分解能を持つため、バルク材の影響を受けずに薄膜自体の機械的強度を測定できる「ウルトラナノインデンタ」を展示した。液体カップや温度制御機能を備えたバイオステージを用いることで37℃といった生体内での材料や薄膜をシミュレートした試験評価を可能にしている。
フィッシャー・インストルメンツは、めっきや塗装膜など表面処理の膜厚を非破壊で膜厚測定できる装置について、持ち運び可能なハンディータイプから設置型などご使用用途に応じた測定機を展示した。協和界面科学は、機能性材料の量産手段として注目されるウェットプロセスコーティングや、電子デバイスの量産を印刷技術で行うプリンテッドエレクトロニクスが注目される中、半導体やフラットパネル、電池分野でキーポイントになる、機能性材料や電子デバイスが製品品質にどう影響し、品質向上にはコーティングや印刷プロセスにおける原料素材どうしの界面挙動をいかに制御し最適化するかを、界面科学の視点から定性・定量的に解析・評価する装置を出展した。
ASTECやSURTECHで紹介された各種の表面改質は、たとえば材料にない低フリクション特性を付与することで省エネルギー化に、優れた機械特性を付与することで材料やそれを使った部品や機械を長寿命化させ、省資源化に寄与できる技術である。また、生体適合性や耐久性などを付与することでインプラント製品など医療機器の耐久性・信頼性を向上し、欧米に立ち遅れている我が国の医療機器市場を創出するキーテクの一つと期待されている。そうした表面改質技術とその開発を支援する各種試験・評価技術の発展によって、医療やグリーンエネルギーなど我が国の新たな産業の確立が促進されることを願う。
第181回~第190回
第181回~第190回第181回 震災によるコンビナート火災を防ぐメカ技術
第181回 震災によるコンビナート火災を防ぐメカ技術屋外タンク全面火災の状況 東日本大震災を教訓にした気象庁の新しい津波警報注意報が、3月7日から運用開始された。東日本大震災の地震直後に発表された津波警報注意報では、地震の規模をマグニチュード7.9と推定して、実際の津波(宮城県・岩手県・福島県など広いエリアで10m)を大きく下回る高さが発表された。そのため住民の避難が遅れ被害を拡大させたことから、今回、気象庁では地震の規模がすぐに分からない巨大地震が発生した場合、直後の津波警報注意報では予測の精度が低いため、数字でなく「巨大」、「高い」と発表し危険が迫っているというメッセージを分かりやすく伝える手法に変えた。東日本大震災の経験を活かした津波リスク回避の取り組みに期待したい。
津波は海溝や沖合の活断層で地震が起きて海底が隆起したり沈んだりして海面が大きく変動した際に発生する波をいう。そのため沿岸にある施設への被害は甚大で、東日本大震災の津波でも石油タンクが被害を受け膨大な油が流出したが、タンクの炎上もあった。気仙沼湾岸では石油タンク23基のうち21基が炎上した。
長くゆっくり揺れる「長周期地震動」では、石油タンク内の石油が共振して液面が大きく波打つ「スロッシング現象」が発生し、揮発防止を目的に液面に薄肉の鋼板(浮き屋根)の外周で可燃性ガスを密封するシールが追従できず、ガスが漏れ出し、またタンク上部と浮き屋根の接触による衝撃火花で発火しタンクが炎上、コンビナートでの延焼が拡大するという事故につながる。先ごろ早稲田大学・浜田政則教授らが、東海地震、東南海地震の連動時に想定される長周期地震動に東京湾岸のコンビナートが見舞われた場合に、スロッシング現象によって115基から大型タンクローリー6000台分の石油が溢れ出し、また同時多発的に火災が起きる可能性を示した。
浮き屋根式石油貯蔵タンクでは、貯蔵油にポンツーンと呼ばれる浮きが付いた屋根を浮かべた構造となっており、貯蔵油の増減に伴って屋根が上下動する。その上下動の際に可燃性ガスが浮き屋根の上部に漏れ出ることのないよう、外周にゴムシールが取り付けられている。また浮き屋根がタンク内で回転することのないよう回り止めの機構もある。
つまり浮き屋根とタンクの(上)壁との接触による火花発生、発火を避けるには、一つには浮き屋根外周シールのタンク側壁への追従性の向上が求められる。可燃性ガスの漏洩防止だけでなく、浮き屋根の異常な上下動も抑制できる。現在は耐油性や摺動特性などに優れるニトリルゴム(NBR)や、その反発力に基づく圧着によるシール性を発揮するウレタンフォームなどが用いられるが、異常な上下動に耐える機械的特性とさらなる追従性(シール性)が求められよう。
もう一つは、浮き屋根とタンクの壁が接触した際に火花が散ることのない表面を装飾することが考えられる。以前、タンク内の清掃時に摩擦による発火事故などの対策として、メカノケミカルポリシングなどによってタンク内の表面粗さを制御して静電気や火花の発生を抑えようという研究があったが、加工や表面改質による表面特性の制御を検討しても良いと思う。先日埼玉県和光市の理化学研究所で開催されたトライボコーティングシンポジウムで三愛プラント工業から発表があった「真空装置用各種金属材料の精密化学研磨技術」などもタンク内の部材を超平滑化する技術として応用できるかもしれない。
東日本大震災の悲劇から2年を迎えたが、依然として復旧のスピードは緩慢だ。それでも天災、人災の怖さを経験し、いつ訪れるかわからない災害に対して多方面からの備えを急がなくてはならない。新しい津波警報注意報のような人災を回避するシステムと、転載に備える信頼性の高い堅牢なメカ技術に期待したい。
第182回 INTERMOLDなど開催、高品質な日本の金型を支える表面改質技術
第182回 INTERMOLDなど開催、高品質な日本の金型を支える表面改質技術展示会のもよう 今月17~20日、東京・有明の東京ビッグサイトで日本金型工業会が主催する「INTERMOLD2013(第24回金型加工技術展)」「金型展2013」、日本金属プレス工業会が主催する「金属プレス加工技術展2013」が開催され、四日間で約46000人を動員した。2011年は東日本大震災の発生により開催が中止になったため、東京での開催は4年振り。当日は工作機械・機器メーカーや、切削工具、CAD/CAM、CAE関連、測定機器、表面改質技術、金属プレス加工事業者などが一堂に会した。
5軸加工機やレーザ加工機を中心に最先端の工作機械4機種を展示することで、最新の金型加工技術を紹介した森精機製作所は、工程集約や被削材、ワークなど様々な観点から金型加工の効率化を実現する技術を紹介した。「HSC 55 linear」は、高速主軸とリニアドライブが特長の5 軸制御マシニングセンタで、リニアドライブによる最高80m/minの高速送りにより切削送り速度を高め、切削加工でありながら研削加工に匹敵する面粗度Ra 0.23μmを達成していることなどをPRした。また、CNC旋盤「NLX2000SY/500」では、旋盤でありながら多彩なツーリングを使用し、旋削・ミーリング加工の工程集約を披露した。回転工具主軸の最高回転速度は 10000 min-1を達成し、マシニングセンタに匹敵するミーリング加工を実現した。
金型の生産では、アジア地域の台頭もあり加工技術の平準化が進展している。そんな中、日本国内では高度な技術、緻密な品質管理による高い信頼と品質などで優位な立場を維持している。そうした要求に応える工具として、日進工具では精密・微細加工分野を得意とするエンドミルを紹介。今回、金型材料として期待されている超硬合金への直彫り加工用エンドミルとして、PCDボールエンドミル「PCDRB」を発表。また昨秋に販売を開始したPCDスクエアエンドミル「PCDSE」や各種cBN小径エンドミルシリーズなど、付加価値のものづくりに貢献する各種小径エンドミルを展示した。
ナノコート・ティーエスのブース 表面改質関連は、コーティングメーカーとしてナノコート・ティーエスが「セルテスDCY」を発表。新プラズマ源採用により180℃以下の低温でDLCコーティングが可能で、PVDとプラズマCVDのハイブリッドプロセスにより高密着を実現した。また、鋼と強い密着力のCr系下地層と、靱性に富んだバッファー層で耐荷重性・耐衝撃性が向上し、高面圧・繰り返し衝撃でもはく離しないとした。清水電設工業は、硬さHv3500の耐摩耗性と耐熱性に優れた「ZERO-1」コーティングを中心に、各種コーティングを冷間鍛造や冷温間プレス、抜き金型などの用途に向けて提案した。
新東工業のブース こうしたコーティングの下地処理として使用される各種ブラスト技術も紹介された。東洋研磨材工業は、エアを使わず遠心力を応用した噴射加工マシン「SMAP」を紹介した。複雑な三次元異形状の鏡面仕上げおよび微細加工における微小バリ取りと外周面のエッジ仕上げが行える。また不二機販では、金属に微粒子を高速衝突させることで疲労強度向上を向上させる「WPC処理」を紹介。金型の疲労寿命延長や耐摩耗性・耐チッピング性の向上、応力腐食防止などに貢献するとした。新東工業はダイカスト金型において、製品の不良低減技術として「D-FLOW」、ヒートチェック寿命向上技術として「D-CHECK」、応力腐食割れ寿命向上技術として「D-SCC」と、必要な機能に対してそれぞれショットピーニングの受託加工を提案した。
製造業の海外移転、韓国や中国を始めとするアジアの金型産業の躍進により、日本の金型産業は低迷を強いられている。しかし、表面改質をはじめとした高い技術を適用することで付加価値を高め、日本国内での金型の生産量増加、かつ海外製品の受注増加が期待される。
第183回 医療の緩和推進で期待される医療機器市場
第183回 医療の緩和推進で期待される医療機器市場MEDTEC JAPAN 2013のもよう 安倍政権の規制改革会議は先ごろ、中間報告をまとめ、健康・医療、エネルギー・環境、雇用、創業等という4分野で規制を緩めるよう求めた。医療機器に関わる規制改革の推進では、欧米等の医療機器先進国に比べ医療機器の実用化の遅れ「デバイス・ラグ」が大きいわが国で、健康に長生きしたいという国民の期待に応えるためには、医薬品とは異なる医療機器の特性を踏まえた制度を構築し、いち早く先進的な医療機器を国民に届けることが必要、と述べ、現在検討中の薬事法改正法案を踏まえ、さらにわが国の医療機器産業を発展させる観点から、認証基準の見直しや計画的な策定をはじめとする種々の改革を求めるとした(主な検討項目:医療機器に関わる認証基準、医療機器に関わる保険制度、医療機器に関わる登録認証機関)。
本稿では、こうした中、先ごろ開催された医療機器の設計に関する展示会・セミナー「MEDTEC JAPAN 2013」と「BIO tech 2013」の出展を通して、医療機器を支える要素技術を紹介する。
工作機械技術
医療機器、特にチタン・チタン合金など生体適合性のある材料が人工歯根や骨折固定用プレート・スクリュー、人工股関節などに多用されている。チタンは欧州で数千万トンの需要があるのに対し、日本では100~200万トンと推察されるが、増加傾向にあるという。しかし、チタンは難削材であり、医療機器では高精度を保持しながら生産性を高め、製品競争力を高めることが求められている。
森精機製作所では、たとえばチタン製骨プレートを10μm以下の精度と表面粗さRa0.3μmで完全加工できる5軸装置を出展した。生産性の面から主軸回転数は2万rpm程度が一般的だが、4万rpm程度が可能な装置も開発しており、精度と生産性を維持するのに、加工工具も適宜推奨しているという。
加工工具
チタン合金の難削性を示す材料特性としては熱伝導率が低く、切削温度の上昇が大きい。化学的に活性であり、工具材との親和性が高い、鋸刃状の切りくずを生成し、切削抵抗の変動による切り刃のチッピング、欠損を引き起こすといったことが挙げられる。そこで切削熱を逃がすコーティングなどを施した超硬エンドミルなどが用いられる。これに対し、日立ツールでは潤滑性・耐熱性・耐摩耗性に優れたコーティングを施したエンドミルを紹介した。
インプラント機器向けコーティング
上述のようなインプラント機器を加工する技術だけでなく、インプラント機器の生体適合性を高めるコーティング技術も紹介された。
市販のステント(薬剤溶出型)は、薬剤コーティング層の金属基材との接着性や、薬剤が完全に放出された後のステントの生体適合性などに問題があり、ステント基材の表面機能の見直しが急務となっている。これに対しトーヨーエイテックでは、ステントの生体適合性を高めるDLCコーティングを開発しているが、用途別に被膜を細分化、フレキシブルDLCや超親水性DLC、耐熱DLCなどを紹介した。
医療機器では機器表面を保護するとともに、生体適合性を持たない機器材質を人体組織から完全に遮断するため、安全で信頼性の高いコーティングの適用が不可欠となっている。機器とコーティングの生体適合性を見るには、細胞毒性や感作性、刺激性/皮内反応性、急性毒性、血液適合性、体内埋込みなどのISO-10993生物学的評価要件をクリアする必要がある。日本パリレンでは、これら要件をクリアしたパラキシリレン系ポリマーコーティング「パリレンC」などを紹介した。ステントや人工関節、ペースメーカー、人工心臓など幅広く適用され、パリレン気相蒸着重合(VPD)の成膜装置なども受注が増えてきているという。
溶射メーカーのトーカロでは、歯科用インプラントでは人工歯根としてチタン、アパタイト材料などを用いたプラズマ溶射などで実績を持つが、さらに人工股関節などへの適用としてプラズマ溶射による多孔質チタンコーティングを紹介した。溶射プロセスを使用することで気候率を10~50%程度にコントロールすることで、多孔質コーティングと生体骨が強固に結合できるという。
医療機器の出荷額は、平成13年に2兆2900億円だったのに対して、平成23年には2兆8300億円と拡大基調にある。すでに経済産業省は、中小企業のものづくり力を活用した医療現場の課題解決に資する医療機器の開発・改良を促進し、もってわが国における医療の質の工場とモノづくり産業の新たな事業分野の開拓を目的とした「課題解決型医療機器等開発事業」を平成22年度補正予算から実施しているが、今回の規制改革会議の中間報告を受けて、医療機器分野での規制緩和が進み、これによって医療機器の開発が加速され、わが国の医療機器市場の拡大が助長されていくことに期待したい。
第184回 人とくるまのテクノロジー展2013でEVから表面改質技術までを展示
第184回 人とくるまのテクノロジー展2013でEVから表面改質技術までを展示自動車技術会は5月22~24日、横浜市西区のパシフィコ横浜で第22回自動車技術展「人とくるまのテクノロジー展2013」を開催、475社(986小間)で製品・技術の展示が行われた。
SIM Driveが展示を行った「SIM CEL」 車両展示では、電気自動車(EV)ベンチャー企業のSIM Driveが一般向けには初公開となる試作EV「SIM-CEL」を展示。0から100km/h加速4.2秒という加速性能の他に、世界最高レベルの効率となる電力消費量を実現した車両を紹介した。また、先行開発車事業第3号参加企業の中からは宇部興産がPP製樹脂製の軽量、高剛性が特徴の「ツインコーン」など、三五がハイドロフォーミング加工による軽量高剛性スティールスペースフレームなど、GMBが電動式ウォータポンプやサスペンションなど、大同工業が軽量化部材など、日本特殊陶業がハブベアリング向けに供給したSiN(窒化ケイ素)製のボールなどのパネル出展を行い、SIM-CELに実際に搭載されている新しい技術を紹介した。日産ブースでは、同社が省エネ大賞・経済産業大臣賞を受賞した「LEAF to Home」電力供給システムや1.2GPa級高成形性超ハイテン材を使用した車体骨格モデル、エルグランドに搭載した世界初の新技術「踏み間違い衝突防止アシスト(駐車枠検知機能付)」等の最新技術を展示し、同社の環境、安全への取り組みを紹介した。
東洋ドライルーブは、二硫化モリブデンやグラファイト、フッ素樹脂等の潤滑物質と各種バインダーを配合し、各種溶剤または水に分散させた有機結合型の機能性被膜を紹介。自動車業界で多数実績のある固体被膜被膜潤滑剤として処理を行った様々な部品の展示を行った。スルザーメテコジャパンでは最新の溶射装置、溶射ガンおよびサンプルを展示。欧州等で豊富な実績を誇るスルザーメタプラスのPVD/DLCサンプルや、スルザーフリクションシステムズのシンクロナイザーリングおよび摩擦材の展示と技術紹介等を行った。フランスパビリオンの一角として出展したH.E.Fグループは、耐摩耗性や耐食性を高める塩浴軟窒化処理「タフトライド処理」やPVDプロセスによるDLCコーティングの処理品をサンプル展示し、日本国内でも同グループの技術を導入した企業による受託加工が可能であるとPRした。
日本自動車工業会が公表している2012年度の国内需要は5,210,291台で、前年度の4,753,273台に比べ9.6%の増加となり、2年連続で前年度を上回った。生産拠点の海外移転が進んでいるとはいえ、依然として自動車産業は裾野が広く我が国産業の中枢であるといえる。近年、HEVやEVに加えてFCV(燃料電池車)などの開発も進んでおり、これらに関連する要素技術も多岐に渡る。機械要素技術に関わる中小製造業としては、自動車に求められる高度な研究・開発能力をさらに高めた上で、他産業への応用を進めていくことが望まれる。
第185回 表面改質展2013開催、機能性付与や耐久性の向上で市場拡大狙う
第185回 表面改質展2013開催、機能性付与や耐久性の向上で市場拡大狙う表面改質展2013のもよう
日刊工業新聞社の主催する表面改質展2013が5月29~31日の三日間、大阪市・南港北のインテックス大阪で開催された。トーヨーエイテック 表面処理事業部 主幹の中谷達行氏が「自動車から医療へ。表面改質の大いなる可能性」と題して特別講演を行ったほか、富士高周波工業が「レーザクラッディングとレーザ焼入れ」、ハウザーテクノコーティングが「ハウザーのPVDコーティング技術」、八田工業が「真空熱処理について」などの出展者によるワークショップが館内で行われた。展示会では、同時開催の微細・精密加工技術展と併せて、自動車部品や電機部品の機能性向上や、金型・工具の耐久性向上等の目的で使用される表面改質技術が多数紹介された。
エア・ウォーターNVのブース 熱処理では、エア・ウォーターNVが自動車・部品メーカーを中心に採用が進んでいる「NV窒化」を紹介。ガス活性化(フッ化)処理とガス窒化処理を組み合わせることにより、400℃~600℃と幅広い温度設定が可能で、炭素鋼や低・高合金鋼、ステンレス、鋳鉄、Ni基合金等と適用鋼種が広いことをPRした。また、各熱処理分野に特化し東海地方を中心に活動している4社共同体の「金属熱処理ソリューション(幹事会社:菱輝技術センター)」は、真空処理、塩浴処理、高周波処理、浸炭処理、窒化処理の専門家集団が素材選択から熱処理、仕上げまでトータルに加工を提案できる体制で品質や納期、コストの問題を解決する、とした。今回の展示会を機に関西圏での受注を目指すという。TD処理を専業でとしている豊島技研では、自動車メーカーの金型を中心に同処理を行っている強みを活かし、他社に比べて短納期で処理できることや寸法精度の変化が少ないことなどを強調し「PVDコーティングの代替処理としても適用が可能」とした。
丸紅情報システムズから参考出品されたULF-Bコートのサンプル コーティングでは、丸紅情報システムズが従来から行っている高硬度のDLC(Diamond‑Like Carbon)コーティング「ULFコート」に加えて、「ULF-Bコート」を参考出品した。ULFコートは炭素のみで構成され、sp3比率が高くHV6500と高硬度のta-c(tetrahedral amorphous carbon)構造だが、ULF-Bコートはsp2比率が高く硬度がHV1500のa-c(amorphous carbon)構造だという。用途としては、クロムめっきやニッケルめっきなど黒色の表面処理の代替処理や高硬度を必要としない精密機械部品や光学系部品をターゲットに受託加工の検討をしているという。また、日本電子工業 大阪工場では、DLC膜にシリコンを含有し高い密着性と摺動性を実現した「NEO Cコーティング」やセラミックコーティングの受託加工を紹介した。コーティング装置では、ハウザーテクノコーティングが最新のアーク成膜技術として「CARC+」や各種PVDコーティング装置の紹介を行ったほか、シーケービーが独・VTD社のPVDコーティング装置「DREVA600」によるコーティングサンプルを展示した。
不二機販(左)とオカノブラスト(右)のブース コーティングなどの前処理として行われるブラスト関連では、不二機販とオカノブラストが出展。前者は精密ショットピーニングとして従来の硬度アップを目的とする表面処理のほか、摺動性の向上、疲労寿命の延長、 耐摩耗・耐ピッチング性の向上などサンプルを展示して提案を行った。後者は、精密ショットピーニングにより処理された機械部品や金型、工具をサンプル出品したほか、樹脂成形用金型におけるラッピング技術やブラスト処理によるバリ取り技術を紹介した。このほか、三愛プラント工業は大物配管などの酸洗浄や、真空装置部品など先端技術で使用されている精密洗浄や電解研磨、化学研磨について紹介。三恵ハイプレシジョンでは、遠心力を利用して精密なバリを取る揺動式遠心バレル研磨機を出展した。研磨用のタンクを回転テーブル上に傾斜させて設置し、揺動するように回転させることにより、被加工物が常に水と研磨材に囲まれ、傷や歪みが抑えられる処理を実演した。
テレビ報道や一般紙などではアベノミクス効果による景気回復が喧伝されているが、会場で話を聞いた限り、中小企業が大勢を占める表面改質関連企業では、まだその恩恵に与る企業は少ない。特に、熱処理を生業とする企業は、電気・ガス料金の値上げなどのエネルギーコスト増大により、苦しい経営が続いている。また今回会場となった大阪ではエレクトロニクス産業の不振により、製造業そのものの生産量が減少している。こうした展示会で各分野に向けて表面改質の有用性を訴えることにより、全体のパイを広げていく努力をすることが今後の表面改質の展望を明るくするものと思われる。
第186回 第17回機械要素技術展開催、部品や金型などの精度・性能を高める技術
第186回 第17回機械要素技術展開催、部品や金型などの精度・性能を高める技術軸受や直動案内機器、歯車などの機械要素や、金属や樹脂などの材料とその加工技術、表面改質技術やそれらの計測・評価技術に関する専門技術展「第17回機械要素技術展」が6月19~21日、東京・有明の東京ビッグサイトで開催された。メンテナンスフリー化を図る軸受や直動案内機器の技術、エッジ品質を向上し部品や金型の精度や性能を高めるバリ取りなど加工技術、部品や金型の性能を高める表面改質技術などの最新の製品技術が出展された。
直動案内機器のメンテナンスフリー技術
軸受や直動案内機器など摺動する箇所では、一般に摩擦を軽減する潤滑油やグリースが必要となる。しかし食品機械や半導体製造プロセスなど潤滑油の使用を避けたい用途や、潤滑油の補給が難しい用途では、潤滑油剤を用いずに稼働することが求められる。
THKのブース THKでは、直動案内にボールリテーナを採用するとともに、ボールねじに潤滑装置QZを採用した電動アクチュエータを出展した。潤滑装置QZは、ボールねじ軸の転動面に適切な量の潤滑油を供給、ボールと転動面の間に油膜が常に形成され、潤滑性の向上とメンテナンス間隔の大幅な延長を可能にするという。 日本トムソンでは、熱硬化形固形潤滑剤「Cルーブ」を充てんした直動案内を出展した。Cルーブは、多量の潤滑油と微粒子の高分子ポリオレフィン樹脂を熱処理固形化した潤滑剤で、直動案内の稼働とともに潤滑剤が軌道面に常時適量しみだし、長時間にわたって直動案内の潤滑性能を維持する。
高精度部品・金型を作る加工技術
機械要素技術展では軸受や直動案内など部品や金型の精度や品質を高める様々な加工技術が紹介されたが、中でもエッジ機能を満足させるためのバリ取り・エッジ仕上げ技術が多数出展された。
三共理化学のブース 三共理化学では、バリ取りのほか、はく離、粗し・下地処理、研磨などに適用できる「ブロワ式ブラスト装置」を提案した。研磨メディアを変えることで微細バリだけを除去できるほか、薄膜、塗膜のはく離、溶接焼けなどの研磨処理、さらには下地処理として面粗度を調整することでコーティング膜の密着性を向上させる役割を果たすという。また、コンプレッサー式に比べて電気消費量が70%削減できる省エネ性、付帯設備・機器が不要なため省スペース性に優れている点などを強調した。同社はこのほか、精密研磨材「ミラーフィルム」や「ラッピングフィルム」などの展示を行ったことで、来場者からは研磨全般についての相談が寄せられた。スイス・イエプコ社のブラスト装置を取り扱うプラストロンは、粒子を吹き付けることで微細なひびや空孔を閉塞させて金型や部品等、金属表面の平滑化・緻密化を行う処理を実機を展示して紹介した。この工程で、トリボフィニッシュ処理と呼ばれる専用の粒子を使用すると表面にすべり性が付与され、金型などの離型性向上やかじり・チッピング防止につながるという。
コーティングなどの表面改質技術
表面処理・改質フェア 表面改質関連技術としてコーティングでは、日本コーティングセンターが親会社のトーカロと共同出展し、耐摩耗性に優れたPVDやDLCコーティングのサンプルを展示したほか、新技術として超硬基材上のTi系被膜の除膜を紹介、表面粗さの変化が少ないことをPRした。アルバックテクノは、硬質アルマイトにフッ素樹脂を複合させた「タフラム」をアルミニウムおよびアルミニウム合金に適用することで、耐摩耗性・摺動性の向上やかじり防止などの特性に加えて電気絶縁性、離型性、耐食性の機能付与が可能とした。同じく硬質アルマイト被膜である「イーマイトUH処理」の紹介を行った熊防メタルは、従来の硬質アルマイトよりも1.7倍の硬度(HV600以上)を有し、耐摩耗性および耐熱・耐クラック性に優れることから半導体や医療関連などの幅広い分野に適用できるとした。
パルメソのブース 表面改質の試験・評価技術では、パルメソが薄膜などの表面改質層から基材までを連続して精密評価する「MSE試験法」を紹介。展示では、DLC薄膜や樹脂系材料の試験事例のほか、このほど新たに可能になった鉄鋼系の焼入れ材の硬さと摩耗率の相関を測定した結果をパネルにして展示。研磨で削りながら表面を摩耗させることで、深さ分解能100nmごとに硬さと摩耗率の相関を高精度に測定できる。同社では国内で唯一同試験の受託測定を行うとともに、装置の販売も行っていることを強みに来場者にPRを行った。
第187回 JASIS2013開催、新ビジネスを支える試験・評価機器
第187回 JASIS2013開催、新ビジネスを支える試験・評価機器JASIS2013のもよう 日本分析機器工業会と日本科学機器協会は9月5日~7日、千葉市の幕張メッセ国際展示場で、「JASIS2013」(旧・分析展/科学機器展)を開催した。今回は「未来発見。-Discover the Future-」をテーマに、医療やバイオ、環境などを中心に、「イノベーションを生み出し将来のビジネス発展につなげるための材料や表面改質層の開発を支える分析装置や試験装置などが多数展示された。
新東科学のブース 環境ビジネスの一つのテーマとして、省エネルギー・省資源があるが、この省エネ・省資源につながる材料特性としては、摩擦・摩耗特性(トライボロジー特性)がある。このトライボロジー特性を評価する摩擦・摩耗試験機では新東科学やCSM Instrumentsなどが出品したが、新東科学では荷重変動型摩擦摩耗試験システムトライボギア「TYPE:HHS2000/3000」を出展、1個の試験片による1回の測定で摩耗回数、垂直荷重、摩擦力、摩耗体積の関係を示す3次元摩耗形態グラフ作成、摩耗の遷移に対応する臨界荷重を決定ができるため、複数の試験片を必要としないだけでなく、試験時間を大幅に短縮し、煩雑なデータ解析を解消できつつ、信頼性の高い試験データが得られる。これによりユーザーの材料やコーティング開発の期間短縮が図れることを提案した。
堀場製作所のブース トライボロジー特性に優れるコーティングの一つに、ダイヤモンドライクカーボン(DLC)膜があるが、堀場製作所ではこうした薄膜の測定や分析に有用な装置を出展、分光エリプソメータ「UVISEL 2」では、非接触・非破壊で薄膜試料にダメージを与えることなく高感度に膜厚や屈折率を測定でき、DLCを分類・評価できる可能性について、グロー放電発光表面分析装置(GD-OES)「GD-Profiler 2」では、前処理なしで薄膜試料中の元素分析を数10ppmオーダーの感度、深さ方向数nmの高分解能で迅速に行えることなどを示した。
各種の機能性薄膜が登場する中で、母材の物性に影響されず、薄膜の機械的特性のみを評価する手法にナノインデンテーション法があるが、この評価装置であるナノインデンターはオミクロン ナノテクノロジー ジャパンやCSM Instruments、東陽テクニカなどから出品された。
オミクロン ナノテクノロジー ジャパンのブース オミクロン ナノテクノロジー ジャパンは、ダイヤモンド圧子を使用し600℃以上の加熱測定が可能な高温ナノインデンテーション装置「高温ステージ xSol 600付き TI 950 」を紹介、インデンテーションによる硬さ・弾性率測定はもとより、スクラッチ機能による膜の密着強度、圧子を動的に振動させる粘弾性測定で貯蔵・損失弾性率・tanδ等、多種のオプションを取り付けることが可能で、セラミックスコーティングなど各種薄膜の物性への温度依存性の評価などにも有用であることを示した。
CSM Instrumentsのブース また、CSM Instrumentsはナノインデンテーション試験のデモンストレーションを交えて、各種ナノインデンターを紹介した。現在、800℃対応の高温ナノインデンターを開発中であることや、最近開発された「バイオインデンター(BioUNHT)」が、超低荷重と大きな深さ方向の変位が可能なことから、バイオ材料だけでなくソフトマテリアルの評価が可能であることを示した。
新ビジネス、たとえば医療ビジネスの我が国における産業規模はまだそう大きくないが、国が注力する長期的な成長分野の一つである。そうした新分野における材料および表面改質層の開発では、紹介したような試験・評価機器による信頼性の高い評価データは不可欠である。各種の試験・評価機器の有効な活用を通じて、わが国が発信する新ビジネスが一つでも多く生まれることを、強く期待してやまない。
第188回 東京モーターショーが開催、世界にまだない、部品・材料技術を発信
第188回 東京モーターショーが開催、世界にまだない、部品・材料技術を発信第43回東京モーターショー2013のもよう 日本自動車工業会( http://www.jama.or.jp )は11月22日~12月1日、東京・有明の東京ビッグサイトで「第43回東京モーターショー2013」を開催した。乗用車、商用車、二輪車、カロッツェリア、車体、部品・機械器具関連製品、自動車関連サービス、SMART MOBILITY CITY 2013を含む総合ショーとして開催。世界12ヶ国から合計177社180ブランド(展示面積38239m2)が参加、すべての国内自動車メーカー14 社・15 ブランドが出展し、海外からは18 社・20 ブランド(乗用車・商用車・二輪車)が出展した。
今回のショーテーマは「世界にまだない未来を競え。」で、環境、安全、エネルギーなど世界の様々な問題を解決するハイブリッド車(HEV)や電気自動車(EV)、燃料電池車(FCV)など新しいエコカーを、日本のお家芸の部品・材料技術を含めて世界に向けて発信した。
実用化目前、FCVの軽量・高耐久材料
トヨタ自動車「FCVコンセプト」 トヨタ自動車では、2015年に市販予定のセダンタイプの次世代燃料電池自動車(FCV)のデザインコンセプト「FCVコンセプト」を出展した。床下に小型・軽量化した新型の燃料電池(FCスタック)や70MPaの高圧水素タンク2本を搭載している。このFCスタックは、実証実験車「FCHV-adv」に搭載されているものの2倍以上となる出力密度3kW/Lを実現している。セル数を削減し小型・軽量化したが、高効率の昇圧コンバータを搭載することで、モータージェネレーターの大出力化と小型化を実現した。タンク質量あたりの水素の貯蔵量を示す貯蔵性能(wt%)と世界最高水準の水素タンクは、ポリアミドなど水素を透過させない内部構造と、カーボン材複層による外部構造で、実際には100MPaの高圧に耐えるほか、米国仕様として、銃弾にも耐えるという。約3分で水素をフル充填でき航続距離が500km以上という実用性能の一方で、水素ガスが満タンであれば一般家庭の使用電力(10kWh)を1週間分以上供給できるなど、非常用電源としても提案された。
走りを改善するEVのインホイールモータ―技術
日産自動車「ブレイドグライダー」 日産では、三角翼をイメージしたEVコンセプトカー「ブレイドグライダー」を出展した。ドライバーがクルマの中心に座り、その後方に2人用シートを配置した3人乗り。シャシーはカーボンファイバー製で軽量化を図った。リチウムイオンバッテリーでリアタイヤに搭載した左右独立制御のインホイールモーターを回して駆動することで、コーナーリング性能を向上させた。
NTN「Q‘moⅡ」 このインホイールモーターでは、ベアリングメーカーのNTNが、モーターと減速機を一体化してホイール内に配置することでモーターの駆動力をタイヤに直接伝達して高効率化を図るとともに、車両の軽量化などに貢献する小型インホイールモーター「IWM」を開発している。その特徴を実証するために今回、4輪すべてにIWMを組み込み、左右輪を転舵する新しいステアリング装置を搭載したコンセプトカー「Q‘moⅡ」をデモし、その場回転や横方向移動を披露した。小型モビリティなど次世代EVに向けてシステムを提案した。
HEVの高出力・高効率化を実現する軸受・材料技術
ホンダ「新型NSXコンセプト」 ホンダは、軽量なボディに次世代の直噴 V型6気筒エンジンをミッドシップレイアウトで配置するとともに、走りと燃費性能を両立した高効率・高出力のハイブリッドシステムを搭載した新しい走りの価値を提案するスーパースポーツモデル「新型NSXコンセプト」を出展した。新型ハイブリッドシステムは、エンジンと高効率モーターを内蔵したデュアル・クラッチ・トランスミッションを組み合わせるとともに、前輪の左右を独立した二つのモーターで駆動する電動式の四輪駆動システムを搭載している。ハイブリッド車(HEV)の出力向上、燃費向上では、小型・軽量化を実現する駆動用モーターとそのトルクを高めるリダクションギヤ、駆動用モーターに大電力を供給する発電機用モーターの高速回転化が進められている。
日本精工のブース このHEV用モーターの高速化、小型化に伴い、プラネタリ機構向けのピニオンギヤには、さらなる高速回転への対応のニーズが高まっている。これに対し日本精工では、保持器に特殊皮膜を施した超高速プラネタリ用ニードル軸受を開発、出展した。軸受の保持器の母材であるクロムモリブデン鋼に浸炭窒化処理した後、特殊皮膜を施すことで、ピニオンギヤと保持器の摺動部における摩擦熱を低減させ耐摩耗性を向上、この結果ピニオンギヤの対応可能な回転速度を超高速プラネタリ用ニードル軸受標準品に対し約2倍、高速仕様に対し約1.5倍に高速化させた。これにより変速機の効率化を図った。
ハイブリッド車やアイドリングストップシステムでは、エンジンが頻繁に起動・停止されることから、またエンジン油が低粘度していることから、エンジンベアリングなどの摺動部では油膜が形成されにくい。これに対し大豊工業では、固体潤滑剤である二硫化モリブデンとポリアミドイミド樹脂からなる樹脂コートエンジン軸受を出展、油膜が形成されずに固体接触した場合の摩擦低減の効果(起動摩擦トルク20%減)と耐摩耗性(起動停止摩耗量60%減)を示した。この起動・停止の潤滑性保持のコーティングでは、大同メタル工業はダイヤモンドライクカーボン(DLC)膜も提案した。
自動車メーカーでは環境、安全、エネルギー問題への対応が必至で、特に今回の出展では、資源に乏しい日本では無尽蔵な水素をエネルギーとするFCVが実用化レベルの形で示された。しかし本質的なテーマとして、自動車メーカーの走りへのこだわりは強い。今回提示された新しい形の車が、日本のお家芸である部品・材料技術のバックアップによって、走りを楽しむ車として世界市場に登場していくことを確信している。
第189回 ASTEC2014/SURTECH2014開催、医療・環境・エネルギーを支える表面改質・評価技術を提案
第189回 ASTEC2014/SURTECH2014開催、医療・環境・エネルギーを支える表面改質・評価技術を提案展示会のもよう 「nano tech 2014 第13回 国際ナノテクノロジー総合展・技術会議」や「ASTEC 2014 第9回 先端表面技術展・会議」、「SURTECH2014 表面技術要素展」などの展示会が、1月29日~31日に東京・有明の東京ビッグサイトで開催、約46000名が来場した。
ナノテクノロジーは情報通信、エレクトロニクスから医療・健康、バイオ、環境・エネルギーまで、様々な重要課題解決のキーとして注目されるが、いずれの展示会においても、特に日本の新産業として注目される医療や環境、新エネルギーの技術革新を支える新技術や新製品が披露された。
特にASTECとSURTECHでは、ダイヤモンドライクカーボン(DLC)コーティングやセラミックコーティングなどのドライコーティングから、めっきなどの環境対応の表面改質技術や、その処理による材料の機械的特性などを評価する硬さや密着性、摩擦・摩耗特性などの試験・評価技術などが紹介された。
パーカーグループのブース パーカーグループのブースでは、パーカー熱処理工業が、韓国J&L Tech社製の新型ハイブリッドPVDシステム「CarboZenシリーズ」を出展した。リニアイオンソース(LIS)、UBMスパッター(UBMS)などプラズマ源の適切な組み合わせにより、耐摩耗、高潤滑、高耐食など適切なDLC膜を成膜できる。CarboZen 1000は6ポート(LISが4ポート、UBMSが2ポート)まで、CarboZen 1200は8ポート(LIS、UBMSが各4ポート)、プラズマ源を配置でき、膜の多彩化や成膜効率の向上などが図れるという。
ナノテックのブース ナノテックでは、DLC薄膜を機能別、用途別に分類した「ICFコーティング」(真性カーボン膜)を紹介するとともに、大電力パルススパッタリング(HiPIMS法)によって高機能水素フリーICFを660nm/minの超高速で成膜できるRoll to Roll成膜装置を紹介した。丸紅情報システムズは、ユニオンツールが開発したDLCコート/ダイヤモンドコート「ULFコート」の受託サービスを提案した。特に、内部応力を緩和しながら高硬度の成膜を実現、従来のULFコートに比べ、鉄系素材に対して耐摩耗性を3割向上させた水素フリーDLC膜「ULF-S」を処理サンプルとともに紹介した。自動車や機械の摺動部品に適用することで、低フリクション化やロングライフ化が可能になると強調した。
日本マクダーミッドのブース めっき関連技術では今回も、有害な重金属としてRoHS指令やELV規制などで規制の進む六価クロムの代替技術が多く紹介された。日本マクダーミッドは、六価クロム化合物を含まない耐食仕様のめっき群、ZinKladシステムを紹介した。同システムは亜鉛/亜鉛合金めっき~三価クロム化成処理~トップコートまでを組み合わせたRoHS指令やELV規制適合のシステムで、GMやフォードなど厳しい塩水噴霧試験をクリアし採用されているという。
アントンパールのブース また、コーティング薄膜の評価装置も多数出展された。薄膜の機械的特性評価装置を専門に扱うCSM Instrumentsは、昨年アントンパール社が買収、新しい体制のもと、薄膜やコーティング表面の機械的特性、たとえば密着性や破壊特性、変形特性などを評価するための専用試験機「スクラッチテスタ」や、軟質材から硬質材料、脆性材料、延性材料などほぼすべての材料について、硬度や弾性率などの機械的特性が計測・評価できる「インデンテーション・テスタ」、ほぼすべての固体材料の組み合わせについて、速度や周波数、接触圧、潤滑剤の有無、時間や雰囲気(温度、湿度や潤滑剤の種類など)といった試験パラメータが制御でき、実際の摩耗状況といった実用条件下に近い環境を再現した摩擦・摩耗試験が可能な「トライボメータ」などを出展した。
フィッシャー・インストルメンツのブース フィッシャー・インストルメンツは、AFM(原子間力顕微鏡)を追加することでナノメートル領域で高解像度の表面三次元画像を取得し、薄膜などの組織の可視化と定量化が可能となる「PICODENTOR HM500」を出展した。ピコメートル領域での高精度の距離測定や数μNまでの小さい荷重調整ができることで、極薄膜の硬質被膜の機械的物性を評価できる。
トリニティーラボのブース トリニティーラボは、台で薄膜や厚膜、塗膜などの界面特性(付着・破壊強度)と表面特性(摩擦・引っ掻き強度)が測定できる被膜性能評価システム「フィルメータ ATPro 301」を出展した。基材と膜の界面や多層膜における層間界面において、断面にピンで直線摺動させることにより外的応力を加え、膜のはく離、付着強度を測定する。また、10μmから1mm/secと極低速の速度範囲で摩擦係数を測定できるため、静止状態から摺動開始時に起こる試験体の弾性変形や摺動時の飛び跳ね現象を抑えたデータが得られる。このほか引っ掻き強度も測定が可能、摩擦係数との相関解明なども行える。
パルメソのブース パルメソは、微細な粒子と水を投射することで、サブミクロンの薄膜に対し膜厚の1/10~1/50、つまりナノメートルサイズの摩耗分解能が得られる「MSE試験装置」を出展した。薄膜や物体表面の材料強さをGD-OES(グロー放電発光分析)装置のように表面から深さ方向に連続して精密評価できるため、微粒子のサイズ・種類を変えるだけで、硬質薄膜だけでなく軟質材料にも適用できるため、工具などに使われるTiN(窒化チタン)膜やDLC膜、セラミックス、金属めっき、半導体・電子部品や樹脂被膜、ゴム表面などに幅広く適用できるという。
医療関連では先ごろ、トーヨーエイテックが、冠動脈用ステントについてステント加工とDLCコーティングの両方で医療機器製造業許可を取得した。我が国の医工連携もようやく本格化の様相を帯びつつある。今回ASTECやSURTECHで紹介された各種の表面改質は、たとえば材料に乏しい生体適合性や耐久性などを付与することでインプラント製品など医療機器の耐久性・信頼性向上を、耐摩耗性を向上することで省資源化を、摩擦特性を改善することでエネルギー消費の節減を実現するキーテクの一つと期待されている。医療、エネルギー、環境、さらには防災など我が国の新産業の柱を支える各種の表面改質技術とその開発を支援する各種試験・評価技術の発展に注目が集まってきている。
第190回 人とくるまのテクノロジー展2014開催、採用進む低フリクション省燃費技術
第190回 人とくるまのテクノロジー展2014開催、採用進む低フリクション省燃費技術自動車技術会は5月21~23日、横浜市西区のパシフィコ横浜で第23回自動車技術展「人とくるまのテクノロジー展2014」を開催、環境や安全、電気自動車(EV)やハイブリッド車(HEV)関連などのテーマを中心に出展がなされた。ここでは同展での出展技術のうち、環境、特にフリクションの低減による燃費改善に関わる技術を紹介したい。
展示会のもよう 自動車メーカーではたとえば、スズキが「ハスラー」に搭載された「R06Aエンジン」の技術を紹介した。燃費改善につながるエンジンのフリクション(メカニカルロス)を低減するため、まずはシリンダーブロックのライナー中心とクランクシャフト軸心をずらすオフセットクランク構造を採用して、膨張行程のピストンサイドフォース低減を図った。また、ピストン回りでは、スカート形状の最適化やスカート部に樹脂コーティングを施すことでフリクションを低減。さらにピストンリングでは、トップリングおよびオイルリングに摺動性能に優れるCrN(窒化クロム)コーティングを施し、フリクションを低減した。
シェフラージャパンのブース 部品メーカーでは、シェフラージャパンが直打式動弁系における表面改質によるフリクション低減の手法として、板金製メカニカルバルブリフターのカム接触面を削り、研磨に加えてCrNコーティングやダイヤモンドライクカーボン(DLC)コーティングで表面仕上げしたサンプルを展示した。同社では、水素含有DLC成膜品と水素フリーDLC成膜製品を提供している。水素フリーDLCは硬質で摩耗に強い上、水素含有DLCで問題にされるエンジンオイル中の添加剤によるDLC膜の摩耗促進の心配はないものの、内部応力の高さからストレスが加わった際の膜の剥がれや相手材への攻撃性などが懸念され、水素含有DLCが選ばれることも少なくないという。
日本ピストンリングのブース このDLCコーティングではフリクション低減を目的に、ピストンリング各社(リケン、日本ピストンリング、TPR)で量産体制が整いつつあるようだ。水素フリーで極めて高硬度のテトラヘデラル・アモルファス・カーボン(ta-C)膜なども検討され、問題となる膜の剥がれがない、内部応力のコントロールも可能になっているという。
H.E.F Durferrit Japanとナノコート・ティーエスのブース 低フリクションの表面改質関連では、H.E.FグループのH.E.F Durferrit Japanとナノコート・ティーエスが共同出展、PVDプロセスによるDLCコーティングの処理品を展示した。新技術としては、独自開発のレーザー装置によりマイクロテクスチャーを施すことで潤滑領域を最適化(流体潤滑領域にシフト)する「Micro-Textured DLC」を紹介、クランクシャフトやシリンダーライナーなどへの適用例を示した。F1などのモータースポーツではすでに実績があり、量産車に展開すべく、生産性を高めたレーザー装置を開発中という。
東洋ドライルーブのブース また、パーカー熱処理工業では、リニアイオンソースやUBMスパッターなどプラズマ源の最適な組み合わせで成膜できる「ハイブリッドPVDシステムCarboZen」を提案、基材との密着性が高く、耐摩耗、高潤滑、高耐食など多彩なDLCコーティングを成膜できることを紹介した。東洋ドライルーブは、従来から取り扱っている二硫化モリブデンやグラファイト、フッ素樹脂などの固体潤材をベースにした結合型固体潤滑被膜のラインナップを補う耐摩耗性の高い被膜として、昨年から受託事業に乗り出したDLCコーティングを紹介した。
トヨタ自動車がグループでの世界販売台数が1000万の大台を超えるなど、2013年度の自動車販売は3年連続で前年度を上回る好調を示した。生産拠点の海外移転が進んでいるとはいえ、依然として自動車産業は裾野が広く、我が国産業の中枢で、また、高度な技術で世界と戦える砦とも言える。今回紹介したようなフリクション低減による燃費改善技術をはじめ、日本がリーダーシップをとる自動車分野を牽引し続ける、革新的な技術が絶えず求められている。
第191回~第200回
第191回~第200回第193回 JASIS2014開催、新産業の創出を支える試験・評価機器
第193回 JASIS2014開催、新産業の創出を支える試験・評価機器JASIS2014のもよう 日本分析機器工業会と日本科学機器協会は9月3日~5日、千葉市の幕張メッセ国際展示場で、アジア最大の分析展/科学機器展「JASIS2014」を開催した。今回は「未来発見。-Discover the Future-」をテーマに、医療やライフサイエンス、環境など、我が国の成長産業の創出につなげるための材料や表面改質層の開発を支える分析装置や試験装置などが多数展示された。
新東科学のブース 材料や膜の摩擦・摩耗を低減することで省エネ・省資源につながる技術が盛んに開発されているが、この特性(トライボロジー特性)を評価する摩擦摩耗試験機では、新東科学やアントンパール・ジャパンなどが出品した。新東科学では汎用機として「トライボギア TYPE:14」を紹介。同品はアタッチメントを様々に変更できることから、摩擦摩耗試験だけでなく、簡単な引っ張り試験やスクラッチ試験などに対応しており、比較的安価に様々な試験を高精度に実施できるとした。また、同社では摩擦摩耗試験機の専門メーカーとして60年以上の実績を強みに受託試験を開始。正確な測定技術とともに低価格で明快な料金体系を打ち出し、自社技術の提供を行っている点などを周知した。
大塚電子のブース 低摩擦や耐摩耗性というトライボロジー特性に優れるコーティングの一つに、ダイヤモンドライクカーボン(DLC)膜があるが、大塚電子では、光干渉法と自社製高精度分光光度計により、DLC膜の非接触・非破壊、高速・高精度の膜厚測定を可能にした光干渉式膜厚計「FE-3000D」を出展した。独自の解析手法「複数点解析」を用いて、あらかじめ用意した厚みの異なる複数サンプルを同時解析することで、従来に比べ高精度にn(屈折率)k(消衰係数)を求めることができる。また、測定波長範囲を変えることで、極薄膜から超厚膜までの幅広い膜厚が測定できる。さらに、独自の顕微鏡光学系を採用することで、モニター・サンプルではなく、工具・ギヤ・シャフトなど、三次元形状のあるサンプルに被覆したDLC膜の実測定を可能にしている。
各種の機能性薄膜が登場する中で、母材の物性に影響されず、薄膜の機械的特性のみを評価する手法にナノインデンテーション法があるが、この評価装置であるナノインデンターはオミクロン ナノテクノロジー ジャパンやアントンパール・ジャパン、東陽テクニカなどから出品された。
オミクロンナノテクノロジー ジャパンのブース オミクロン ナノテクノロジー ジャパンは、フロアノイズ(装置設置時の測定ノイズ)の30nN以下を実現し、低荷重領域でも安定したデータの取得ができるHysitron社製の「TI950 Tribo Indenter」の実機を展示。SPM(走査プローブ顕微鏡)機能による表面形状像、ナノインデンテーションによる硬さ・弾性率、ナノスクラッチによる膜の密着強度、ナノウェアによる耐摩擦特性の測定機能を標準装備し、600℃以上の加熱測定が可能な高温ナノインデンテーション装置としてPRを行った。
アントンパール・ジャパンのブース また、アントンパール・ジャパンでは2012年末に買収したCSM Instruments(現CSM TriTec)製のウルトラナノインデンテーションテスターを展示した。現在、1000℃以上の高温や―50℃といった低温に対応する機種やを開発中であることや、近年開発された「バイオウルトラナノインデンテーションテスター(BioUNHT)」が、超低荷重と大きな深さ方向の変位が可能なことから、バイオ材料だけでなくソフトマテリアルの評価が可能であることなどを紹介した。
日本電子のブース 日本電子では、こうした試験・評価装置を多数取り揃え、たとえば「陽極酸化膜の分析ソリューション」として提案した。AEM(分析電子顕微鏡)やXPS(光電子分光装置)による表面・界面分析、NMR(核磁気共鳴装置)による化学状態分析、MS(質量分析計)による質量分析、FIB(集束イオンビーム加工観察装置)による資料前処理技術、FE-SEM(走査電子顕微鏡)による表面構造解析、TEM(透過電子顕微鏡)による断面構造解析といった様々な課題を解決するための装置群、アプリケーション等のトータルソリューションを提供するとした。
新産業、たとえば医療産業を、安倍政権は重要な成長産業と位置付け、育成すべく各種の政策を進めている。そうした新産業創出の基盤となる材料および表面改質層の開発では、紹介したような試験・評価機器による、材料・表面改質層の信頼性を裏付ける評価データが欠かせない。各種の試験・評価機器を有効に活用していくことで、わが国の成長産業となる新産業の創出につながることに期待したい。
第194回 JIMTOF2014に見る、加工の高効率・高精度化を支える機械要素・表面改質技術
第194回 JIMTOF2014に見る、加工の高効率・高精度化を支える機械要素・表面改質技術会場のもよう 10月30日~11月4日、東京・有明の東京ビッグサイトで「第27回日本国際工作機械見本市(JIMTOF2014)」が開催、切削・研削・研磨・プレス加工などの工作機械をはじめ、直動案内機器や軸受などの工作機器、工具、工具・金型のコーティング、加工油剤などの関連技術が一堂に会した。我が国ものづくりの競争力を高める加工の高精度や高効率加工、省エネルギー、低コスト化を実現する多軸機や複合機、その可動部を支える軸受や直動案内などの機械要素技術、切削工具や金型の耐久性を高め加工品位を高める各種コーティング技術も多数出展された。
NTN「工作機械主軸用空冷間座付軸受」 加工の高効率化は、工作機械において工具主軸の高速回転と送りの高速化で実現される。工作機械の主軸は、難削材や金型、複雑形状部品、医療機器部品などの加工で、高剛性・高速回転が求められる。特に近年の工作機械は多様なワークに対応するため、1台で複数の加工機能を持つ5軸加工機や複合加工機が主流で、加工機能の向上に伴い、主軸用軸受には剛性をより高めた超高速回転のニーズが高まっている。これに対しNTNでは「工作機械主軸用空冷間座付軸受」を開発、材料や熱処理の改良、内部設計の変更、潤滑面の改善などの従来のアプローチではなく、主軸の発熱低減に着目し、独自の空冷技術を用いた「空冷間座」を適用している。これにより、内外輪の温度差を抑制することができ、従来品(超高速アンギュラ玉軸受)と比べ高速回転性能が20%向上、エアオイル潤滑・定位置予圧でdmn値210万を達成し、世界最高水準の高速回転性能を実現した。軸受内径φ70、回転速度23000min-1(dmn値210万)において、従来品は組み込み後軸受内部に予圧を与えることができなかったが、開発品は最大1300Nの予圧を確保でき、組み込み時における主軸の剛性を大幅に高めることで、幅広い速度域において加工性能の向上に貢献する。さらに、主軸を冷却するエアにより発生する騒音については、「空冷間座」の内部設計を工夫することで騒音値の上昇を抑え、従来の「環境対応型エアオイル潤滑アンギュラ玉軸受」と同水準を維持している。
日本精工「工作機械用高機能ボールねじ」 送りの高速化(高速送り)では、近年、ボールねじ自体の発熱を低減することで強制冷却を省略したい、ボールねじの運動誤差を小さくしてさらなる高精度に対応したいという要望が増えてきた。これに対し日本精工では、設計面、生産技術面からボールねじの予圧・剛性・発熱量・温度上昇のバランスを最適化した「工作機械用高機能ボールねじ」の新技術を開発した。剛性を維持しつつ発熱を低減して温度上昇を約20%低減するとともに、ボールねじナットの位置の違いによる運動誤差を低減した。これにより、発熱量と運動誤差を低減することで工作機械の位置決め精度の向上が可能にしている。
工作機械側でこうした主軸や送りの高速・高精度・高剛性化が図られているわけだが、同様に工作機械スピンドルの先端で各種材料に対して加工を施すドリルやエンドミルなどの加工工具にもビビリの抑制や、長寿命・高能率加工に最適な耐摩耗性向上が要求される。
ユニオンツールは、自社のφ0.1のマイクロドリルの潤滑性・耐摩耗性を高めたDLCコート「ウルフコート」と、ダイヤモンドコート「UDC」の工具、金型のほか、各種機械要素などへの受託加工サービスをPRした。また不二越は、潤滑性と耐熱性・耐摩耗性を高め、ドライ加工でも高速高能率・長寿命化を図るアクアEXコートを施し、切削性能を向上させた超硬ドリルやエンドミルなどを出展した。アクアEXコートは超アルミリッチAl-Cr-Ti系コーティングで1100℃での耐酸化性を従来TiAlN系コーティングに対し3倍に向上させたことで超高速加工でも優れた耐摩耗性と耐熱性を実現したほか、最表層に特殊潤滑膜を施すことで切りくずとの摩擦抵抗を低減、耐溶着性を大幅に低減した。さらに複層構造膜の採用により、膜強度がアップ、工具の耐チッピング性の向上にもつながっている。
こうした耐摩耗性や潤滑性を付与した表面改質を施した製品が各工具メーカーから展示される一方、各種コーティングの受託加工メーカーや成膜装置メーカーも出展した。
オンワード技研は、パンチなどの金型を想定した超高硬度DLC膜「AC-X・W」を紹介。硬さ60~70GPaと高硬度で膜厚1μmを実現し、アルミニウムや銅加工の耐凝着対策に有効であるとした。12月以降に受託加工の受付を開始するという。アヤボでは、切削工具や金型などに対して、コーティングの前処理である研削・研磨工程とPVDコーティング工程を一貫生産する「nano warp」を提案。このシステムにより短納期・低コスト・高品質を実現する。PVDコーティングは、アークイオンプレーティング、ホロカソード、スパッタリングと三種の成膜方式を用意しており、顧客の要望に適したコーティングを選定する。
「INGENIA」を展示した日本エリコンバルザースのブース 日本エリコンバルザースは、マイクロドリルの寿命を飛躍的に向上する同社最新コーティングの「BALIQシリーズ」を施した各種工具を展示したほか、設置スペースがコンパクトで、高速、高精度、高柔軟性なコーティングを実現するシステム「INGENIA」の実機を展示。同装置では、同社のHIPIMS(High Power Impulse Magnetron Sputtering)ソリューションであるS3p(拡張可能なパルス出力プラズマ)テクノロジーにより、表面が滑らかで高密度のコーティングを実現し、特許技術である万能マグネットシステムVMSにより安定したコーティング時間と高品質のコーティングを提供する。
IHIグループのブース IHIグループは、IHIイオンボンドがCVD、CVA、PVDおよびPA-CVD装置のラインアップを提案、切削工具・金型・各種機械部品・航空エンジン部品・医療機器などの性能向上を図るコーティングサービスを紹介した。装置販売においては、IHI機械システムが真空・加圧脱脂焼結炉、真空浸炭炉、真空脱脂洗浄機、真空炉などの熱処理関連装置、IHIハウザーコーティングがPVD/PACVD成膜装置Flexicoatシリーズと、工具・金型分野で適用されている最新のアーク成膜技術「CARC+」を中心にポスター展示と工具、自動車部品のコーティングサンプルも展示した。
今回のJIMTOF2014では、航空機、医療、エネルギーなど成長分野のアプリケーションに対応する工作機械や工具・金型などが多数紹介される一方で、海外生産の進む中で求められるコスト低減に対応する生産性向上の要素技術が数多く出展された。こうした新分野などでの各種要求に対応する機械要素技術や表面改質技術など基盤技術の技術革新がますます求められてきている。
第191回 第18回機械要素技術展開催、部品や金型などの精度・性能を高める技術
第191回 第18回機械要素技術展開催、部品や金型などの精度・性能を高める技術機械要素技術展のもよう 表面改質技術やそれらの計測・評価技術に関する専門技術展「第18回機械要素技術展」が6月25日~27日、東京・有明の東京ビッグサイトで開催された。特殊環境で高い耐久性を実現する軸受や直動案内機器の技術、エッジ品質を向上し部品や金型の精度や性能を高めるバリ取りなど加工技術、部品や金型の性能を高める表面改質技術などの最新の製品技術が出展された。
軸受の耐久性向上技術
軸受や直動案内機器など摺動する箇所では、一般に摩擦を軽減する潤滑油やグリースが必要となる。しかし食品機械や医療機器など潤滑油剤の使用を避けたい用途や潤滑油剤が洗い流される可能性のある用途などでは、潤滑油剤を補う熱処理やコーティングなどの技術が必要になる。NSKマイクロプレシジョンでは、従来のステンレス鋼SUS440C以上の耐食性を示す新開発材料TBN-6Hに独自の熱処理技術で、耐荷重性能を実現したベアリング「キャストップ」を出展した。塩水にさらされる船舶や釣具、消毒液を使用する医療機器等の酸性・アルカリ環境に抜群の性能を発揮するという。
高精度部品・金型を作る加工技術
機械要素技術展では軸受や直動案内など部品や金型の精度や品質を高める様々な加工技術が紹介されたが、中でもエッジ機能を満足させるためのバリ取り・エッジ仕上げ技術が多数出展された。
ユニテック・ジャパンのブース 三共理化学では、バリ取りのほか、はく離、粗し・下地処理、研磨などに適用できる「ブロワ式ブラスト装置」を提案した。研磨メディアを変えることで微細バリだけを除去できるほか、薄膜、塗膜のはく離、溶接焼けなどの研磨処理、さらには下地処理として面粗度を調整することでコーティング膜の密着性を向上させる役割を果たすという。また、コンプレッサー式に比べて電気消費量が70%削減できる省エネ性、付帯設備・機器が不要なため省スペース性に優れている点などを強調した。同社はこのほか、精密研磨材「ミラーフィルム」や「ラッピングフィルム」などの展示を行ったことで、来場者からは研磨全般についての相談が寄せられた。ユニテック・ジャパンでは、プラスチック製のブラスト材を吹き付けることにより、ワークに付着した樹脂を取り除く「UNICLEAN TC-X1」の実機を出展し、デモを行った。ブラスト材がプラスチックのため、ワークにダメージを与えないことや、熱を加えることなく洗浄が行えるためガスの発生がないことなどをPRし、スクリュー、ダイス、射出ノズル、クロスヘッドパーツ、金型の洗浄に適しているとした。
コーティングなどの表面改質技術
日本コーティングセンターのブース コーティングなどの表面改質関連技術では、日本コーティングセンターが今秋から受託加工を開始する予定の量産対応可能なダイヤモンドライクカーボン(DLC)コーティング「Try-F(仮称)」を紹介した。新成膜方式により1~3μm厚の高硬度で密着性の高いDLCコーティングを樹脂やゴムなどの軟質材、真鍮などの軟質金属にも成膜できるという。
日本マクダーミッドのブース また、日本マクダーミッドでは、LDS工法で成形された部品に対して選択的めっき析出性を実現、ファインピッチめっきやワイヤボンディングなど高スペックに対応したMID(Molded Interconnect Devices)めっきプロセスを紹介した。BMW Z4ステアリングスイッチなど多くの実績を持つという。
ナノコート・ティーエスのブース H.E.F DURFERRIT JAPANと共同出展したナノコート・ティーエスは「セルテスDCY」を紹介。新プラズマ源採用により180℃以下の低温でDLCコーティングが可能で、PVDとプラズマCVDのハイブリッドプロセスにより高密着を実現した。また、鋼と強い密着力のCr系下地層と、靱性に富んだバッファー層で耐荷重性・耐衝撃性が向上し、高面圧・繰り返し衝撃でもはく離しないとした。清水電設工業は、硬さHv3500の耐摩耗性と耐熱性に優れた「ZERO-1」コーティングを中心に、各種コーティングを冷間鍛造や冷温間プレス、抜き金型などの用途に向けて提案した。
不二WPCのブース 不二WPCでは、金属の疲労強度向上と微細なディンプルを付与するショットピーニング「WPC処理」処理や、金属加工の最終仕上げとして用いられる鏡面加工「3Dラッピング」、安定した密着力でナノレベルの薄膜を成膜するDLCコーティング、各処理の複合処理による機能向上などを紹介した。
第192回 表面改質展2014が名古屋で開催、熱処理・コーティングなどの製品・技術を展示
第192回 表面改質展2014が名古屋で開催、熱処理・コーティングなどの製品・技術を展示表面改質展2014のもよう 日刊工業新聞社の主催する表面改質展2014が7月2日~4日の三日間、名古屋市のポートメッセなごやで開催、9094人が来場した。難加工技術展と同時開催することで加工工具や金型なども多数展示され、それら製品の耐久性向上を図る技術や自動車部品の摺動性を向上する技術など、様々な表面改質関連の製品・技術が一堂に会した。
日本アイ・ティ・エフのブース 東研サーモテックでは、熱処理技術やDLCコーティングなどのドライコーティング技術の提案を行った。同社では、熱処理の受託加工はタイを中心とした海外での伸び率が高く、それに伴いコーティングの需要も増加しているという。展示会では国内11拠点のほか、タイ、中国、マレーシア、メキシコで事業を行っていることを強みに国内と同様の高品質な熱処理、コーティングが実現できるとPRした。国内では、自動車部品にDLCコーティングが採用されているほか、エンドミルなどの切削工具で窒化クロムコーティング「S-CrN」がHV3600と高硬度で耐熱温度1200℃という特性が評価されて採用が広がっているという。日本アイ・ティ・エフでは、高度がHV6000から7000で油中摺動特性に優れた機械部品用DLCコーティング「ジニアスコート HA」を紹介。日産自動車のエンジン用バルブリフタで採用されたとおり、潤滑油を用いずに低い摩擦係数を示す水素フリーDLC(ta-C)だが、エンジン油中ではさらに摩擦係数を低下、省燃費に貢献する。他の自動車メーカーでの採用も決まっており、今後も幅広いラインナップと実績を強みに自動車部品を中心にDLCコーティングの拡大を図っていく。
オーエスジーコーティングサービスのブース オーエスジーコーティングサービスは、ドリル、エンドミル、タップの再研磨・コーティング処理品を展示。特に注目を浴びたのは超硬ドリルに対してCVD(化学蒸着法)法でダイヤモンドコーティングを行った事例。超微細結晶の多層構造により表面が平滑で切れ味がよく、航空機で採用が進んでいるCFRPの加工でデラミネーション(層間はく離)の発生を防止するという。同社が行ったアルミニウム合金のドライ穴加工では、DLCコーティングが709穴で折損するのに対してダイヤモンドコーティングは7177穴を達成、DLCと比較して10倍以上の耐久性を確認している。脱膜・再コーティングにも応じる。硬度はHV9000、摩擦係数は0.15で密着性にも優れるため、摺動部品や樹脂成形金型などにも適用できる。このほか、PVD法(アークイオンプレーティング法、電子ビーム法、スパッタリング法)により、TiAlNやTiCNなどのセラミックコーティング、DLCコーティングの膜種も豊富にラインナップしており、今後は親会社であるオーエスジーが扱う加工工具のコーティングのほかに、機械部品や金型にも適用を拡大していく考えだという。
TD処理の除膜を行ったサンプル 豊島技研は、金型や機械部品などに炭化物・硼化物、固溶体および化合物層などを形成することで耐摩耗性や耐焼付き性を付与する表面改質としてTD処理を提案。同処理専業の技術力によりPVDコーティングの代替処理として適用できるとPRを行った。また、同社では同処理の薬剤除膜サービスを新たに開始。従来の再コーティングではブラストで除膜をしてから磨き、ラップを行い再度TD処理を施していたが、同サービスでは薬液除膜を行いラップ、再TD処理となる。金型などで見られる細穴に対して再コーティングを行う場合、ブラストでは除膜が難しかったが、専用の薬液を使用することで膜の残存がなく、再コーティングにおいても高密着な膜が形成できる。また、ブラストのように母材が粗くなることもないため、再磨きによる形状変化が少ないことも特徴の一つで、現在のところ精度が求められる製品に対して適用が進んでおり評価を得ているという。今後、コスト面の問題をクリアして適用拡大を図る。
メタルヒートのブース 熱処理関連では、メタルヒートが最大1300mm(H) × 1300mm(W) × 1650mm(L)の真空熱処理炉における受託加工のPRを行ったほか、同社が幹事会社となって進める4社共同体の「金属熱処理ソリューション」を紹介。真空焼入れのほか、塩浴焼入れ、高周波焼入れ、液体浸炭、ガス軟窒化などの専門家集団が加工品質や納期、コストの問題解決に貢献するとした。また、同社では社外から受講生を募り、金属熱処理の知識、実技を教える「金属熱処理スクール」を開講。熱処理の基礎・基本を学ぶ座学コースと、熱処理技術を体験する実践コース、熱処理管理者を養成するコースと三種類を用意した。各コースを月に一回程度開講して同業他社の人材育成を助けるほか、ユーザーに対する熱処理技術の周知を図る。
レーザー焼入れのサンプル(黒色部分が処理済み) 金型の設計・製作・表面処理(めっきやアルマイト処理)までを一貫して生産する中日クラフトは、レーザー焼入れを紹介。レーザー焼入れは、レーザー光を鋼部品の表面に照射することで、急速な加熱と内部への熱度伝導による自己冷却により、マルテンサイト組織へと変態させ表面を硬化する技術。同社では高周波焼入れで熱歪みが問題になっている来場者に対して提案を行った。ただ、高周波焼入れに比べて加工価格が高価なこともあり、現在では半導体や医療関連などの比較的コストに余裕のある業種に向けて勧めているという。また、熱歪みを最小限にするため、今後はレーザー焼入れ後の冷却処理も検討するなど処理の幅を広げるとともに、より一層洗練した処理を完成させ、数年後に採用拡大を考えているという。
レーザー焼入れ(左)と高周波焼入れ(右)のサンプル 一方、主に高周波焼入れを主力に受託加工を行っている富士高周波工業もレーザー焼入れを提案。高周波焼入れとレーザー焼入れの違いについて解説した資料を配布した。高周波焼入れは大面積で焼入れ深さが1mm以上、レーザー焼入れは局所焼入れで焼入れ深さ1mm以下であることや、焼入れ硬度の違い、歪み量の違いなどを示すことで、用途によってユーザーが焼入れの選択をできるようにした。同社におけるレーザー焼入れの単価は高周波焼入れと同等だという。
冨士川氏の講演のもよう 7月3日には、エア・ウォーターNV 顧問の冨士川 尚男氏が「最近話題の低温浸炭および低温窒化処理」と題した特別講演を行った。講演では、浸炭処理や窒化処理において、特にクロム含有鋼では耐食性や耐熱性などを劣化させると指摘。同社が行う低温浸炭処理「PIONITE処理」では、特にオーステナイトステンレスに400℃前後で浸炭処理を行うと、クロム炭化物を生成させことで耐食性を落とさずに表面硬化させることができるとした。低温窒化処理「NV窒化」は、300℃後半の低温で窒化処理を行うことで、炭素鋼からニッケル基合金など幅広い鋼種に対して低歪み、母材硬度低下の抑制、S相形成による耐食性向上などの特徴をもった窒化処理が行えるとした。また、どちらの処理も圧縮残留応力が残存された状態となるため、疲労強度の向上や応力腐食割れを防ぐなどの特性向上を図ることができる特徴を持った処理であることを報告した。